*
Discussion Forum
Discussion Forum
Up Next
Video Shorts
Featured Story
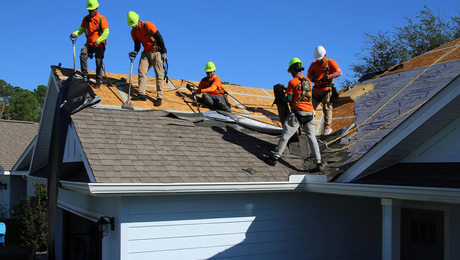
Listeners write in about haunted pipes and building-science tomes, and they ask questions about roof venting and roof leaks.
Featured Video
How to Install Cable Rail Around Wood-Post CornersHighlights
"I have learned so much thanks to the searchable articles on the FHB website. I can confidently say that I expect to be a life-long subscriber." - M.K.
Replies
*
what is the proper method of waterproofing a bench in a tile shower? This is in new construction.
*
Michael Byrne has a great tile installation book out- the best I've read. He's got a section about mudding showers. Follow his advice. He's also written articles on the web- search under his name? If you don't have experience here, I'd sub out at least the shower pan/bench.You can do the tile, etc. Have fun.
*Post your question to http://www.jlconline.com/forums/tile/Assuming it is solid (wood or masonry underneath), treat it just like a shower floor, which means CPE.
*Rich and others had nice responses a while back...I think it was TinaG that had in improperly sloped bench and had to redo it?Try a search using "TinaG" and "bench", something on those lines. Aw, heck... here it is...not quite the one I thought it was.
*Any guy so oft referred to as M.B. is over rated.Here, I'm gonna' still his thunder, commit this to FHB archives, and develop my own referral-based bidness.Keith, new construction? Then you have a wood frame, yes? (If you're really sharp, you get the rough bench built modular to the size tile you'll be using)One, cut back the drywall to height of 3" min. above the bench. Do the same on each side where the bench meets the walls. Remove any drywall or other material from top, sides, and front of bench. You should now have a wooden frames of the desired rough dimensions with the wall framing exposed around the bench.Use a waterproof membrane to cover the bench from the shower receptacle to the cutout on the wall above the bench. This membrane should extend down to and lap over the shower floor pan membrane. If this membrane is not a single piece, each piece should lap over each successive piece by 2"min. In this case, the first piece will be at the bottom of the bench working towards the top of the bench. Each joint should be glued with a waterproof--when cured--adhesive. The membrane can be held in place by nails or staples, but do not penetrate the membrane on the bench top, front, or sides. It can be done. Be methodical during installation and avoid any wrinkling of the membrane. Any ex-mil out there know what I'm talking about when I say any folds in the membrane should be "hospital corners". Make your corners as tight and as flat as possible. Now you are ready for a mud mortar setting bed over metal lath. If you are using a backerboard, simply nail board on vertical surfaces only being mindful to not nail below 3" above ht of finished curb.HTH
*And if you build this shower like Rich says and have to cut DRYWALL back 3' above bench STOP NOW and decide to use Durock behind those shower walls
*Embed the Durock in the mud about 2 inches.
*
Tile setting! I love it! The only thing that brings up as many different opinions as ventilation!
Mud! Thinset! Sheetrock! Durock! Plastic! No plastic!
*
Joel, ya go that right. Assuming one would want an installation that is long-lasting and beautiful to look at, one would want to do the job right. Further, because you are introducing a water source into the home in the form of a shower or tub, one would want to use the proper methods and materials. Based on alot of work I have seen over the years that's a big assumption.
Not all these crappy jobs started out that way. Some built down and dirty and called it good until the check was cashed, but that's a separate subject. Homeowner and tradesman alike have chosen the wrong installation method and/or substituted materials called out for a particular installtion.
Most of us know you wouldn't use an aliphatic glue for outdoor furniture and expect it to last. In the same manner, you wouldn't use an organic mastic for tile installation in a wet area such as a shower (even though this type of installation method can be found in recent issues of the TCA Handbook). Nothing wrong with these materials, just misused.
Myself, when I charge money to perform actual work on a res or comm job, I make damned sure I'm not about to be bit in the years to come. Think of it as CYA. Then there is the personal pride I feel from a job well done. Only the proper methods called out for the job will do. Sure I can use alternate methods, but time does tell.
Also, when I go into a job, people are deferring their opinion to mine. I'm the expert. (I don't mean I'm perfect, only that they want my "expert" opinion) To preserve this trust I make very certain the methods and materials I plan to use are intended for the job at hand. This may mean I contact the mfg or do other research before proceeding.
I was on a comm job laying 28,000 feet of slate in 40 rooms of a lodge. The arch did all the hiring. He had rough carps cutting and installing a tile backerboard for all the soaking tubs and shower walls. The backerboard was glued with a Type II mastic to fiberglas panels. I told him this wouldn't last. Before we finished the job, some of those units failed when the backerboard and marble tiles sheared off the fiberglas. Others failed when the fiberglas panels on the exterior wall overheated in the sun--all the units had the same layout to maximize the view--and literally popped from the nails or screws holding them in place. Same job, different installation: the resturant floor--not my bid--failed because the knothead putting it down decided to skip the mud bed and layed the tiles into 1/2"-1 1/4" thinset. The arch approved this. Eight months later, the entire floor came out.
The point: the fibeglas panels were innovative as all get out but the combination of materials and performance expectations doomed the installtions. Also, thinset mortar is not intended for such thickness. The materials weren't up to the performance required.
I have repaired over 200 tiled showerstalls. Some only suffered because of a structural defect not associated with the shower. Most were because of a poor choice of materials. These represent job security for me in the repair market. Still, I'd rather not see inferior work.
*
Joel I hahe recently installed a shower with a bench in it and this is how i did it.
First I built the bench out of red wood and used stainless steel hardware to fasten it together, after it was made I glued down to the bench some of the material that I used for the shower pan being careful not to leave any open seams (where water could enter,) using the recomended glue for the particular liner in question.Then after a suitable period of time I laid a coat tile mastic down and set the tiles, grouted as usual its been 3 years and no leaks yet. I built thes against the wall and built in an inspection panel in the adjoining room just looked in there i week ago all is well.
Michael.
*