Is radiant heat worth the extra money? Then no AC, so AC is an add on cost? What are your thoughts about the two types of heat.
Discussion Forum
Discussion Forum
Up Next
Video Shorts
Featured Story
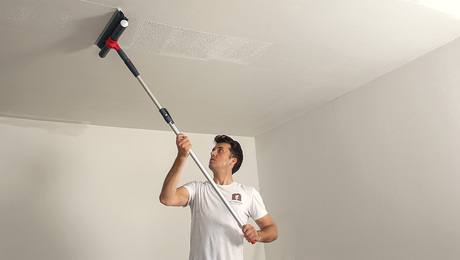
Skim-coating with joint compound covers texture, renews old drywall and plaster, and leaves smooth surfaces ready to paint.
Featured Video
How to Install Cable Rail Around Wood-Post CornersHighlights
"I have learned so much thanks to the searchable articles on the FHB website. I can confidently say that I expect to be a life-long subscriber." - M.K.
Replies
I have forced hot air in the northeast and it SUCKS. It always seems to be trying to catch up. It's sized properly and was installed by a pro, but when it gets below zero and the wind starts, the house always seems cold.
Conversely, I stood next to an open 14' garage door in a firestation in winter. I couldn't tell the door was open standing 4 feet away from it. Toasty warm. I've been thinking for years to put radiant floors in.
By the way, the myth of cooling and heat in the same ductwork doesn't work in residential applications, in my humble opinion. Either the ducts are sized for cool air and blows the curtains off the windows, or sized for warm air and the AC just dribbles out.
Good luck...G
"By the way, the myth of cooling and heat in the same ductwork doesn't work in residential applications.."
A myth? Never heard that one before. How do you know that your system was sized properly? Would you know the difference between an installation well done and one poorly done. Don't confuse your poorly operating system with the entire collection of forced air systems. They can and do work and work well.
Don't be offended Tim. I qualified all of my comments as my opinion and still mean it. I can say it was sized properly and installed well because I've been in the building business for 18 years and can tell a good sub from a poor one. I also know of several people who took out FHA to put in radiant. I've never seen someone take out radiant to put in FHA.
All I was trying to say is that you make compromises trying to run cooling and heating through the same ductwork. If you can make a FHA system that can heat AND cool a space through one set of ductwork with optimum efficiency you are VERY good at it.
Gman
I am not offended, it just that you statement:
"It's sized properly and was installed by a pro, but when it gets below zero and the wind starts, the house always seems cold."
is contradictory. IF it were sized properly, the house would not always seem cold. So part of your staement in not accurate. Either the system is not sized properly or not installed properly. One of these two IS a fact of your installation.
Regardless of the desirability of the RFH (and I fully agree with and promote RFH, I design and sell the systems), it does not exclude a well operating forced air system. The best forced air systems are a slight compromise, but in a well done system, the limitations are unnoticeable by all but the most observant. It is however the accomodations for both a lesser volume of warm air for heating and the greater volume of cold air the same system would typically be called on to deliver for cooling, that separates the good from the average. Based on what you have said, your is at best, average.
I have, BTW, seen radiant systems replaced with forced air systems, though not a good RFH system in a residence.
There is no "yes or no" answer. To many, the answer is an unqualified "absolutely". To others the cost is not worth it. A properly done forced air system provides a very comfotable space, with added benefit of being able to humidify the space is necessary or desired, introduce conditioned fresh air, and filter the air. Hydronics/radiant floor heat is easier to zone, typically provides a more uniform and to most a more comfortable heat. A real myth is that it is healthier and doesn't dry the space (both complete BS). With hydronics there will be no drafts, and if you refuse to clean, it will not move the dust around. Hydronic sytems are usually quieter. Walking barefoot in the winter on a warmfloor is a wonderful pleasure.
Other benifits of having a boiler as a heat source is that you can use it to make domestic hot water as well.
If I had the opportunity to build a new home I would pay for RFH heat, have an indirect water heater and have a couple of simple air handlers/dx coil units for the ac. I would not spend the extra money for a high velocity type of AC. On the other hand, my present varialbe speed, 2-stage furnce and AC system works quite well and is very comfotable.
Does radiant with separate A/C cost more? Yes. WAY more. Forced air is far cheaper in capital cost. I suspect forced air wins on the labour side too.
Is it cheaper in operating cost? That greatly depends on design. Based on my understanding of the heat transfer involved, at a given air temperature there's little to no difference in operating costs between well-designed systems of either type. However, at temperatures set to give similar levels of comfort, RFH can provide heat more efficiently (ie. at lower operating cost) than forced air can.
Does radiant heating feel more comfortable than forced air? Yes. I think most people would agree that it "feels" better than even a well-designed forced air system from a temperature comfort perspective (humidity/dryness comfort is another matter). People feel more comfortable at lower temperatures with RFH (during the heating season) because you don't feel the air movement. THAT is what can be used to reduce operating costs. You can of course throw away that advantage with bad design or by setting the thermostat based on the number rather than on your comfort level. You can also gain an advantage by turning down your thermostat at night with the forced air system- something that an RFH system can't benefit from as readily because it responds far less quickly to changes in temperature setpoint.
Can you design a forced air system properly? Yes, I'm sure it's possible. Although I am not an HVAC person, I know a thing or two about heat transfer and fluid mechanics. It seems to me that you'd want to feed your A/C to your room via ducts in the ceiling and your hot air via ducts in the floor to minimize stratification of hot or cold air, otherwise you'll be cranking your setpoints up/down in either season to feel comfortable. Most forced air systems operate with one set of ducts, compromising the distribution of air during one season or the other. No doubt it's possible to minimize this with proper design, but it is an inherent design feature of a single ducted system. Nothing that some ceiling fans couldn't fix in summer I suppose, but that's not a great fix in winter.
Is it worth the extra capital cost? That's a value decision- how much do you value comfort? Nobody can make that decision for you.
For me, it was a no brainer. Our house is heated with rads now via an antiquated thermosiphon hot water boiler, and the system is VERY comfortable. My wife benefits enormously from NOT circulating the air and dust/pollen/mites- regardless how well you filter, moving air will re-suspend stuff that's already settled out and make you less comfortable than if the air is still. We'll be heating the addition via RFH, replacing a few of the rads and heating the rest with a dedicated loop of this system using a modern boiler. A/C has yet to be decided- we're still shopping the options.
Allow me to add my support to your long and thoughtful post.Our house has RFH and regular AC. While it sported just hot air to heat prior to the renovation, I made a committment to make the home comfortable and energy efficient. Separating the heating and cooling systems is part of that equation as IMO forced air systems typically have to make compromises when they have to heat and cool.For instance, to minimize duct noise and so on, it is necessary to size ducts according to the load they're trying to carry. In many homes, the loads experienced in the summer and the winter vary a great deal. If you use a program like HVAC-Calc to size your ducts (and I wouldn't advise you to go this route, BTW), then the ducts are either oversized in the summer or the winter wherever there are large load differences.You can deal with the duct size issue by zoning a great deal or by adjusting baffles from summer to winter and back, as needed. However, considering how much trouble most homeowners have just doing the basics (i.e. changing filters), I'm not convinced that setting baffles is for the majority out there. Microzoning is possible, but expensive... Setting up the cooling system to do just that and perhaps recirc air for cleaning and/or HRV distribution is a welcome bonus.For example, a room may have a large south-facing window that is well-insulated. In the wintertime, the heat loss via the window may be moderate. In the summertime, the heat gain may require a great deal of heat extraction. Similarly, on older homes that have small windows and uninsulated walls, the heat gain may be moderate while the heat loss could be murder. It all depends on local climate, house construction, orientation, etc. In other words, YMMV.In my mind, the only combined systems that qualify for decent space heating and cooling are ceiling radiant systems like the Karo stuff sold at http://www.naturalcooling.com. Even then, you have to watch out, as something has to remove the latent heat (i.e. you still need a high-speed duct system to remove humidity). I may have sprung for the Karo system if a qualified installer could have been found locally. Particularly in older homes, the thin walls do not lend themselves to running any amount of ductwork...And so I find myself with both RFH and a regular AC system. Time will tell if this was a wise choice.
Edited 8/11/2005 5:37 pm ET by Constantin
Some of this is intuitive, some just learned by OJT and experience. Not a lot of analysis involved in low pressure, low temperature & low velocity air movement.
The layout of systems has nothing to do with heat transfer or fluid mechanics. (This is the equivalent of using finite element analysis to determine how to frame a wall).
Critical features of a well operating forced air system are: crossing air flow patterns, adequate returns and proper selection of diffusers to get the desired throw. Important design criteria to keep in mind to keep duct and register/grille noise to a minimum is air velocity in ducts and face velocity at reg/grls.
The first feature is accomplished with low supply/high return, high supply/low return and supplies being located at/or as near to point loads as possible. If the air moves from one corner of the room at the floor to the opposite corner of the room high on the wall near the ceiling, stratification is greatly reduced. Another important feature, available only in variable speed furnace/air handler units, is continuous, low speed fan operation.
The second feature I mention is the most neglected feature of forced air systems in residential installations. EVERY room that you want to be consistently comfortable shall have a return, sized for the cooling supply air flow (the limiting operating conditions for designing air flow side of the system is during the cooling mode). The only exception is in rooms where return is prohibited by code, i.e. toilets (and those should be exhausted at a rate of 10 air changes per hour during occupancy). The return should be located to give the best cross flow that room shape and other constraints allow. No one would ever think of running a pluming supply without a drain, air should be treated the same. It will only go where you want it to, when you give it no other choice.
Selection of registers to acheive the proper throw is an equally neglected facet of proper design and installation. A 10x4 (the only size most contractors buy) floor register at 90 cfm performs quite a bit differently than it does at 50 cfm. Different air flows require different sizes. If I am designing for a 12 foot ceiling, I size diffusers differently than if I'm I designing for an 8 ft ceiling. Depending on the environment (i.e. wether cooling or heating is the dominant operating mode), and the location (wall, floor or ceiling), you select the terminal to get the air where you want it initially or to counteract the natural tendency of hot air to rise.
The remaining feature of a well done system is selection of duct and return grille/register sizes to minimize noise and unnecessary pressure drop. Air in supply ducts should never exceed 0.08" of static pressure drop per 100 ft of duct, return grilles face velocity and return duct air velocity should never exceed 500 fpm. Additionally, dampers (this is what they are called Constantin) should be installed at every branch from the main trunk line.
Edited 8/12/2005 1:37 pm ET by Tim
I'd think you'd have to be way up north to make radiant worth the cost. But that's just an opinion.
I think the arguement that forced air causes dust problems is ridiculous. DW has alergies, and I think that filtering the air helps make her more comfortable.
The dust has to go somewhere - It might as well get stuck in a filter as be laying around in the carpet.
I also think the's a lot of value in circulating the air. It helps keep the humidity down in the basement during the winter and summer. And circulates some air through the bathrooms when the fans aren't run enough after showers.
It also helps dilute cooking odors when DW burns dinner. (-:
>I'd think you'd have to be way up north to make radiant worth the cost. But that's just an opinion.Ron, I'd give a resounding "No Way" to that, recognizing that it's just your opinion. Even if I built in TX or FL, I'd still include some RFH capacity to take the chill outta the floor. And where I am, it is absolutely fantastic. Now, "worth the cost" is subjective, be/c cost is quantifiable, while "worth" isn't. Could we have installed a ducted system for less $$$? Sure. Would we be as comfortable? Absolutely not. How much is comfort worth? It's an individual answer. To us, you could take away practically any single component of the house, but you'd better not touch my RFH or Central Vac. I'd probably get a gun to protect those, which gives you an idea of my seriousness! :)
"... RFH capacity to take the chill outta the floor."
Well being as I live in a "normal" house.....(-:
With a heated basement you don't NEED to take the chill out of the floor. And that's how probably 90% of the houses are built here.
So I guess it's partly a matter of house type also.
The follies which a man regrets the most in his life are those which he didn't commit when he had the opportunity. [Helen Rowland]
"With a heated basement you don't NEED to take the chill out of the floor. And that's how probably 90% of the houses are built here. "
Up here, 99.99% of the houses have heated basements, and the floors are still cold. Nothing like rfh on a -40 day. The only thing better is a cast iron rad to sit beside.
>Up here, 99.99% of the houses have heated basements, and the floors are still cold. Nothing like rfh on a -40 day.I agree. A floor will be, at best, room temp, and a 72 degree floor will be less comfortable than an 82 degree floor in the same way that a 72 degree bath will be less comfortable than an 82 degree bath.I stayed in a hotel in Ft Worth a few winters ago on an upper floor, and wondered why it felt uncomfortable even though the ambient temp was fine. Then I realized my feet were cold and that chilled the rest of me.Easy to say, "ain't no big deal" until you've lived with and experienced it done right, and then you wouldn't give it up without a fight!
I installed hydronic radiant heat in my floors a couple of years ago (we had electric - in New England!!)
I can say that it is the most comfortable heating system - bar none. We keep our house at 69-70 degrees. When visiting friends with FHA and they the house at 72+ and we 'feel' cold. In fact are lower limb areas are cold.
I have a young daughter, and my wife does home based daycare.... kids love it as well (they just don't know it!). The colder it is outside, the more toasty the feet feel. I come home, kick off the snow and remove the boots to warm up the feet.
People spend outrageous amounts of money on things that have far less of an impact on their comfort.
We have rfh , it's not so much the chill but the overall level of comfort is better.
Five Radiant Heat jobs, Virginia, West Virginia, Michigan & Florida. Five happy customers, including my wife. The respnce that ref heating and cooling in the same duct work is on the money. If you want to cool you should dump the cool air out of the ceiling and take the return air off the ceililng, to heat you want to put the cool air up out of the floor and return air off the floor. IMHO it is worth the extra $ for RA.
Thought you might like to see a picture of a radiant heat manifold from a recent home. I couldn't get back far enough to fit it all in. When you add in all the tubing in the floors you have a considerable amount of water to heat. Because the radiant heat does part of it's job by heating up the mass of the flooring, it is very hard to control. If it gets too hot, you have to open the windows, too cold and you just wait. The amount of energy it takes to heat all that water is significant. If you have a leak, well, lets not talk about that!
Comparing radiant to forced air is hard. They are entirely different. I'm a carpenter not a heating expert but I've been around long enough to see a variety of radiant heat over the years. I doubt if there is one radiant electric system from the 70's that is still operating. With the cost of oil, the folks that own the one in the picture can't afford to use it. Good thing they have wood back up.
I'm still skeptical of the radiant systems. Some folks swear by them but I think it depends on many factors. I know the quality and controllability of forced air. In another 25-30 years I'll have a better take on the radiant.
Beat it to fit / Paint it to match
I've created a page where you can download a complimentary older version of the:Home Owner's Guide to Indoor Comfort Quality
A Five Step Blueprint to Creating Indoor Health, Wellness and Comfort for North America's Maturing Population.Its a 5 chapter eBook (pdf)...about 200 pages if I recall.http://www.healthyheating.com/ebooks/Complimentary_Copy.htmHope it helps answering many of the questions on interior on radiant vs forced air.By the way...there is no comparison to be made.
The formula is:IAQ + ICQ = IEQIndoor Air quality + Indoor Comfort Quality = Indoor Environmental Quality.You can have IAQ but poor ICQYou can have ICQ but poor IAQBut you need both IAQ and ICQ to satisfy 'ALL' the human factors....there is more but its all in the book.Enjoy.RBean
web: http://www.healthyheating.com
blog: http://wonderfulwombs.typepad.com
What exactly is an Engineering Technologist? Is that like a degreed engineer? A Bachelor of Arts or Science? I don't understand.
Hi Tim,Thanks for asking...In Canada we differentiate between Professional Engineers, Engineering Technologists, Engineering Technicians and the Trades. Within the profession of technology, governed by the Canadian Council of Technicians and Technologists [CCTT], (independent of the professional engineering society governed by Canadian Council of Professional Engineers [CCPE]) there are a number of technology tiers. The highest level is a Certified Engineering Technologist (C.E.T.) or Applied Science Technologist (A.Sc.T.). The exception is offered through the Alberta Society of Engineering Technologist (ASET )[http://www.aset.ab.ca/] along with The Association of Professional Engineers, Geologists, and Geophysicists of Alberta (APEGGA)[http://www.apegga.org/] where one can with the permission of the Joint Registration Board (ASET/APEGGA) obtain a Registered Engineering Technologist (R.E.T.) designation. At the very least it takes a combined eight years of education and work experience to obtain an R.E.T designation, a thorough back ground check into ones competency verified by numerous professional references verifying engineering skills, letters of recommendations and a three part professional examination which covers engineering law in Alberta, professional and ethical practice, plus the Engineering, Geological and Geophysical Professions Act (EGGP Act) and Regulations, Occupational Health Act and Worker's Compensation Act. Many holding technology designations intially came from the trades like I did. It's a great combination to have.There is also a Registered Professional Technologist (R.P.T.) Eng. Available through APEGGA which is professional practice limited to ones specialty. I’ll be working towards this additional designation next year. This would allow me to practice under both ASET and APEGGA. So there ya go...RBean
web: http://www.healthyheating.com
blog: http://wonderfulwombs.typepad.com
I just wondered, after I read the article that you co-authroed in the ASHRAE journal, I wasn't sure what that was equivalent to in the US. Obviously a substantial acheivement.
Regards,
Tim
The article had been sitting in brain for a few years and bouncing stuff around with Dr. Olesen, Dr. Simmonds and Tim Doran during the development was worth the PITA writing for a peer-reviewed publication. Tim, have you done anything yet with radiant cooling or thermally activated building systems? Would like to hear your thoughts.By the way not sure if you know Constantin, his humbleness hides his great resources!Cheers,RBean
web: http://www.healthyheating.com
blog: http://wonderfulwombs.typepad.com
I have not designed either of the types of system to which you refer. I think that I would love the opportunity to do so.
I have discussed some issues with C recently, seems very well informed, a little fuzzy on the details with actual HVAC systems and design of same.
That is the coolest picture!
I designed and installed a radiant system for my house - it works perfectly (well for the last 5 years, anyhow) - and it is not even a third as complex as the system in that picture. And I'm heating 8,000 sq feet of main floor and basement, plus I have DHW off the radiant boiler.
If simple works, use simple. A basic radiant system needs a main loop, one or more temperature regulated loops, distribution manifolds, distribution loops, some circ pumps, optionally zone valves, and a control unit. The boiler helps too. My entire distribution system fits on a 3x4 piece of plywood with room to spare. I never even bothered to hook up the zone valves because the heating is nice and even.
Now, it may be that I have no idea what I'm doing, but I'm awfully suspicious of the guy who put together that monstosity, as good as a plumber he might have been.
Of course, if the customer is willing to pay for all that wonderful plumbing, why not!
Do the complicated systems insure job security ? I have seem many other systems that look like the one pictured.
Having installed my own system with six zones and dhw, I don't see the need for all the extra controls and piping. My system is not a low end or basic heating system, but it is a straight forward installation. I can almost remember how it all works.
If you go here...
http://www.healthyheating.com/Seminar_Downloads.htmthen scroll down until you find the slide show called:
Prefabricated Hydronic Control and Boiler Systems (7.9 mb)
(on a high speed wireless it shouldn't take more than 22 seconds)It's a presentation on the evoltion of residential boiler rooms concluding with the developemnt of prefabricated systems.This attached picture gives you (in my not so humble opinion) an idea of where boiler rooms are (should be) headed.RBean
web: http://www.healthyheating.com
blog: http://wonderfulwombs.typepad.com
Here is the other half of the same boiler room.<!----><!---->
These panels are selected from a catalogue like any other hydronic product.<!---->
They're prewired, tested and certified to UL/CSA standards...the better ones come with a plug...mount, connected, fill, test and plug it in.<!---->
Many people think these products "dumb" down the industry but in fact, it takes more engineering skill to use them since the piping distributing and heat terminal units have to be designed around a standardized product with fixed capacity rather than design and build custom panels for each job. <!---->
To design around a catalogued item like a control panel requires a deep understanding of system hydraulics and control applications such as valve authority. <!---->
Lots of benefits, too many to go into here but if you appreciate installation efficiency based on standardization, reduction in job site wastes including labor and materials and cradle to cradle philosophy then it should be too difficult to grasp the beauty of these factory built systems.<!---->
RBean
web: http://www.healthyheating.com
blog: http://wonderfulwombs.typepad.com
I have an older viessman system, but it is similar. The controls are straight forward and they are less complicated than many installations I have seen. The initial price is higher which may account for all the contrived systems we see out there.
Monstrosity is the word, Piccioni. I've seen others that are as big. This is the realm of the heating installer, I've got all I can do handling my end. That house not only had radiant in the floors but also in the walls and ceilings. You could be talking four or five times as much as a floor only system. The owner GC'd this one so this wasn't anything I specified. The place is a timberframe with a large volume, in a cold climate. It's only about 4000 sq.ft. not counting the basement. There are four sheets of plywood on that wall. The ceilings in the great room are around 25' tall and the bedrooms are at least 18'. This is, however a rather modest house compared to some of the ones that look like resort hotels.Many of the heating systems that are installed in my area are done by plumbers. There is a wide range of experience and approaches. Although hydronic heat has been around a long time, it is still a bit new in my area for some. I like to keep things basic when I can. Obviously that installer had to be good with all those fittings and gizmos. If the sheetrock hangers hadn't punctured the Pex in several places...I think one of the issues with radiant heat is that you can't turn it on and off when temperatures fluctuate. As another poster mentioned, a lot can be done to conserve energy with insulation, orientation and a bit of common sense. It's a shame this country doesn't have a better handle on consumption and relies so heavily on fossil fuel. We should be light years ahead of where we are. People in other parts of the world think Americans are gluttons, I wonder why.
I don't see insulating the house properly and then including that in the heating and cooling debate?? shouldn't this be included??
using the right insulation ( in my opinion FOAM) will allow you to better decide what size heating unit you need. you may be able to afford the radiant and the separate ac, because they would be smaller. or you might get a smaller forced air unit with a smaller ac unit (2 ton instead of the 5 ton) or 1 unit instead of 2. all to often this factor is over looked until after all the mechanicals are installed, then oops to late .
well that is my opinion
GOOD LUCK DECIDING!!
I totally agree with you that the envelope should be addressed in conjunction with the heating and cooling systems. It amazes me how much interior space people are willing to waste for utilities, AC ducts, etc. when making simple architectual changes to a home could make it far more resistant to heat flux, summer insolation, etc. Nevermind the much lower utility bills that a well-insulated home entails, along with better occupant comfort, less noise, etc. A home's energy needs requires to be addressed holistically. To that end, the heating contractor should evolve into an energy specialist so that insulation, envelope design, heating and cooling systems, HRV's, IQO, etc. can be adressed comprehensively by him/her. The greater value that such a specialist brings to the table ought to be compensated appropriately by the marketplace...
Edited 8/12/2005 7:19 am ET by Constantin
"...using the right insulation ( in my opinion FOAM) will allow you to better decide what size heating unit you need."
Knowing what the construction details of the structure are, including the insulation type and amount and air infiltration expected/estimated are critical pieces of information in the proper selection of equipment. Even if the "wrong" insulation were used, and the person selecting the heating/cooling equipment had accurate information, the proper equipment could still be selected. So what you typed is inaccurate.
However, in radiant floor heating systems, the cost is primarily dicatated by the area in which the tubes are installed, the labor required to install that tubing and the controls selected for the job. When taken into account of the overall project cost, the realtive cost of a boiler/hot water generator and the potential for savings from going one size to a smaller size, is negligible. Say, for instance in a 3000 sf house a typical RFH system installed with basic zoning and controls would cost $21,000, an average contruction and the boiler is 155 mbh with a list price of $4,222.00. Now I upgrade my insulation and I only need an 80 mbh boiler, with a list price of $3396.00, a savings of $826 out of 20K, less than 5%. The same amount of tubing, thermostats, piping (maybe some smaller manifold feeds), manifolds, pumps relays and other controls are required. The only difference is that either the flow and/or the temperature of the supply water is changed. Obviously, energy consumption year in and year out would be a significant savings and well worth the investment in better insulation.
In a forced air system, a greater percentage of the total cost would be realized because all of the ductwork would be corresponingly smaller, and the unit is a more significant portion of the cost.
I believe that this is overlooked by only the most ignorant of builders/subs/contractors/owners.
Tim
I do agree that there are a lot and I mean a lot of ignorant people in the building trades. Most thinking this is simple anyone can do it . then oops... reality sets in and they get there butts sued off. but as to being wrong I don't know what you typed shows a savings in the cost. also I have met only 2 HVAC contractors in the last 4 yeas that truly understand foam or any other insulation for that matter. They tend to look at the sq ft size of the home and they seam to automatically know.
Yep that one needs 2 forced air units and 2 ac units and radiant heat for the basement and ......
I know not every one is like this and I'm not trying to start a hate mail campaign But this goes on day in and day out. the worst thing is I also get this from most of the GC's. there again I'm not lumping every one into that pile it jest seams there is a lot of how did you say Ignorant builders/subs/contractors/owners who don't look at the big picture.
"Ignorance is bliss tell it cost you"
The house I'm working on now - 300s.f. turn of the century Queen Anne - had dual forced air systems, both oversized.
I am planning to use Icynene in the walls and under the roof deck (12' plus ceiling in attic), rehabbed windows, new wooden storms, etc.
What I would LIKE to do is mix forced air and RFH - using RFH in the bathrooms and maybe the kitchen and use a hot water coil in two air handlers.
It seems to me that not having to buy two complete forced air systems should at least partially offset the boiler cost. Ducts are already in place.
One of my concerns is finding the right person to install it without again oversizing it.
Everytime I see a basement slab in new construction poured without the provision ( pex tubing ) for radiant heat it breaks my heart. I can't think of any way to make a basement more comfortable in the winter.
"Everytime I see a basement slab in new construction poured without the provision ( pex tubing ) for radiant heat it breaks my heart. I can't think of any way to make a basement more comfortable in the winter."
Thats how I feel when I see a slab poored without foam insulation and a vapor barrier underneath. Keeps it wam in winter, cool in summer, and greatly reduced the damp.
All for less than $1 square foot .....