*
We are GREENBLOCK dealers and installers in Dallas. If only all potential customers where like Andy. Unfortunately this is not the case. We will not sell GREENBLOCK to do it your self homeowners or for that matter contractors that have no experience with ICF’S unless they agree to allow us to help with the installation and concrete placement. People look at these systems and think it’s easy just because they stack like childrens building blocks. Anything is easy if you know what you are doing. DON’T BE FOOLED There is a lot to know about ICF’S and concrete. Right now there are over 40 systems on the market. DO YOUR RESEARCH!!!!! DON’T BE OVER SOLD!!!!! Take Andy’s advice and you will save yourself a lot of heartache.
Here is a starting picture of an 11000 sq. ft. home we just finished in Bridgeport TX. It is on the cove of a lake and is so long we can’t get it all in the camera lense. Regards Norman
Discussion Forum
Discussion Forum
Up Next
Video Shorts
Featured Story
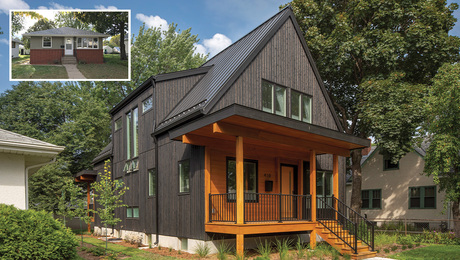
A small and dated house lends its foundation to a stylish new home with more than twice the space.
Featured Video
How to Install Cable Rail Around Wood-Post CornersHighlights
"I have learned so much thanks to the searchable articles on the FHB website. I can confidently say that I expect to be a life-long subscriber." - M.K.
Fine Homebuilding Magazine
- Home Group
- Antique Trader
- Arts & Crafts Homes
- Bank Note Reporter
- Cabin Life
- Cuisine at Home
- Fine Gardening
- Fine Woodworking
- Green Building Advisor
- Garden Gate
- Horticulture
- Keep Craft Alive
- Log Home Living
- Military Trader/Vehicles
- Numismatic News
- Numismaster
- Old Cars Weekly
- Old House Journal
- Period Homes
- Popular Woodworking
- Script
- ShopNotes
- Sports Collectors Digest
- Threads
- Timber Home Living
- Traditional Building
- Woodsmith
- World Coin News
- Writer's Digest
Replies
*
I've built four ICF structures so far, three foundations and a two-storey house, and I'm a convert. I love the things.
I have been building, repairing and renovating in wood for 20 years, I suppose, working almost exclusively on older houses and learning older techniques through dismantling things. I was quite surprised a few years ago to discover what a flimsy structure results from modern framing techniques. You know what I mean - no sheathing, or the sheathing replaced with foam, a few metal T-braces inserted here and there to hold the place up until the real structural strength is installed by the drywallers. It's not for me. I want to build a place that might outlast its first mortgage.
It's a pleasure to build something solid, strong, quiet and warm and know it's going to remain that way.
The first one I built was the foundation for an addition to my own house and I chose ICF because I could do the whole job alone without having to do old-fashioned formwork, which I have always disliked. And there is a big advantage of the things from my point of view - it puts foundation work into my hands again at a reasonable cost. I want that control because I'm the one the customer calls when things go wrong, not the subcontractor.
I won't bore you with a my advice on ICF (I'm just a neophyte), but my opinion is that ICF construction leaves everything else in the dust and I want to do more.
Andy's advice is good advice. Check out the discussion area at the ICF website he mentioned. There are some very experienced people there and some questions just like yours. Also, check the Breaktime archives. The subject has come and gone several times in the short time since I first came here.
Good luck with it.
*No Don not yet. But it is just a matter of time.
*
Don,
I saw a promo flyer from one of the distributors for PolySteel that showed an ICF house in Illinois that had been hit by a tornado. The roof was off, the windows were out, and the siding was gone but the walls were still standing.
Norman,
At one time there was considerable concern about termites nesting in ICFs. What is the industry position on this issue?
*
Don, I have not had this problem. However it is a concern. We cover all foam below grade with a peel and stick waterproofing membrane.(polyguard 101) The foam does not have any nutritional value for insects. But I have heard that termites and carpenter ants will nest in them. There is some talk about impregnating the foam with boric acid to lower the risk of infestation. We feel that good construction practices will all but eliminate the risk. (make sure all foam is covered, use termite flashing when needed and don't bury any scrap lumber on the site.) If anyone has any first hand experience with this problem please share it with this fourm. Thank You Norman
*
AFM Foam Corp makes an ICF they call Diamond Snap-Form that is impregnated with boric acid. They may have recently changed the name to R-Control something on another. I used it to form a full basement for an addition on my house; I guess time will tell.
Jerry
*
Do cold joints affect an ICF wall to any reasonable degree?
*
Were is your cold joint ? Do you guys use plastisizers in all your ICF ? Poly fibers?
*Terry,I'm working with a local Therm-o-wall distributor. Standard procedure seems to be to pour in 12 foot lifts, so there is a "cold" joint, but a ragged one since you can't reach down in the wall and knock off the top of the first pour. Combined with rebar, doesn't seem like a problem to me. I'm just trying to make an exhaustive list of wall penetrations.... Some people use plasticizers, but I've never heard of fiberglass being used for ICF's. Another trick when using a small, towable concrete pump is to use a 2" hose, not a 2 1/2" or bigger. I understand the manpower difference is substantial. Aaron
*Aaron,What's the secret to using a 2" line? I did an ICF pour last month; the pump operaror specified the mix so we could use the 2" and it kept jamming at the reducer. Switched to the 4" line and all went well but we broke our a** moving the line around.Jerry
*
Aaron, I don't know how you were able to lift a 4" line full of concrete. Since you did I would not want to have to fight you! There are a number of issues when you reduce to a 2" line. We use a batch design that is 1200 to 1500 lbs. of 3/8 pea gravel. 800 lbs. of sand. The rest of the design ie: water reducers, cement, plastisizers and retarders depends on the weather and what products the plant batching the mix has available.
The most important thing is that you stress to the concrete supplier that aggregate size is critical. Many smaller plants do not have seperate hoppers for pea gravel. If they do not backwash the hopper and the truck you will have a terrible time because larger rocks will keep jambing in the reducer and the lines. We sometimes place an expanded metal screen over the pump hopper to filter out the larger rocks. Be careful with this method. Make sure the screen openings are large enough to allow the free flow of concrete or you will segregate the mix. I hope this helps. Regards Norman
*
Norman,
Thanks for the reply. Moving that 4" line around was some of the hardest work I've done in a long time. I think your right on about the aggregate. Our supplier gave us 3/8" bluestone instead of pea gravel and I think that the sharp edges and occaisional large stone caused our problems.
I guess you're saying that if the mix is right the 2" line will work.
Thanks, Jerry
*Poured my wall thursday . Used a belt conveyer truck with a 6" trunk , about 5' long . Just kept walking around the form till it was full . Used regular concrete 6bag mix and a 4" slump . Took about 2 1/2 hr. to place 40 yds.
*
Dear Arron,
I have been a representive for the past 6 years have completed many jobs with much sucess. One house that was built a 2400 Sq Ft using electric heat for the month of January 1999 with a cost of total bill $90.00. In northern Indiana. They love it.
*Don: I may have missed it, but what system was it that you placed concrete in? Are you sure you placed the concrete at a 4" slump, and not higher?Ian
*
Ian, It was as close to a 4" slump as you can get . The concrete did not move more than a foot from the spot that it was placed. We had to pull it under the window openings. about half way ,one load came with about a 5 1/2 " slump ,made me think it was soup. I used the Rforms system out of West Palm Beach Fl. Uses extruded polystyrene 2" by 4'x8' , 16 plastic ties 16" on center, 8" from the edge. Lots of open space concrete flows well. Seems that the company has gone out of business. I think that there are similar systems out there.Don
*
Can this ICF forms be used to construct a solid concrete wall that will be stripped after the concrete sets? I have done a few projects that have required concrete containment walls for tanks and for other equipment. We typically form the walls with wood forms and strip them after the concrete sets. These are industrial type jobs with very specific wall layout. We always end up making specific forms and than scraping the wood. I currently have a truck dock project that I would like to buid a solid wall for with inserts for dock locks, levelers and restraints. Has anyone used ICF forms for that type of work?
*
Ed. Ihave stripped the poly off of the concrete on one job. I think that wood is a better choice if you want to strip the form, unless you plan on a lot of small or irregular shapes. The foam will make nice pockets in wood form work also. If it will not pull out , just a little flame from the torch will make it disappear. Don
*
Don: I am familiar with R-forms, The company was run by a man named Ed Roby, I believe he is primarily a builder, I'm not sure. The reason I asked about the slump issue is that a 4" slump going into any wall form, be it ICF or traditional will usually end up not consolidated well at all. With the ICF, nobody will ever see it, and the structural integrity is probably sufficient for the intended purpose, but I think you may want to make spot checks. I take it you did not use mechanical vibration, not the tapping on the wall stuff, but a real concrete vibrator? I am not trying to scare you or anything, I just think that if you were not aware, perhaps you might start checking on the next job......sure don't want to see you run into trouble. If I can help, email me directly and I can call you on a land line. Ian
*
Ian,We poured in lifts of 12 to 24" at the most . With the concrete dropping from the belt about 5 1/2 ' above the form that is 12' tall ,I don't think I would have wanted it any wetter. I do think that the last loads were in the 5" slump range. If you are familiar with R-forms you can tell if it was poured too wet or too dry by looking at the buttons . too dry and they have no deflection , if very wet they will be concave with a ring in the center. Mine are in the middle about were I like them. No I did't vibrate, but rodded around windows. I don't like to vibrate the foam forms . I know that Ed was a contrator ,I never talked to him but to a Cris Lang when I called them. I wonder if he is still in the contacting or if he makes the R-forms componants?
*
Hello Ed, We have used ICF's for retaining walls. The last one we did was 15' tall and 90' long. We used a form called Formtec. We chose it because it is easy to strip the foam. It is field assembled and you can vary the width of the concrete from 4" up to 12". I will try to get by the sight and shoot a picture with a digital camera and post it on this site. Hope this helps.
*I stripped the forms from one side of a foundation I poured for a house addition. It was slow and damaged quite a lot of the foam (which I wanted to use elsewhere) and left us with a lot of patchwork and parging to do. This wall was formed with Lite Form. You can form walls from 4 to 12 inches with Lite Form, too, and if the appearance is not critical it might be suitable for your purposes.
*Ed, Sorry I took so long to get this picture. This is the Formtech wall. It has not been parged.We have also done this with GREENBLOCK. I'll try to get a picture to post.
*Thanks for the picture. The system looks like it may work in the type of application we normally encounter. How far did you cut the hill back for installation? How many lifts was the wall poured in? Do you have a "bogey" number you use to estimate the dirt moved?Thanks for the information!EJ
*There was no cut. We had all the room in the world. The footing was placed at the bottom of the slope. About 1100 cubic yards of dirt was used to back fill the wall. We poured this wall in two lifts. Had the form been GREENBLOCK or AMVIC it could have been poured in one lift. The overall performance of the form was good and it is easy to strip.
*
As a prospective owner / builder, I am becoming increasingly interested in using ICFs in a new residence. There is a local contractor who has pumped many ICF houses, so that stress is lessened. I see ICF's as an environmentally sound, low-labor, cost-competitive solution, especially if you want an insulated, liveable basement. Sounds like a new construction challenge, too. Please tell me about your experience with ICF's.
*Aaron- Now I know how my customers feel when I'm talking about shear, uplift, and loads, etc. Oh, I get it, "Insulating Concrete Forms",yeah. We did a 9000sf 2-story one time and went way over budget. The brand of blocks we used had no reinforcement built in, just foam. As a result, we could only go up 4 feet at a time (not the advertised 12'). So, we called the pump truck much more than we expected. The exterior walls took 8 men two months (not less than 2 weeks, as promised). Cha-ching, cha-ching. Lesson: Sub out the ICF part until you have seen enough to feel confident. We also spent more on cleanup, because if the form blows, it blows at the bottom, and truckloads of mud pour out. Thank God this was a cost-plus job.
*I built my basement from them last summer, and wish I'd taken them to the roof. Cost was about the same as hiring a conventional foundation done. I had none of JR's troubles, but I built a simple rectangle that was low enough to pour without a pump. Angles other than 90 degrees could be a headache. I also had a salesman who actually came out to the job and spent two evenings showing my wife and I how to assemble the forms. Find a salesman like that. Pay whatever price he asks for the material, it will be returned many times over by his knowledge. There is definitely a learning curve. If I ever do another ICF job, it will go much faster. Also, I spent a bit of time this summer researching an upcoming FHB article about ICFs. I visited un-air-conditioned ICF houses that were cool and quiet during this summer's heat wave in the NE, and talked with homeowners who claimed incredibly low heating bills. Select your ICFs carefully. Buy quality, and buy good local support. If you don't have construction experience, building with ICFs may not be for you. If you're carpenter who is willing to invest some time learning,ICFs may be an alternative. For the above-grade walls of a house, even the most dedicated ICF builders whom I spoke with admitted that frame is 5% to 10 % cheaper. Wasn't that two of the three little pigs rationale, though? Check out http://www.insulatingconcreteform.com for good information that doesn't push a particular system.Andy
*I am in the prosess now , I bought the Rforms system [4x8sheets of 2" 25psi extruded polystirene plastic tys 8" from edge and 16 on center]. Use 4or5" slump . I will use a super plastisizer in my house walls. we only had one blowout in the basement ,truck driver wet the stuff toa7"+ slump [JUST LOVE TOBEAT THE HELL OUTA THE DRIVERS THAT KNOW MORE THAN THEY REALY KNOW} My system calls for 16ga. steel stud wailers and stifbacks with 1/2" hex head snap tys every32" in the stifbacks set at about 4' centers and abrace at every 8' I now brace every stifback on one side of the form . After the basement pour I am puting a1/8" cable from one side to the other at the top of each corner, 1 cable per side. My hope is this will keep the form from pushing out. On the basement it movedup to 2". With this setup I can use any mix that will flow out of the truck. I used a convayor truck to place my concrete in the basement, and will use it for my walls . Allways use more braces than called for . Use the driest mix you can . Pour at arate of no more than 4' per hour. Reject any load that the driver wets without your permission. Ithink a plastisizer and /or a water replacer will help. If you can have someone else do the work.
*We are GREENBLOCK dealers and installers in Dallas. If only all potential customers where like Andy. Unfortunately this is not the case. We will not sell GREENBLOCK to do it your self homeowners or for that matter contractors that have no experience with ICF'S unless they agree to allow us to help with the installation and concrete placement. People look at these systems and think it's easy just because they stack like childrens building blocks. Anything is easy if you know what you are doing. DON'T BE FOOLED There is a lot to know about ICF'S and concrete. Right now there are over 40 systems on the market. DO YOUR RESEARCH!!!!! DON'T BE OVER SOLD!!!!! Take Andy's advice and you will save yourself a lot of heartache. Here is a starting picture of an 11000 sq. ft. home we just finished in Bridgeport TX. It is on the cove of a lake and is so long we can't get it all in the camera lense. Regards Norman
*Norman , Have any of the ICF houses you bilt been through a tornado ? you seem to have some nasty one in your area. I know of a farm house in Wisc. that is built of large cut stone atleast14" thick that has seen 4 barns destroyed and is still standing. Just wondering how they held up to there wood frame houses.