We are building a new house and want to be familiar with the basic “chain of events” starting with the foundation. Without getting too detailed, can someone please post a basic listing. Thanks.
Discussion Forum
Discussion Forum
Up Next
Video Shorts
Featured Story
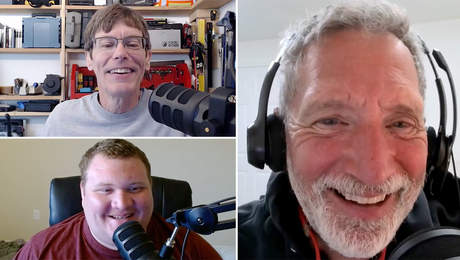
Learn more about the pros and cons of single-room ERVs.
Featured Video
How to Install Exterior Window TrimHighlights
"I have learned so much thanks to the searchable articles on the FHB website. I can confidently say that I expect to be a life-long subscriber." - M.K.
Fine Homebuilding Magazine
- Home Group
- Antique Trader
- Arts & Crafts Homes
- Bank Note Reporter
- Cabin Life
- Cuisine at Home
- Fine Gardening
- Fine Woodworking
- Green Building Advisor
- Garden Gate
- Horticulture
- Keep Craft Alive
- Log Home Living
- Military Trader/Vehicles
- Numismatic News
- Numismaster
- Old Cars Weekly
- Old House Journal
- Period Homes
- Popular Woodworking
- Script
- ShopNotes
- Sports Collectors Digest
- Threads
- Timber Home Living
- Traditional Building
- Woodsmith
- World Coin News
- Writer's Digest
Replies
Are you dealing with a builder or are you intending to contract this home yourself?
A great place for Information, Comraderie, and a sucker punch.
Remodeling Contractor just outside the Glass City.
http://www.quittintime.com/
This is a DIY list, DW and I did 100%:
Read lots of books and scrub the minds of the denizens at BT.
Scrounge garage sales and surplus stores for a few years first to amass (at low cost) all your high pricd items.
Search and buy land with water and perk or sewer in mind
buy some tools
build a few 'no permit' sheds to keep from being ripped off or buy a sturdy trailer.
determine what permits may be needed
buy a dozer and backhoe
clear road and install access
draw up your plans and submit for approval
get permits - road permit, build, septic, plumbing, elec, permission to scratch yourself, etc.
buy more tools
install temporary power
buy lots of extention cords
buy more tools
drill well or install water meter
clearing and grading as required
buy more tools
edit - forgot the sewer hookup or installing septic system.
buy a bigger truck
buy a cement mixer
buy air compressor
buy another air compressor 'cause you forgot to pput the first one in a shed overnight
dig foundation
install footing, incl welding in rebar for concrete encased grounding electrode
Install forms and basement window frames
buy more tools
pour foundation/install sesmic anchors, etc.
install footing drains, etc, asphalt and insulate wall exteriors.
get bids for framing materials from at least 3 (real) lumber yards (not big box)
frame that puppy (this is the fastest and most enjoyable for most DIY)
1/2 way thru framing, buy a couple more nailers
Roof that puppy in asap
install electrical and plumbing
Install doors and windows
2007 - reinstall elec and plumbing as the crackheads ripped off all your copper.
plumb and elec inspections
insulate, seal, and drywall
buy more tools
move in but dont tell the building inspectors in some places<G>, you can finish as you go, by now you need the cash from selling your old house to finish this one
Finish one room at a time, kitchen first, one BR, your choice. Get 2 or 3 rooms finished. move insome crates for furniture.
make sure all to code per firewalls, railing, etc. and get cert of occupancy
finish the rest, install that 3rd bath while you finish that the city wanted $300 more in fees for ....
buy more tools to fully equip the shop
now you are ready to build your furniture.
enjoy
Edited 11/8/2007 10:03 pm ET by junkhound
>buy some toolsThat reminded me of the old days when I was an Apple developer. Someone created a flow chart for the steps in starting a software company.Step 1. Buy T-Shirts.
That's a good list! I might add 'review zoning and bulk regulations' very early on to confirm that no variances are required .... at least that's what I do professionally.
Jeff
Excluding site work (grading, driveway, excavation for foundation, etc.,), I'll take a crack at it (assuming conventional stick building). This is very basic. Depending on crew size and subcontractor schedules, some tasks are often done concurrently, or in slightly different order, and every project has it's own character/timeline based on many, many variables. You can take a look at almost any basic textbook on house construction and the chapters are usually laid out in typical sequential order.
footings, foundation, foundation drainage, backfill, mud sills, floor system, walls, second floor (if applicable), more walls (if applicable), roof frame, roof deck, roofing, house wrap (unless this went on earlier), windows/doors, any remaining interior walls, exterior trim, siding, plumbing/hvac rough-in, electric rough in, insulation, drywall, interior trim/kitchen, flooring, plumbing/electric finish.
There are obviously lots of other things that can occur but I think these are the basics.
where do sewer / water supply typically get brought in? im thinkng after the footings / foundation but before the slab? (in with basement)
Yes, after the footings/foundation and before the slab. If your foundation guy is on the ball, he will place conduits for these utilities to pass through
Be nice to all your inspectors and have them over often to clarify what they are looking for.
Since you said start with the foundation, I'll just add that the most common problem is probably forgetting the ufer ground until the foundation is backfilled and you get to dig up a section of the backfill put in a ufer ground, cover with concrete and backfill again.
The ufer is a perfect example of an inspection that you need to know about, but if you don't know what you don't know, you may not know it.
Good building
Beer was created so carpenters wouldn't rule the world.
A well managed chain of events makes a huge difference in time and quality.
After a survey, staking out the plot, establishing set back lines, establishing the elevations and marking out the foundation hole, the excavators come in. They dig the foundation, put in the septic field (when needed), dig trenches for utilities, often hook up sewer and water, build the rough driveway.
Some jurisdictions will require inspections at different times. We get one before backfilling the foundation, which is normally poured concrete.
There are so many little things along the way that make the job easier if you think ahead. When the excavation crew leaves, you have a backfilled foundation, the grade is final except top soil or sod, you have a good gravel driveway, no mud. Any trucks or equipment that come to the site have easy access.
You need to make sure the elevations are correct and proper drainage is installed. This is one of the more difficult areas for DIYers and it's a place where a mistake is not something you want to deal with. You want to know where the sewer pipe comes in and why, not discover it's at the stair landing or the bathrooms are at the opposite end of the building.
Framing starts. We place the sills, make and place carrying beams, frame the floor, place the subfloor. After the deck is complete, we shoot it with a level and shim if needed and place the lally columns. Once the columns are in place, the concrete slab will go in the basement. Next are exterior walls. Frame, straighten, square, sheathe, cut openings, building wrap, mark out top plate for the next floor or roof, lift, plumb, straighten and brace off. Any necessary bearing partitions are built and placed and either the second floor or roof frame follows.
Once the roof frame is up and sheathed, we put on the exterior roof trim and do the roofing. Bring in any large items like tub/shower units, install doors and windows. Now the shell is dry. We strap ceilings in Maine, 1x3 16OC, build and place interior partitions, stair carriages, necessary blocking, chases, etc. If a second layer of subfloor or underlayment is used, we'll put that down before framing the partitions, unless it's only in a particular room. Interior framing is now complete, time to call in the electricians, plumbers, HVAC, audio subs, chimney masons. Once they complete their rough, another inspection is called.
After the inspection, the insulation contractors do their job, followed by the drywall hangers, drywall tapers. While all this is going on inside, we're outside doing siding, decks porches, etc. or move to another job.
Many of us will differ on the following sequence. I prefer to have the painters come in and prime and coat all the walls and ceilings at this point. They will also stain/paint the trim, doors, etc. Interior doors are hung, baseboard, windows, closets, specialty items, mantle, china closet, etc. Vanities, millwork, cabinets and such items are worked in with the trim as necessary. I like to get the kitchen cabinets in as soon as possible since we often have the tops made. The counter folks can come in and make their templates and we can work on the rest of the trim in the house. I like to put in the finished staircases last so travel is limited. Any paint touch up is done and items like the stairs may need the finish applied.
Once the interior carpentry work is done, the electrician and plumbers come in for their finish, hang lights, hook up sinks, etc. The last subs on our jobs are the tile/flooring/carpet installers. This is also the time that the landscapers come in, lawn is put in, driveway is paved. Things like closet rods, door stops, towel bars are put back. The cleaners come in, do the windows, vacuum up, dust. Final inspection is next, habitation permit is issued and the customer moves in. Nothing to it!
Beat it to fit / Paint it to match
I haven't seen termite treatment after footings or before slab,roughin for plumbing before slab.
ANDYSZ2WHY DO I HAVE TO EXPLAIN TO FRIENDS AND FAMILY THAT BEING A SOLE PROPRIETOR IS A REAL JOB?
REMODELER/PUNCHOUT SPECIALIST
termite treatment after footings or before slab
good point for many areas, PNW has very low incidence of termites, but does have lots of carp. ants.
but the termite question does remind me of the DIY items left out -- 3 more items in my list from 1970's :
1. buy 5 gal of chlorodane concentrate and (even ealier) a 1/2 gal of DDT before it is restricted, and store it in a shed.
2. buy 10 gal of penta concentrate and 5 of creosote before restriction take effect and store in a shed
3. build more sheds, they dont need a permit. Buy all the R12 the auto parts stores are unloading (before EPA regs) for 50 cents/can in early 1990s and store in a shed.
ya still sitting on your r12? i had over 30 30lber's. some sold as high as 700.00,but i just sold my last 2 the other day for 275.00 each. if you have it still i 'd start selling it,because it's getting pretty obsolete in most stuff.
now cloradane i wouldn't part with if i had it. best dang product they ever made,thats whats wrong with it it won't go away.wish i would of bought a couple 5 gal jugs of it . larryif a man speaks in the forest,and there's not a woman to hear him,is he still wrong?
Only r-12 I still have is in the 14 oz cans, about 10 left. Still have a '92 voyager and '87 Blazer that use it, each take about a can every 2 years, so looks like it'll break even by th;e time those vehicles get parted..
I'd'a bought more chlorodane in ('76?), but 5 gal then was about $400, and was still a poor boy at the time. <g>.
Actually scored a few gal. of DDT and chlorodane and Penta at an estate sale a couple years ago, but all was the already diluted stuff.
We ain't got no termites up here, all the pipes, conduit are covered by "utilities". We still put on termite shields, under the sills, when it's a government job, they require it.Beat it to fit / Paint it to match
I like to start by shingling the roof. Eliminates all those other laborious and expensive steps.
Go to the Lending institution.
Sign your life away .
The rest is a piece of cake.
You have some good info thus far. Things vary depending on what the house gets. For example: Crawl space, basement or slab house? Brick or siding? Painted siding or vinyl? and inside: Vinyl kitchen/bath floors or tile? Prefinished flooring or site finished hardwood? Etc, etc, etc.
Anyway, take a look at this recent thread which covers the last half of the process:
http://forums.taunton.com/tp-breaktime/messages?msg=96218.10
Really though, it's such a broad topic and to get more info, it would be better if you asked specific questions. As you have it phrased, it's kinda like "How do you build a house?" :-)
Who is the GC - you or someone else?
Edited 11/10/2007 6:31 am ET by Matt