*
recently we installed a hip truss
package on a 24’x40′ house. after
plumbing and bracing we nailed on
spacers – then had to fight the trusses
during sheeting. using a long 2×6 to
tweak rafter against chord and vice
versa we took care of most of the warps
but when it came to some of the rafter
tails they’d be out 3/4″ over 18″ and
they’re was no leverage to beat them
into place. anyone ever had this much
trouble with factory made? any comments
about whether it’s just better to build
them yourself?
Discussion Forum
Discussion Forum
Up Next
Video Shorts
Featured Story
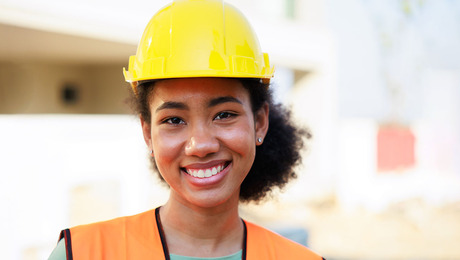
The "She Build" initiative is empowering women in Seattle, WA by ensuring they have safe, healthy homes.
Featured Video
Builder’s Advocate: An Interview With ViewrailHighlights
"I have learned so much thanks to the searchable articles on the FHB website. I can confidently say that I expect to be a life-long subscriber." - M.K.
Replies
*
salem,
If I were you, I might consider finding another truss company.
Unless your top plates and walls were out big time, you should not have had that much trouble. I'd get the salesperson back out there to see what you got from their factory.
Ed. Williams
*Two things come to mind. First, they may simply have been made from warped lumber. Truss manufacturers sometimes get bad loads of lumber, just as lumberyards do. The second may have to do with the way trusses are currently manufactured. Years ago, large hydraulic presses were used to press the plates in at each joint. This type of machine produced a very flat truss, but isn't very common anymore. That majority of trusses are manufacturered with roller systems. Large metal rollers pass over the truss and press the joints into place. This can sometimes create a bit of "curl" in the truss. But it shouldn't be real bad unless their roller is out of adjustment. You say the tails were "out 3/4" over 18"". Out which way ? Too high, too low, or twisted to the side ?Also, have you talked to the truss manufacturer about it ? If no one tells them, they'll never realize they have a problem.
*
salem:
Ditto on telling the truss manufacturer. You or the homeowner pad dearly for the ease of installation and convenience of trusses. Extra work doesn't save any aggrevation or money for anyone.
I once made very, very detailed drawings for the manufacure of a truss to match an existing roof line. In spite of the great pains that I went to to ensure the correct truss, they arrived 3 and 1/2 inches off over a 7 foot roof line. Too much to correct on site. The site happened to be a few hours away from our normal working area and I had to go through the trouble of finding extra help for the day. The truss manufacturer had to load them up by hand and rework them. Waste of his time and mine. Put the job back by an additional seven days and the decking got soaked by a week straight rain. Lots of fun!
Have no mercy on the truss company the next time it happens and don't ever rack or twist a truss to fit. You'll regret it over the inevitable call-backs to fix popped drywall, wavy ceilings, and cracked wall joints.
*
recently we installed a hip truss
package on a 24'x40' house. after
plumbing and bracing we nailed on
spacers - then had to fight the trusses
during sheeting. using a long 2x6 to
tweak rafter against chord and vice
versa we took care of most of the warps
but when it came to some of the rafter
tails they'd be out 3/4" over 18" and
they're was no leverage to beat them
into place. anyone ever had this much
trouble with factory made? any comments
about whether it's just better to build
them yourself?