I am building a small barn for my kids… and their animals. Ag buildings do not require stamped prints n my area but a permit is required. On a 20′ span with a gambrel roof topped with metal roofing, how far apart can I space trusses and what size purlins would be recommended?
Discussion Forum
Discussion Forum
Up Next
Video Shorts
Featured Story
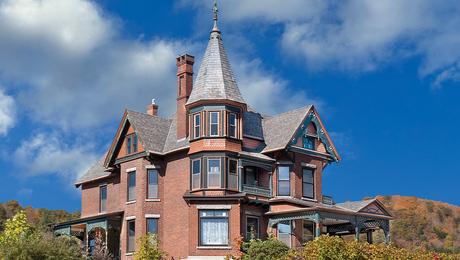
Fine Homebuilding's editorial director has some fun news to share.
Highlights
"I have learned so much thanks to the searchable articles on the FHB website. I can confidently say that I expect to be a life-long subscriber." - M.K.
Replies
This is a question for your truss supplier. They will design for spacing and purlins free of charge.Just tell them what your trying to do and they will fix ya up.
Good luck,
dug
I though that might be the case; but not wanting to feel like the vilage idiot when I went in, I thought I'd ask here first. Even though I've done my share of building, it seems some guys in the business for real salivate when they see a school principal coming!
Thanks.
I have no problem asking........it's just another way to double check yourself. Heck I have the concrete supplier figure all of my pours and I do this stuff for a living........26yrs and counting!
Around here, 8' OC spcaing with 2X4 purlins is the most common.
You can go to 10' centers, but then you need 2X6 purlins because of our snow loads. I've seen buildings built with 12' spacing, but they're rare.
Trusses are made to order the vast majority of the time, so you'll just order what you want and they'll design them accordingly. When yuo talk to the supplier they'll need stuff like your loading requirements, if you want the trusses designed for a ceiling load, etc.
I have built many a barn with the 8' truss spacing you describe.
The purlins were standing on edge, and had to be nailed with ring shank 40's or 60's, can't remember which.
Last one I did I used 6" GRK's and they worked mo betta.
Matt
All truss drawings which I get from the local suppliers have the purlin size and placement marked on the drawing or in the notes. Any permanent wind bracing is also speced either on drawing or in notes.
You should also get a sheet from the supplier which illustrates and details temporary bracing during erection. Pay attention and follow the directions. When in doubt or the weather (wind) looks threatening - add more.
Once one truss goes over during installation, the rest follow like dominoes - results of improper bracing can be expensive, injurious or fatal.
Don't be afraid to ask.
Jim
Never underestimate the value of a sharp pencil or good light.
"All truss drawings which I get from the local suppliers have the purlin size and placement marked on the drawing or in the notes. "
If the purlin SIZE is shown it's only a default in the part of the program that makes the drawings. The spacing of the purlins is the only thing that's important to the truss design.
"Any permanent wind bracing is also speced either on drawing or in notes."
What's shown on the drawing is most likey CLBs, or web braces. That has nothing to do with wind bracing.
There's a thread about CLBs here if you aren't familiar with what they are:
http://forums.taunton.com/tp-breaktime/messages?msg=87378.1
The reward of energy, enterprise and thrift - is taxes. [W. Feather]
I went back and added the CLBs to my trusses after that thread.
The only additional advise I might add for the OP is to check your local codes. I hapeen to live in a boundry county. My truss supplier did not realise that the ground snow load requirements changed at the county line. He had to go back and redsign for an increase from 15 to 20 psf ground snow load. I can throw a rock into the next county, but it makes no differance to BI.
I also thighten up my spacing to 4" o.c. and laid my purlins flat. That met the loading requirements and makes hitting them with screws a lot easier.
Dave
Perhaps the size is a default setting - they always are 2x4, if it's in the notes or on the drawing - we put it in, size and placement per the drawing - COA (cover our azz).
Know some about CLB's - thanks for link.
Jim
Never underestimate the value of a sharp pencil or good light.
BillD60,
consider doing a timberframe!
Seriously you'll find it cheaper and something that will add some real value far beyond the value of the building..
Timberframing is really simple and can be done quickly. There are some specialized tools but you only need them if you plan on finishing off the timbers rather than leave them rough..
Let me give you some examples of how much money you can save..
A house the size of mine would normally have a $75-80,000 lumberyard bill just for the framing.. I massively over did this place using the finest hardwoods available like black walnut cherry white oak etc.. and spent less than $25,000. Go to 85891.1 to see what's involved there is also some pictures o fthe front at 94941.1
I believe I could have built this place properly and spent less than $10.000 on the wood.. if it were a simple barn I believe that you could built it for around $1000 worth of sawmill wood.. that's for walls, roof, siding, and floors! If you post and beam it instead of timberframing you'll have nearly the same thing and spend even less time doing it.. (it will require some big drill bits and probably a decent impact wrench) .
I'll gladly talk you through the details..
Edited 9/25/2007 12:58 pm ET by frenchy
Is a timberframe the answer to everything?
Jon Blakemore RappahannockINC.com Fredericksburg, VA
JonBlakemore,
Well no, but it's an option, perhaps he hadn't considered it prior to my mentioning it..
Here's some numbers for you to chew on..
He didn't mention the sizes involved so I'll take a stab at it.. Ash is common right now because of the green ash borer, so let's use that. I'll take a simple ash timber say 3 inches by 9 inches by 18 feet and use three of them to form my truss. My cost for those three would be $66.00 What would the cost of a 18 foot 12/12 pitch roof truss be? (actualy that's massively over simple but it get's us in the ball park)
I'm guessing so maybe Boss hog could answer,But I suspect about $150.00 each? let's assume that he's building a 20 foot long building and decides to space these at 2 foot intervals? that means he'd need 11 at $150 for a total of $1650 or sawmill wood he'd need $726. Just in roof trusses we're speaking about a savings of $924.00
Frenchy,You're comparing apples to oranges.We get that you love timberframes. I think many here have appreciation for the visual appeal and potential longevity of a timberframe.However, you're comparing pieces of rough lumber to a roof truss. And the assumptions you are making leave a lot of room for error.+++++ Your way: +++++You drive to pick up rough boards at the sawmill. You incur cost in both time and vehicle expenses.You haven't purchased any fasteners for your truss. Figure about six 1/2"x6" carriage bolts @ $1.50 each for each "truss". That adds $9 per truss.You have to assemble these trusses. Since you're building a barn with a dirt floor, you will have to make a somewhat flat area where you can set up a jig for your trusses.Installation will be a chore since you're lifting what is essentially 45' long 3"x9" piece of hardwood. Not very easy for two men to do. Add crane rental of $450.Fill in the gable area with lumber so you can attach your exterior finish.+++++ The conventional way: +++++Call up your truss supplier. Tell them you want a nine common trusses and two gable trusses for an 18' span and 12/12 pitch. For quick reference, we purchased 8 scissor & 1 gable trusses that were 18' long about two years ago. The pitch was 6/12. The delivered cost was $554.You don't have to assemble, you'll need about 100 12d nails for assembly, and the trusses are light enough that two men can install without too much effort.In my opinion, trusses are the easy way by far.BTW- the building inspector takes about two minutes to inspect our trusses. He glances at the stamped drawings and checks that the necessary bracing was installed. How has the building dept. felt about your timberframe? Did you have to prove that your design was sufficient or did they sign off quickly?
Jon Blakemore RappahannockINC.com Fredericksburg, VA
I set six 18' trusses on an 8' wall by myself last fall. Stuck one end up on the wall, humped the other end up a ladder and set it on the wall, then set the ridge on my bakers scafold and flipped it over against my T brace on the outside wall. Added a couple of kickers to the first truss and set the second one to them. The rest were easier because I could then run strap bracing across a couple of points on the top cord. Took about five hours total to set, plumb and brace the hole set.
No way could I have done a tinber frame set of trusses by myself without equipment.
Dave
Dave Richeson,
Absolutely true, stick building is easier. Many of the pieces are precut and it's simply a matter of banging them together.
Maybe that's why the handcrafted details of a timberframe are so much in demand.
On the other hand I priced out building my home with tradional 2x6's etc, and compared it to the cost of building it with SIP's, Timbers, and ICF's and found it was cheaper for me to buy those than to go to a lumberyard and purchase the required materials. Have a foundation put underneath it, etc. etc..
Now the only remaining issue is my labor.. I've spent six years building this place and I'm still not finished.. But that's six years of part time work while I worked a 40 plus hour week at earning a living..
Plus I'm not a pro, I'm fat, and out of shape (well, round is a shape isn't it?) ;-) and prone to massive overbuilding.. I honestly want this place to remain standing in the event a tornado hits it..
I could be pragmatic and say that my work has increased the value of my home by well over a million dollars. (The bank appraised it on Dec. 19 in a down market as being worth 2.3 million dollars, I paid $107,000 for it originally) so my part time job has earned me in excess of $5000 a week.. OK I know, but it's fun to play with numbers isn't it?
To Answer your question yes I used a telehandler to put the trusses up (and a million other tasks as well.) If I'd bought one instead of rented it I still would have been more than a million ahead of where I am now.. Equipment doesn't cost, it pays!
Jon Blakemore,
I hope I've never claimed that timberframing was easier that stick building*.. I'm pretty sure that I haven't.. so if you want quick and easy then by all means stick build it..
On the other hand stick building is a me too game, especially right now. while timberframers still have massive backlogs.. Stick builders around here are trying desperately to survive and more than a few of them are robbing Peter to pay Paul, that is they are taking less profit simply to keep making payments on everything.. while a large number of them can't even do that!
I don't understand why you insist on a crane rental.. cranes require three people. one to hook up the load, one to operate the equipment, and another to unhook the load once in place.. true you can double duty things if you don't mind slowing things way down while someone runs back and forth.. A forklift on the other hand with simply the operator can pick up the load, put it in place, and go back for the next one while someone is nailing it in place..
As for timberframing and inspectors.. once you get over a certain size there is no inspection required.. data is right in the inspectors manual as to what size is required. True most aren't familar with that section but it's there. I used the UBC when I got my approvals but I've seen it in the new code as well. My building inspector took one look at my sketches and approved it with only a few questions to check my competance. When I not only had the answers correct but knew the page and often the exact wording he relaxed. If you've seen my pictures you understand why strength isn't an issue here..
* I own a (actaully many) nail gun so I'm certainly familar with just how fast a wall etc, can be built nowdays, but I can say as I did to the OP timberframing is easy at least as easy to do as a pole barn is.. If you want you can use nails to assemble everything and it's just fine. You could post and beam it which is what I believe that you are trying to say or you can do a true timberframe..
I will say that the Amish and Menonites around here can certainly build a barn quickly and they don't use forklifts, cranes, or nail guns.. while it's true they all get together and raise the barn with the aide of their horses etc.. you don't really have to be that committed to the luddite world to put one up quickly..
Uh Jig? to build trusses? why would you do that? You do a lay out of the first one and cut each right on top of the other. If I was doing it without aide of equipment I 'd cut each one, lay it on top of the others to make sure everything is correct and then assemble up in place.. true a 18 foot long 3 x9 is heavy but not too hravy for two people.. you don't ever lift the whole thing at once. Always one end at a time.. that's how I moved 6"x12"x 24 foot white oak timbers around myself.. I'm not really that strong I simply understand leverage.
Frenchy,
I will deal with a few statements one at a time.
"I hope I've never claimed that timberframing was easier that stick building*.. I'm pretty sure that I haven't.. so if you want quick and easy then by all means stick build it.."
Maybe you've never made the direct statement that "timberframing was easier that stick building" but you often bring up statements to that effect. In this very thread you said:
"Timberframing is really simple and can be done quickly."
Timberframing has value, but you cannot realistically compare timber framing to stick framing. I would bet that you could not find more than a handful of entry level tract homes but with a timberframe, (maybe you can't even find any). That's because stick framing is cheaper.
"On the other hand stick building is a me too game, especially right now. while timberframers still have massive backlogs.. Stick builders around here are trying desperately to survive..."
Timberframers is a niche. I don't see how you can compare stick framers to timberframers.
"I don't understand why you insist on a crane rental... A forklift on the other hand with simply the operator can pick up the load, put it in place, and go back for the next one while someone is nailing it in place.."
If there's two things that I think you love to talk about, I would pick forklifts & timberframes. I can rent a 40 ton crane and operator for about $450 for four hours to help setting trusses on an addition. A forklift may help some, but most of the work on jobs we do is more than humping materials. How much would it cost to rent a forklift for a day, including delivery charges?
"As for timberframing and inspectors.. once you get over a certain size there is no inspection required.. data is right in the inspectors manual as to what size is required."
We are under the IRC 2003 in the counties that we operate in. I haven't ever asked an inspector about using non-graded lumber, but I would be skeptical. Here is what the IRC says-
{R502.1.6 Structural log members. Stress grading of structural
log members of nonrectangular shape, as typically
used in log buildings, shall be in accordance with ASTM D
3957. Such structural log members shall be identified by the
grade mark of an approved lumber grading or inspection
agency. In lieu of a grade mark on the material, a certificate
of inspection as to species and grade issued by a lumber-
grading or inspection agency meeting the requirements
of this section shall be permitted to be accepted.}
To be fair, I've never asked about this so maybe there are some provisions that I'm not aware of.
"Uh Jig? to build trusses? why would you do that? You do a lay out of the first one and cut each right on top of the other. If I was doing it without aide of equipment I 'd cut each one, lay it on top of the others to make sure everything is correct and then assemble up in place."
Maybe we're talking about two different things, but I can't imagine installing 18' long 3"x9" timber trusses up in the air. If you're talking about using the timbers as rafters and ceiling joists, then I see what you mean.
Jon Blakemore RappahannockINC.com Fredericksburg, VA
JonBlakemore,
First let me state in no uncertain terms that building without a telehandler is a waste, of money , of time, and is less safe.
I no longer sell them, I was fired, (let go , dismissed for lack of sales) at my old company and am going to change industries since I believe here in Minnesota for a few years anyway sales won't return to sustainable levels. Thus I cannot possibly benefit from your choice to use them or not. For your own sake I hope that you do..
I have 17 years in the industry and went from when they were a novel item to where virtually every builder needed one in order to compete with those who had them.. Telehandlers do so much more than set up trusses, that's like only using your hammer to open beer cans..
Short and simple they allow builders to build homes 20% faster using 20% less labor.. those are very conservative numbers that experienced builders have told me over the years.. (most use bigger percentages) You could buy a brand new loaded one, pay for it with the labor savings alone and still benefit from being available to build 20% more than you do.
Once it's paid off they cost next to nothing for the next 20 years or so and still will save you that 20/20 over not using them..
My last part of that statement less safe I've noted myself. Properly trained operators will eliminate a large number of the traditional jobs that injure people. Installing windows on the second floor for example. No longer will you need to hump that big wide bow up a couple of ladders risking dropping it or losing control and having somebody fall off a ladder. You set it in your work basket and a couple of you slide it into place once the operator (or yourself if you got the remote controls) sets the platform a half an inch below the opening.
You have built in fall protection when you are putting plywood on, siding on, roofing on and soffits and facia etc..
Instead of setting up scaffolding you can be installing, instead of tearing down scaffolding and moving it you are doing productive work..
even building floors goes nearly 50% faster with a telehandler than without one!
Next, timberframing is simple! You make a pocket called a mortice where a post that's reduced in size called a tenon goes. Put a frame called a bent together and repeat. Because of the size of the timbers you don't need to make very many bents..
If that's too hard you can simply lag bolt things together and call it a post and beam, most outside the industry will still call it a timberframe
If you want smooth wood there are all sorts of options but you don't need smooth wood to have a timberframe.
I didn't say stick builders were the same as timberframers, it's clearly a higher scale of construction.. Yes it's a niche, one that isn't flooded with builders because the skill level that people seek is higher than the skill level required to stick build.. However, any decent carpenter could do a timberframe Plus be well compensated for the added skill required..
I am absolutely sure that timberframing is permitted in every building code. If you were to visit my community you'd find out just how exacting they are with regard to conformance to building codes.. One inspector made a negative comment because he percieved my shingles were 1/4 inch apart rather than the 3/16ths he demanded. Only when several weeks had gone by and the green shingles had dried out and shrunk giving me that 3/16ths did he relent and approve.. Frankly you don't let just any Yahoo build in multimillion dollar communities..
Yes I did use a telehandler to install my trusses. However it still would have been possible without a telehandler, just not as safe or anywhere near as quick..
Jon, I don't understand your challenging me on these issues..
You said you like stick building.. No doubt it's a niche you feel comfortable in and based on the tone of your posts over the years that need for a comfort level is very important to you..
That's absolutely fine.. nothing wrong with that. If I offer you a differant approach it doesn't make it wrong, simply differant.. same with telehandlers.
At one time they were like nail guns here in Minnesota, sorta rare. Today no builder could consider building without them.. Telehandlers are the same thing.. If you want to be profitable here in Minnesota you need one.. Otherwise those who can build 20% faster for 20% less will underbid you every time..
Edited 9/26/2007 1:50 pm ET by frenchy
Frenchy,You have proven once again your love for telehandlers. I do not disagree with you that someone who frames full time should seriously consider the purchase of a telehandler.My company, on the other hand, does a mix of work. We enjoy doing additions and building new homes, but we still do a lot of other types of jobs.Right now, we're building a deck on a new home. The client would likely have us shot if we drove a telehandler on his new sod, and we would be foolish to because all of the lumber can be carried from the drop to the sawhorses in back in probably 45 minutes. We did a basement finish before that where we could not use a telehandler at all.Sure, the house we built in the spring was a great candidate for a telehandler with basket (and guess what, we rented one for a month) for framing and some of the high siding work. But that's the only job that we could really utilize a telehandler this year so far.How much would the payment be on a 44' IR telehandler? I'm guessing somewhere around $1,750/month, possibly more. That's a lot of equipment to sit dormant when we have a stretch of three months where it can't be used.A crane costs me about $450 for 4 hours. I don't have to maintain, store, insure, or make payments on a crane rental when it's not in use. For me, that's a big benefit.As far as the timberframing vs. stick framing, I laid out where I thought your numbers were spurious. Timberframing is great but you cannot compare it to stick framing for speed & cost. Since you didn't respond to my points about how you under-estimated the cost of timberframing and over-estimated the cost of framing with trusses, I will assume you agree with my assessment.
Jon Blakemore RappahannockINC.com Fredericksburg, VA
Jon Blakemore,
Hopefully this is informative to you and not simply an arguement. Right now here in Minnesota you can buy a late model say 2001 or 2002 telehandler as low as $30,000. most likely it will have less than 1000 hours on it and be well equiped.
If you amortize the cost over the useful life of the machine it will average you about $125 a month. A bank lending at near prime will require payments of around. $600 a month.. or you could do a tax lease and reduce your payemnts to under $500.00 a month.. You need to understand that this isn't a truck.. it doesn't depreciate a lot once it reaches these levels.. We regularly sold 10 year old forklifts for more than this, the reason prices are depressed right now is Minnesota is massively overbuilt with spec homes.
Assuming you bought from a framer rather than a mason your operating costs per year would be well under $1000 that's maintinace and fuel costs.. Insurance on something like that would be right around $800 a year or so.. A nice number to budget per move would be around $250 per house or $125 deliver and $125 pickup.
As for my numbers regarding the cost of timberframing
You could, if you really wanted to, check rather than simply assuming something. Simply get a copy of the hardwood market report http://www.hmr.com and verify that the prices I gave are the prices sawmills get for a 9"x7"x9 foot railroad tie..
It's been $22.00 for a long time now.. Now ties are any hardwood such as ash, oak, maple, etc. there are real tight standards regarding soundness of the wood because they don't want to waste the cost of treating them with creseote on junk and they will be in place for 20 years or more!
Soft woods are significantly cheaper..
It's too bad you can't stop buy and review my reciepts from the sawmill on my home.. others have been here and you could ask them. Or you could simply call Johnson Bros logging in Cannon Falls Minnesota and talk to Connie or Dan..
As for agreeing that you paid what you claim on trusses those are much, much, lower than the numbers I normally see, was there any reason for it? Surplus, returns, unclaimed?
"Is a timberframe the answer to everything?"You should see the timberframe drag racer that I am building As soon has I solve the problem of wheels comming apart at 60 MPH it is ready to go..
.
A-holes. Hey every group has to have one. And I have been elected to be the one. I should make that my tagline.
BillHartmann,
In your case I'd highly reccomend an ICF drag racer... ;-)
I love the idea of a timberframe... just thought I could put up a pole building quicker and easier. I'm not one does things half way so I'm not afraid of the work. I just have no experience with timberframe and it sounds a bit over whelming.
BillD60.
Think of it as a pole building with square poles, seems simpler now doesn't it? You can use pretty much the same approach same spacing etc.. If you want you can do a post and beam and wind up looking nearly the same as a timberframe..saves time over a true timber frame. instead of metal siding you can put up wood siding, but you don't have to.. if you like metal then go ahead and use metal.. might find that wood is a lot cheaper than metal.
Here's the kicker.. if you go to a sawmill and order railroad ties you'll get a hardwood that is 9 inches wide 7 inches thick and 9 feet long that timber will cost you $22.00 the wood might be oak/ash or whatever.. (No it won't betreated with creosote, yet) most sawmills will sell you an 18 foot long one for $44.00 so there you have your costs.. I can do the rough calculations for the rest of the building if you give me an idea of how you want to build it, what size you want, and maybe some dertails about windows doors etc..
I did build a building once using post and beam techniques but the fasteners and connections were mechanical. It worked fine; that's kind of what I'm considering here. I though I could save smoe money using a more pole-built approach.
I appreciate your interest and ideas.
BillD60
That's excellant.. you don't have to be a purist to own a timberframe. I used stainless steel lags instead of pins to hold mine together.. In fact European code requires metal connections in timberframes. (ask, I'll explain why)
I gave you sawmill prices but it's possible to get even better deals on some wood..
What I do is accept any wood that someone orders but fails to pick up, that's how I paid as little as 10 cents a bd.ft. for some really terrific wood. (yeh it turned grey but so what run it thru the planner if you want it to look nice or paint it!
A couple of things to be concerned about, if you use white oak or black walnut as I did you must also use stainless steel fasteners. White oak is real cheap right now 80 cents a bd.ft buys mill run in whatever size you need. It doesn't rot easily while it's not quite as perminent as pressure treated there isn't any potential fall out of unexpected repercussions as there was with the first and second variety..
Right now Ash is really flooding the sawmills and there is no real market for it thus it's about as cheap a wood as there is. yet ash is really a solid, strong, and extremely durable wood that you can nail into nicely while it's still green but as it dries gets harder and harder untill you couldn't drive a tack in with a sledge hammer! ;-)