My wife wants soapstone slab countertops in our new kitchen. I said OK. I have never worked with soapstone but I said OK because I thought I could do it myself. If she wanted granite then I would most likely sub the job out. The slabs come in 69x39x3/4″ pieces. The people at the slab sales say that you can use regular woodworking tools to work soapstone. I want to have an undermounted sink. I was thinking of dropping the sink so the flange is flush with the 3/4″ plywood and then using a flush trimming bit and using the sink as a guide for the roller to cut out the sink hole. I will use a piece of cherry trim to cover the plywood edge under the nosing.
What do you think of this idea? Is soapstone too hard on router bits? Any suggestions? I am making an A frame for my truck bed right now for transporting the slabs.
Discussion Forum
Start out slow. Then ease up.
Discussion Forum
Up Next
Video Shorts
Featured Story
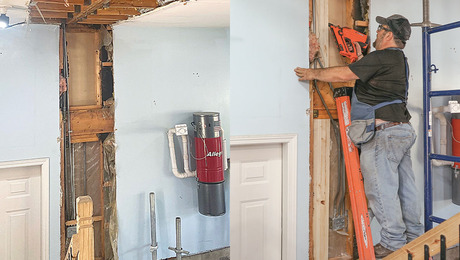
Don't buy in to the TV show nightmares—when you uncover something unforeseen on a remodeling project, take these steps to keep the process moving and fix the issue.
Highlights
"I have learned so much thanks to the searchable articles on the FHB website. I can confidently say that I expect to be a life-long subscriber." - M.K.
Replies
I've never worked soapstone, but I can't imagine using the sink as a router template is a good idea. You'll be throwing around lots of abrasive stuff in the sink, and pushing hard against it with the pilot bearing. Stainless steel is durable but not real hard. I'll bet you'll leave scars in the sink. Instead, use the cardboard template that comes with the sink to make an MDF template, and use that to cut the soapstone. Install the sink later.
You may be right about this not being a good idea, but not because soapstone is abrasive. It's not. In fact, it's the same stuff they make talcum powder out of.
I plan on making a few test passes with the router to see what speed works best and if it even looks doable. We don't have a template because my wife bought the sink for half price from Home Depot Expo. I guess we could write Kohler and send away for a template. The sides of the sink are vertical and as long as I set the depth on the router bit right then it should make a perfect guide for the bearing. The sink is heavy gauge SS and I don't think it would score from the bearing.
I plan on roughing out a hole with a carborundum blade before I break out the router. That way I won't have a heavy piece to break off when I am making the final pass.
Soapstone does mill easily with carbide bits. Your second post regarding roughing out the sink cutout is better, only because you won't now be trying to route through the full thickness of the soapstone in one pass.
I've made sink templates in the past by putting the sink upside-down on a piece of MDF, sticking my hand through the drainhole, and roughly running a pencil around the edge of the bowl. Add a bit for error, and it works well enough for the rough cut. Make sure you orient your template on the countertop correctly before cutting.<g>
If you do end up using the sink as the "template" to run the router bit bearing off of, use a larger than neccessary bearing for the first pass. You might even prefer having the soapstone overhang the inside of the sink by an eighth or so. If you want to go flush, then replace the bearing and go for the flush cut.
Thanks for the input Mongo. The larger bearing sounds like a good idea. It would be nice to have a stone rim for the sink divider. A larger bearing would make the divider a little wider. The divider if flush cut would only be about an inch wide.
Any reccomendations for the type of epoxy for the seams in the soapstone? Would clear "Home Cheapo" epoxy be OK?
Treat the seam just like you would with wood.
Example, put a half-inch straight bit in your router. Space to two slabs about 3/8ths of an inch apart, with the front edges aligned with each other. Set a fence and run the bit right down the middle of the gap, shaving 1/16th off each slab.
The edges will mirror each other perfectly for a nice tight seam.
I don't know what epoxy HD sells, I use West systems. A good investment, the two parts last forever, and you'll find myraid uses for it. Use a filler as well to thicken the epoxy.
I worked in many homes that had saopstone installed. The fabricator we used said he has tried every type of glue/epoxy and has had the best success with superglue.
FWIW, Super glue is more commonly known as CA or Cyanoacrylate glue. I too have the best results with it.
For best results I cut my seams tight enough down their length you cant get a razor blade in it. I then use a thin CA glue and a heptane accelerator (as needed) to penetrate into the seam. I follow up by masking both sides of the seam with tape and applying a medium viscosity CA which I screed off the masking tape with a single edge razor. Look out for gluing your fingers! I always wear disposable gloves. After curing use #2 steel wool to remove any excess glue and create a perfect transition from the slab edge to the glue.
Medium viscosity glue is essential if the seam is not adequately tight. Typical super glue will run out without ever filling the gap.
Try rocklers for different viscosity CA glues and heptane accelerator.
Karl
I use a lot of different polyester resins, two part epoxys and cyanoacrylate adhesives for seams. I havent worked with soapstone personally but my recommendation would be to get some c-cure epoxy grout/mortar with the part b in a color that approximates your soapstone. Get an accurate scale for mixing up partial quantities as the c-cure's smallest quantity is six pounds. I think I pay about twenty or twenty five bucks for that quantity. With this the seam will be very durable and it will look more like a tight grout joint than an invisible seam. Use acrylic paint in very minute quantities if you need to further adjust the tint of the epoxy. There are special epoxy tints I use but I have successfully used acrylic artists paint in a pinch.
C Cure epoxy is great for the joint around the sink as well and I find it is a lot easier to scrub clean than any type of caulking. So far no problems with differential expansion as one material grows/shrinks more in response to temperature changes.
Five minute epoxy is my least favorite choice. Most fabricators choose Akemi polyester resin for seams. I am not very impressed with polyester resin but you might look into buying a qt from Braxton Bragg, look up their website on google.
Karl
good advice! Very astute and knowledgeable!
s2
I have cut limestone with my router and carbide bit and the bit is still good . Soapstone will be a piece o cake.
Be aware that soapstone chips and scratches very easily. I'd go with granite or concrete, but soapstone is easy to work. Recent clients had a soapstone Tulikivi woodstove installed and used the same for counters. Looks good but after 3 months its scratched and chiped. Not pretty.No longer looks pretty in my opinion.
Jonathan
Thank you Karl and everyone for the replies. I googled c-cure and found a local supplier. I like the fact that it comes in colors. Would a few dabs between the slab and the plywood be enough to adhere the slab to the plywood or would you reccommend a notched trowel and adhesive?.
Dogwood, did you locate the Tulikvi dealer in Napa?? I see your in tahoe, and they are suppliers of both slab and 12x12 tiles....as well as the Tulikivi Masonry Heaters and Bakeovens,.
I had the oppurtunity to build one in our showroom and am looking forward to building more. The 12x 12's are easy to work with, as for slab, I've yet to try. Tho I have been told the same, routers and other woodworking materials do fine.
Post pictures if you do. If you want Tulikvi contact info, let me know or online search of course.
one minor detail- the sides of your sink are almost certainly NOT perfectly vertical. check them with a square to be sure. this will have some effect on where the edge of the countertop actually ends up. if the router bearing is down too far into the sink as you cut, you'll get a noticeable lip or overhang. if the bearing isn't low enough, it won't track well on the radiused/rounded upper edge of the sink and might even bind in the gap between the two (assuming there isn't a sharp, more or less square corner at the top of the sink basin). depending on the actual slope of the sink walls, you might do better with one of those tapered (somewhat cone-shaped) bits w/ bearings for mating solid surface countertops with solid surface sinks, but those bits might have too much angle (one good point about these bits is they have plastic covered bearings so they don't scratch). maybe you could rout it to leave a small overhang, then shape/round off/bevel back the underside edge to meet the top of the sink more exactly?
my advice- clamp a few small test pieces to the rim of the sink and experiment. use some five minute epoxy to keep it from slipping, then when you want to take it off just heat it from under the sink rim with a torch just hot enough to pop it off. i use that trick to hold even delicate pieces of jewelry to work on them. or maybe some good quality two-sided tape would work too. my wife and i are planning a major kitchen redo and are thinking about soapstone, but nothing is engraved in stone yet, so to speak.
m
Mitch, All my input comes from granite, marble, limestone, slate experience. I would never try and use a bearing follower bit against the actual sink. To risky and complicated to set up.
Make a 1/4" plywood template and cut/shape it to the exact size you desire. The wood should be a breeze to make minor adjustments to. Then if you are determined to use the router, use the plywood for a bearing guide.
I use a small waterfed diamond saw (4 1/2") and do a rough cut out to within an 1/8" of the template. Then I use diamond grinding drums and silicon carbide stones to get the exact shape. Then I go to 3" sanding drums for final smoothing and 4" diamond wet pads to get the final polish.
If I didn't want to tool up for real production I would get one 60 or 80 grit 4or 5" by 2"silicon carbide grinding stone and put it in a grinder/sander with 5/8-11 threaded spindle and a max speed of 4k rpm. The tricky part is learning to balance a new grind stone with a wheel dresser. If you don't balance it, it will vibrate against the stone and chip the hell out of it.
If this sounds too complicated get a cheap 3" mandrel for sander drums you can put in an electric drill and get drums in 40, 60,120.220 grit.
Hopefully the router will do what you are after but definitely make a ply template rather than using the sink.
Karl
Dog,
I would do as you mentioned and just put a series of dabs under the slabs. I say this without ever having worked with Soapstone so be sure to verify with the supplier. If the soapstone is tile format, I would presume a notch trowel is the way to go.
When you go to mix the c cure, be sure to have it at room temperature or you will have to work way to hard to mix it. Also you will have about an hour or two to work with it, depending on temperature.
I have also used c cure epoxy for the seal between the backsplash and the countertop with no complaints. I know you are supposed to use a flexible seal between the two but the epoxy seems to work with granite.
One job I tore out after discovering a (unrelated) crack had the sink to countertop joint sealed with C Cure. As I was breaking, prying, and pulling chunks of stone up the epoxy actually pulled the enamel coating off the cast iron sink. I would never have guessed that epoxy could have a superior bond to that of the enamel/cast iron.
Final thought on DIY slab countertops is to bear in mind virtually all granite and marble fabricators epoxy steel rods into the stone to reinforce sink and stovetop cutouts. I can't afford the risk of trying to move unreinforced slabs with cutouts.
Be sure to post your end results and tell us what you learned along the way.
Karl
You can't get any better than soapstone for a countertop. I've never worked it myself, but would like to get it for my own kitchen after I hit the lottery. I've seen it worked on some TV show before with carbide bits and it really didn't look to hard. Post some pics when your done, Id like to see how it came out and hear what you thought about working with it...thanks!
I don't understand! I cut it twice and it's still too short!
THe sink is almost square. On my little starrett square, the sink is about 1/16" off of vertical in 4". The angle seems to be consistant around the entire rim. The rim of the sink has a 3/8" roundover. Thanks you for the steel rod reinforcement idea. I may have to dry fit the piece a few times and the steel would help make it stronger. I guess you would make the groove for the steel with a cove bit. If the stone dealer doesn't have steel rods then I can get 1/4" threaded rod at the local hardware store. I plan to measure very carefully. I still plan on using the sink as a guide for the final pass. I will line the edge with masking tape where the guide roller will bear. I will be getting a new computer in the coming week (Another Mac) and I hope to be able to post photos with it.
In granite I just cut two saw kerfs to create a slot for the steel rod. Many fabricators use polyester resin to set the rods. The cheapest most readily availible form of a paste resin is to buy Bondo autobody filler. I use a flowing epoxy but you should probable be ok using a polyester resin like bondo.
If you want to use a flowing resin, you can sometimes find it at surf shops for doing board repairs.
I use stainless steel 1/4" rod but you should be fine using 1/4" allthread. I figure 10 grams of resin per foot of rod as a rough guide when measuring epoxy for a kerf that is 5/16" deep.
It sounds like you have a good perspective on the process.
Karl
Dog, After thinking over your router idea for the sink hole I tried it with a franke sink that came supplied with an inaccurate cutout template for the sink hole in the countertop.
I taped off the sink, used CA glue to tack a piece of 1/4 ply the sink and ran a laminate trimmer around the perimeter. No damage to the sink, a very clean accurate template and quite easy. I did first rough out the hole with a jigsaw.
I would encourage you to do this rather than trying to route the actual stone using the sink as a guide. I am guessing you will need to do some followup sanding to radius the top and bottom of the sink hole so I would say use the plywood template clamped to the soapstone on sawhorses outside. That way you can do any finish sanding, etc, keep the dust under control and not have to lift the stone on and off the cabinets multiple times.
Good luck,
karl
Glad I found this post. The idea to use the sink as a template guide worked out great.
The sink I used, Kindred undermount, had this funky method to make the cutout in the countertop using the supplied male template. The first step called for using a 1/4-inch cutting bit in the router with a 1/2-inch guide bushing to create the female template from the male template - no problem. The second step was to use the female template with a 1/2-inch cutting bit coupled with a 1 9/64-inch guide bushing - what? I checked a couple catalogs for this size bushing and nothing.
So, I taped off the sink as described. Used a 1/2-inch flush bit to make the template out of 1/2-inch ply and used a 1/2-inch pattern bit to make the final cut in the countertop with the female template. The countertop material was Richlite - solid surface 3/4-inch thick so the going was slow, but the results were great. The sink opening mated perfectly with the countertop cutout.
Thanks for everyone's input on this thread.