*
I don’t consider myself an expert but,I think running the plywood horizontally will provide more strenght assuming the edges are blocked and nailed…….for the same reason you run plywood perdendicular to floor joists. When racking forces are applied to walls, the plywood resists it, but under real pressure it really wants to buckle out from the wall.Horizontal would resist that more. The buckling is one reason why proper nailing and edge blocking are important and to create a greater section (modulus) to tie it all together. Whether horizontal or verticle provides a signifacnt difference or not is questionable considering studs are 16-24″ apart.
PE in Tennessee
Discussion Forum
Discussion Forum
Up Next
Video Shorts
Featured Story
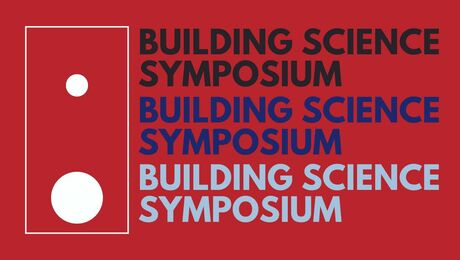
Fine Homebuilding is excited to be the official media partner of the 2024 Building Science Symposium series! This event offers builders, tradesmen, architects, designers and suppliers to discuss topics ranging…
Featured Video
Video: Build a Fireplace, Brick by BrickHighlights
"I have learned so much thanks to the searchable articles on the FHB website. I can confidently say that I expect to be a life-long subscriber." - M.K.
Replies
*
Daved,
Here in earthquake country (L.A. basin) it has always been the practice to shear the walls with vertical sheets, run from at least the bottom wall plate (I like to catch the mud sill on a raised-foundation if I can) to the top wall plates (and again I like getting blocking and ceiling joist ends if I can). That is why so much Struc.I 4'X 10' sheets are sold around here. One of the keys is, of course to use wide sheets. Anywhere you rip a sheet down to 32", 24", or, heaven forfend, 16" you have weakened the structural strength a bit. It seems that engineers here have gone nuts with structural strength these days, giving us these insane amounts of welded iron and hold-downs all over the place, and anchor bolts on 12" centers and lagging bottom plates down at 2" centers. After the Northridge biggie I had no failures to any of the structures I had built and since then the codes and engineers' specs have gone through the roof. I'm firmly convinced that engineers get kick-backs by the pound from the steel manufacturers.
Anyway, to return to the thread of what you were talking about, if we can't make vertical sheets work we have to block at any joints not broken on studs, so I think that in the end it doesn't matter horizontal or vertical, especially since (I assume) OSB has no grain to it.
There you go....for what it's worth...
-Ben
....and another thing... Why is it called tourist season if we can't shoot at them?
View Image
*
Skip
I live and do most of my work on the west coast of Florida. We run our 1/2" four ply sheeting vertical, nailed 4" oc on the perimeter 6" in the field. Generally, the bottom sheet ties onto the sill plate and the rip is placed on top over lapping the top plates. Soild blocking is required between sheets. I believe this is a hold over from the days when only the corners required plywood for wind shear. We also must use enough strapping that spot weilding the plywood would seem to be a valid alternative to nails.
*Waferboard does not have a grain but OSB does. More of the flakes are "oriented" the long way rather than random. Since shear is predominatly diagonal, the fastening pattern is more important than the direction of the sheets.By the way, OSB is made in sheets up to 8' x 28'. One sheet per wall would be nice wouldn't it?
*Thanks for the info Jake. We are getting a lot more tin in our codes to. Most of it seems reasonable. All foundation bolts must run up through the sill plates which seems like it would be a Royal pain for the masons. Skip ps. Andrew may be interested that You mentioned 1/2" 4ply as he was talking about that not long ago.
*Here's everything you always wanted to forget about Waferboard.... I learned this through the Wafer Board Association, and the Council of AmericanBuilding Officials (CABO). First of all, Wafer Board is the actual name of these panels.They are classified into two groups: 1) Random Wafer Board, graded as R-1, and 2) Oriented Strand Board, graded as either O-1, or O-2. These panels are commonly, although erroneously, referred to as simply OSB (Oriented Strand Board). Indeed, there are two types and grades. Now for the the difference, and where they are supposed to be used. Wafer Board is simply chips of wood (usually Aspen) that are sliced off of a log. They are sliced in the direction of the grain, so as to provide the tree material strength. The chips are dried and sorted according to size. Once separated, the chips are mixed with specially formulated waterproof phenolic resins. They are then assembled into mats, and subjected to 400 degrees of heat, and 650 pounds per square inch of pressure. Wafer Board may have three, four, or five layers (depending on thickness of the panels, and complexity of the forming process). Where the distinction comes in is when the chips are placed for processing. RandomWafer Board chips are randomly placed on both inner and outer layers. The chips basicallylook like they go every which way (north, south, east, and west) These chips are long and thin, and when talking about which way they go, I am referring to long ways. Random is just that. The strands are just randomly placed. These panels are used for general purpose, and have the least amount of strength or fastener holding power. Attic decking, dog houses, filler pieces, etc... are the most common uses of the Random Wafer Board panels. Oriented Strand Board (OSB) has two gradings. O-1 is the best, and the strongest. With O-1, the strands are placed facing the length of the panel. This provides the greatest strength and fastener holding power. O-2 has the exterior (or face) strands facing the length of the panel, but the interior layers are random. This is still better than Random Wafer Board, but not quite as strong as O-1. Both O-1 and O-2 are recommended for sub flooring, sheathing exterior or interior walls, and for roof decking. Just a little FYI.James DuHamel
*James,Thanks for the excellent information. I'm not convinced that running the OSB with the 8' edge plumb is better than running it with the 8' edge level. When fastened properly, I also question that running it with the 8' side plumb results in more anti-racking strength. I'd like to see the data that supports that notion.The only real advantage that I see in running it with the 8' edge plumb, is that if blocking were required, you would have to put in a second row for walls that were taller than 8' ( and that's a whole lotta blocking ).Where are all the "building inspector,engineer" type people when you need them for a little more input on this subject?
*I noticed it -- wasn't it Adrian who'd never heard of even-plied plywood?
*
"In wall construction the face grain of the plywood can be
either be parallel or perpendicular to the studs(supports).
For shearwall action all edges of the plywood must be supported.This is provided by studs in one direction and wall plates or blocking between the studs in the other direction".
Design of Wood Structures
Donald E. Breyer
McGraw-Hill Book Company
*
May as well throw in my two cents... While I agree with Dave that running the sheets with the 8' side level results in a greater section, I'm not sure that in practice this means a structurally superior frame. The part I question is the joints that will be inherent in this method vs. the lack of a joint in a corner with the 8'length placed plumb. No matter how carefully the sheets are blocked, there is still going to be some amount of relative motion between the sheets; it's hard to avoid this with the tolerances that are bound to stack up in framing. With at least one sheet placed vertically at the corner and properly nailed off on the periphery and the field, there is no relative motion other than what will take place between the nails and panel. Whether the lack of relative motion between the panels is offset by the gain in section of having the panels level I'm not sure.... I guess that's one more thing to consider.
Sam
*OK folks now I'm thoroughly confused. When using plywood I've never worried about which way it was applied unless specified for the job. This is because years ago I was told each ply has its' grain changed 90 degrees from the preceeding ply. So, even if odd plyed the effect of grain is minimal. Plus the glue provides substantial strength. Was I misinformed,or have things changed?
*Fred, Put the grain issue off to the side for the moment and just imagine the plywood as a solid member with odd dimensions (4' x 8') fastened to the framing. Next, ask what effect those dimensions may play with regard to the strength, shear ability etc. when fastened to the framing in one direction or the other. Gradually remove fasteners from one edge or another and visualize how that affects the wall with regard to shear. Sam
*Remember that ply does have grain but it is of little importance when the panel is not laying down where someone will step on it. The sheer strength of a panel is virtually unchanged. We usually run panels horizontally. But change direction at the second floor so as to get a good lap and tie the building together. Blocking adds to the uplift strength of the panel.Rick Tuk
*I should add that traditionally the plywood is oriented whichever way will include the most framing members. For example, putting sheathing longway horizontal includes 5 studs(24") where putting it longway vertical only includes 3 studs. Whether this really makes a difference I don't really know because when using something like T1-11 it is always vertical and seems to do just fine structurally even though it includes a smaller number of studs. My confusion came because I understood this thread said plywood's strength changed with its' orientation as installed.
*
Fred;
The 8 foot side of the plywood should be run perpendicular
to the framing members it will be attached to, because the plywwod has two more plys running the lenght of the sheet than across the sheet. Osb without grain makes no difference
except on shear walls. Inspectors in our area make us block walls if we lay the osb on its side also, so I stand it up.
brisketbean
*
Dallas it sounds like we had the same teacher. We always bring the plywood down to rim joist. Also on multi story we lap the plywood between the first and second floors. We also use the trick using rubber/felt strips in plywood joints to protect the shell inside from wet weather.
*Brisketbean: Well I guess which direction has the most plys depends on whether the sheet is even or odd plyed, I've seen both. Of course T-1-11 is plywood and it is almost always placed 8' side parallel to the framing members(studs).When I said traditionally that was because that is the way I was taught, and "of course" that is right, right? I see it done both ways so maybe this is one of those discussions about a difference that really doesn't matter unless the inspector has a preference you have to satisfy.Until this board I didn't know anybody didn't overlap the rim joist.
*Gentlemen. Regardless of plywood orientation: horizontal or vertical, a plywood sheet fully supported at all edges is always stronger than a sheet with some edges unsupported. If there is no blocking installed at the 4 foot mark, the sheathing is stronger installed vertically, as long as all edges are supported by solid framing. GeneL.
* Gene,
Joseph Fusco View Image
*Boy has this one been irritating me.I don't think the answer has to do with grain direction at all, but rather with the long v. short dimensions of the sheathing. Racking forces are essentially diagonal across the plane of the wall (picture the bottom corner as a hinge); a 4x8 sheet on its side distributes that force without interruption to a much further point, and thus is a better brace. The proof would be in whether 4x4 sheets affect racking strength if mounting direction is changed. Now, I could check this empirically, but my life is not THAT slow... (though maybe i'll do it anyway)
*I was hopping this thread wouldn't fade into obscurity, but rather someone could come up with a definitive answer. I know some of you don't have to deal with hurricane winds, but then, I don't worry about snow loads. It has recently come to by attention that unless specified by the architect or engineer, sheeting can be installed either vertical or horizonal. And even though we must still fasten our sheeting with 8d nails 4" oc on the perimeter and 6" oc in the field with solid blocking, and overlap plates and rim joist, sheeting is no longer considered a factor for uplift,or hold down. All of this stress has been given to our system anchor bolts, plate tie downs and stud strapping. Even a single sheet of siding, aka $4x8x10$ doesn't count.
*Joe. Does not my #18 post answer your question? In a sheet of plywood most of the shear force is resisted by those plies whose grain is parallel to the direction of the applied force. As previously noted, regardless of plywood orientation: vertical or horizontal, a sheet of plywood fully supported at all edges is always stronger than a sheet with some edges unsupported. In fact Table 23-II-1-1 of the 1997 Uniform Building Code applies "only to fully blocked shear walls." Ergo, all plywood edges must be supported by a minimum of 2x framing. The direction the plywood takes depends on the presence or absence of blocking at the 4-foot mark. Note that these "rules" do not apply to roof sheathing because the sheathing is subjected to both perpendicular and parallel forces. Whereas wall sheathing is usually subjected to lateral loads from high winds or earthquakes.Genel.
*Here's the latest scoop: orientation doesn't matter much unless it's 7/16" plywood or less.According to a P.E. writing in JLC a year or so ago (I found this on the CD-ROM), most of the racking force is horizontal and, as Gene has said, you want the maximum number of plies running in that direction. At 3 plies, the ratio of horizontal to vertical plies is 2:1, a big difference. As the plies get thicker and increase in number, the difference becomes slight.The only hint of this in the Code was suggested by the PE, in the same UBC table that Gene refers to: "This fact is reflected in the Uniform Building Code’s nailing schedule for structural panel shear walls (1997 UBC, Table 23-II-I-1), which permits the allowable shear for 3/8-inch and 7/16-inch panels, if oriented horizontally across the wall studs, to be increased to that of corresponding 15/32-inch panels." I believe that failure to block the horizontal seam would more than erase this slight advantage -- the panel would be apt to buckle with a loose edge. Of course, you also need to nail the heck out of such thin, tear-prone panels. Weak, I know, (the plywood too!) but the best I've seen so far.Incidentally, I was reading a fire-safety article that said where blocking is used to limit the spread or fire within a wall, no gaps larger than 1/8" may be permitted. That's fairly tight, esp. as the lumber dries. Wires and such that will fail in a fire are supposed to be surrounded by intumescent caulk and other compounds that expand when heated.
*Gene,
Joseph FuscoView Image"Whenever, therefore, people are deceived and form opinions wide of the truth, it is clear that the error has slid into their minds through the medium of certain resemblance's to that truth." Socrates
*Winter must be on its' way! Why else would we spend all this time pointing out that plywood orientation as it applies to us is a distinction without a difference?
*I write faster than you think! That's what liberal arts/lawyers do -- words. As for the info, I just stumbled across it while looking into something about framing roofs.
*Joe. I don't see that the configuration you propose changes the rules. If there is no blocking at the 4 foot mark for the horizontally applied pair, then the vertically applied pair is stronger. Note that the code requires that additional bracing must be applied every 25 feet of wall length. GeneL. Good hearing from you. Saw your post on JLC.GeneL
*
According to FHB "Structural panels can be installed vertically, though installing them horizontally provides more stiffness for a given panel thickness." According to a 1999 Carpentry book by William Spence, "Plywood and OSB panels applied vertically produce a wall with the greatest lateral load capacity. Panels applied horizontally without blocking on the unsupported edges have about 75% of the capacity of the vertical panels. If they have two-inch blocking on the horizontal edges they have the SAME lateral load capacity. Walls braced with panels on each end have about 40% of the lateral load capacity, and those using let-in diagonal bracing have only about 10% of the capacity of vertical plywood or OSB panels." Joe, why is your writing always blue?
*
Reno,
Joseph Fusco
View Image
* Gene,
Joseph Fusco View Image
*
Yes Joseph, that is indeed quite interesting. I will ponder that over a spot of tea.
*
Reno,
Joseph Fusco
View Image
*
When I started framing in New England all the framers ran the plywood sheating on the walls with the 8' side level. Now I frame in Colorado and everyone runs plywood or OSB with the 8' side plumb. I am pretty sure it was code in MA to run the ply. horizontally.
The framers in my area run the sheathing with the 8' side plumb. Most block all the joints. Some cover the rim joist and others go to the rim. If it works out better near the tops of gable walls they change direction.
I have talked with the building inspector and he told me if I run the ply or osb horizontally I do not need to block the joints.
On a very large frame we did last year the structural engineer did a walk through and made us block every ply joint. We ran the ply with the eight foot side level.
I have always thought that it was stronger to run ply with the 8' side level. I have converted to sheating with the 8' side plumb because I won't go through that blocking disaster again.
What is the best way to sheath and why???
Thanks for the help.
*Here's my impression -- and I'd appreciate a response to it:Running the sheets horizontal gives you the greatest impact resistance if, for example, you tried to put your fist through it. However, it does result in the problem of the unsupported and leaky horizontal gap that may or may not need blocking. Running the sheets vertically, on the other hand, gives the greatest anti-racking strength. So choose vertically.As for the rim joist, some here believe in lapping it to improve overall connection strength between the levels, others contend that rim joist shrinkage as the damp lumber dries will cause buckling.
*daved,I prefer to run it vertically with all edges blocked. It does take a few more nails etc but it gives you a very tight shell and makes alot of the things we argue about on this board, felt vs tyvek etc. academic. I'm of the opinion that seeing daylight streaming through the walls of your newly sheathed house is a bad thing. Others may disagree.JonC
*I don't consider myself an expert but,I think running the plywood horizontally will provide more strenght assuming the edges are blocked and nailed.......for the same reason you run plywood perdendicular to floor joists. When racking forces are applied to walls, the plywood resists it, but under real pressure it really wants to buckle out from the wall.Horizontal would resist that more. The buckling is one reason why proper nailing and edge blocking are important and to create a greater section (modulus) to tie it all together. Whether horizontal or verticle provides a signifacnt difference or not is questionable considering studs are 16-24" apart.PE in Tennessee
*Horizontal probably works just a well for me if its blocked. Built several shops with 8'+ walls and one run went horizontal in those. Anything here over 10' requires fireblocking but I'd block all edges anyway. Those shops quite often never get finished inside around here and thats where I learned the importance of a tight shell. As long as light doesnt come through the sheathing I'm happy.JonC
*I don't think i makes a ton of difference either way. Running it horizontally does connect your rim joist to your wall quite well. The horizontal sheets provide less racking strength this way, but it's certainly enough for residential construction. My contention with current construction practices is that holding it b downis the biggest weakness. The connections between the foundation and the floor system, the walls to the floor system, and the roof to the walls generally aren't all that great. This area could use a lot of improvement.
*I was always taught to run the sheathing perpendicular to the walls and always take it down to the mudsill past the rim joist. The reason for this is that you don't have an 8' joint in the sheathing anywhere which can weaken the wall structure. You always stagger the 4' joints at least two stud spaces away, and fold in a run of rubber roof flashing when you stack on the next sheet up. I was taught to also install a run of rubber sheet flashing across the face of the rim joist and let it fold out over the brick ledge. This method just seems to tie the whole wall structure to the joist underpinning together really well, and creates a tight and strong skin with no continuious breaks in the sheathing from top to bottom. Blocks at the joints between studs is optional. We always add a row of fire blocks anyway. These blocks can be placed at that joint if you want. Most of the walls we frame these days are 10' and up. So we usually don't fire block at the sheathing break.Ed. Williams
*Daved I am on the coast of North Carolina and hurricanes have had a significant effect on the building coodes here. In most areas the sheathing is run with the long side level.The bottom sheet overhangs the plates and the top sheet goes to the top of the plate. This results in a gap in the middle which is filled with a rip and the two joints are blocked solid.. It's overkill until the wind kicks up then it suddenly seems quite reasonable.Fortunately it is code so everyone is on an even playing field. OSB is not allowed in some areas. But You probably don't get many hurricanes out Your way. Anyone from Florida reading this? Skip