We just received a change order of $848.88 to put pine base shoe on our 1700 sq ft ranch. The reason we need this now is because of uneven floors and wavy walls. Is it appropriate that we eat this when it was never part of the original bid?
Our move in date was December 20th, 2005. There are many days when there is only a crew of one working, so don’t have much inclination to pay this bill request. If there was a light at the end of the tunnel, it wouldn’t be a problem. What do you think?
Discussion Forum
Discussion Forum
Up Next
Video Shorts
Featured Story
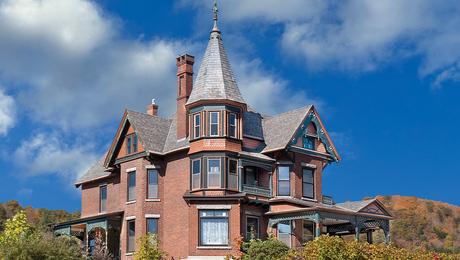
Fine Homebuilding's editorial director has some fun news to share.
Featured Video
How to Install Cable Rail Around Wood-Post CornersHighlights
"I have learned so much thanks to the searchable articles on the FHB website. I can confidently say that I expect to be a life-long subscriber." - M.K.
Replies
As you say... it was not on the original bid. Did you ask for the change ?
That's what a change order is... A change or addition to the original bid.
If you asked for the change order, and the job was done in a satisfactory manner... Then pay for the change order. Period.
The destination is not the point. The completion is not the point. Enjoy today. If you can't enjoy today, then what is the point ?
Ditto Luka.
Doesn't matter if it's $1 or $1000. If you agreed to it, then you pay for it.
But ... if shoe mould is not on the plans, and they truly did install it to cover other sloppy work, then maybe it's time for a little talk with the GC. Why are the floors and walls wavy? Maybe they should correct the defective work rather than add a bandaid.
Any pics of the problem areas?
"When asked if you can do something, tell'em "Why certainly I can", then get busy and find a way to do it." T. Roosevelt
If this is new construction, you shouldn't be paying for anything with uneven floors or wavy walls.
If they can't make what you see right, you can only begin to imagine what the hidden things look like.
What do you mean by "wavy"? Is it a slate floor or hardwood? Too many variables to just say yes or no, but the bottom line is, if you approved the change order, you should pay it. Then, if there are other issues, you can negotiate a charge back or make them fix whatever the problem is. I would rather have them fix it, than take a discount.One thing to remember, there is no wall that is truly flat, it just gives the appearance it is flat. Well, perhaps I shouldn't say no wall, as for enough money I have built one or two for photographic studio backgrounds. You need special studs and extreame attention to detail, certainly not standard house building work.
Edited 4/26/2006 6:45 pm ET by KirkG
Thanks for the input. Let's see if I can answer all of the questions.
- I didn't ask for the toe shoe, but agreed that it was necessary.
- This is new construction in Wisconsin
- It has not been done yet.
- The uneven floors are supposed to be corrected. It is
floating engineered wood over gypcrete/infloor heating.
- Don't know why the walls are wavy. They are mostly 1/4 inch
bowed in or out over a 4 foot level. I'm told this is OK.
- There are many gaps between the base trim and flooring that make
the shoe necessary.
- We definitely would prefer things fixed instead of a charge back
I'm thinking we pay for this, but am a little irked because the floor/trim didn't meet and this is a cover-up.
-
It sounds like the gypcrete was not floated flat. Is the engineered flooring installed? If so, it would be a fairly big deal to remove it and fix the problem. I would suggest that if the problem was caused by poor building practice (it sounds like) then the builder should cover the cost of the shoe. I wouldn't make them tear-up the floor though. Floating concrete product perfectly flat is pretty hard to do. Having said that, I aim to get the concrete flat at the walls at least just to avoid this problem. Most important, talk to your GC. Keep communication open. Have HIM explain what the problem is - there could be more to the story than we on the forum are seeing.
Sounds pretty awful. I wouldn't expect to be able to fit a playing card in 4 feet of a wall. There is no excuse for the base to not fit the floor evenly.It can only get worse. Things do move as a home ages.
Sounds pretty awful. I wouldn't expect to be able to fit a playing card in 4 feet of a wall. There is no excuse for the base to not fit the floor evenly.
A playing card? I suppose you skim coat all your interior walls with plaster that is knocked down with a 10' straightedge?
Jon Blakemore RappahannockINC.com Fredericksburg, VA
with a 10' straightedge?
world's longest custom made Darby...Life is not a journey to the grave with the intention of arriving safely in a pretty and well preserved body, but rather to skid in broadside, thoroughly used up, totally worn out, and loudly proclaiming<!----><!----><!---->
WOW!!! What a Ride!<!----><!---->
Forget the primal scream, just ROAR!!!
This scenario sounds insanely like the contents of the book "House". That book drove me crazy....... Everyone who ever plans to build a house should read it.
Semper Fi
"A playing card? I suppose you skim coat all your interior walls with plaster that is knocked down with a 10' straightedge?"When doing real lime plaster I use a 8' screed, for drywall just a 14" trowel like most. There is no way I'd ever signoff on 1/4" of wave in 4' feet of wall.This all goes back to many other complaints mentioned here about subs doing poor work.Call me old fashioned but I expect floors level and even with walls straight and plumb. I always thought that's why I was hired instead of the home being a DIY project.I'll give you 1/4" margin for foundation elevation difference in 80-100' and that's the only place I'd expect an error that large.
You're Hired!
There is no way I'd ever signoff on 1/4" of wave in 4' feet of wall
I just pictured that--that's half a sheet's thickness bowed in just half it's length. I'm thinking if I saw a sheet bent that much before installing it, it'd get a double take.
So, now, I'm having a bit of a muddle imagining what sort of wigglesticks are masquerading as the wall studs (hey, doan woory, iz jus' a partition wall--can't see it fr'myhouse . . . )Occupational hazard of my occupation not being around (sorry Bubba)
- I didn't ask for the toe shoe, but agreed that it was necessary.
Ok, how did that conversation go? "Mr Raymund, this here floor is wavy, and it makes gaps under the base, so the only solution is to add some shoe mould. Now don't you agree that the shoe would look better than the gaps?" And so you agreed that it would look better, and he did it without first telling you it would cost more.
It has not been done yet.
Tell him to make the floors level, and the walls straight, and he can omit the shoe.
They are mostly 1/4 inch bowed in or out over a 4 foot level.
The only time you would see that much bow is if the wall is short and the level is riding on the fat corner bead. But even then they should have floated it out a foot or so.
Sounds like a hack job. Pending pictures, of course.
"When asked if you can do something, tell'em "Why certainly I can", then get busy and find a way to do it." T. Roosevelt
Putting shoe mold at the floor wall intersection on engineered wood floor (or most any other type of wood floor) is standard operating procedure. The shoe mold is nailed to the wall so that the floating floor can do just that. The addition of the shoe is used to cover the base/floor gap. This is because the base mold is not flexible enough to conform to variances in the floor although the floor should probably be within an eighth.
The 1/4" wavy wall in 4' sounds pretty standard too.
So, I guess the only thing in question is weather whatever contract is in place included the shoe mold. Our contracts don't specify, but shoe molding is assumed and provided "free".
Edited 4/27/2006 7:32 am ET by Matt
I'm curious, did the flooring supplier also install the floor? Who chose them, who hired them?Every floating floor I've been associated with had it's own pre-finished shoe and transition pieces, and was supplied and installed by the flooring folks as part of their package.I'm a trim subcontractor, and installing shoe on hard flooring surfaces is always part of a bid, unless specifically requested to be excluded.I'm also a gc, and the flooring companies I have used always ask about shoe before they price.I'm not clear on your change order status, anything signed?And, if you don't mind, how are the wavy floors going to be flattened? I need a dump truck, baby, to unload my head
Expectations:I'm not a pro builder. I am a pro custom (high end = $$$) furniture maker. I remodeled my own house, early 80"s vintage, ranch, standard floor joists, and studs. This house was originally built OK, but not great. I put heat into the floor using sleepers and gypcrete in between. I did the install of my wood floor, this was the first and hopefully last, floor I've ever done. I need a shoe, but just barely. I took the time to get the floor straight. I don't have any gap over 1/8" and most are less than 1/16. If you have a worse condition than that, I'd say your buider is a schmuck.Walls..... I did my own drywall work (I'm crazy, I know), smooth, no texture. I am not a drywall guy, just someone who can mimic one for a spell. My walls are very flat. Remember, these are old stud walls. There are no 1/4" gaps in 4'. If your walls are that out, then your builder is a schmuck.I wouldn't pay him for this extra to cover his own ......
Thanks to all for your replies. Here's a few updates. - The builder had his carpenter install the floating floor.
- I heard the architect tell the carpeter to add 1/8" of something
to the valley in the flooring- I'll ask tomorrow what it is.
- Today, we were told that deadbolts on exterior doors are not
standard- if we want them, we'll be billed approx $800. There
are 4 exterior doors.
- Did I mention that in the hallway to the garage I could slide my
notebook between the trim and the floor? This is the worst spot.I appreciate all of the input. I'll make my decision this weekend- it'll probably be to pay the bill and set up a meeting with the architect and builder. The main goal is to get a well built home.
I dfisgaree on the need for shoe mould with laminate floor in a new house. The standard base should have been held up high enough for the flooring to slip under, and it would have provided more than 1/2" expansion room.
$800 sounds a little high for 4 deadbolts. Unless the doors are not already bored, then it's not bad. Figure $50 for the lock and an hour to prep the door and install. But check the drawings or specs. I would be surprised that they did not include DB's on the exterior doors.
If the flooring is already installed, how are they going to add 1/8" of anything to the low spots?
"When asked if you can do something, tell'em "Why certainly I can", then get busy and find a way to do it." T. Roosevelt
So, you are saying that the base can be installed first at the correct height and then the engineered hardwood floor could be installed afterward and a perfect or at least acceptable fit could be obtained through-out the job so that shoe molding would not be required? Mind if I have a hit off that crack pipe you are smoking?
You make good points about the dead bolts though.
I would think that if the doors were pre-bored for deadbolts, that would mean that the builder was aware that deadbolts were included and there should be no extra charge. If the doors are not pre-bored that means either that the builder planed on deadbolts not being installed or maybe it's the builder's first or second house.
"we were told that deadbolts on exterior doors are not standard"
What the architect was actually saying was "I forgot to spec for deadbolts". I don't know, maybe in some parts of the country that's the case, I'm just having a hard time believing it. Might want to confirm those are actually exterior doors while you're at it!
i wonder why the carpenter didn't scribe and then plane the baseboard to fit the waviness of the floor...ESPECIALLY if he knew there was no shoe mould...one should be able to get everything looking perfectly joined without using the shoe mould.
"I hate quotations. Tell me what you know" Ralph Waldo Emerson
You said:
i wonder why the carpenter didn't scribe and then plane the baseboard to fit the waviness of the floor...
Because that would have cost just as much in labor as it would for the labor and material to install shoe mold. Further, that would mean that the damage prone engineered floor would need to be installed before the trim, which would also mean that all the priming and initial painting would occur after the perfinished engineered floor was installed.
With the latest posts, I would suggest that you hire another contractor to come out and check the standards of the construction. It sounds like there is more to this project than just a little base shoe. Have them review the construction documents, contracts, plans with GC and Arch and then review the work done so far. Once you have that info, you will be in a better place to decide how to proceed.
Your update raises more questions than it answers.
- Today, we were told that deadbolts on exterior doors are not standard- if we want them, we'll be billed approx $800. There are 4 exterior doors.
How do these conversations happen? Did they they just casually mention it you? What would have prompted that? Did you bring it up? Why? What's on the blueprints? Are the doors pre-drilled for deadbolts? Which deadbolts are being installed? How much do they cost?
- Did I mention that in the hallway to the garage I could slide my notebook between the trim and the floor? This is the worst spot.
What is a notebook? Why not just measure the gap? And by "trim", do you mean baseboard?
Maybe the ultimate question here is: Do you trust these people?
If you do, then all of these speculations are pretty academic. If you don't (which is what it sounds like), then maybe you had better bring in an objective 3rd party.
-Don
Thanks again to all for input. Had a good talk with the builder this week and are back on track. You bring up a good point about trust. I think we have good people working for us, so have decided to stop stressing about it,(the best I can). Our main concerns were addressed and corrected in the past 3 days. Now we're just looking forward to moving in and throwing one BIG post-construction party! Have a good weekend!
Hey all, I've been trimming sub standard houses for a while. The builder is reputable but his walls and floors are terribly out of level, plumb, flat , etc. I personally take the time to make things fit these adverse conditions and make the best of the situation for the customer. If shoe molding is on the plan I don't scribe to fit. If no shoe is planned I scribe the base within a 1/16" . For stain grade trim I will even float the walls at the base here and there myself as well as some belt sanding. All this may be why I make so little as a sub but the customer deserves my best regardless of those before me. This is the reason for me moving away from subbing and taking control of my own projects start to finish. From that perspective the GC (realizing a shortcoming in his plan) should come to you honestly and say "listen, we installed the base before the laminate floor to protect the floor. however the base doesn't meet it well in spots. I feel terrible about how it turned out. I would like to put down shoe molding to help this issue but I am already tight on the budget. can I split this with you?" Honesty has always paid off for me with good referals. No one is flawless, no job is perfect, so long as all involved care you should have a well built home. Good luck, call the gc on your concerns but be human about it without being unfair to yourself . hopefully he will bend a little. good luck
Has anyone mentioned in this thread that the flooring manufacturer expects a very flat floor, and a "notebooks" worth of a lowspot will stress the product, and causes squeeks and gaps. It needs to be level.
And if the floor is that low, there is no way to attach the moulding if it is below the original base, abnd why is the base on before the floor anyways?
I think this guy is going to suckered if he does not hold firm on these issues.
"The builder is reputable but his walls and floors are terribly out of level, plumb, flat , etc."I never understand a statement like this.Reputable usuallyu means that he deserves a good reputationm by reason of the quality work he turns out.
But in a case like this, it is obvious the only reason any kind of good work comes out of his outfit is the attention you give to covering up his defaults. His only reputation deserved is one of poor quality when he allows the framers top throw away their levels and squares!
Welcome to the Taunton University of Knowledge FHB Campus at Breaktime. where ... Excellence is its own reward!
I thought the same thing. A reputation of building crooked non level houses I suppose. DanT
a quick note about the deadbolts. Standard practice here because often homeowners feel uncomfotable knowing that the builders(and their crew) had keys and an oppertunity to copy the keys. Still you should have been informed______________________________________________
--> measure once / scribble several lines / spend some time figuring out wich scribble / cut the wrong line / get mad
Raymond.
Wavy walls to the tolerance you mentioned are simply a fact of life.. I know some carpenters will take extrodinary measure to make walls appear perfectly flat, however once the house goes thru a heating season or two the wood will warp and weave under the drywall and what was once flat will now not remain flat.
It's the nature of wood.
If you'd like I can elaborate on the subject. In the future if you don't like the effect wood has then don't build with wood.. there are plenty of other products out there that don't have these limitations. Steel studs or ICF's or SIP's for example..
Back in the old days when a plaster coating was put on the walls the plaster could compensate for the inevitable bowing and twisting that happens with wood studs.. usually the mass of plaster was enough to force the stud to dry straight.
With cheaper sheetrock it simply conforms to whatever the studs decide to do..
I have used kiln dried material on the last few jobs and it has been great. The problems have been minimized.
My local yard recently switched either suppliers or something on their studs. The kiln dried stuff they are getting now are as hard as rocks. I had a helper for a few days using box nails to build out a wall, and it was so bad he had to predrill the damn things. That was the worst batch, but in general they are all hard to work with. The last guy I had before that gave up and went out and got his compressor.
I'm almost tempted to go somewhere else, but that would push me to Home Depot and I just don't want to be bothered.
Don K.
EJG Homes Renovations - New Construction - Rentals
What kind of lumber was it that you used?
I know most of what I've had in the past was good old Doug Fir. I will double check tomorrow and let you know.
Don K.
EJG Homes Renovations - New Construction - Rentals
The wood might be Western Hemlock....very hard when KD.
Douglas Fir is the only thing they would let us use where I lived. It takes a good nail gun to drive the nails.
I checked the stamp. It is Doug Fir. I was amazed it was #1 and better. Still too many knots for my liking. As far as the hardness, I've used plenty of DF, I enjoy hand nailing so that's the way it was usually done and it was never anywhere near this tough. I know some of what I got in the past was wet, not kd.
Don K.
EJG Homes Renovations - New Construction - Rentals
In the south east US using other than KD is unheard of - except for maybe for a tractor shed or other farm building. The KD is all "SPF" (spruce/pine/fir) or maybe some SYP (southern yellow pine), although lately we have been seeing, some european studs, that I think are from Denmark or something - they cal 'em euro-studs I think it is. Who knows what they are....
Edited 5/2/2006 7:13 am ET by Matt
I am a custom builder and installation of shoemold or base shoe is always a standard when using tile, hardwood, vinyl, or any type of hard floor covering. We call these hard floor areas.
In our installation of wood floors, we have sometimes installed a true 3/4" x 3/4" 1/4 round. The 1/4 round can be stained to match the wood floor, or painted according to HOs selection. This is standard with no extra charges or change order. It is also stated in our original specs when submitting our original bid.
Wavy walls and uneven floors in a new home? Builders fault. If he has not included shoe mold or 1/4 round, and plans to cover his faulty work and charge you....do not pay. If you asked for the shoe mold and 1/4 round ask him why it was not included in hard floor areas.
It is my opinion and practise, that just as a doors gets casing, and a Pantry gets shelves, hard floor areas should get shoemold or 1/4 round that is included. This should not be a gray area that is undefined and subject to additional charges. Others may differ in opinion, but I believe it is part of building a good home.
To finish a wall / floor junction with baseboard only, the baseboard would typically need to be installed after the floor covering. The only cases I have found / seen this practised is with cheapo corner cutting builders, DIYers and inexperienced non-professionals. I would not consider omitting the shoemold in inexpensive rental properties.
The deadbolt deal sounds like BS, but what are the details? What was in the specs? Our specs detail each door with "Lockset ONLY" but mostly "Lockset and Deadbolt". Lockset ONLY is rare and must be requested by the HO, otherwise they get deadbolts.
A gap that should be tight and is big enough for a notebook, sounds like an problem that needs fixing no matter what size notebook you used. Finding things like this would cause me to throughly examine the rest of the home.
I think you have a case for debate with the builder.
Edited 5/2/2006 10:49 am ET by txlandlord
Hey TX,
Just one place you might not see shoe is when the designer, architect or homeowner specifically doesn't want it. Then the base needs to be scribed to the floor. I do this on kitchens and sometimes when the trim details are very modern and square edged and minimal. I know this is not the standard situatiosn but just food for thought. later
Yes, I have seen some of the style you describe, but never been a participant.
I can see your point. Custom home? No shoe? OK.
I just finished a house with no shoe, and no, it wasn't all carpeted:-)GC tried to get me to agree it should be a wash between scribing base and running shoe...try scribing 16' of finger jointed, stiff and kinky stuff...then try washing it.HO tried to help: the base had a roundover on both edges, he ripped one edge...at a negative (to our purpose, maybe that's positive) bevel, oh, thanks.Floor finishers had a good time, too.I can see it as a look, but it's a costly one.I dunno, seems like shoe's de rigeur for a reason, but that could just be me<G> I need a dump truck, baby, to unload my head
Maybe it works in some cases like hvtrim's modern look, but it is always a standard with us.
What state are you in? I know where my license is that the public has a way to compalin about the work of anyone licensed or unlicensed.
If this over hardwood floors or vinyl (or anything but carpet), it should have been in there to begin with. Then, the question is who provided the design and specifications?
If you did, then it's your oversight. If the architect, builder and/or designer, then it's their fault. But really, the contractor should have forseen this need.
And (especially) what everyone else said.
Its hard for anyone here to determine if you should pay the bill without knowing what kind of arraingement you have with your contractor.
Is he the GC or are you assuming that role. If he is, did he give you a "package" price for the entire scope of the project or is he working on an hourly basis?
You said you agreed the shoe was neccessary, at that point did you know it was'nt part of the original scope or did you think the contractor should eat it and why?
and, are you just pissed enough that the project is moving too slowly for your liking that you would'nt mind imposing some kind of penalty on your contractor?
Please be honest
We signed on with an architect who matched us up with a builder. So we have the architect as a go-between.
This is our first and most likely only home that we'll have built. It seems like forever since the project was started last July, and we're getting tired of being patient. It's like waiting for Xmas as a kid.
The house is beautiful- maybe we need to relax and trust the architect and builder, and pay this bill, too.
This is a typical type of question MOST Clients ask during and after a project.See, everyone dreams of a perfect job, wants to be as cost efficient as possible and really doesn't understand the relationship/ dynamics of the two. When they see what their hard earned/ loaned money paid for, it rarely is in line with what they actually imagined.When painting, and ask for price I tell everyone that I can paint a room for $100, $1,000 or $10,000 - all including paint. The $100 job takes about 30 minutes (dropcloth layout, splashing paint on walls directly from buckets and gathering dropcloths into garbage bags). The $10K job takes about 3-4 weeks (lots of dust control, movers, skimming, priming, sanding, priming... ).Once they understand that each price has its pros and cons they better understand where they want to place themselves. You need to do this too. Where on the $ scale are you and your GC?If you went with the cheapest $ then you're going to get the cheapest job - unless the GC is a newbie, wants to impress you and is willing to loose his/ her shirt.Life is full of trade-offs. When building a home this point is dealt with many times daily. Look at the big picture - including budget - and prioritize. Once you get your priorities in order, have a discussion with the GC. Maybe you will want to upgrade one feature (the walls) and downgrade another area (kitchen appliances) which could easily be upgraded at a later date.As for the 1/4" high points in the walls (every 8' or 12'), they are a result of butt joints and can be pervasive if a budget crew was used. It could also be a result of lumber drying (random full height bumps). When framing, most do their best to use only straight lumber but we have no control over a 2x twisting, bowing or otherwise deforming when drying.BTW - as someone mentioned earlier - shoe moulding serves a purpose. Not to cover errors, but to manage the connection of where the wall meets the floor. Builders learned that all floors are not even and walls aren't either. Shoe molding is for the visual transition. Many architects nowadays, like to omit the shoe moulding to acheive a "cleaner" look. They are missing the lessons of their forbearers.But, because of this trend, if the shoe is not spec'd out, it is not in MY price/ bid. You want it later? - not a problem, but I am going to charge you for it. If it's free to you, then my family is paying for your moulding. I used to do that to keep things on "good terms" with the Client but it also tended to keep things on "bad terms" at home, so I don't do it any longer. Also, if it is not spec'd then how do I price it? Is it paint grade, cherry, oak, wenge or maple? I can't price what is not defined. Creating allowances only drives up my bid price (others may not include it) and tells the Client and Arch that I am proof reading their decisions thereby setting a precident. Now I am responsable for any omissions errors yet I am not driving the bus.Hope this explains a bit more and is helpful,Frankie>P<!---->font color=#61B2E0<!---->B<!---->/B<!---->/font<!---->—Hunter S. Thompson
from Fear And Loathing In Las Vegas
Sounds like production standards, not semi or custom standards.
But perhaps get another unbiased set of eyes to take a look.
If it's required to shoe it as standard practice" " says the GC then it should be included. If it's cover up for crapola work then NC with a is it acceptable to hide the crapola.
And at the end of the project is this just a push to nickle dime you now that you see the finish line. And if it is take a stand.
And if you are on good terms with the GC/project and this is only a minor incident then perhaps a 50/50 will work.
"Sounds like production standards, not semi or custom standards."I would say it is not even that good.
Did the GC know at the time of the original proposal that you were going with an engineered laminate floor? If so, then he would have known to price shoe molding right from the get go.
If the flooring choices were made after the initial quote, the shoe molding is an expense associated with your choice of flooring and your responsibility.
Terry
As has been said earlier, the builder should have encluded base shoe in the areas without carpet. You never mention the size of your base trim. I find it hard to imagine that the base is not tight to the walls, even with the 1/4" waves in the wall. The only place you might expect to see any gap would be at outside corners and perhaps inside corners if the taper didn't float out the corners enough. Sounds to me like it was nailed with a gun and the nails weren't re-set to pull it tight to the wall where necessary. I would use base shoe instead of quarter round unless you have a tall base and cap. 1/4 round can look way too heavy with most of the thin and narrow base used these days.
You shouldn't have to pay for the full price of the deadbolts either. You should pay anything over a good quality Schlage type deadbolt, (you pay for the upgrade) but deadbolts are a standard item. In many areas they are required for exterior entry doors. Let the architect and builder fight it out, but don't pay for anything before you work who is ultimately responsible for the cost.
I've known of trimmers who pinch nail (meaning they don't find studs, just shoot the nails to the rock at opposing angles to clinch it to the rock. works great till someone kicks it or bumps it with a vaccum. maybe this is what they did.
I'm a little late reading this post, but there seems to be an awful lot of assuming going on.
It's impossible for us to know if the contractor is a nuckle head or a good guy based on what's been posted so far and it sounds like a croud of witch burners in here.
If a piece of base has a huge gap, it's a no brainer that it needs to be fixed and if the GC didn't know about it simply pointing it out would get the problem solved. Perhaps the carpenter who put it up knew it needed more help and intended to come back and tighten it up, or the cause of the gap needed to be investigated, or an inexperienced carpenter put it up and didn't know better, or one of a dozen other causes that happen all the time.
Not all trim carpenters or GCs use shoe over hardwood, and fewer still use it over other flooring materials. Personally, it appears too often, used to save money and combined with base that won't support the shoe visually it just looks cheap. A tight fitting base, scribed to the floor looks better to my eye, and that of many better carpenters, but it can't be had for free. Calling shoe a given in any construction contract because it's standard practice is incorrect and misleading.
As far as sheetrock goes, there's a good chance that the GC didn't have his guys straighten the walls (plane/shim) before the sheetrock guys came in, and of course the sheetrock guys always claim to check for waves, but in fact rarely do. Once the rock is us, what's the GC to do? This is such a common problem with sheetrockers that we always straighten the walls. The GC should have known better, but other waves are the result of the crappy lumber that is so common now. Combine that with cheap sheetrock and you get what you get.
A common rule of thumb for waves is that 1/16" per foot generally isn't noticable unless there is harsh light, or it's possible to easily sight down the wall. Given that, 1/4" over 4' isn't that uncommon, nor is it that terrible. On one of our jobs I'd want to chew someone's asss, but that's well within the quality standards set by trade associations such as NAHB.
If the trim carps were sharp they wouldn't let their base follow the waves, but we aren't the GC and again, it's well within industry standards for "normal" construction (gag).
As for the waves in the floor, my first gut reation is that the gypcrete was probably poured with 2x stickers placed as nailers for a normal nail-down floor. The gypcrete shrinks considerably (perhaps the "valleys" spoken of by the architect?) and now your flooring either has to free span between the nailers or the low spots need to be filled. If the nailers weren't put down correctly it's impossible to nail down a normal floor so they went with an engineered floor.
Without knowing we're speculating at best. Maybe the gypcrete was put down thick enough to not self level.
Am I the only one that heard engineered flooring and though of how wavy the stuff is all by itself? The thinner and cheaper the flooring, the more waves you'll get.
Maybe it's not the gypcrete that's wavy, but the padding under the flooring.
For the majority of the better builders out there, it doesn't sound like anything that happened is outside the relm of possibility of a normal job. On the other hand, you will generally get more grease as the "squeeky wheel." A GC generally won't fix something that he sees as borderline unless you bring it up.
If it were my project I'd be offended at all the armchair quarterbacking and if the client was taking any of it seriously it would be time for a heart to heart to get everyone on the same page.
As for paying for a change order that was agreed to, if an invoice was one day late I'd stop work completely until it was paid. I take my role seriously and expect the client to do the same. Having said that, the absolute first rule of hiring someone in the construction trades is to agree in advance that a sizeable chunk of change is held back until the job is satisfactorly completed.
Edited 5/9/2006 2:34 am by trout