In my area sheetrock hanging and finish is normally bid by the sq. ft. of wall board used and wasted instead of the actual sq. ft. of walls, is this practice normal in most areas?
Discussion Forum
Discussion Forum
Up Next
Video Shorts
Featured Story
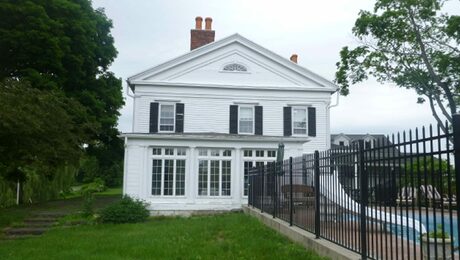
Listeners write in about attics, foundations, and dodgy electrical devices. They ask questions about trusses, wet ceilings and siding installs.
Highlights
"I have learned so much thanks to the searchable articles on the FHB website. I can confidently say that I expect to be a life-long subscriber." - M.K.
Replies
Yes. Well it is here in MA anyway.
Here its by the # of boards used, regardless of waste.
King,
Here too in Minnesota. One guy doesn't do that but charges a high enough premium that it comes out the same..
Yes
We pay by the board... So it's pretty much the same thing. What's worse, assuming you (the builder) are supplying the board, if you over order on the board, they sometimes just cut up the extra and throw it out the window with the rest of the scraps... :-( Also one hanging crew can be more or less efficient than another. Regardless of who is hanging, there are always some big scraps. One strategy is to let them run out just shy of completion, let them scrounge, and then get a few more sheets (if necessary) to the job just before they leave.
Re paying by the sq foot for the material used (including scrap) it's that way with most any finish material: flooring, siding, carpet, roofing, bricks, etc. OTOH, it's not like I see too many people (if any) getting rich doing it.
yes it is
In my experience on the west coast (Seattle, Portland,S.F., L.A.), yes, by the sq. ft.
The builder most always purchases the board in my area and the hangers waste tons of it as they are being paid by the amount of board purchased. I was thinking about making the hangers and finishers bid the job by the actual sq. ft. of wall. to cut down on waste.
>> I was thinking about making the hangers and finishers bid the job by the actual sq. ft. of wall. to cut down on waste. << The only way you are gonna cut down on waste is to get a turn key job (they supply everything). Even then, there will still be a fair amount of waste because the workers don't really care how much the boss man with the new truck makes... They still get paid by material used. They have hungry mouths at home and they aren't making a lot to start with. So, their boss man will just factor it into the price, plus you pay a premium because he has to put up the money up front to pay for all the materials.
Really, you don't even necessarily want very efficient use of the board, because then you end up with a bunch of smaller pieces patched in.
Here is your best advice: make your takeoff and board delivery very accurate. The best way to do that is to actually measure the framed house. A measuring wheel works great. Don't subtract out for windows and doors. Add in a waste factor. The ceiling material can be taken right off the plans. If you under-order, you will have a schedule delay which equates to $$. If you over-order you will have more waste. To me, the best of both worlds is to be 2 boards short - then when they start running low, they will use some of the big scraps. But be right there when they are in the hanging finish up stages so you can run to the store real fast and get the last 2 boards before they walk off the job. This is PITA for you though. Don't let them run out on the 2nd floor though, as it may be a big hassle getting it up there.
The unfortunate fact is that certain aspects of construction generate a fair amount of waste. My trash people (whoever I'm using) are always specific about drywall trash - their contract does or does not include drywall trash - indicating that it is always a big hitter. Unless I just pay by the load, and then trash removal is even more expensive.
When you are getting your drywall bids, be specific about who removes the trash too. One of my drywall guys does, another does not.
My drywall guys price by the board. Rather than actually measuring the rooms, they just walk around and count how many 12' sheets it will take. No allowance is made for doors and windows. When a sheet goes up over a door or window, you try to avoid any joints going directly up the sides, which will crack later. In essence, the sheet goes over the window, the window is cut out and that piece becomes waste. Just about any piece that is less than full width gets tossed. To a non-professional, throwing out all those 3' x 3', and sometimes larger pieces, seems like a waste of material. The real cost in doing drywall is in the taping. Patchworking a bunch of small pieces will cost far more than just tossing the cut outs. In addition, we try to eliminate unnecessary joints and those that may be in a position that will show in the future. Unlike many other trades, there isn't much difference in pricing between one company and another. The big difference is the finishing and how well they clean up after themselves. Don't sweat the waste factor, it's actually saving you money and ensuring a better job in the long run.
Beat it to fit / Paint it to match