I have a 480 sq ft workshop built right next to a 30′ x 40′ concrete slab. Some of you may remember a post asking about setting piers or digging out under the slab edges to build an addition to my shop….Anyway, with the economy and all, I have yet to do anything, but now it is apparent to me to be satisfied with a smaller addition than the whole 1200 sq ft one…..I have thought about it and would be happy with extending out from my existing shop a space 16′ x 24′ or 384 sq ft….That added to my 480 sq ft shop would give me 864 sq ft…..I can live with that, so now to my big question…..The slab is 20″ lower than the floor in my existing shop floor….My thinking is to attach a 2 x 8 floor framework to the long side of my shop that would extend out 16’….Now for the zinger…I think it would be fine to use a series of 4 x 4 pt post, notched into the 2 x 8’s like a deck and concrete preformed pier supports, set on top of the 3 1/2″ slab, maybe even glued to or mortered to the slab….If the weight is distributed out enough, seems like building a light weight shop on top of that would work…..Also, since I am a finish carpenter who works mostly out in the field trimming houses, the heaviest piece of equipment is a contractors saw….See attachment….Thanks, Alex
Discussion Forum
Discussion Forum
Up Next
Video Shorts
Featured Story
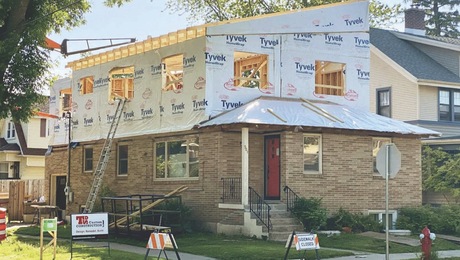
Get expert guidance on finding a fixer-upper that's worth the effort.
Featured Video
Video: Build a Fireplace, Brick by BrickHighlights
"I have learned so much thanks to the searchable articles on the FHB website. I can confidently say that I expect to be a life-long subscriber." - M.K.
Fine Homebuilding Magazine
- Home Group
- Antique Trader
- Arts & Crafts Homes
- Bank Note Reporter
- Cabin Life
- Cuisine at Home
- Fine Gardening
- Fine Woodworking
- Green Building Advisor
- Garden Gate
- Horticulture
- Keep Craft Alive
- Log Home Living
- Military Trader/Vehicles
- Numismatic News
- Numismaster
- Old Cars Weekly
- Old House Journal
- Period Homes
- Popular Woodworking
- Script
- ShopNotes
- Sports Collectors Digest
- Threads
- Timber Home Living
- Traditional Building
- Woodsmith
- World Coin News
- Writer's Digest
Replies
I'm thinking I would use 2x12 floor joists and skip the intermediate run of 4x4s
The reduces the 20" elevation to about 16". I'd lay two courses of block at the exterior wall to set on instead of 4x4 peglegs
Welcome to the
Taunton University of Knowledge FHB Campus at Breaktime.
where ...
Excellence is its own reward!
No. You have to go to footer grade. What is it there in Tenn? 24" No biggie.
It really wouldn't be that hard, depending of course what you're digging. Just under dig the outside edge every 8', that would be 4 holes, dump in your crete and block up from there, & there are your bearing points for your double rim joist. Simpson hang the rest. Labor is more than the materials. Hire a kid for a morning to dig the holes.
Do I think you could get away ok with your plan? I'm guessing maybe, but putting in all those pier posts is a lot more labor, plus you should not notch load bearing 4x4's. I know it's been done a lot in the past but it's not good building practice because they have a tendency to split. Is there re-bar in the slab? It makes a difference if you're doing it your proposed way.
Good luck
reading Jer's reply made me go back and review what you wrote...
I guess some things are not clear.
The slab is already there and no failing, heaving, or whatever, right?
I agree with him that 4x4s are too slender.
But I also pick up another inconsistency.
In the text, you say the slab is 20" down from your existing FLOOR level, but the drawing shows 20" from bottom of floor frame system. Which would be right?
Welcome to the
Taunton University of Knowledge FHB Campus at Breaktime.
where ...
Excellence is its own reward!
epoxy some anchor bolts for a sill plate
Yes the slab is 15 years old, no heaving, no cracking, almost perfect with just a couple inches of fall towards the back.....Yes there is wire mesh and it is the fiberlglass concrete.....The distance from shop floor to top of slab is about 20"....I really was wanting, for now, to just build out 16', which puts me on top of the slab and makes it hard to dig down through the concrete to footing depth which is is 24" here in East Tennessee.... My slab is sitting on firm, tamped down clay and with the 3" of gravel and 3 1/2" to 4" of concrete, it's a well done slab.....Oh, there are real keyway expansion joints every 10' or so......I hate to cover it up and would love to be able to afford building around and using the entire 1200 sq ft for a shop, but with both my kids now in college and student loans hard to get, well here I am trying to get by as cheap and having to settle for a little less.....thanks for your time on this and any other ideas are welcome.....Alex I guess you could tell in the drawing that my old shop, which is 24 years old, sits on piers with posts set in concrete...I checked it the other day with my laser level and it is still perfectly level....no settleing I just added some pictures to help out here, bushes are coming out and going to restain and finish battens when new part is added on......Alex
I normally don't open any attachments larger than 150-200KBs, so the first was a challenge. These are just impossible unless you or somebody else resizes them.If the existing slab is not moving, then you should be fine without going down to sink footings. It is the point load that could give you stress cracks by loading on the pier style supports. That is why I was thinking continuous CMU block to spread the load.So if it is 20" F/F, then 2x12 and a sill plate and 3/4" subfloor would use up 13.5" leaving 6.5"...
Think about laying a ground contact 6x6 PT as a curb/beam and expoxy bolt it down, then shim the sill to level.There may be another way of looking at this whole project too though. Talk to your accountant about planning. There may be a way of financing and paying this full sized shop you want that lowers your family income on paper so that you are eligible for greater college assistance.
Welcome to the Taunton University of Knowledge FHB Campus at Breaktime. where ... Excellence is its own reward!
Piffin,
Since when can you build an addition on top of a 3-1/2" without any footings? Am I missing something here?
I f that were the case, everyone could be building additions on top of their backyard 4" slabs.
All he needs to do is cut out the slab in three spots, end, 12' to the middle and 24' away and use a 3-1/2" x 9-1/2" or 5-/12"x 9-1/2" microlam for a girder depending on which way the roof runs and use 2x10's or I-joists for the joists.
Joe Carola
Edited 9/28/2008 6:34 pm ET by Framer
Technically you are right. And if he is going to do the pier style he is thinking of originally, that is what he needs to do.But the slab is a load spreading device, it is not heaving or moving, is re-inforced, there will be little load on it, and either of my suggestions spread what load he adds across a larger area.In the realm of good, better, best, what I am suggesting is on the lower end of good, certainly not ratched up to best or excellent, but this is an econo-shop, not the Taj-Mahal
Welcome to the Taunton University of Knowledge FHB Campus at Breaktime. where ... Excellence is its own reward!
Piffin,
So your saying that since the slab is bigger than the addition, he doesn't need footings? There's little load? How about the roof sitting on a 3-1/2" slab? Point loads where the girders are?
Since when can you build additions on slabs without footings? Doesn't matter what you call his shop, it's an addition, the same as any other addition and you can't frame additions on 3-1/2" slabs with no footings.
Additions don't need foundations, you can just use footings like you do a deck and use girders to support roof and floor loads. That's his case here. He just has to cut out three spots to put footings and then use girders on the 24' section and if the rafters run on the 16' section he still can use girders for that it the wall.
The outside footings are going to carry all the weight no mater what. How can just a 3-1/2" slab carry it? If I frame on a slab and there is a bearing wall in the center, they frame put a haunch footing under that wall to support the load. That slab is bigger than that load bearing wall and it needs a footing, the same as what he's talking about. His 24' wall lands in the middle of a slab like a basement slab. How can his slab support the load without some king of a footing?
Obviously the guy is not getting permits because building on 3-1/2" slabs would never pass inspection.
Tell me what I'm still missing here.
Joe Carola
Joe,i'm not seeing anything that says the original building is on footings. If it's not on footings, wouldn't want the addition to have footings He says the original building is 480 sq ft. around here we can build a garage or shop on a floating slab up to 22' x 22' iirc
Barry E-Remodeler
He says the original building is 480 sq ft. around here we can build a garage or shop on a floating slab up to 22' x 22' iirc
We can't around here. Garages have the same footings as a house or addition, besides this guys building an addition with floor joists not a garage no matter what he calls it. It has everything an addition has.
So you can build additions with floor joists on slabs with no footings?
Joe Carola
of course an attached garage can't be built on a floating slab. i'm talking freestanding garages or out buildings, which I'm assuming this is<So you can build additions with floor joists on slabs with no footings?>not to say i've done it, but i've seen it done, except they call them decks around here <g>Like piffin said it's not best choice and if the orginal building has footings i would at least cut some holes in the slab and do some pier footers,that being said, i've seen bigger building than that built with out frost footing in the Iowa countryside and some of them have been standing 100+ years .... it would serve his purpose for a time
Barry E-Remodeler
of course an attached garage can't be built on a floating slab. i'm talking freestanding garages or out buildings, which I'm assuming this is
Attached or detached garages with slabs have to be built with the same footings as a house or addition where I'm from. Again, where not talking about a garage here. This is an addition with floor joists, decking and a girder, not a garage.
Joe Carola
Seems your local jurisdiction is stricter than mine<Again, where not talking about a garage here. This is an addition with floor joists, decking and a girder, not a garage. >But it is an outbuilding, not a house. I'm wondering if the original is floating or footings
Barry E-Remodeler
But it is an outbuilding, not a house.
What does that mean? It's still an addition, getting framed same as any other addition.
Joe Carola
Maybe your BIs and codes require you to look at it that way, but most places have some lighter rules for some spaces that are not living space and not heavy commercial.
Welcome to the Taunton University of Knowledge FHB Campus at Breaktime. where ... Excellence is its own reward!
I'm in farm country so maybe our terms are different. like Piffin said the rules can be different here for spaces that are not used as living area
Barry E-Remodeler
I'm in farm country so maybe our terms are different.
Addition is a term used everywhere. This is what this guy is building no matter what he calls it. He's got floor joists, girder, decking, walls, roof...etc. It's an addition! It's also a shop and probably carrying a lot of weight.
Joe Carola
I just think it would easier to pour 3 or 4 footers and be done with it. That way you would avoid all the hassle of cutting & building more piers & trying to spread the load. Cut through where you're digging, dig, pour, float the crete of the footers even with the existing floor, leaving 1/2" bolt downs sticking up 3" lay down your foam barrier, lay in a 2x6 sill and bolt it to the footers...just like a regular foundation wall. Ride a built up 2x10 (maybe 2),on top of that sill & fasten it down. Run a rim, then set your 2x10 floor joists on top so there is a down load, (better than a shear). That should get you just about level with your existing floor. Done. Badda Bing! as they say in Jersey. Ride over everything.
A minimum of wood will be touching the masonry, (none if you lay in the foam), like it should be. You have a rat-slab in place now.
I really don't see how something else is going to be that much less cost wise.
Also if this is a shop, I assume you're gonna want to use it as a write-off. Taxman wants you on the up & up so what about insurance then? Don't you need some sort of inspectors stamp for that?Piffin's way would probably work and he's right about spreading the load. I just think this way would be around the same amount of work & materials.Pretty straight forward stuff, and it's not that big a deal.
"Point loads where the girders are?"The way I am suggesting, there are no point loads. The girder beam spreads the load out.You can build right on soil if the soil is able to handle the load. I worked on a house with brick wall 16" thick directly on soil only 12" down with no footing. 2-1/2 stories and no foundation problem.I have seen Lots of garages built on slabs with no footings, just 3-4" thick and no failure. I can think of one that is two stories tall and has one corner washed out under the slab and no failure for ten years now.I don't build that way and most places probably wouldn't permit it, but it works just fine much of the time. I don't hear him describing any of the situations that might make me think it would be a concern.I can gaurantee you that the slab spreads the load over a larger area of soil than the piers you would have him dig in. The bearing is less of a concern than is frost heave. But he reports no signs of that having happened. So the slab is good and stable.
Welcome to the Taunton University of Knowledge FHB Campus at Breaktime. where ... Excellence is its own reward!
The way I am suggesting, there are no point loads. The girder beam spreads the load out.
So, you're saying that you can lay a wall of block down in the middle of a 3-1/2" thick slab that's the ends of the block if the rafters are running the 16' way is alright and there's no load on the ends supporting a roof? Joe Carola
Yes, there is a load, Joe.But there is no point load. A point load is if that wall is on a beam or girder and the ends of that girder are on piers like he first said, the posts or piers are a point load.Spread the load out evenly all along and it is not a point load.
Welcome to the Taunton University of Knowledge FHB Campus at Breaktime. where ... Excellence is its own reward!
Alright Piffin, no point load. Your still saying that you can frame a entire addition with a block wall in the middle of a 3-1/2" slab without no footings? Are you just saying that because the slab is bigger?
What about the slab on a house that has a bearing wall in the middle, that has to have a haunch footing to support that wall and that wall can only be holding up a center wall plus a ceiling. This guys addition is holding up joists and a roof and he needs no footing?
What if he wasn't in the middle of a slab, would you still be saying the same thing?
Joe Carola
I might.Like I already said, I could take you on a tour of structures built on 4" slabs. Heck, my shop has 4' CMU walls topped with 6' wood framed walls on a 4" slab. I haven't seen the floor for a year, but I think there are still no cracks in it anywheres. Whole building is nice and straight and the doors work.I'm not criticising what you are saying. The codes are there for a reason. Do it absolutely rightly and there is far less chance any thing will ever go wrong.But when you understand why the rules exist you have a better idea when you can change them or modify them, instead of following the letter of the law rigidly.so his shop at sixteen feet wide will have eight feet bearing per lineal foot of this wall. Figure 100#/sf for live and dead loads and you have this wall loaded with only 800#/LF of girder. Make that girder beam be a 6x6 and it is loaded with only 1600#/sf or a little more than eleven pounds per square inch. Well compacted mineral soil can handle that kind of load! But assume the slab spreading it out a foot each way and that 800pounds is now spread over more area and loads the soil at less than three pounds per sq inch.Take your thumb and put three pounds of pressure on some well compacted and see if it breaks or compresses. I know that when I prep for a slab, I can walk over the soil and not make impressions. I just did a rough calc on foot size and my weight. comes up to about five pounds per sq inch, nearly double what this guy is planning to put on his slab.There is one way and one way only that this would be likely to be any problem. That is if he has water directed to be running in under the slab where it freezes, or maybe hits expansive clay. The upward thrust of freezing water or expanding clay will create an equal upthrust pressure everywhere if the amt of water getting in is equal everywhere, but the counterforce of load pressing down is focused along that wall.So if the rebar there is not sufficient to resist the unequal stresses created within the slab, it could crack a little.Or the whole slab might lift an inch and then settle back down again. That is why we call it a floating slab.In a home, that would be downright bad. Somebody would be patching cracks ion the SR and caulking and painting regularly - bad for property values.But a shop or a barn is a place where cosmetics are not critical. It's a palce where you learn to live and give.
Welcome to the Taunton University of Knowledge FHB Campus at Breaktime. where ... Excellence is its own reward!
Which way are your rafters running? If they're running the 16' way, you can use a microlam as a header with one side resting on the existing foundation and the outer side will be supported by the footings on each end.
Here's what I'm talking about.
Thanks for the help....There is no footing anywhere.... The existing shop sits on poles set in concrete....The slab is just a basketball court, well done, but still just a slab used for a basketball court.....Originally, I was going to rent a bobcat with auger, dig holes at perimeter and pour concrete for posts to set on, then beam where needed and put a tin roof system on that....I need to keep costs down now and that is why I was going to try to get by setting on top of the slab, thinking that by distributing the weight of the floor, walls and roof system on the slab, that would work....guess you are right in needing to cut out concrete, pouring footings and then setting posts on that....sorry bout the big picture files, I will down size to help out....I basically wanted to extend shop to match existing and have ability to add on later....Thanks again, Alex
Well, you just got the best to debate your question.
I want to question your question.
A shop contains many different tools, machines, storage, setup, etc. Many different jobs being done.
Can you re-layout your floorplan to put those tools that need the present floor level and put the more flexible ones at the current slab level? Maybe with only some form of transition in between? Ramp, lift, chainfall, whatever.
Mytrkut--
It would appear that your original shop is about the size of a small 2 car garage. Having it raised and supported by posts really set the bells to ringing--but I'm in Colorado--a mile high. I think it would be a shame not to have a concrete floor--but I guess needs vary. Unless there was some requirement to have a floor at the same level I would keep the existing slab, build the addition to the edge of the concrete and have stairs or a ramp connect the two. By not building to the edge around here there is constant trapping of water from rain or snow melt. Doubt you have the snow but rain??
By eliminating the floor framing and decking materials you could have more bucks for the longer walls. trusses and roof decking. Maybe a skylight or two. Just a thought. Tyr
I built my existing shop some 24 years ago, completely by myself, from digging the 28 holes, mixing bags of sacrete, setting poles, framing floor with 2 x 8's, plwd, building walls, setting main truss to support the clear story, stick framing rafters and installing the tin roof....Anyway, I couldn't afford to hire it out, so I did it by myself....Even though I am now 53, I am looking at doing this addition by myself, which is why I am seeking the best and easiest way to do so....EVERYONE here has been great about my question and I would bet money that if we were all in a room debating this issue, we would certainly be looking at each other when sharing our ideas.....Sorry, got a little political there....Anyway, even though this is going to a light weight building and I don't have heavy equipment to put in it, I am now looking to rent a concrete cutter and mixer and bottle of ibuprofen to get footing pads done first and then order my framing package....Thanks to all of you and if I have any more questions, I am glad to have you all to ask.....Alex