I’m making plans for a foundation with about 8 feet unsupported back-fill in a rather sandy loam soil area. Actually a steep hillside. I propose a 12 inch filled block back with 2 side walls. Backwall is 64 ft. Books show use of pilasters which I call buttresses. Do you have suggestions as to what spacing to use between them and if they can be on outside of wall instead of inside which screws out my fllor plan ?? Also how thick should the pilasters be ?? And I do appreciate yoou– alllll . smitty
Discussion Forum
Discussion Forum
Up Next
Video Shorts
Featured Story
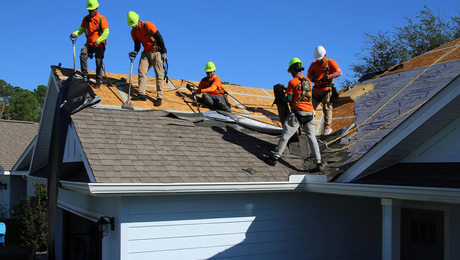
Listeners write in about haunted pipes and building-science tomes, and they ask questions about roof venting and roof leaks.
Featured Video
How to Install Cable Rail Around Wood-Post CornersHighlights
"I have learned so much thanks to the searchable articles on the FHB website. I can confidently say that I expect to be a life-long subscriber." - M.K.
Replies
You need a structural engineer to advise on this.
We appreciate you too, which is why we are advising you to find a civil engineer or soils engineer familiar with the land in your area to help you design this. The costs of a failure would make the bill for engineering seem like bus fare.
Good planning never costs, it pays big dividends both in execution and in peace of mind.
Welcome to the
Taunton University of Knowledge FHB Campus at Breaktime.
where ...
Excellence is its own reward!
I'm pretty sure you're going to find that the footing and footing/wall connection to be more important. I can do a 12" cast wall, lots of rebar,with a 5'10" wide footing for 8' of fill with a 1in1 slope above. No pilasters needed.
When I had my 15' tall backfill wall engineered I asked about pilasters. Engineer said there was no reason. It's 14" cast, with an 8'11" footing. Building inspector said she'd never seen anything like it. Apparently the engineer was conservative. They wear two pairs of underwear "just in case".
Time to spend some bucks, assuming there's an engineer available.
Forgot to mention that the building inspector suggested the engineer called for twice as much steel as was necessary. So I asked which half was unnecessary and was told that it was my decision. Great, the guy who knows nothing makes the choice. Rebar really isn't a lot of money. Wall failure is.
PAHS Designer/Builder- Bury it!
Edited 2/26/2004 9:29:21 PM ET by VaTom
As I understand it, the historical reason for pilasters, was to stabilize segmented walls, or walls built of individual stones, bricks, or cmus. With a re-inforced poured concrete wall, you already have the stabilizing action built in.
The engineer has a major place in determining soil type to figure the size of the footer for spreading loaad and for ballast.
Welcome to the Taunton University of Knowledge FHB Campus at Breaktime. where ... Excellence is its own reward!
Thank you for explaining the reason for pilasters. Would've been nice if the engineer had.
My engineer was unconcerned with soil type. I understand the potential difference, and there is variation of soil around. I dealt with both local engineers and hired the more competent. My assumption was that he took a "worst case" scenario.
The engineer (steel co. employee and the only local engineer with a state stamp) who detailed my roof structure asked me what my dirt weighed. I gave him numbers I'd read. So far so good.
(He says, living under a couple hundred tons.) PAHS Designer/Builder- Bury it!
sandy loam weight about 112 lb per cu ft, thats all I can offer in this conversation
sandy loam weight about 112 lb per cu ft,
Thanks. None of that on this mountaintop. Decomposed stone, after the inch or so of top soil. Further complicating the issue was the PAHS concept requiring dry dirt overlaid by occasionally wet dirt, separated by the insulation umbrella.
I'd have to do some digging to see what we used. Total load was 300 psf with live load of 75 psf. We've had 24" of snow sitting on top, well over our normal yearly total, and it worked.PAHS Designer/Builder- Bury it!
"... the historical reason for pilasters, was to stabilize segmented walls, or walls built of individual stones, bricks, or cmus. With a re-inforced poured concrete wall, you already have the stabilizing action built in."
Not trying to pick an arguement - I just don't understand this.
My first thought was that pilasters was EXACTLY what this guy needs. Wouldn't the pilaster(s) help hold the wall vertical? Isn't that what they're designed to do?
Even a poured concrete wall can develop cracks, and act more like a "segmented" wall.The United States is the only country where it takes more brains to figure your tax than to earn the money to pay it. [Edward J. Gurney]
Surre pilasters could help, but not nearly as well as integral re-inforcing. Old way vs new way.
With a stone wall, if pressure bears from behind, a single stone can be forced out, or a crack acan run diagoinally down the wall folowing the joints between stones. The pillaster breaks up the destructive strresses and provide mass / inertia against the thrust. It acts similarly to a steel stake in the ground holding a form board to see a smalle model, so to speak.
But the pilaster is still individual pieces as is the wall and any of them can separate from the others.
With a concrete wall containing a well thought out system of re-bar, the whole wall acts as one.
It's not too much different in principle from your trusses. A truss is designed to act as a unit. Stick framed roofs act differently.
A crack can develope in concrete but the rebar is intended to preven that and to help resist total failure if a crack does happen.
Welcome to the Taunton University of Knowledge FHB Campus at Breaktime. where ... Excellence is its own reward!
There are many cases in reinforced concrete construction where pilasters are formed and poured integrally with walls.
The precast concrete foundation panels by Superior Walls have nice examples of integral pilasters, done on 16-inch centers.
And yes, I will say it again. This guy needs an engineer for his project. His situation is way too complex and with too many variables for advice via forum web page.
Smitty thanks you for your experience about the back-filled foundation wall. your use of a 5'1" footing under a 12" block filled and reinforced wall seems unique. Did you use the footing "inside" the wall as a floor. Was the wall centered on the footing ? Also I appreciated the other remarks about using the professional engineering approach which I will do. THanks to all that responded. Smitty
All good advice for you from the previous posters, especially the part about getting an engineer.
The wide footing and the rebar inside the poured wall are designed to resist overturn and lateral displacement. (You may hear the engineer refer to a "moment connection", that's what he's talking about in this case).
Your engineer will make some assumptions about the equivalent hydraulic pressure that will be exerted on the wall and the bearing competence of the soils under the footing, and on that basis calculate the size and placement of the rebar, and the width of the footing required.
This is the relevance of Johnnie(Brownbagg)'s observation about soil weight per cubic foot. If your engineer doesn't express any interest in the soil type (i.e. if he doesn't want to do a site visit), find another engineer.
Piffin is right, of course, pilasters would not do a thing for you.
If you do the work yourself, note that the rebar placement inside the wall and in the footing is crucial. Build it exactly as it's drawn. If the engineer says the rebar needs to be in the outside third of the wall, you need to do it that way.
An overturn footing, simply stated, is kinda like a lever that holds your wall where it is supposed to be. If backfill and compaction are a concern, here's a tip to ask your engineer about.
I've done retaining walls on really weird sites with unusual soil conditions. When the soil conditions are especially scary, I have backfilled the first foot or so behind the wall, over top of the overturn footing (just like what was previously described) with lean fill. This is also called CLSM (controlled low-strength material), also known as "flowable fill" or (improperly) "sand mix".
Properly formulated, it's pumpable, which is a good thing.
It's always worth talking with your engineer about options. I came up with this idea beause what the engineer specified was out of the question budget-wise. After a little discussion I understood his concern, and realized he needed to lock the footing in with something better than the soils at hand, and compaction would have slid the whole project down the hill. I suggested the lean fill, he did the calculations, and he approved it.
There is almost always a way to do a good job and get what you want for a result if you keep an open mind and employ professionals who are similarly inclined. As previously noted, all engineers are not created equal, so it's worth shopping around.
Good Luck,
DRC
"If your engineer doesn't express any interest in the soil type (i.e. if he doesn't want to do a site visit), find another engineer. "
Absolutely. I was surprised at Avtom's engineer not dealing with soil type. Seems as though he simply assumed for the worst case scenario and designed the most expensive footing to cover his butt with Vatom's money, instead of doing what he was paid for and running some tests and calculations. But maybe I assume too much.
i'll re-emphasize what you said about the rebar placement. That is one of the most misunderstood concepts I see on the jobs. Guys think all they have to do is throw it in there with no understanding of how it helps cpmpressive or tensile strengths depending on reference location I understand that a wall can have four times the tensile strength just by moving the rebar from one location to another.
Welcome to the Taunton University of Knowledge FHB Campus at Breaktime. where ... Excellence is its own reward!
Absolutely. I was surprised at Avtom's engineer not dealing with soil type. Seems as though he simply assumed for the worst case scenario and designed the most expensive footing to cover his butt with Vatom's money, instead of doing what he was paid for and running some tests and calculations. But maybe I assume too much.
You assume correctly. I don't think much of our engineers. My first wall, 50' wide with 15' of backfill has a 3' curve in it. I asked the engineer how much the curve helped. His answer was that he was designing a straight wall which would be cheaper to build, including over-reinforcement, than paying him to figure in the curve. Site visit? I've never heard of one outside large commercial projects. And there are a lot of failing foundations around. Fortunately, mine aren't any of them.
The point about the expensive footing, however, probably isn't valid. Assuming even 50% over-building, my footing was less expensive than a lot more engineering time. The same engineer went ballistic when I went back, with a client, and he heard that I was reusing the engineering. Thought that was horrible. He wanted to be paid a second time. Actually, it was the third use. Similar soils on all sites.
We were inquiring into even more backfill which shocked him. When I asked about a process of using polystyrene blocks to displace the dirt (used 70 miles away), he said he'd heard of it and had no intention of knowing anything more. Got the same answer when I asked if he could design a thinshell concrete structure, like a hyperbolic parabola. I have most of the engineering, but need somebody to put it together for a higher than normal load. Ain't gonna happen with our local guys. Client gave up and built what I had engineering for.
This emphasizes the potential problem with the stock "get an engineer" answer. There may not be a good one available. Bring one in from afar? I wouldn't know if he/she was any better than the local talent. Not necessarily a simple solution.
There are also books of drawings of "stock" retaining walls. Soil assumptions? Beats me.
PAHS Designer/Builder- Bury it!
your use of a 5'1" footing under a 12" block filled and reinforced wall seems unique. Did you use the footing "inside" the wall as a floor. Was the wall centered on the footing ?
Sorry, no block for me. As previously described, the footing is to keep the wall vertical. Footing can be either mostly unburied or buried. Design changes if you decide not to have the dirt weight resting on it. All mine have dirt on top. Made for a simpler footing and a nice place to work when building the wall.
There's a reason you want to use block? Cast-in-place concrete is really simple, as is rebar placement. Also as mentioned, you really want to pay attention to where the engineering says to place the rebar. No expert here, but I've poured 400' of retaining wall successfully (various places), with up to 15' backfill.
I wouldn't have any idea how to do your wall with block.PAHS Designer/Builder- Bury it!
A thought, while you are making Plans, be thinking and asking, how soon can I backfill my wall,, 28 days you say!!!, with my floor system in place too. I 'am figureing that you will have the cadillac of drainage systems behind your wall.This last one is not directed at you, just a general thought of mine, A lot of people, just plain have a hard time grasping the ideal, of spending thousands, upon thousands on their foundation. Bottom line, is building cost money. good Luck Jim J
The soil type is significant because the angle of repose for that type and the weight of the soil will determine the amount of pressure on the wall.
I, too, would go with an in-situ concrete wall and design the rebar to slab and wall so that they work as a unit -- the slab functioning as the toe of the retaining wall.
Efficient drainage of the soil behind the wall is also important -- trapped water will add a significant load to the wall as well as de-stabilising the soil.
Definitely one for the engineers!
IanDG
I've been thinking some more about your question, and I'm wondering if this is a DIY job.
If so, you might consider using ICF. Reward has an 11" block and a 13" block that is easy to use.
With #5 grade 60 rebar on 2' centers with 2' bends into an overturn footing you can get amazing values.
Again, you'll need an engineer. Rebar placement and footing design is crucial.
But at least this way you could do it yourself.
Don't let the engineer push you into a #6 bar if more #5 will work. Cutting #5 grade 60 with a cutter bender will give you a workout. Cutting #6 is a whole different story.
Please let us know what happens.
DRC