*
My husband is not home and I am trying to install a new light fixture. The problem is that the fixture has two wires, white, black and green. But the outlet has two, white and black. I am assuming the green wire is a ground wire. What do I do with it?
Discussion Forum
Discussion Forum
Up Next
Video Shorts
Featured Story
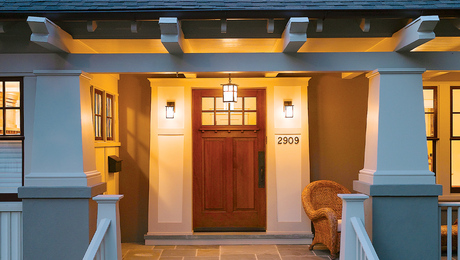
Lighting up an exterior isn't just about ambiance— it's also about code compliance. Here is what the code says about safety and efficiency when it comes to outdoor lighting.
Highlights
"I have learned so much thanks to the searchable articles on the FHB website. I can confidently say that I expect to be a life-long subscriber." - M.K.
Fine Homebuilding Magazine
- Home Group
- Antique Trader
- Arts & Crafts Homes
- Bank Note Reporter
- Cabin Life
- Cuisine at Home
- Fine Gardening
- Fine Woodworking
- Green Building Advisor
- Garden Gate
- Horticulture
- Keep Craft Alive
- Log Home Living
- Military Trader/Vehicles
- Numismatic News
- Numismaster
- Old Cars Weekly
- Old House Journal
- Period Homes
- Popular Woodworking
- Script
- ShopNotes
- Sports Collectors Digest
- Threads
- Timber Home Living
- Traditional Building
- Woodsmith
- World Coin News
- Writer's Digest
Replies
*
How old is the house? Are you sure there isn't a green or bare wire secured to a screw on the box?
Rich Beckman
*
the house is 5 years old, and my husband built it. I'm not sure about a wire in the back. I can check.
*
There better be a ground coming to the box if the house is only five years old....
If it's a metal box, the box should be grounded as well.
*Inside your octagon box there is a grounding screw. Attached to it should a bare coper wire if it has been wired properly. Attach the green wire to the bare copper wire. If not attach the green wire to the gounding screw in the octagon box.
*If the house is five years old, then there should be a bare wire in that box. Usually the light fixture will have a green screw somewhere in the mounting bracket. The green wire from the fixture and the bare wire in the box should be secured under that screw.Let us know what you find.As an aside, are you using wire nuts? Be sure that all of your connections are tight and secure with good contact between the wires.Rich Beckman
*
I did just that, and it worked. Thank you very much
*I used the little orange plastic screw nuts. The light looks great. Thank you so much for your help.
*
Rich:
My my how time has changed. When I started you couldn't get anyone to pass a connection as being "tight and secure with good contact between the wires" unless it was pigtailed and soldered. Now we make a twist, stick a penny piece of plastic on it and call it good. Still call it the same thing though: "A good, safe connection"
Oh well.
*'cept now the penny pieces of plastic have metal threads inside, and the longevity of soldered connections are starting to be questioned. Pigtails are always a good idea, and usually are on the lighting fixture from the factory. and a "good ground" (if any) was metal to metal contact of the box to the fixture. Jeff
*Solder is a terrible conductor and could well conceal a poor mechanical contact between the wires. Electrical tape is an iffy long-term insulator. The main thing I guess is to do good work whatever you're using, a sloppy installer can make anything dangerous....I was going to ask the poster to have her connections checked by someone else, given that she hadn't done this before. Specifically, make sure the wires are in good contact with each other rather than depending on the nut for a connection, and that the nut is tight enough that it can't be pulled off. A bad connection can mean resistance, which means heat, which can mean failure or fire. I also would not assume that the box is grounded, or even if it is that it is a good (low-resistance) ground -- you may want to check it with a $1 neon bulb tester (the bulb should light when placed between hot (black) and ground).One thing that scares the heck out of me: If it's a flush ceiling fixture, please DON'T OVERLAMP IT like everyone seems to do anyway. The heat fries the wire insulation. If your wiring is pre-1985 the insulation has a particularly low temperature rating. Bad connections, worn wires, and overloaded/overheated circuits cause a lot of house fires.Which ARE the "wire nuts" that have actual nuts in them? I know I've seen them, but every brand I've looked at recently actually has a little conical spring..
*
Hey Jewel, was that your house that I saw on TV last night? (Just kiddin,smile). Glad it worked out for you.
*
I just rewired my 50's era house to all the junction boxes.
(From the junction boxes to all the switches and outlets are next.)
I was amazed and impressed with the way the old timers twisted and soldered anywhere between 3 to 5 12-gauge or 10 gauge wires and managed to push this down into the boxes after they were wrapped in what seemed like a very rubbery electrical tape. Took me some cursing and sweating trying to undo the wires - my regular soldering gun couldn't put a dent in the old solder.
Wire nuts certainly made the job easier but had to use a large set of pliers to twist them on.
*If you want solder fun, try disassembling a 1910 vintage trolley car for restoration. Solder joints everywhere. Solder is very reliable when done right, but as you say, it is really easy to do it wrong. The solder really is a mechanical holder; all of the directions call for twisted connection first, which will give electrical connections. Then you apply the solder, which alloys into the copper and locks everything together, adds some conductivity, and keeps corrosion out of the joint.
*Actually andrew, back in the days when we did the solder joints the real "secret" to a good joint was in the twist. The solder didn't really do a lot of conducting. It just held things together. Then we used this electrical tape like Alan mentioned. And it was Rubber, not the cheap vinyl stuff we get today. Then, in some places you covered all that with friction tape. Oh yes, as I recall the solder was indeed a much tougher product than what we use today. Most folks looked down their noses at the new fangled way of doing things on the cheap when wire nuts started showing up on jobs.A better way to do the job? I don't really know. Certainly it took longer to do. But we didn't have any connection failure problems due to poor contact, or some yayhoo not putting a nut on right. But the key then and now is for the person doing the job to want to do it right and to take the time to put some pride in the work.
*Oh no, I agree, the important thing is wire-to-wire contact. The connector, whether a nut, crimp or solder, is not there to conduct the power. I don't think the solder does anything more than stick to the copper, and it won't even do that if the joint is not properly cleaned and fluxed. But lots of people fudge solder joints (ever see the wires spring apart when you melted the solder?). As for not being able to melt an old joint, I would suspect an inadequate iron -- the copper wires do sink away the heat easily, at the expense of the insulation.A better way? How about welding? :) Or maybe a circuit breaker that would add up power consumption at all circuit devices (reported by miniature transponders) and cut the power if the circuit was drawing more? (Don't laugh, maybe someday...) Or some way to identify "yahoo electricians"?
*andrew:1.So you weren't blown away in last week's wind.2. Doesn't a circuit breaker already work by sensing total power consumed in a circuit and cut the power when the circuit is drawing more power than rated. I must have not gotten the point you were making...3. Welding connections. In the electric motor repair field, connections inside the motor are brazed with " silver solder " using an oxy-acetelyne torch. They do not want a hot motor melting the solder before other items like insulation can fail. The connections on commutators are soldered with tin/lead solder, probably because of the possible damage to the mica or phenolic from the torch. Also connections inside of heating appliances are brazed.4. Properly cleaned and fluxed connections, good advise, just do not use acid flux on electrical wiring! Rosin flux only, and usually just what is inside the solder is perfect for the job on clean connections.5. Correct, the bigger the copper the bigger the iron/gun needs to be. A bigger iron can melt the solder before the heat has a chance to travel up the copper and damage the insulation. Or one can leave it on too long and really melt everything... The other trick is the soldering iron needs a clean and shiny( with melted solder ) tip in order to conduct the heat to the joint. A dull crusty iron will be trouble. A wet sponge makes a good iron wipe.6. I have never seen a wire nut with an actual machine screw nut inside. Most have the conical spring, the purpose of which is to gather the wires and apply more pressure as you tighten the nut. I have seen ceramic wire nuts that have no metal parts, the conical groves are in the ceramic.7. Yahoo electricians...Hey! Don't go there...
*About 15 years ago I had some "wire nuts" that had a hollow brass insert with a set screw on the side which tightened against the wires. The brass insert threaded into a plastic cap which looked like a common wirenut. As I recall, they were much more expensive than the conical spring type.
*1) No, we were OK on the wind ... it actually removed some garbage for us. :)2) I meant a "smart" breaker more like a GFCI which would compare the cumulative device loads to the actual load ... and trip if there were excessive current "unaccounted for" ... obviously this would be expensive! (with 'current' technology)3-6) No, I want a copper-only connection -- melt those suckers together! And I could swear I've heard of wire nuts that actually are wire nuts -- here perhaps. But one hears all sorts of stories on this board....7) Nothing personal!
*Ok, well now I'm wondering what all of you think about those Wire Nuts that say "no pre-twisting required." Are those the spring/conical type you mentioned above? I see that the manufacturer 'GB' makes these. Are they safe or cheap?
*The only ones I've seen, and I just happened to look at them yesterday, are made by Ideal. They are made especially for damp/underground applications, but the package says specifically not for submerged application. They had a plastic star shaped opening (imagine slicing an asterisk in a coffee can lid) to the nut, but I don't know if they had any metal inside. They also say they're for one-time use only. A blister pack of two nuts cost the same as a small pack of about 20 regular. Not the type of thing I want to use unless I really had to.
*Some regular ones say this I think. It's been debated here before. Don't do it.
*
My husband is not home and I am trying to install a new light fixture. The problem is that the fixture has two wires, white, black and green. But the outlet has two, white and black. I am assuming the green wire is a ground wire. What do I do with it?