Guys, Been away from the construction game for awhile so I hope you can enlighten me. Currently doing the framing for the second floor of a ICF home. The specs call for a vapor barrier behind the sheetrock and R 38 insulation in the attic. This does not seem like a good idea to me considering the fact that any moisture in the home will essentially be trapped. The house is located in New York By the way. Leave vapor barrier and install air exchanger? What about the bathroom and also there is a second floor laundry room to add to the problem.
Discussion Forum
Discussion Forum
Up Next
Video Shorts
Featured Story
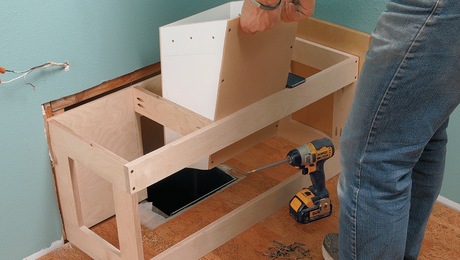
Learn how to plan, fabricate, and install a chute to conveniently send your dirty clothes from an upstairs bathroom or hallway to your laundry room below.
Featured Video
Builder’s Advocate: An Interview With ViewrailHighlights
"I have learned so much thanks to the searchable articles on the FHB website. I can confidently say that I expect to be a life-long subscriber." - M.K.
Replies
By all means, use a vapor barrier and seal all openings into the attic. You want to keep the movement of moisture and warm air into the attic to an absolute miniumum. Also, avoid recessed light cans and duct work up there. This will save energy, avoid moisture problems and prevent ice dams.
The bathroom should have its own vent fan (Panasonic) ducted to the outside. You might want to allow a little make-up air for the dryer.
Al Mollitor, Sharon MA
I keep on being surprised about the use of a vapor barrier in the States. By code every house built in Canada must have a 6 mil sealed vapor barrier. New York is just across the border the climate is not that much different than Canada's.
A vapor barrier does not trap moisture what it does is prevent moisture born in the air from migrating through the building materials (gyproc, insulation) and condensing back into water when it finds a dew point.
If you have wet insulation chances are there isn't a vapor barrier.
I would be really interested in discussing this especially the use of VB in hot humid climates, Florida for example where I know it is not used.
At last,another well informed canuck (me too) on this Vapor Barrier technology.
And I agree,in New York or even Florida, a temperature of 30 degree F is the same . And condensation and moisture has the same effect no matter where you live.
"And I agree,in New York or even Florida, a temperature of 30 degree F is the same . And condensation and moisture has the same effect no matter where you live."But which surface is the condensing surface changes drastically.In Fl you might only have the 30 degrees for 10-20 days out of the year.But for maybe 120-180 days you will have where the outside is 90 degrees or better and the RH is 75% or higher.If you put poly on the inside of the insulation like you do Canada then you would have a lake behind that wall.Or places like where I am where we have about 2-3 months where the moisture is being driven in and 4-5 months where it is being drive outwards.Yes, moisture control is critical.The other is to have systems that will tolerate a very small amount of condensation and then allow it to dry.But an poly barrier is not always the best way to go.Most moisture moves via air leaks, not through the building materials.So, expect for the extreme cold climates sealing air leaks. Is the main element in controlling moisture problems.
No, you would not have a lake behind the wall if you put Poly (V/B) next to the insulation. Millions of homes in Canada are done this way with no problems with moisture what-so-ever.
Vapor barrier is always applied on the heated side of the home.
Working from the interior to exterior the correct order of installation is ;drywall, 6 mil poly v/b on stud face, , insulation,tyvex, siding.
Edited 2/6/2005 8:29 am ET by Hube
Hube,
You are right about putting the VB on the heated side but in Florida that would be the outside of the wall for the vast majority of the year. Not the inside like up here in Canada.
I expect a wall system that allows a quick evaporation from the cavity would be a better choice in Florida.
The reason the VB is on the inside of the house under the gyproc is because of the moisture created from cooking, bathing, washing and human bodies living in the house. Enough air borne water vapor is created that if allowed to condense on or in the walls water dampness will result. The VB is on the warm side so the moisture evaporates and is allowed to dry from air movement in the house.In Florida I take it the humidity inside the house is equal to or greater than the natural humidity outside. Is this why VB barriers are not used in these warm humid areas?If I were to build a house with no VB and live in it the house would be completely destroyed. The moisture in the air would permeate all of the gyproc surfaces, move into the insulation, condense at a dew point and saturate the entire building structure.
"If I were to build a house with no VB and live in it the house would be completely destroyed."Define vapor barrier?Too often that term is used to mean poly film.No one is suggest that moiture vapor not be CONTROLLED.But depending on a film has several drastic problems.All the vapor stops at a single point that does not have any insulative value. So anytime that you have the "wrong" conditions then you will have condensation on the film.Any water that you do get on the film, either through condensation or by minor leakage through the weather plane can't is limited to drying to one side.http://www.buildingscience.com/resources/articles/Understanding_Vapor_Barriers_ASHRAE_2004_08.pdf"Vapor barriers are also a cold climate artifact that have diffused into
other cli-mates more from ignorance than need. The history of cold climate vapor barri-ers
itself is a story based more on per-sonalities than physics. Rose 2 regales
readers of this history. It is frightening that construction practices can be so dra-matically
influenced by so little research and reassuring that the inherent robust-ness
of most building assemblies has been able to tolerate such foolishness.The Incorrect use of vapor barriers is leading to an increase in moisture-related
problems. Vapor barriers were originally intended to prevent assem-blies
from getting wet. However, they often prevent assemblies from drying.
Vapor barriers installed on the interior of assemblies prevent assemblies from
drying inward. This can be a problem in any air-conditioned enclosure, in any
below grade space, or when a vapor barrier is also on the exterior. Addition-ally,
this can be a problem where brick is installed over building paper and
vapor permeable sheathing. An excellent discussion about the dif-ferences
between vapor barriers and air What Do We Really Want to Do?
Two seemingly simple requirementsfor building enclosures bedevil engineers
and architects almost endlessly:
¨ Keep water out, and
¨ Let water out if it gets in."http://www.buildingscience.com/resources/walls/Vapor_Barriers_Wall_Design.pdf"Ideally, building assemblies would always be built with dry materials under dry conditions, and would never get wet from imperfect design, poor workmanship or occupants. Unfortunately, these conditions do not exist. It has been accepted by the building industry that many building as-semblies become wet during service, and in many cases start out wet. Furthermore, the industry has recognized that in many circumstances it may be impractical to design and build building assemblies which never get wet. This has given rise to the concept of acceptable perfor-mance. Acceptable performance implies the design and construction of building assemblies which may periodically get wet, or start out wet yet are still durable and provide a long, useful service life. Repeated wetting followed by repeated drying can provide acceptable perfor-mance
if during the wet period, materials do not stay wet long enough
under adverse conditions to deteriorate.
Good design and practice involve controlling the wetting of building
assemblies from both the exterior and interior. They also involve the
drying of building assemblies should they become wet during service
or as a result of building with wet materials or under wet conditions.Moisture BalanceMoisture accumulates when the rate of moisture entry into an assembly
exceeds the rate of moisture removal. When moisture accumulation ex-ceeds the ability of the assembly materials to store the moisture with-out degrading performance or long term service life, moisture prob-lems result.Building assemblies can get wet from the building interior or exterior, or they can start out wet as a result of the construction process due to wet building materials or construction under wet conditions. Good de-sign and practice address these wetting mechanisms. Various strategies can be implemented to minimize the risk of moisture damage. The strategies fall into the following three groups:
¨ control of moisture entry
¨ control of moisture accumulation
¨ removal of moisture"
Bill, 6 mil poly film is used as a vapor barrier, I think we are talking about the same thing. I can just go by my own experience, I have seen houses without or poorly installed VB and it is not good. Millions of houses are built with VB with no ill effect.I worked for a housing corporation during the seventies at the height of the new energy awareness. There were insulation/VB/efficiency gurus who advocated all kinds of 'new' methods. Saving energy took on a holy grail type of atmosphere, science and practicality went out the window. The material you posted seems more opinion orientated than practical application.
Did you read the articles? Where they discuss the differences between vapor impermeable, vapor semi-impremealbe, and vapor semi-permeable materials?And where they dicuss the different climate zones? And where the show the temp/humidify profile through the walls for different construction in different zones?
Sorry Bill I didn't, if I had a dollar for every course, seminar, etc, I took over the years I would be rich. It comes down to what works and proven construction practices. VB, 6 mil poly off the shelf works, with no problems, hundred of thousands of times.
Hey, Dave ,i'm on the same path you are. The correct one.
Millions of homes over the years have proven these methods.
This "bldg science" stuff has not been in effect too long to ever be really proven.
Afew years from now they will probably find out these "new" methods are fatal.
Thanks, Bill ,but no thanks, I'll stick to methods that have many ,many years of proven beneficial results. Hube
"Hey, Dave ,i'm on the same path you are. The correct one."
Bill's taking a beating, but that response implies a closed mind.
Many structures also have moisture problems with vapor barriers installed.
There is growing evidence that many moisture problems previously blamed on driven vapor are actually caused by moisture travelling on air currents.
'Convention wisdom' is not automatically right. Conventional wisdom has fiberglass batts as the #1 insulation material. Conventional wisdom has R-values as the end-all be-all measure of thermal performance. We have vented crawlspaces, and vented cathedral ceilings mandated by code. Both good and bad ideas make it to the mainstream of construction practice. The hard part is getting rid of the bad (or inflexible) ideas once they become mandated.
CSNOW, agreed.
Typically, in wet tropical climates (south FL) 6 mil vapor retarding barriers do not go on the inside as they do in upper NY. By all means in a tightly concealed space exchange some air but this is conditioned air, key.Mr. Hartmann has it right.I'm an architect who is not particularly interested in creating moisture problems for clients so it is important to know WHERE you are working. It is not fools' gold to research and find the perms of construction assemblies and materials. Hardly.
Too, I would say that the Building Science information (link) is hardly new or unproven. When examining it one will find that those practices have breakdowns to various locales (moderate - wet; dry - arid, etc). BS does take issue with some local (routine)practices but primarily refutes the current codifications relating to venting, as an example.
"Typically, in wet tropical climates (south FL) 6 mil vapor retarding barriers do not go on the inside as they do in upper NY."
In the south, they have all sorts of moisture problems too, sometimes made worse by vapor barriers on the outside. The mid-atlantic is really rough, since it is very hot and humid in the summer, and plenty cold in the winter. There is no good place for a vapor barrier. I predict more adoption of the 'airtight drywall approach' in the longer term. Besides accepting the science, one hurdle is that it requires more care (time and skill) to get the details right.
"BS does take issue with some local (routine)practices but primarily refutes the current codifications relating to venting, as an example."
If we start calling the outfit BS, that could be troublesome. Welcome. This board could use more input from architects. Pretty scarce around here. Maybe the architect bashing threads scare y'all off.
"Working from the interior to exterior the correct order of installation is ;drywall, 6 mil poly v/b on stud face, , insulation,tyvex, siding.""Vapor barrier is always applied on the heated side of the home."And when the HEATED SIDE (by the enviroment) is on the OUTSIDE what is the aseembly.And where does the poly go when the HEATED SIDE is on one side 6 months ofthe year and the other side the other 6 months?
I would rely on tried and true practices in each particular area.
Thanks for the reply. I think I am going to look into an air axchanger to see if this air is conditioned before being brought into the house. I am also concerned about this house being to tight because of the type of construction. As of right now there will be six people, two full baths and a laundry on the second floor, not to mention a steam bath in the master bedroom. I am thinking we had better be careful about getting this vapor out.
If you do build a tight house, you do need some sort of air exchange. Personally, I think an HRV is the best bet in a cold climate.
Do vapor barriers work? About 2 months ago, I had to run some vents between the joists to the outside. Some of the rim joist was insulated and had 6-mil poly, some had no poly and some had no insulation. Where there was no insulation and and where there was insulation and poly, the sheathing was bone dry. Where there was insluation only, The sheathing was soaking wet. You could wipe the water off with your hand. Outdoor temp was -20, indoor temp was 70, basement was poured 8 months earlier and the house was not occupied.