I have to build a raised wood floor over a concrete floor in a garage. This garage is huge and the HO wants to use part of it as a breezeway(attached garage). I plan on using 2x6pt to build the frame and cover with 3/4″ OSB. Am I missing anything? Do I need to add anything else underneath the floor? Should I vent this at all or will the irregularities in the concrete be enough ventilation?
Discussion Forum
Discussion Forum
Up Next
Video Shorts
Featured Story
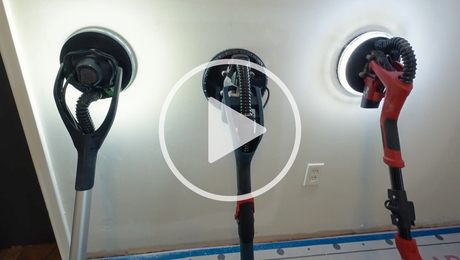
A pro painter evaluates a variety of drywall sanders and dust collection systems for quality of finish, user fatigue, and more.
Featured Video
SawStop's Portable Tablesaw is Bigger and Better Than BeforeHighlights
"I have learned so much thanks to the searchable articles on the FHB website. I can confidently say that I expect to be a life-long subscriber." - M.K.
Fine Homebuilding Magazine
- Home Group
- Antique Trader
- Arts & Crafts Homes
- Bank Note Reporter
- Cabin Life
- Cuisine at Home
- Fine Gardening
- Fine Woodworking
- Green Building Advisor
- Garden Gate
- Horticulture
- Keep Craft Alive
- Log Home Living
- Military Trader/Vehicles
- Numismatic News
- Numismaster
- Old Cars Weekly
- Old House Journal
- Period Homes
- Popular Woodworking
- Script
- ShopNotes
- Sports Collectors Digest
- Threads
- Timber Home Living
- Traditional Building
- Woodsmith
- World Coin News
- Writer's Digest
Replies
I would just be concerned about moisture (condensation) so you might want to think about a plan to ventilate the space beneath the new floor.
Make sure you use nails rated for the new PT when nailing the OSB sheathing on top otherwise the nails will rot and you'll have one squeaky floor.
Thanks, i'm aware of the nail requirements but do you have any ventilation reccomendations? Should I just drill some holes in the rim joist?
If this garage is adjacent to a basement and there is anyway you could get an opening from this space to the basement then ventilate the rim joist or however and get a flow of air through that space, especially in the summer. (what climate are you in)
Is your framing going to be in contact with the gaage floor or elevated? If elevated you could ventilate below with HVAC grills or foundation vents. But it just dawned on me that you should not ventilate into the garage space. Fumes from cars, stored gasoline and other products could find their way under this space. You would be best to ventilate to the outside air and have an opening if possible to the adjacent basement if there is one. The vents to the outside could be partially or completely closed in the winter. depending on your climate.
If you ventilate under that floor you will get condensation especially in the summer. The warm humid air will hit the cold concrete and condense. I would seal the concrete and the i would put down rigid insulation under the whole floor and tape all the joints. Then put your sleepers down and then the sub-floor. You could even put more rigid in between the sleepers if you wanted .
does it absolutely, positively have to be raised? if not, check out http://www.dricore.com the owner might prefer to preserve some ceiling height, too.
m
Its a twelve foot ceiling(to open trusses). He definitely wants the step. It was his idea.
The big question is whether the framing is raised or is it sleepers. If the framing is raised it is no different than any crawl space addition. As I said if the garage is attached and there is a full basement on the house an opening to the basement would help keep that area dry. Humidity is transient and any excessive condensation would evaporate and the humidity would be absorbed into the presumably lower humidity atmosphere of the basement. If high humidity is a problem in the basement a de-humidifier could be utilized. Some inspectors ask for venting on crawl spaces but is is not necessary when you can get the air from a basement into the crawl space.
Sleepers are never my favorite way to go because despite your best efforts you never know what is going on under there. If the floor is sloping I would suggest pouring a new leval slab over the existing and after the concrete is completely dry, COMPLETELY, installing an engineered floating wood product.
I am not saying that sleepers are a bad idea, there are certainly countless successful installations.
Were not talking about sleepers here. Let me try to explain better. The house is attached to the garage. There are three steps(heightwise) from the house to the garage floor. The HO wants to create a "Breezeway" to kind of seperate the two and while doing so eliminate one of the steps. In other words he wants the breezeway to be 7 inches off of the garage floor.
Hope this clears things up. I dont believe i'll need to vent to the basement(this raised floor will be in the unheated garage built on the cement).
Is the "Breezway going to be heated?
Des I dont think he plans on heating it. I'm almost positive hes not. I would plan on insulating the floor if he was.
Edited 12/12/2004 12:17 am ET by MSA1
We're putting a wood floor down over a concrete slab in a custom home and we're following the Hardwood Manufacturer's Association(hardwood.org) reccomendations to keep moisture problems at bay.
First seal the concrete good, they suggest an asphalt primer, we couldn't find anybody who carries this locally so we just used 2 coats of Drylok(from local home improvement store). I think any good concrete sealer would work.
Next, butter the bottom of your treated sleepers with hot or cold asphalt mastic before you put them down. Again, we are using an cold asphalt roofing cement from the local home improvement store. Shoot down with ramset or tapcons or whatever. Roofing cement acts as an adhesive once it "dries".
Next, in our case the floor will be in a heated space so we will put blueboard between the sleepers.
Next, put 4 or 6 mil poly over the top of all that, overlapping the joints.
Next, in our case we are using Advantech as subfloor.
Next, 15 lb felt under your hardwood floor.
Done.
Maybe sounds like overkill but we didn't make it up, this method comes from the Hardwood Manufacturer's Association and we had problems with wood floors over concrete before we started following their reccomendations.
I think that the original post is not putting the floor framing in contact with the floor but framing above it.
I do have a couple of reservations about the technique you described.
First, the asphalt cement as an adhesive is not going to last as an adhesive. In my experience I have never seen an asphalt product that ddid not dry up in a few years. Case in point, always paint drywall before having mirrors installed by an adhesive. The drywall sucks all the oils out of the adhesive and it dries and fails. I believe that the wood sleepers will do the same to the asphalt product.
Also while moisture coming through the concrete can be a potential problem I am also concerned about condensation. The slab by nature is typically cooler than the air temperature due to its contact with the soil, and any thing you coat it with is going to be at that same temperature. Warm air that can reach that space could condense.
Yes the intention as it was explained to me was to build a 2x6 frame right on the concrete floor. What if I rest the frame on 3/4 sleepers? That would maintain a gap that should allow moisture to escape. BTW the climate is Michigan thumb(Imlay City).
I'm very interested in your information. I am also in the process of converting my attached garage into a den area and building a new garage onto the side of the existing garage.
I am covering the existing garage concrete floor with 6 mil poly taping the seams. The joists are 12 ft. long 2x8's, 16" on centre tied into the rim boards and not touching the floor. I am installing R40 (10.325") pink insulation I purchased from Home Depot in Feb. at a very discounted price. On top of this I am placing another 6 mil poly vapour barrier. I believe the 2 poly barriers will prevent moisture from wicking from the concrete onto the bottom of the joist system and the topside barrier will prevent moisture from gravitating through the floor. The space between the concrete and the new floor will not be heated intentionally, but may become heated from the heat transfer from the existing basement through conduction. However, this heat conduction may be offset by the conduction of the heat into the existing concrete floor which is not insulated underneath.
Would installing the 6 mil poly not be as good as trying to seal the concrete floor ?
I've studied what I'm doing and it still seems the right way. A comment I've had is the 2 vapour barriers will trap the moisture. I feel the concrete floor is acting like a dirt floor over an unheated crawl space and the 6 mil poly will totally prevent moisture from this source.
I'm also not sure what to use for the subfloor. I don't know what Advantech is as mentioned by dogfish. We are planning on installing a wood floor as a finished floor and why 15# felt under the wood floor ?.
Any input is welcomed and appreciated.