*
Have to sweat some pipes and I’ve only seen it done. Please correct me where I go wrong here: Drain the line, completely clean and shine the line and coupling, wipe on flux to the two surfaces to be joined, put the pieces together, start heating and add solder when getting hot, remove heat from surfaces when solder starts to flow, wipe off the joint. This is what I remember but am uncertain. I know this isn’t the right forum for plumbing but I read this forum every day and you all seem to know something about all phases of construction. Thanks for your help.
Jared
Discussion Forum
Discussion Forum
Up Next
Video Shorts
Featured Story
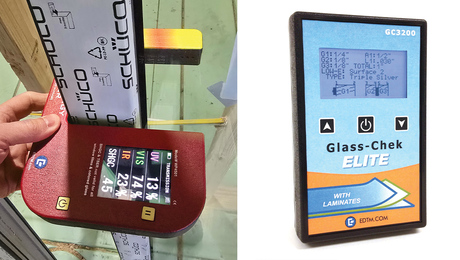
New devices showcased at the Builders' Show make it easy to measure glass performance, u-factor, SHGC, window thickness, and more.
Featured Video
How to Install Cable Rail Around Wood-Post CornersHighlights
"I have learned so much thanks to the searchable articles on the FHB website. I can confidently say that I expect to be a life-long subscriber." - M.K.
Fine Homebuilding Magazine
- Home Group
- Antique Trader
- Arts & Crafts Homes
- Bank Note Reporter
- Cabin Life
- Cuisine at Home
- Fine Gardening
- Fine Woodworking
- Green Building Advisor
- Garden Gate
- Horticulture
- Keep Craft Alive
- Log Home Living
- Military Trader/Vehicles
- Numismatic News
- Numismaster
- Old Cars Weekly
- Old House Journal
- Period Homes
- Popular Woodworking
- Script
- ShopNotes
- Sports Collectors Digest
- Threads
- Timber Home Living
- Traditional Building
- Woodsmith
- World Coin News
- Writer's Digest
Replies
*
Have to sweat some copper lines and I have only seen it done. Please correct my line of thinking here: Drain the line, completely clean and shine the two pieces to be joined, wipe on flux, join the two pieces, use torch to fan the joint until hot, add solder, remove torch when solder starts to flow, wipe joint. I know this is not the right forum for this question, but read this forum everyday and you all seem to know a lot about all phases of construction. Thanks for your help.
Jared
*thats about it except for you only need about a 3/4" length of solder not a whole lot per joint. another little thing i do is after the solder is applied to the joint spray it lightly with water using a spray bottle.
*Apply the solder to the joint on the opposite side of your flame. The flame will draw the solder around the union.
*If it is 1" or bigger, or if it is a cast bronze valve or fitting with very thick walls, make sure you've got enough heat to do the job. Use MAPP gas and a decent torch head or something that will let you get enough heat if you are sweating anything bigger than 3/4". I have heard that wiping the joint when it is hot can pull solder out of the joint and shouldnt be done. Any comments to that? There is always the wonder bread trick - if you can't completely stop the water from dripping and sucking up all of your heat, stuff a piece of wonder bread in the pipe and it will swell and plug things up long enough to make up the joint. I think it has to be wonder bread. 7-grain just doesnt have the swelling capacity. Blow out the pieces after you are done through a faucet with the strainer removed or a hose bibb or something. Of course, they make that jet sweat tool that does the same job more neatly and under more water pressure.One last thing, if you are in the wall with this joint, buy a heat shield or use some hardiplank or durock scraps or something to protect everything from catching fire. Have a bucket of water or a fire extinguisher handy in case something goes up in flames. You will probably have the water turned off while you are doing this and that is a bad thing if the wall cavity starts to burn (been there, done that).Good luck!Sami
*If you are not real quick, the Wonderbread trick won't work (it will start to leak as soon as it gets saturated, then you'll have a leak with bread dough in it!).Even the teeniest, tiniest leak will ruin your joint because the water will absorb all the heat and you'll never get the solder to sweat properly. No matter how much heat you put in there (water is greedy that way - you can boil water in a paper cup over open flame! The paper won't burn until after the water has boiled away. Try it if you don't believe me).If you have this situation, you can practice several times on scrap pieces to speed up your performance before you try again, or you can call a plumber, or you can look for another way to stop the water:Since the valves will be all messed up with mineral deposits after a few years they often leak no matter how hard you turn them. You may not be lucky enough to have ball valves on your supply (the best thing ever, if you've got them!).You still have two more options though. You can try to turn off the water at the street (you need a long special wrench for this, some hardware stores sell these - really long ones if you live in the North), or you can sometimes disconnect ONE side of your water meter and let the water drip into a bucket instead of working its way all the way thru the house and driping on your joint. This option is only possible if you've got one of the old meters that is only sealed on one side or if you want to have the water company come back out and re-seal your meter when your done.In extreme cases the above may be necessary.As long as you remember that no drip is "small enough" to try and solder around, you'll be ok. The pros make it look soooo easy. Thats why we pay them!
*Do be careful about fire! My usual sort of mistake is to forget what's on the other side of the pipe from the flame (e.g., PVC), or to point the flame in random directions after removing it. A fire can smolder for an hour or more before turning into visible flame. I got a self-igniting trigger torch that I like much better. (But someone here wrote about theirs going off when it got squished in the back of his van, starting a fire!)I switched to MAPP out of impatience with propane, but only I got good. It's very easy to scorch the joint, drive the flux out, and oxidize or deform the copper. MAPP will boil more water, but in generally you're out of luck if there water anywhere within a foot -- I usually just cut out a section so I can drain it (it's be nice if pipes weren't laid with hard to drain dead spots). I've heard of using compressed air, too?Don't apply the solder until it flows easily, then apply plenty so that it gets sucked into the joint, while you also remove the heat. The wipe afterwards cleans up the joint, I really doubt you could pull solder out but if your wiggle the joint as it is cooling I can see the joint getting broken. Wiping is meant to remove the excess flux, it is acidic and will eat away the pipe. I've seen a bunch of corroded joints that were still slimy with flux.
*After cutting any pipe or tubing, make sure there are no burrs remaining inside the pipe.I don't heat the tubing...just the coupling...and I let it cool a bit before wiping down or you can (as someone already wrote) draw solder out...worse, you can break the joint. Wiping down will remove excess flux, which is important.Heat the coupling...touch the solder to it. Doesn't get drawn in? Repeat. Careful you don't burn the flux in your first attempts. Take the flame off the coupling when adding solder.Any water remaining in the pipe will defeat a propane torch's attempts to heat it up.I'd recommend a novice dissemble valves if you can, open ball valves if using those, and remove bleed nipples so the little rubber gasket doesn't get deformed from the heat.
*I've never plumbed a house. Only plumbing I do is small amounts, adding fixtures, moving stuff.Haven's sweated a pipe in a long time. Compression fittings are so fast and easy and they work even if there is a trickle of water.
*I wipe joints with a wet rag while it is still above 212F, but to be safe, wait till the rag DOESN'T sizzle before wiping the joint. Wear leather gloves for all the steps. As Mongo and others have said, heat the fitting, not the pipe and when the opposite side is hot enough to suck solder, the whole joint will fill.There are couplings without stops that can slide all the way onto the pipe. This is very handy when doing the last joint on an old pipe run if both ends are fixed. -David
*I have attached a wet/dry shop vac to the (usually with duct tape) and let it run for about 10 minutes. open a facet or two to draw a little air and it will will pretty much clear all the standing water out of the pipes.
*Instead of a heat shield, a while back the counter guy at my plumbing supply house suggested I try a heat shield gel they had. Don't remember the name but you slather the stuff on the wall behind the joint and it puffs up into a protective foam if the flame hits it. To test it, I slathered some on a piece of plywood and then held the propane torch directly on it for quite a few seconds. When I wiped the stuff off, there was nothing but a damp spot on the plywood where I had applied the flame. I was really surprised how well this stuff protected the board.
*Many thanks to all of you for your replys and for the added info that I hadn't thought of. Will be doing this Saturday at my son's house and believe we'll get thru it ok with this info. Will be prepared with all the tips that came in. Thanks, Jared
*Jared, One last thing...Running copper is fairly simple, but there is a bit of a learning curve. I like to cut and fit all my pieces, then I shine/flux/install them. Once everything is in place I then light the totch and solder. Assure that each joint is tight before soldering...sometimes they can work apart when soldering an adjacent joint.After soldering, if you do have a joint that leaks, I'd recommend reheating the coupling and knocking the joint apart. Be careful, as sometimes heated solder can splatter. I usually use pair of pliers to grab the coupling and slowly twist it, while backing it off of the pipe.Let the copper cool, then re-shine the pipe with emory cloth. Toss the coupling...you can clean out the inside, but for 10 cents I'd rather use a new one.Then repeat, improving each time.Once done, take any filters off a downstream fixture and turn the water back on. Let it run for a few minutes to flush and junk out.No leaks? Replace the filters and have a beverage.Best of luck.
*I'm less patient than Mongo; if I leave a leak (never!) I'll sometimes just hack the pipe farther up in a way that makes it easiest to drain. Life is short, pipe cheap, and I have enough little marks from spattered solder. :) So wear glasses, and you'll be thankful for the gloves when you forget and grab a very hot piece of copper. Save the beer for afterwards, or if you drink Mongo's discount stuff use it to wipe the joints.
*This is perhaps overkill for a small repair job, but i like to plumb in a fitting for attaching my air guage. Fill the system with air to check for leaks with soapy water, just like gas lines. Take out the air guage and put in a plug when finished. If you messed up, you don't have to drain again.
*In our area, most house have full basements and that's where the hot water heater resides: usually the tank drain is the lowest fitting in the house and with the water turned off at the meter and by juggling the supply valves to the heater you can drain the lines quickly. I think someone was hinting at using white bread (with the crust cut off) to more compltely dry a short section of tubing. BUT, the most important thing is to make sure you buy the lead-free solder.
*It does need to be white bread. Grained breads contain chunks of grain that can clog any filters/aerators you forget to remove. White bread has a more even texture & consistency, so it breaks down evenly. I have not had a problem with aerators that I forgot to remove, I found it breaks down small enough to fit through. I still reccomend taking off aerators anyway - you're likely to kick up some sediment, etc. when you drain & refill pipes.
*The proper amount of solder to use is equal to the diameter of the pipe. Any more and you will start to fill the pipe with solder and it will clog areortors.
*Reminds me of the time my husband needed to fix the drain under the kitchen sink, so he placed a bucket under the sink, undid the pipe connected to the drain, collected the water, and then... needing to keep things tidy, dumped the bucket back into the sink.We still laugh about it sometimes.
*Been there, done that. :)
*?? does not compute ??
*Always do the lower joint first, heat rises. When you finish with the lower joint the upper joint will just need a little heating and it will be ready. Also the heat from the upper joint will not go back to affect the lower joint.
*
Have to sweat some pipes and I've only seen it done. Please correct me where I go wrong here: Drain the line, completely clean and shine the line and coupling, wipe on flux to the two surfaces to be joined, put the pieces together, start heating and add solder when getting hot, remove heat from surfaces when solder starts to flow, wipe off the joint. This is what I remember but am uncertain. I know this isn't the right forum for plumbing but I read this forum every day and you all seem to know something about all phases of construction. Thanks for your help.
Jared