*
I am a carpentry contractor that works in Southeast PA. Last November I built an addition to the front of a home that involved a 5/4 x 6 mahogany deck. This deck was built with a pressure treated structure. The mahogany was fastened with a concealed system made by Ebty. This system uses a plastic biscuit with a stainless screw. Each board is biscuited on each side of the joist. I regretably did not use any glue. This deck was built over stone and is approx. 27″ above grade. The deck is attached to the house on two sides. The other two sides have newly built stone walls. The new stone work did not have any vents in the architects’ design. I believe the failure is due to lack of ventilation. The client is asking me to repair this. Before I assume responsibility, I would like to be sure that I am not solving another design problem at my expense. I also want to be sure to properly warranty my work. To further complicate things, the architect is a friend as well as a business associate for years. The client however, was the only client I worked for that I would never consider working for again. Also, this deck has no overhead protection, no sealer or coating was used on the boards and the deck was built level.
Any advice or opinions would help.
Discussion Forum
Discussion Forum
Up Next
Video Shorts
Featured Story
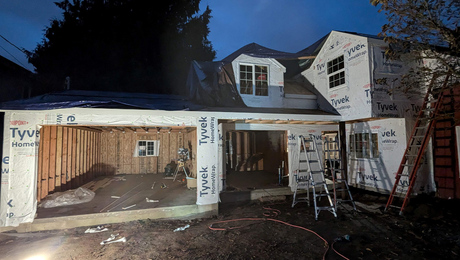
The FHB Podcast crew takes a closer look at an interesting roof.
Featured Video
How to Install Exterior Window TrimHighlights
"I have learned so much thanks to the searchable articles on the FHB website. I can confidently say that I expect to be a life-long subscriber." - M.K.
Replies
*
AJC,
You described the situation pretty well, but you didn't tell us what the problem is.
*AJC-As Luka said -please tell us the problem.I'm guessing you are getting warping do to moisture, since the deck is not covered and the stone mason(not the deck builder) did not allow any ventilation and the homeowner did not apply a sealer after completion of the work,and you are using 6" instead of 4" 5/4 decking which is alot of surface area when biscuit jointed for outdoors.So exactly what did you promise your customer?I don't think glue would have solved the problem.Clarification of maintaining the deck with a sealer for warranty purposes might have been a good idea.Ventilation is a must.Friends or not,the architect is usually an artist,not a builder,and what looks good on paper is not always the most practical,structurally or cosmetically.Please tell us more.Bob
*AJC.I think I know wha your problem is without you decribing it. The boards are probably cupping, meaning that they are now concave instead of flat.I have had this problem as well with 5/4x6. The way to prevent this is to treat all 4 sides before installation with either a product called messmers hardwood deck stain or cetol by seikens. I've also been told that this is just the nature of the wood when it is that wide. Wheather this is your fault or not is a judgement call. If it was me, I would pull the boards up, treat them, then flip them over. You will notice that the side facing down still look like new. Flipping the concave boards over will eventually take some of the bow out. Hope this helps.Jay
*AJC - 5/4 Meranti decking warps a bit (unpredictably) after installation, particularly in strong sunlight. A large one that we did with self-countersinking stainless screws is holding up pretty well - maybe 2 or 3 boards warped and were replaced on 1,200 SF. A UV-inhibiting deck sealer should be used - and any stain/finish should be on all sides. I find it hard to believe that all of it is warping - what percentage is the problem?Jeff
*The problem is warped boards. Crowned like a tee-pee.No sealer was specified. The architect told me they had completed many other projects like this with no problems.Although I thought that it would be nice, the client did not want to pay an additional work order.The perimeter walls offer no vents. The only venting we have are the spaces between boards. They are only an 1/8 inch.This space is regulated by the eb-ty fastner. Tell me more about sealing and the uv-inhibitor. About 3o% are warped.NO specific mahog was specified.
*AJC - I'm not sure what was used - maybe Cabot's? I'm not sure that it matters as long as it is a quality sealer. Most of the 5/4 x 6 mahog decking is Meranti - I think - maybe a lumber yard guy can confirm. I don't believe anyone who says "we've used this all the time and never had problems" - it's pretty well known around here that Meranti can move. I suspect that the concealed (edge-biscuit) fastening might permit more movement than face screwing (edge cupping forcing biscuit to bend/fail?). 30% is a lot of boards to have warp, but it's the nature of the material. Click here and go to b Wood Myth #8 "When you buy mahogany you get mahogany" for more info.My guess is that with face-screwed fasteners and sealer you would have been more like 1-3% warpage ("normal").Jeff
*The boards are crowned like a tee pee. Was any expansion space allowed between the decking?
*It's not that - if boards are restrained at the i edges only(by a biscuit retainer) and can't warp down (due to construction below) the board has only one direction that it can move - the center will move UP. If they had been face screwed this cannot happen as readily, since the center of the board is restrained from moving up.Jeff
*
I am a carpentry contractor that works in Southeast PA. Last November I built an addition to the front of a home that involved a 5/4 x 6 mahogany deck. This deck was built with a pressure treated structure. The mahogany was fastened with a concealed system made by Ebty. This system uses a plastic biscuit with a stainless screw. Each board is biscuited on each side of the joist. I regretably did not use any glue. This deck was built over stone and is approx. 27" above grade. The deck is attached to the house on two sides. The other two sides have newly built stone walls. The new stone work did not have any vents in the architects' design. I believe the failure is due to lack of ventilation. The client is asking me to repair this. Before I assume responsibility, I would like to be sure that I am not solving another design problem at my expense. I also want to be sure to properly warranty my work. To further complicate things, the architect is a friend as well as a business associate for years. The client however, was the only client I worked for that I would never consider working for again. Also, this deck has no overhead protection, no sealer or coating was used on the boards and the deck was built level.
Any advice or opinions would help.