*
What type and size do you like to use to join stock kitchen cabinets together?
Discussion Forum
Discussion Forum
Up Next
Video Shorts
Featured Story
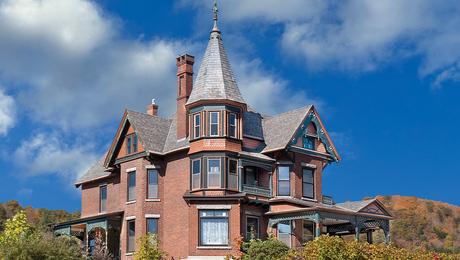
Fine Homebuilding's editorial director has some fun news to share.
Highlights
"I have learned so much thanks to the searchable articles on the FHB website. I can confidently say that I expect to be a life-long subscriber." - M.K.
Replies
*
Sorry, your question is to vague. Are you talking joining the various components together, or joining completed units to each other? Also, what type of wood? MDF, pine, and oak cabinets each require various types of fasteners.
*oak units together. thru the stiles
*we use SS tee-nuts and bolts with SS finish washers..or the sex-bolts that some of the mfr's provide..sometimes we use a few judicious sheetrock screws...we use a lot of SS finish washers in various locations..
*Anyone use Chicago screws ?
*cc - Around here the kitchen installers use those fairly coarse thread gold-galvanized phillips head screws for stile-to-stile and the good ones hide the heads under the hinge mounts, depending on the type of hinging.Jeff
*Me too Jeff..
*I do it exactly the same as Jeff and L. Siders...I have always thought "the less visible the better". If there's a better way I'm willing to listen though
*If the cabinets are dark I screw the stiles together with black trim head screws, but I have to predrill them in hardwoods. I prefer the "s" tip, when I can find them. I use regular wood screws under the hinges when I can. Lots of times I screw through the wall of one cabinet into the wall of the ajacent one with bugle head drywall screws too, if the cabinets are made of plywood. I recently began experimenting with MDF core sheet goods (at the urging of certain members of this board) and that stuff requires special screws, but I think the techniques may be the same. The screws I'm currently testing are maybe 1/4" in diameter and have a blunt point. I have to use a certain drill bit (40.00 frikkin' bucks!) to predrill, but they seem to hold very well. Probably the most important thing to remember about screwing cabinets, to each other - or to the building, is that drywall screws have NO shear strength, so never rely on them to support weight. I just feel obligated to mention this every time this subject comes up. Plates and china and books get mighty heavy, and it doesn't take much of a tremmor to start unzipping a row of drywall screws.
*I've been playing with MDF for a couple of years now and this is the first I've heard of special screws for it. could someone give me a little more detail? (please)BTW Jim I've always used galvanized deck screws to put in cabinets, I realize they're not exactly drywall screws but what's the boards opinion of those.
*I'm goin' in to the hardware dealer tomorrow Steve. I'll find out the name and as much info as I can about those screws. If you e mail me your mailing address, I'll be glad to drop a few of them in the mail to you. They are unique screws, that's for sure. Either 1/4" or 5mm or something like that, with no point at all. Aggressive threads and just the slightest head. The diameter of the pilot hole is critical. My supplier carries them in a couple diameters and several lengths, like for screwing drawer slides to frameless boxes, or screwing boxes together side by side. You've probably seen them and I just didn't describe them well enough. Give me your address, and I'll send you some.About galvanized deck screws, I really don't know, but my understanding is that ANY screw that is "drop forged", instead of cut from a wire, has no shear strength because of the way they are made. I could be mixing up bits of info here, maybe someone else can set me straight. I just know that I had a cabinet unzip right off the wall in a home beauty salon several years ago and the only good thing about it was there wasn't anyone stretched out in the chair at the time (could have been BAD). That, and I started paying attention to manufacturer's suggestions and the UBC a lot more.
*We use brass drywall screws. pre drill with an 2" countersink bit and drive with a 90 degree vspeed or if there is room use the makita impact driver.
*deck screws are part of a family of 'production screws' (industry term as far as I know), which includes particle board screws. Often square drive, hi-lo thread, some have an auger point, and unhardened (that's the difference with drywall screws). And they often have nibs to self countersink. I use deck screws when I get stuck for particleboard screws, and live with the green colour (That's what they are here). I do find deck screws snap easier than a bright P.B screw though, so I use those when I can. As far as joining cabs together, we do mostly frameless. We use 1 1/4 steel P.B screws with steel cup washers. You can get 1 1/8 screws with white heads, but if you crinkle the melamine it looks like crap and you can drive right through if you're not careful. And the cup washers increase holding power considerably. Check out the Deerfield Co. for cabinet screws, and there is another co (S & G? They advertise a lot) that makes a long washerhead screw for fastening to the wall.
*As Jim points out, drywall screws can be easily abused (meaning ab-used) in cabinet applications. I once saw a guy putting up bookshelves for heavy books high on a wall at a day care center with type S drywall screws. Hope it hasn't fallen off the wall on the kiddies (yes, I did ask him about it but his reaction was 'we use 'em for everything.') Jim - have you run into MDF made from recycled materials that includes incidental metal particles? Apparently there are several different types and the type that ends up with recycled staples, etc. is really hard on tools. You can tell from the 'sparks.'Jeff
*We don't screw our stiles and rails together but for screwing together the casework (one to another) we use 1 1/4" black corse thread bugle heads.Ed. Williams
*There are lots of different types; i haven't seen the type you're describing, but you can tell from looking at them if they are made from hardwood or softwood fibres. I'll never willinglly buy hardwood again (it's darker and the surface seems harder). MUCH heavier than softwood. All types get 'inclusions' (bits of metal and stuff); the trade mags run pictures from time to time. One guy cut into a complete nut and bolt.