*
Discussion Forum
Discussion Forum
Up Next
Video Shorts
Featured Story
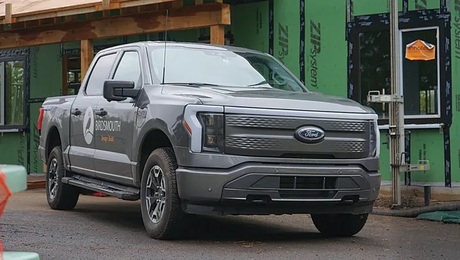
Ford Motor Company slashes prices for some F-150 Lightning models to stimulate demand for electric vehicles (EVs).
Featured Video
Video: Build a Fireplace, Brick by BrickHighlights
"I have learned so much thanks to the searchable articles on the FHB website. I can confidently say that I expect to be a life-long subscriber." - M.K.
Replies
*
I am considering adding 3" x 3/4" maple T & G over my existing laminate kitchen countertops. Would like opinions and advice. Questions include: will it work? should it be glued or merely nailed down? Is wood movement a problem? Does the laminate need to be removed from the 3/4" plywood base? What 100% waterproof glue should be used between boards? What about finishes? How best to waterproof sink area? Will the extra 3/4" of height be significant? etc.
*3214What about expansion & contraction, differential moisture content due to usage variation, sanitation of "all those cracks and crevices", water sealing the sink, watersealing the substrate, .......endless problems that would plaque you for a long time. Rethink this one or hope for a different opinion from another contributor..........................Iron Helix
*We have juniper countertops from wood milled off our ranch. It's been 2 years now and no problems. They are planks joined with biscuits and glued to chipboard underlayment. There was some initial cracking. The small cracks we left, the bigger cracks we filled with a combination of sawdust and woodglue. The entire counter is finished with a wonderful product call Velvit Oil (http://www.velvitproducts.com/) -- when dry it is food-safe and very hard. Many colors to choose from. We LOVE these counters!
*Further to Iron and Tina; I'd advise against T&G, just edge to edge with biscuits and a PVA like Gorilla or Excell One - Weldbond could handle it too. I would take the old laminate off; but, I say that as a preference, I have no idea if it's necessary.
*Thanks, Tina. What glues did you use beneath, and between, your planks? Where are the cracks--at the joints or within the wood?
*Thanks, Phill. Why do you disfavor T & G, vs. biscuits? I guess this also means you don't think nailing is necessary. Would you use Gorilla, etc., beneath or just between?
*Thanks, iron. Yeah, I've worried about those things, too. But I know butcher block, which is glued-up maple, I think, has been fairly successful in the past. But the cons are important to me; that's why I'm asking you all for advice,so I don't end up presiding over a disaster(I hope)
*3214I would like to add my dislike for gorilla glue to this thread as I've had too many failures with this product. Stay away from it where there is a lot of potential expansion and contraction or where there is moisture applied or present.I HAD a 32x65 hand cut and gorilla glued quarter sawn hard maple work island top...it failed at several of the joints and the mold/bacteria loved the soft glue joints.I had other general construction usages where the gorilla glue just "turns loose". My short sojourn with the gorilla glue took me back to the old standbys by Elmers.Good Luck.......................Iron Helix
*I'm not sure what glue we used (I'll ask the carpenter) but think it was just wood glue. Will let you know. The cracks appeared along the grain of the wood planks. This wood is VERY old (500 - 1000 years), and was outside until it was milled and used for the counters. They were "standing dead" trees. Imagine there was some moisture left in them, but not much, so cracking really was minimal. Maybe a half dozen altogether, over many many board feet (LOTS of counter space and a large island). We've had no widening of the spaces where the planks butt/join. My gut would second the motion to avoid t&g --
*Dear woodworkers,Despite having two biscuit cutters, stationary and handheld, I rarely use them. The two advantages I sought from biscuits were strength and alignment in my joints. For me, biscuits didn't produce either.I can get good alignment in the bar clamps just by sliding the wet glued boards. And with just yellow glue, the joints I've tested have always been stronger than surrounding wood. What am I missing with my biscuit machines stowed under the bench?Also, interesting to hear about polyurethane glue failures. That has not been my experience. But then, my stuff isn't made for wet exposures.Thanks to all, Fred
*MHO, using a T&G configuration and nailing (like flooring) will permit the joints to be in movement and to allow the passage/entrapment for fluids and small particles; I much prefer the idea of the single, inpenetrable surface that edge-gluing can provide. Using biscuits to mitigate the potential of a "shear" failure of the glue joints in this humid environment due to wood movement and the use of a good adhesive will make this a lasting project.Before buscuit joiners, a dowel-joint would have been recommended, and you still have that option or use a more precise glued T&G; however, if you go for a shaper/router joint, my preference would be the simpler finger-joint. Please be aware that these mechanical edge joining usually require a lot more planing and sanding to get them smooth than buscuits.Gorilla Glue, Excell One, or one of the other water-proof PVA glues are the proven commodity for a joint that will experience moisture. That being said, if it were my top, I'd just reach for the Weldbond and I think it would last, but they do not claim water-proof.How to attach it is trickier. You could bore some over-sized holes in the existing top and screw up from below using a cup washer over a larger flat washer to bridge the hole. If it were my job, I'd be tempted to go with something like Goop, or maybe dollaps of mirror-mastic. Maybe someone can chime in here with alternates.
*i Gorilla Glue, Excell One, or one of the other water-proof PVA glues are the proven commodity for a joint that will experience moisture. That being said, if it were my top, I'd just reach for the Weldbond and I think it would last, but they do not claim water-proof. Actually poly, PVA type II, and epoxies are not water proof either. They are water resistant.
*?? The Gorilla Glue ads say "100% waterproof" - are you saying they're misleading ?
*Phill100% waterproof for how long? I checked their web sitte and while they use that term they never list it under "specifications". In fact they really don't give much in the way of specs.I never did find the definitions that I was looking for, but I did find this http://www.woodweb.com/knowledge_base/Exterior_glues.html----Has anyone used a product called "Gorilla Glue"? I suggest you start by researching the federal specs on glue types. Type I glues are true waterproof glues. These include epoxy, resorcinol and catalyzed PVA. Type II glues are water resistant. These include Titebond I and II and urea formaldehyde. When I ordered my glue from the Gorilla people, I asked them if it was a Type I glue. They did not know what I was talking about. -------But I see that I was somewhat mistaken. At least Titebond Poly has the following spec; "100% waterproof (Passes ANSI Type I & II water-resistance testing)"
*I have had built curved laminated pressure treated arches with gorilla glue that have been exposed to Louisiana weather with no paint or treatment for over 6 years with no problems.In my option thats water proof.
*Says" 100% waterproof. http://www.gorillaglue.com/compare.html
*I build hundreds of cutting boards per year with poly glues; these see a lot of water. The only failures have been from premature removal from the clamps. I used to use Titebond II, but tired of glue failures in open-pored woods and oily exotics. Nice to be done with glue creep, too.Phill's idea of screwing to the top through oversized holes in the carcass appeals to me as maple moves a lot, esp flatsawn. I wouldn't rely on a glue-to-Formica joint to stand up to that movement.
*You folks are giving me great feedback, just what I wanted. Keep it coming, please. I am a bit confused by the the Gorilla (polyurethane) lovers vs. haters, and wonder what variables there must have been to produce such different outcomes.As partial payback for your generous advice, I would like to introduce you to a book I bought at Harbor Freight (800-423-2567; http://www.harborfreight.com) a couple of months ago for $9.99. Its dimensions are 5 3/8" x 3 3/16" x 5/8", so it fits nicely in a shirt pocket, and it has information on absolutely bloody everything. It is b Pocket Ref,by Thomas J. Glover. Published by Sequoia Publishing, Inc., POB 620820, , Dept. 101, Littleton, CO 80162-0820; (303) 932-1400; http://www.sequoiapublishing.com Anyhow, this book lists 24 glues, but doesn't say anything about Bill H.'s federal specs, which sound very relevant. It lists the following glues as both appropriate for rigid wood joints and "waterproof": acrylic resin (eg 3 Ton Adhesive and P.A.C.), epoxy, polyester resin (as is used for fiberglassing car bodies), polyurethane (Gorilla), resorcinol, water-phase epoxy (eg Dur-A-Poxy). It lists the following as "highly water-resistant": contact cement, casein. It lists these as "water-resistant": aliphatic resin (yellow glue), urea-resin (eg Weldwood Plastic Resin).So--more comments?Unfortunately, my personal experience with high-moisture wood gluing situations is limited to resorcinol and a little urea-resin. The former works fine, but of course you get that dark-red line.Is it possible the differing results with the polyurethanes have to do with different brands, like Gorilla (which I have used, but not in high-moisture circumstances) or Excel?
*did a counter of std. oak flooring over sound existing formica severalyears ago. construction adhesive and plugged screws. stain and 4 coats of solvent base poly. no cracks, splits, water damage aroundsink or anything negative.
*Stephen, I'll toss my ideas out.With 3" thick strip maple, your first goal is to get a good grain pattern in the strips so that any wood movement in one strip will offset the movement of its neighboring piece.For a counterop I would recommend glueing vs just nailing 3" thick T&G strips together. If the 3" thick is already T&G, leave it at that and glue it. If you were going to mill the T&G, save the effort and consider using biscuits.I think biscuits do help in registering the pieces during glue-up, and prevent possible board shifting while they're clamped up. If you're using a glue that is suspect to creep, then glue the biscuits. If you're using something more bulletproof, like epoxy, you don;t need to epoxy the biscuits themselves.One possible downside of some glues is the color...some polyurethanes are dark and can lend a dark line to each glue line. That's okay with a dark wood like teak, but may be aesthetically undesireable with a light wood like maple.Think epoxy. You can get easily match the wood color, it'll hold 3" strips together like nothing else, and it is waterproof.How are you going to finish the countertop? If you're going to seal it with a cured film-finish, then seal all sides of the top before installation. With the top sealed, you could install it directly over your current countertop. I'd prefer not to, though.If you are going to use a non-film, breathable finish, then I'd yank the current countertop and mount the maple over the cabinet carcasses. If the top can breath, the bottom should be able to as well. Otherwise the slab could curl from uneven moisture absorption. That holds true UNLESS the slab is going in over a dishwasher. The moisture put out by a DW can wreak havok on wood countertops, so if a DW is involved, add detail to protect the top from DW moisture. For securing the countertop to the cabinets below, do as Phill mentioned. Either anchor the front or back of the countertop (whichever end you DON'T want to move) to the cabinets with screws or lag bolts, in tight holes. The bolts at the other end of the cabinet...either the back or front...should be installed with a large washer through an elongated hole to allow for wood movement. This anchors either the front of back of the top, yet still allows the top to freely expand/contract.If you go with a non-film finish and have any wood exposed to an undermount sink cutout, I prefer to seal that grain with a thinned epoxy. Not enough for a glossy coat, but enough to partially penetrate the wood grain and save the wood from repeated wetting/drying cycles.Pocket Ref is full of trivial information, isn't it? It makes a nice little gift for those that dabble in construction projects.
*Stephen, go to the Fine Woodworking forum and search on glues for even more dissension! (Click on "Taunton Press Discussions" near the top of this page, and then click on "Knots-Woodworking" to get there.)I had a severe poly failure last season when i had a 25% failure rate in my cutting boards using Excel. I thought it might be due to using the cheaper brand, purchased at a HD. So i bought a few more types of poly glue and tested again, only i left the pieces clamped for at least 12 hours. I had one failed joint out of hundreds of joints with that trial, which was convincing enough to me that the variable was the clamp time, not the brand or price of glue. One thing to know, though it may not be as important for a countertop as a piece of furniture, is that dowel or biscuit locations can telegraph over time to the surface. When i glue up a table top, i do it by clamping just two boards together at a time. I start at either the middle or one end, use a pipe clamp to fix that together, then wiggle the next section into plane, clamp, etc. until i'm all done. I never use biscuits for alignment bec there seems to be too much slop unless glued, and not enough time to mess with gluing them all in when i'm working alone.All the poly glues i've used leave a tan glue line, unlike what Mongo describes, so maybe he can steer you clear of those brands that dry too dark. I like the poly idea over Mongo's epoxy only bec of the cost and ease of use (no mixing).I was musing about attaching the top, about drying to only one side as mentioned, so i thought i'd throw out the idea of using Cedar Breather under the wood. I've never used it for anything, but does anyone think this has potential for providing enough ventilation to keep the top [more] stable?
*I read and didn't see that anyone mentioned that flooring t&g joints aren't exactly milled to allow for enough contact area for a good glue joint. If you look at the ends you will see that the edges are slightly tapered and the t& g's don't exactly fit together as one. I am not crazy about the idea of using strip flooring for the top, if you want to rip the wood you have and glue it up, that might be your best bet.Install it over cedar breather? Go for it. I don't care if you also install a mast and call it a sailboat. ;-)
*Arrgghhh...After reading Splinty's post #14, I thought "how the heck could biscuits telegraph through 3" thick maple?Then I read Qtrmg's post #15 and knew that I really blew this one.I mis-read your intro and thought you were using 3" thick maple, not 3" wide strips of 3/4" thick maple T&G flooring.Disregard EVERYTHING I wrote in my above post, which just happens to be unllucky post #13.Sorry, Mongo
*Tina: is VelvitOil a breathable finish, like Mongo was talking about, or an impervious one? I really like Watco-type oils for staining non-food surfaces, and it sounds like VO is similar.Splintergroupie: What polyurethanes leave a tan line? I agree that PU would be a lot easier and cheaper than epoxy. And when I read on Gorilla's web site, they said 95% of the gluing failures they had dealt with were due to inadequate moisture available for the glue to cure, and recommended wiping maple and one other dense-grained wood with a damp rag before glue-up. They also emphasized the importance of hard clamping, so that's the other 5%, I guess, as you found.gregg: could you be a little more. . .explicit? Did you keep the T&G or plane it off and use biscuits? Where was the const. adhesive, just under, just between, or both? I would think between wouldn't work too well, since it would be gummy and flexible and that odd color, and PU or epoxy would be better. If no glue between, what did you fill the seams with, if anything? Do I understand that you face-screwed them down? If so, did you leave wiggle room for each piece or for a solid slab, as Iron and Mongo suggested, or just crank them down? Maybe you could get away with cranking down because you used an impervious finish? Did you finish all 4 sides, then? Any problems with the extra 3/4" height?
*i What polyurethanes leave a tan line?I think i've used every one i've ever come across: Gorilla, Titebond's version, Excel, and a few others with odd names that the lumberyard carried that were a LOT cheaper than the brand names, but no doubt fell due to advertising budgets. I would characterize all of the glue lines as tan-colored. I use sugar maple, birch and beech as the basic wood in my cutting boards and all the glues have been good matches for those lighter woods, but i also use a variety of exotics ranging to pure black in color and still don't see a line at all. I clamp the cutting boards about 100 laminations at a go (four cutting boards' worth) and end up using a wrench to crank the handles. When i do something like a tabletop without so many lams, i don't need to resort to a cheater, but i still use all the hand-pressure i can muster on 1/2" and 3/4" pipe clamps. I never have spritzed any of my joints with water before glue-up; all my wood is kiln-dried and stored in a basement that is seldom less than 50 degrees.BTW, i ran a little thread over on the cook's side of things about wood v. plastic in cutting boards and the sanitation properties of each material. The results might surprise some.
*Splint, I endeavor to comply with all your wishes, and have found it most rewarding. First, I went to the FWW discussion site you suggested and found this Forest Products Laboratory URL which appears to have everything knowable about every wood-related topic on earth:http://www.fpl.fs.fed.us/documnts/FPLGTR/fplgtr113/fplgtr113.htmWood Handbook, FPL-GTR-113Second, I read your cutting-board thread with the cooks, and found it most enjoyable, particularly the clash of the Experts at the ivory towers. It appears that as far as the cooks themselves are concerned, you will have no dearth of markets.
*Yes, it's breathable (no polyurethanes or acrylics). We also used it on all our window and door trim. Velvit Oil also sells true Lemon Oil with no additives which is great for replenishing furniture and the trim. For the counter, about once a year I just rub a little more of the velvit oil into it.
*But water beads on it, too so it's like GoreTex -- let's wood breathe but keeps water out?
*Use what boatbuilders use and you won't go wrong, resorcinol or epoxy. Resorcinol would be my first choice, altho the glue lines may be more visable.On the other hand, I made my wife a cutting board, a couple of years ago, using just Titebond II, which is frequently run through the dishwasher. It hasn't failed, yet. Actually, I used the Titebond II on purpose just to see what would happen, since it only took me 15 minutes to make the thing.
*“What polyurethanes leave a tan line?”I know this one, I know this one! Polyurethane bikini’s, ha, and you all thought I was stupid.Mongo, how stupid is this? I didn’t even notice you were thinking 3” thick. Ahh, too much to read and too many voices.Jim, nice boat reference, I think we have a theme now. But shouldn’t Stephen be thinking of a teak deck now?Ok, I feel bad now for goofing off, but I don’t see any of this a project I would recommend. Did you ever think of using the wood for a coffee table? Maybe some yard furniture? How great would t&g maple be for closet shelves. (taking the shovel and making sure I have dug down far enough)
*Qtrmeg, Yup...I booted this thread big-time. And I draw the same conclusion...don't use the flooring as a countertop.
*I wouldn't want all this wet wood in my kitchen either, but...but...Stephen has a DREAM!!!! And then there's Tina's messy evidence of success (boo, hiss), plus i would really like someone to try the Cedar Breather idea and report back. And the polyurethane bikinis--man, i thought it was hard to get the stuff off my hands!--i think we broke new ground here.
*I also have access to 110 sqft of first-cut maple T&G at a low price. I've been mulling various countertop ideas over for a while now: concrete, sheet metal, butcherblock, etc. I've seen butcherblock successfully used as countertop and even as butcherblock. It seems to me that the T&G is just a variation on this theme. So when the stuff came on the market, it seemed like Kismet, and I determined that I would submit my idea to some experts. And you guys have come through like champs.Please tell me more about Cedar Breather. I gather that the idea is to provide some air circulation beneath the maple slab to equalize moisture exposure top and bottom. In that case, I wouldn't want to put any adhesive beneath the slab, right?
*Cedar Breather3/4" T&G and butcherblocks are a variation on a theme the way a Volkswagen and a Panzer are both motor vehicles.
*Oh.
*Sorry about the delay in responding. The const. adhesive was between the formica and bootom of the flrg. only. No adhesive at the T&G. The flrg. was placed at a 45 deg. angle and each strip was screwed with 6 screws... 2 at each end, and 2 in the center. No allowance was made for movement. Oak was installed and then finished... visible surfaces only. Never noticed any movement or stress from trying to move.
*Just a thought here about something other than glue. It's about maple's tendency towards large amounts of movement due to seasonal changes. I initially made the same misassumption as Mongo in reading this post. I thought Mr. Miller would be building a 3" thick maple top which would be drilled and clamped for life with allthread as is typical for end grain maple butcher block tops. I realized that unless the kitchen was being reconfigured for an NBA star, that this wouldn't be practical. Our floor laying experience has shown that 2 1/4" maple shrinks a lot in winter and the 3" is even worse. The floors gap like crazy and look like hell. The summertime brings them back to full tightness. If you are going to do this, I would definitely recommend Gregg Smith's idea of using construction adhesive to bond the boards to the laminate.