*
… and can tell me how this got made. I saw an incredible vanity top made of Marine-grade plywood. It was one piece and had a RADIUS CURVE to it that formed a bathroom sink basin, all out of one plywood piece. Had a tempered glass front and wood splash at back to contain the sink water – NO preformed sink compartment, just plywood and glass. Faucet was above into wall not vanity top. Curve must have had a +/- 7″ radius. Any ideas.
Hours of Steaming?
Discussion Forum
Discussion Forum
Up Next
Video Shorts
Featured Story
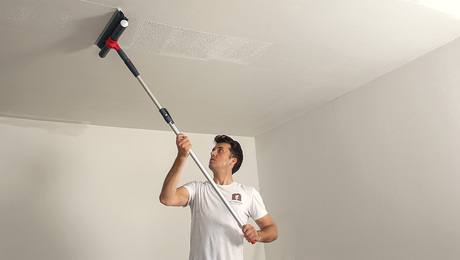
Skim-coating with joint compound covers texture, renews old drywall and plaster, and leaves smooth surfaces ready to paint.
Featured Video
SawStop's Portable Tablesaw is Bigger and Better Than BeforeHighlights
"I have learned so much thanks to the searchable articles on the FHB website. I can confidently say that I expect to be a life-long subscriber." - M.K.
Replies
*
Well, here is a look at the sink/countertop. The file is about 66k - hope that doesn't present any problems.
*
It appears that they may have used several pieces of ¼or 4mm to 6mm plywood. They made a top and bottom mould and squeezed it all using epoxy as the glue. Build a jig for the router to rout a grove at the front for the glass. They set the glass in epoxy or silicon. Many marine plywoods are made from African mahogany. The epoxy is also used as a water sealer it is know as the west system Varnish can be applied over the epoxy as an addition finish and as a UV inhibitor. Bronze screws to faster the bowl to the back with epoxy and it all done.
*Nice looking sink. Kerry sounds like he has the answer there are one or two other ways but what he says seems the most likely. Gonna give it a try Yourself? Let us know how it works. You may be interested in contacting the Gougean brothers who send out a newsletter about West system epoxy and some unique applications. I'm not sure if I spelled their name right but i believe the publication is called Epoxy works and is also usually available at West System dealers. Good luck, Skip
*Another approach to it would be to build a form as Kerry described, and lay up multiple layers of veneer with the grain running in the same direction, and press it in a vacuum press (or using a mating 'caul' if you don't have a press). You can get all kinds of curves and compound shapes that way; the advantage of having the veneers run the same way is you don't get that plwood look of veneers alternating direction on the exposed edge, it just looks at first glance like solid wood. Resorcinol glue is easier to work with for the lamination in this type of thing, seal with epoxy like the other guys said. But if this is not a one-off, but from a manufacturer, they may be using one of several new systems to impregnate the fibres of the wood with a resin to counteract wood movement. Very nice.
*
Hey thanks. I'll still wait to hear more but I've gone ahead and printed these responses out. I just needed a place to start. You've given me a clearer picture on were to go. I've shown it around and when I broached the subject of whether or not they could do this I've had most people kinda 'roll their eyes at me.' I don't think they knew where to start; and, I only knew that it was "marine-grade plywood."
What is really striking about this design is the way the contemporary curve of the sink and glass front mates pretty well with the "old time" look of the wall fixtures -- my view. Many thanks.
Phil
*Hello Skip, I would only try this one MYSELF if I definitely had the right system to use and a cabinet maker friend helping me along. The one other person locally who had any idea at all said that it might be able to be done with a new product called "flexible plywood," sorry I don't have a tradename as of yet, but it is a plywood he said that has one side 'scored' and is in thin sheets. I'm not sure if it is Marine-grade or not. I was also wondering if it was absolutely necessary to use Marine-grade pwd, if you could find the right epoxy, sealant and finishes could you go without using m-g pwd? Any ideas on that one.I might be wrong, but I think this is actually a piece of craftmanship from Britian (it was in a British publication) -- this would figure wouldn't it, Shipbuilders!I know that Marine-grade would be best but just wondering about availability in 1/4" sheets as Kerry said.Gotta tell you, I was hoping that someone would say, "I know of a company that has a product line of various curved shapes to Pwd." Maybe next time. :)
*
I really like that.
*
Jim, we've done countertops before here but never anything that 'tricky.' It is always nice to devise a way of making a great product, cheaply -- isn't it?
We did an entire office workstation layout, oh, 'bout 65Lf of 3 ft. deep desktops, continuous, flowing around half walls, all out of MDF w/ spar-varnish satin finish, w/ oak bevel edge. The MDF is real stable and the amber tone to the finish of it is real warm. When light hits the stuff it really picks-out the small sand-grain sized black pixels of the MDF. NO one believes it is MDF.
Always looking for the near impossible,
Phil
*
JUST MDF + spar varnish? And it doesn't look like old cardboard? I'll have to try this.
*PRP; the big difference between regular ply and marine is the glue; resorcinol for marine as against urea formaldehyde. You can make your own ply if you want (you need a press though); some shops still do, but it's usually cheaper to get the veneer supplier to lay it up.the only product I know that's scored on the back is called kerf-core, and it's MDF; great for interiors, but I don't know in this application. Flexible ply wood is basically two thick pieces of veneer separated by a piece of fabric; you specify if you want it to bend along the length or the width. You have to face it on both sides after you establish the curve with laminate or a face veneer. You would still be faced with an ugly front edge (can you get a close look at that and see which way the veneers run; right angles to each other like ply, or all in the same direction? I'm willing to bet it's the latter).As far as a company that makes curves like these, big chair factories are one source (think of all the curved plywood seats and backs on wood chairs; a lot of them are formed into more complex curves than this). If you just want one or two, a cabinetmaker with a vacuum press could do this pretty easily.
*
OK, I'm impressed.
I remember that one of the most striking types of rifle stocks I ever saw was made of a laminate of two contrasting woods like walnut and maple. The sheets were 1/16 to 1/8 thick and pressed together under high pressure with epoxy glue. This resulted in complete saturation of the wood with the epoxy and eliminated any wood movement which was critical in high-power tack-driving rifles.
The marine grade plywood in this sink has water-proof glues and is probably made of woods that are resistant to water emersion. I wonder if it may also have copper or mercury based additives that discourage marine creature growth like they have in antifouling paint?
*Adrian:Thanks for the information. I will look more towards the cabinet shops. And, the plys are all parallel to one another as much as I can tell -- it's a pretty clean looking edge.Phil
*Ditto for me too. Jezz, that is b onenice looking piece of work. A very fine example of what can be done with simple materials, elegent design, imagination and some serious know-how. Beautiful. If any of you that do try this and pull it off, post it, I would be curious as to how simple/difficult it is. I have a basement bathroom to put in (one of these days, you guys know how it is) and I would like to something of the showpiece variety (ssuggestions????). Simple, elegent without breaking the ol' budget.Fascinatedly yours, cybergreg.
*that is one nice looking custom sink. making curved pieces like that are so much easier than most people imagine--especialy since the advent of vaccuum presses.unfortunately, it'll look like shit in 6 mo.'s to a year, unless of course the clients never turn on the water.
*
PRP,
I guess you could use bender board in a form to build up the shape. It comes in either 4x8 sheets or 8x4 sheets depending on what your making. I've used 1/4", 3/8" and 1/2" bender board ( bending plywood my supplier calls it ) but you would have to veneer the surface because it usually comes with a luan face.
Curved plywood furniture was very popular back in the 50's. I would think that these pieces were factory made with some incredible machines.
I don't have a clue how this "sink" was made, but I would LOVE to know how it was done.
Thanks for sharing that with us.
Ed. Williams
*However and by whoever it was made, this is one hell of a nice piece of design/workmanship!!!
*
Regarding Bullet's point about this design not lasting more than 6 mons to a year, any comments to that? I've never worked with marine-grade plywood before. Is the resorcinol (sp) for bonding in it 'totally' waterproofed, preventing layer separation and delam.? I would think that a surface treatment would be the first level of protection from delamination.
Much appreciated.
Phil
*
PRP Since I don't know Your experience I may be out of line telling you to go ahead but that's what I'd do. Nothing beats a failure like a try. So you end up with a freeform doorstop or books ends. Try and find someone in Your area with some boat building experience. You may be able to buy part of a sheet of 4MM marine ply. They may also be able to give You a hand. Wooden boat builders can be quite helpful. On the marine plywood question I always believed that the big difference between marine and standard plywood was that marine plywood is free of voids which would affect bending and integrity in a hull. For a sink where Your life won't be on the line You've got some flexibility.For what it's worth. Skip ps. You are right that the surface is all that should be subject to moisture and glassing the top may work well.
*Try to find a supplier in your area that markets Finnish birch bending plywood. It's resin bonded, so it's good for interior/exterior/moisture applications. No voids.I've seen it in the past in 1/32, 1/16, and 1/8th-inch thicknesses. The 1/16th-inch would work for this application, it can be bent down into a three or four-inch diamter tube. Even though it's only 1/16" thick, it's still a 3-ply and would certainly work in this sink. The 1/8th-inch could work as well, though it's a bit stiffer. The 1/32 rolls so easily you could use it for cigarette paper. Okay, maybe it doesn't roll that tight...Definitely make up a press with male/female halves, and use a good epoxy. West Systems was previously mentioned. They have a great product line and great tech support. You use this ply with properly applied epoxy and it'll never move. Before you even pump the first batch of epoxy, do a few dry runs assembling the plies and clamping it up to get an idea of the working time you'd require from the epoxy. When ready, mix the epoxy in proper and consistent ratios, each batch the same. Apply evenly. Don't go too crazy (fast) when aplying or you could introduce a lot of air bubbles. Use a roller on top of each layer of ply-epoxy sandwich to get good bonding and eliminate air bubbles. Clamp up and have a beverage.Consider purchasing your drain before designing so you can ensure you'll have the minimum radius needed at the bottom of the sink to get a good seal.If you have no luck finding the ply, let me know, I'll dig through my files...
*A friend I mentioned this to passed on that epoxy may bleed through thin veneers. May want to do a few samples first, or at least talk to the reps at West Systems.
*
Thanks Mongo! That's the kind of information I was looking for, epoxy and bleeding. I was telling Adrian that I'm not a Cabinetmaker and need to get a friend who is one to help me with this. It will be awhile - I'm still hoping that this doesn't "blow" the budget.
Phil
*
I'm with Skip about fiberglasssing the surfaces. That stuff is tough and waterproof. That would be my first try. - jb
*Crazy idea -- could you just buy the sink in the picture? Or, as I'm guessing, is it something insane like $5000?
*Breaktime is a forum I seldom look in, but a contributor to this specific topic asked if I'd seen anything like the timber sink discussed here, and might I have any insight on the subject. Follow these links for pertinent information.http://www.iswonline.com (I was trying to give one of those blue underlined easy click deals, but I'm afraid it doesn't seem to be posting that way. Sorry.)Once in there click on Eclectic Woodworking. It's on the left hand side below the barrels and things. About four titles down in the subject list click on the article, "No Joke. This bathtub wood made quite an impression."Towards the end of this article is a link to Image Wooden Sinks (I think.) Click on it, and browse around their website for product range and prices. Considering what they are offering, I don't think the prices are too bad.Personally, I think the sink featured as the opening of this subject is a rather half-cock affair where the rear joint, and the lump of glass tacked onto the front edge is just inviting trouble in terms of leakage (joints and finish,) glass breakage, and cleaning those sharp internal corners. I don't think I would want to copy the design for the reasons I've listed, but making bends like this is not too big a problem. Expensive? Yes, for a one-off, but eminently do-able.To avoid the possibility of glue failure from laminating such a structure, and the water sloshing around, one solution not yet mentioned might be to steam bend a solid piece of teak or iroko. Lock the formed shape into a matching channel routed in the back upright; easily done with a pattern, or use a CNC router. Other possibilities have already been discussed by previous contributors.
*
I'm sure it would be expensive to purchase but one thing I really liked was the clean bend and easy line of the sinuous curve that seems to say 'look it is only plywood.' Not to mention that minimal (-ist) materials doesn't have to mean "schlock" (sp). I'm still holding-out for "Good Design and Craftsmanship doesn't have to be expensive."
I have thought that maybe the material application was wrong for a sink. Corian could do this w/ half as few problems (anticipated). But for the reason or two listed above, Corian just wouldn't have the same 'fit.'
On the other side, I've mused that maybe "sinuous" is the wrong word; maybe it should be "sinister," as in 'sinister curve' and 'sinister design.'
I visited the Image website and I have to tell you that stuff is Over-the-Top. It is great looking. Very machined, not craftsmen. My take.
Still Interested,
Phil
*
If you're interested in a straight copy, you could try contacting the magazine you saw this in and get the maker's name and telephone number. (I think someone else suggested this before.) I'd hazard that the maker would be only too happy to make another one or two and ship it/them, perhaps with modifications to suit your needs. That would be significantly cheaper than developing a new prototype. After all, the designer has already been through this process, and hopefully resolved any technical problems. For instance, I have a very shrewd idea how to make something similar, but as a one off, I wouldn't offer any guarantee.
I also wonder if there is a patent or other legal protection here that might have legal ramifications.
*There's a great company in Ohio that offers curved plywood components, Geometric forms~ 1-800-331-7689. They might do custom work, or you could modify the design to work with their stock items. If anyone is going to try to build this and can't get the proper materials locally, try http://www.aircraft-spruce.com. They carry an excellent selection of specialty plywood as thin as 1/16".I've built alot of curved plywood chair backs and seats using a two piece mold, with long carriage bolts to clamp them together. It's a pretty easy process. After my first attempts I realized that the thicker the plywood, the more spring back. So, now I only use 1/32"-1/16" layers and build the forms with a bit more curve that I want the finished piece. I would also recommend WestSystem Epoxy from Gougeon Bros. for both glue up and top coat. However, epoxies do breakdown with exposure to ultra violet, so always scuff sand and finish with a high quality varnish (water white varnish from Lee Valley is my favorite). Well I guess I've dropped enough company and product names for one day :) I hope this helps. Best of luck to anyone who builds this piece or something like it. Curved plywood forms have opened up alot of design possibilities for me.cms
*As far as practicality, i think it's a power-room kind of lav sink -- to impress the guests -- not the use-every-day sort.Maybe the word you want in sinusoidal? Serpentine? Undulating?Corian = barf.
*
Thanks all; thanks CMS for entering the conversation. I'll check out the sites, keeping passing along any others. I do think that this is simple enough to seem like a minimalist piece. The high backsplash makes it seem like a cross between an old time industrial sink on casters and a institutional kitchen sink, my take.
phil
*
I have to ask -- isn't this the less appropriate forum for this? Did you take it to Knots? (I don't go there, even reading about furniture-making makes me itchy.)
*I'm thinking that marine grade may not be the only way to go. You might look into "Aircraft grade" birch plywood. It comes in all kinds of thicknesses, down to less than 1/8", has multiple plys, is VERY strong, and very nice looking. I would also think that laying up multiple plys would be effective, but I would lean toward resorcinal glue rather than West system in this application. Easier to work with and just as strong. The finish is where you'll prevent water penetration, even with marine grade ply. I would think this wouldn't be too difficult once you got by constructin the jig. I love the look. May give it a try myself.
*Guess who just published a fabulous article which pretty much explains some great ways to do somthing like this? Yes, our hosts, Taunton--in this month's Fine Woodworking, which just dropped on my doorstep Monday. The article is about using a vacuum press to make curved panels. Highly reccommended.Doug
*
Thanks A., Drvnputt, Douglas H.
Ok, well I've never even considered another posting somewhere, just never crossed my mind.
I'll check the Fine Woodworking article out. I'm not a subscriber but I picked last month's up at the newstand.
By the way, 'she's' leaning away from doing anything this "experimental."
*
PRP, man, weren't you around recently when we had the "Words of Wisdom" thread? Best one on there was from some danged Canadian, something like "It's easier to ask forgiveness later than ask permission before". - jb
*
I'll get it done, sooner or later. I'm collecting my data. I missed that posting -- like it much, mistake made, aa!. Recently, I did hear one of ya say "trying to make a silk purse from a sow's ear." That's one quote that is worth as much.
Thanks Jim,
Phil
*
... and can tell me how this got made. I saw an incredible vanity top made of Marine-grade plywood. It was one piece and had a RADIUS CURVE to it that formed a bathroom sink basin, all out of one plywood piece. Had a tempered glass front and wood splash at back to contain the sink water - NO preformed sink compartment, just plywood and glass. Faucet was above into wall not vanity top. Curve must have had a +/- 7" radius. Any ideas.
Hours of Steaming?