Wrecked Angle’s SIP house project
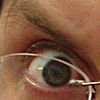
At the suggestion of a couple of Breaktimers I have decided to expose myself to potential ridicule and embarrassment by tracking the framing of my Structural Insulated Panel house here for all to see. This is an unconventional form of construction so, in the spirit of this forum, I hope that my experience will serve as intellectual fodder for those of you considering the use of SIP’s in your own projects.
I will post what I learn as I go and welcome your input and questions.
Disclaimer:
I am reasonably experienced in construction but it is no longer my day job.
This is the first time I am building with SIPs.
I am serving as general contractor and primary labor on evenings and weekends so this thread will go on for a while. In other words – don’t rely on the time it takes me to put together a SIP house for scheduling your own crew.
Please understand that my free time is going to be limited for a while and don’t be offended if you post a question or comment and I don’t respond for a few days. I’ll do my best to keep up.
I will be honest when (not if) I screw up in the interest of helping others learn from my mistakes. If you have a suggestion that will help I would appreciate it. If you just have a smart alec remark – well, I’ll probably appreciate that too but I would like to minimize the chit-chat in order to make this a more viable tool for those scanning it for info.
All that said, here is a picture of the house as of Saturday night. In order to make details somewhat legible I will be posting compressed JPEG’s at 600 x 800 DPI – let me know if too many of you are having trouble with files that size and I will make them a little smaller. Accounting for severe weather delays this is the equivalent of about 4 days worth of work for a crew of three – my father, my brother-in-law and myself. My lunch hour is over so I will cover the process of how it got to this point a little later.
Here we go – sit back, relax and take a SIP. This ought’a be fun!
Kevin Halliburton
“I believe that architecture is a pragmatic art. To become art it must be built on a foundation of necessity.” – I.M. Pei –
Replies
Ordering and Shipping:
My first mistake was not getting the panels ordered early enough. It took seven weeks for my panels to be ready to ship. Plan on a big lead time if you are using panels. Especially if you are having the door and window cutouts and other required fabrication done at the factory. They can knock them out pretty fast but only when they get the orders in front of yours processed.
Another concern when using panels is that you are not going to be able to run down to the local lumber yard and pick up shortages on your lunch break. I had planned to take delivery of my roof panels in a few weeks when the walls were done and ready for them. Unfortunately, six of my wall panels were mistakenly excluded from the initial delivery so I had the plant send another load with all the remaining panels in order to keep going. Hopefully the weather will not adversely affect the panels while they sit.
It is about 270 miles to the plant where my panels were fabricated. Shipping for both trucks set me back $1000. Don't forget that little detail in your budget...
Another important budget item: You will need to have a forklift with eight foot fork extensions available to unload the truck. Forklift rental in Abilene is about $240/day with a contractor discount. I paid a log home builder working on a friends house nearby $120 to drive his home made fork lift over to offload the first truck. It is a monstrous looking contraption but it worked pretty well. (see attached)
The panel manufacturer had promised to include a pair of loaner fork extensions on the first truck but they were missed, along with the panels that were overlooked, so we ended up having to run straps around the panel stacks and strap them to the lift in order to prevent them from toppling off the front. It worked but I wouldn't try it as a first resort. It was a real challenge on the two stacks that had window cutouts on the panels at the bottom of the stack. I bridged the windows with 2x6's at the tip of the forks but they snapped a few feet away from the truck on the first stack giving me a minor coronary. As far as I can tell, no panels were damaged.
As an alternative, the panels are light enough that they can be unloaded by hand with enough people. I proved that to myself when the forklift was unavailable for the second emergency shipment. It took four guys about an hour and a half to unload about 50 panels. The plant was kind enough to include the fork extensions on the second shipment of course. Ugh! I think I lost about 12 pounds that morning. Get the fork lift with extensions if at all possible.
Once the panels were on site, the next step was prepping to put them up... I'll cover that step in the next installment.
Kevin Halliburton
"I believe that architecture is a pragmatic art. To become art it must be built on a foundation of necessity." - I.M. Pei -
Kevin,
I'm glad to see your progress. Did you use the osb splines or make your own plywood splines?
as for delivery, I'm able to get some panels in a week. worst case is three weeks..
I pick up the panels at the factory myself and have my own forklift so that part is seldom more than the driving time plus about 10 to fifteen minutes to unstrap and unload..
My panel manufactor allows up to one year before any problems with the panels crop up and I can testify to that.. I know I pushed that envelope well in excess of a year.. Part of that is building a timber frame by myself (almost) and demolution of the old house as I went..
as for fork extensions, you can strap* or simply run scews into a scrap of wood and if you are carefull lift the panels that way.. (that's the only way I could get panels forty plus feet into the air.. )
Have you figured out how to get the glue they use out of clothing yet? (hint, feeeze em)
* if you strap remember to put a spline into the grove for the spline or the strap will crush the OSB in that location..
* if you strap remember to put a spline into the grove for the spline or the strap will crush the OSB in that location..
Good point! A detail missed by the driver of the first truck when my panel load tried to climb off the back of his truck. It looked like a spider had strapped them back on when he showed up. He even had some of the straps attached to the top skin of the bottom panel. (see attached) Several of my panels were damaged at the edges by his straps but so far I've been able to straighten them out enough to get the dimensional lumber and splines in the pockets without too much trouble.Kevin Halliburton
"I believe that architecture is a pragmatic art. To become art it must be built on a foundation of necessity." - I.M. Pei -
Hi Wrecked -
I just finished wiring my new "barn-garage-workshop" built of SIPs panels. You can view some early erection pictures here:
http://www.rcgroups.com/forums/showthread.php?s=&threadid=64681&perpage=15&highlight=the%20workshop&pagenumber=2
Just scroll down through the thread. I started it last September and spent one of our worst winters in it finishing up. It was worth every penny and impresses everyone who enters it, especially if they pound on the walls: STRONG!
The temperature inside was always warmer than outside but the difference varied according to weather - warmer when it was sunnier, etc. The next step is to add a balcony for storage at about 9' - 6" and finish moving in.
It took about 5 weeks to get the panels and 2 weeks to erect them, delayed because of lousy weather. There was one mistake made by the guys who drew up the panel drawings and that required some hustling and trimming - nothing serious. You'll enjoy the final result. I'll never build any other way after this experience. The increase in lumber costs due to the GWB tax on Canadian lumber makes the SIPS a winner on cost too.
BTW, my local lumber yard beat out HomeDepot for price, availability and certainly quality hands down (I'm and inveterate and experienced shopper).
ronw
Ron,
That is a good looking building. I hope you will stick around and chip in with your own answer to any questions posted. I sure would like to have that reticulating fork lift you used. Those machines are the cat's meow when it comes to putting up a SIP structure in record time.Kevin Halliburton
"I believe that architecture is a pragmatic art. To become art it must be built on a foundation of necessity." - I.M. Pei -
Kevin,
Those fork lifts are actually correctly called rough terrain telescopic fork lifts.. the genaric term seems to be "Lulls" although they only have a tiny market share now compared to a decade ago..
Since I sell and rent them for a living I'm able to keep a demo here at home.. I couldn't build this place without mine.. or with a lessor brand..
Hi Wrecked -
I'm not getting your pictures either.
I'd think long and hard about using a grinder or any such thing to cut foam from the edges of panels because it makes a mess that lasts and lasts and lasts . . . I'll be picking up foam forever. If I lived on the desert and had very high daily winds I might not mind but next time I'll make a hot wire. One can be made with a piece of 1/16" stainless steel welding rod or even a coat hanger and a two by four and some nails. Just bend the wire in the shape of the cut to be made and move it slowly. It can be heated with a deep cycle 12 volt battery. It will save hours of work - HOURS!
Do not be led astray by the seeming "weatherability" of the OSB. Its deterioration accelerates and some of what happens does not show up for days or even months. It should be protected as soon as possible - waste no time.
On Long Island nails are not used to attach panels for inseting 2 x's. They've been found to loosen over time and so galvanized deck screws are used at splines and at edge members. Cement coated staples hold very well but are often hard to find.
We used tension straps with a ratchet tightener to pull the panels together and had no problems with "growth", but then again, we only had a few joints per wall run.
Frankly, I'd build in conventional stick built if I had to use panels as small as yours. Because of the Bush tax on Canadian lumber, panels should be less expensive than stick built these days, but only if one uses their labor saving features, such as speed of erection.
My panels came from Insulspan/Panelpros. The OSB has the AAP stamp and the underwriter's stamp. See post #10 for access to pictures of my building.
ronw
Edited 6/13/2003 10:07:47 PM ET by ronw
Good info ronw. I've been using 2500 pound ratcheting tie down straps to pull panels together but I still picked up a little growth. One of the problems I had was that a couple of panels that should have been 8'-0" wide were actually about 1/4" wider. They got wet but I would be surprised if they grew that much. I suspect the 8'-0" sheets of OSB the plant used were not dead on. Some of my foam has been relieved too deep as well so I'm not getting a really good seal with the structural adhesive. I'm thinking of adding a shot of expanding foam on those panels to bridge the gap but I think I will call Chapman Building Systems for their advice first.
Chapman is only able to order OSB in 8'-0" widths but they can be as long as you want them so as long as your walls are no taller than 8'-0" you could theoretically make an entire wall out of a single panel. Since my downstairs walls are 9'-0" tall I'm limited to 8'-0" wide wall sections but it really hasn't been that big of a deal to put the panels together. My upstairs walls are only 7'-0" tall between gables so there are a lot fewer panels on the second floor eve walls.
The majority of my roof panels are nearly 16'-0" long but in order to achieve a ridge to wall clear span I had to make them 4'-0" wide. This allowed me to add double 2x6's at 4'-0" O.C. and eliminate the need for trusses altogether. The clear span vaulted ceilings upstairs should look pretty nice when it's all together. I'm certainly looking forward to seeing the house that far along. I'll see if I can attach my panel drawings in a future e-mail when I have time to log back on from the office.
As for the foam routing, we do get enough wind here to keep the slab pretty clean but I would still prefer a little cleaner method. I may try putting together a resistance foam cutter of some type. Thanks for the tips.Kevin Halliburton
"I believe that architecture is a pragmatic art. To become art it must be built on a foundation of necessity." - I.M. Pei -
Please WA I haveta have the picture that's missing in #48. Unfuddle me.
Here it is as an attachment but if you want to see any of the images that are displaying as squares on your 'puter just right click over the square, select properties from the drop down menu, highlight the web address from the information displayed, right click again and copy it. Then just click in the address box of your browser, right click again and select paste to go directly to the site where I'm stashing my photos and illustrations.
I'm wondering what is going on with my pics. I see them fine on both my home and office systems. Do you have your preferences set for basic or advanced mode? I don't think it would inhibit photo displays as well but do you have the option to hide signatures under your preferences selected? For the moment I will go back to attaching any photos I include to the end of my messages.Kevin Halliburton
"I believe that architecture is a pragmatic art. To become art it must be built on a foundation of necessity." - I.M. Pei -
I see the 3 pic in post 45, but not the others...fyi
>My Energy Wise analysis also included a guarantee that my average utility bill for any given year would not exceed $84.00/month or Energy Wise will pay the difference. The guarantee is based on the current utility rate of $0.086 per KWH (summer) and $0.0560 per KWH (winter) for electricity in my area. That can be compared to the average cost of heating and cooling a conventional stick built home at $258.00 per month. That is an average savings of $174 per month!
I'm a little suspicious. Not that sips have energy savings, but the magnitude of savings and the percentage attributed to sips. And I'm really surprised by the guarantee! I'm not doubting it, but still amazed.
Here's my thinking. There's a large part of the electric bill that's competely unrelated to the structural composition of the house. Your frig is your frig. Bathroom lights. Porch light. TV. Water heater. Washer. Range. Whatever else is electric. You're going to have a bill of some base size even if you never run the hvac at all. Since a >67% overall reduction is being projected, that means that he's projecting a much greater than 67% reduction from the cooling/heating portion of the bill alone. You dropped to 3.5 ton from 5 ton. A 3.5 ton draws about 70% of the energy of a 5. Are you going to be running it the same amount or less? If less, how much less, and will you be running it enough to get sufficient dehumidification? If the non-hvac portion of utilities is $50 (and that seems low for 8.6 cents all-electric and 2400 sf, be/c a water heater could do that all by itself), that means an hvac component going from 238 to 34 a month. I don't get the numbers.
I'm really not trying to knock it, and have no problem accepting that sips have better numbers than framed. But even when I'm looking at a building with 3-4" of continuous polyurethane plus thermal mass, and we would be sizing the hvac at 1 ton/sf on average--or a 2.5 ton for your size house--we'd only project savings of 50% or so on the hvac portion, and not >67% across the board. I'm missing something here, and look forward to learning.
I understand your suspicion Cloud - I had a lot of my own questions about this one. Here are some of the answers I was given:
I asked Richard, "so what if I decide to leave my refrigerator open for the entire month?" He responded, "that is why I put a 40% mark-up on my estimation. You should really expect to spend an average of less than $50/month." The average is calculated over an entire twelve month period so he has a lot of room to compensate for error with a 40% monthly increase in his projected expense. The guarantee is in writing and it is viable.
As to the efficiency of the system - The longer an A/C unit runs the more efficiently it performs. The greatest amount of energy is consumed on start-up so on a system that short cycles all day because it is over-sized it is always running in its least efficient mode. A comparable analogy would be driving a car in stop and go traffic versus on the highway. It will always perform most efficiently on longer trips.
The disparity is even greater when you drive a 2 ton flat bed to haul a box of crackers. The given load just doesn't warrant the monster system. The bigger the HVAC system, the more energy is required to start it up and get it moving. Sure, if the 2 ton truck runs all day under a massive load it will definitely operate more efficiently than a 1/2 ton truck that is way over loaded but when the load requirement isn't there it will always be more efficient to operate with the smallest unit that will handle the given load.
Further more, while you could use a five ton unit on my house and effectively "cool" the air it would never run long enough to fully "condition" the air. That is one of the biggest reasons why so many "tight" homes using conventional rule-of-thumb sized systems have a problem with mold. The systems only have to run for a minute or two in order to cool the air to the desired temperature so they never run long enough to adequately remove the accumulated condensation. When it comes to HVAC, bigger is rarely better.
The biggest advantage that SIPs have over conventional construction is that, with the exception of doors and windows, they are a seamless shell. Air leakage is the number one culprit when it comes to compromising the energy efficiency of a home. There is simply no way to construct a typical stick built home as tightly as a SIP built home. On SIPs even the roof is fully sealed to the walls. Your concrete domes are probably comparable on minimizing air leakage.
In all fairness the comparison of numbers I presented represents a "typical" stick built home where very little attention is paid to sealing up every stud bay with calking, sealing around electrical outlets and can lights, sealing between roof and wall, etc. compared to a typical SIP built home where each of these items is thoroughly addressed. There are a lot of things one could do to make a stick built home far more energy efficient than the norm but it would be nearly impossible to seal one up as tightly as a SIP structure.
If it were not for doors and windows you could theoretically heat a SIP structure with a candle and cool it with an ice cube. (well, maybe a few candles and a bag of ice cubes) They really are like an insulated cooler. The only way to make an insulated cooler enjoyable to live in however, is to compromise some of its thermal efficiency in order to bring in fresh air, sunshine and access. If you look at a bar graph of my loads there is a huge spike over doors and windows. With the exception of human bodies, and heat generating appliances there is virtually no load present elsewhere in the house.
Listen, the bottom line is that Richard has done the load requirement on several thousand homes and, according to him, has only had to pay out on his guarantee once, to the tune of about $35, when the system he specified turned out to be over rated by the manufacturer. I did a lot of detective work and contacted several people he has done energy analysis work for before I hired him. To a man, every one of them said their actual experience was better than his projected expense. Every one of them also said their HVAC contractors were still scratching their heads and trying to figure out how their woefully inadequate HVAC systems seem to be performing so far above the norm. The HVAC designer here in my own office still thinks I'm a gullible idiot. We'll see...
I would bet that someone who has been in the business as long as Richard Rue has, has a dissatisfied client out there somewhere but I couldn't find them. He knows what he is doing and I trust him. His guarantee just makes it a little easier, that's all.
Hope I satisfied some of your questions but if not, give Richard a call (817) 477-1387 or (817) 473-2349. I know he would welcome the opportunity to discuss your questions with you. You might even discover a new consultant that will be a solid boost to your own business. Your concrete domes are right up his alley.
It's been several months since I contracted his services so I don't know if he'll remember me but tell him I suggested you give him a call if you do get in touch with him. I've made a few changes to my drawings that I think will make them even more efficient and I want him to take another look at them. Maybe he'll give me a break if you tell him what a great guy I am for telling you about him. :-)>Kevin Halliburton
"I believe that architecture is a pragmatic art. To become art it must be built on a foundation of necessity." - I.M. Pei -
I have no problem with the tonnage specified or the load calculation. Completely agree on sizing so that the unit can run properly. Grasp the advantages of limiting air infiltration, and the benefits in reducing size to match the real load--every day I deal with explaining that we really, really are averaging 1 ton per thousand sf in complete comfort. It was the monthly savings that raised my eyebrow--given that the only difference appears to be dropping from a 5 ton to a 3.5 ton unit--the rest of the usage being equal--I'm having a hard time seeing how the approx 30% reduction in power usage on the heat pump translates into $174 monthly savings. For example, http://www.geoexchange.org/residential/res_case_hillside.htm is a case study of a SIP development in TX. Houses 1000 to 1500 sf, using a 2 ton GSHP (are you ground source or air source?). They're experiencing $35/month avg hvac costs, based on sub-metering, compared to $90-150 for conventional of the same size. They estimate further that the ground source heat pump is 40% lower operating cost than air-sourced. Extrapolating, that comes to over $90/month equivalent for just hvac with an air-sourced heat pump in a 2400 sf sip house, but since they don't mention kWh costs, I can't do the math for a comparison with your projected costs. It'd be interesting to see the hvac cost separated from the other electric usage, or to get a gauge on what expected non-hvac kW usage is--I've searched the net and not found a working number.
In principle I completely agree with you that there are ways to build that definitively reduce the hvac load, drop the tonnage requirement, and provide a monthly reduction in utility costs. Since I'm average 33% less tonnage than even the numbers here, I just may have to be less conservative in discussing operating costs of different structures. :) But I worry that this is sometimes over-sold, like the client who had concluded that she'd need absolutely no hvac because of how "magically" efficient the insulated thin-shells were (not far from your "heat with candles" reference--some people will miss your intentioned hyperbole). Her actual 2 tons for 2000 sf requirement is still good, but a far cry from the 0 she had somehow concluded.
Ok, I hear where you're coming from... sorry for the earlier sermon.
It was the monthly savings that raised my eyebrow--given that the only difference appears to be dropping from a 5 ton to a 3.5 ton unit--the rest of the usage being equal--I'm having a hard time seeing how the approx 30% reduction in power usage on the heat pump translates into $174 monthly savings.
The big difference is not just that I am dropping my HVAC usage from 5 tons to 3.5 tons but that the house it is being installed in is far, far, far more energy efficient than the conventional stick built house it is being compared to.
It's not a comparison of the difference in installing five tons in a SIP house versus installing 3.5 tons in a SIP house, it is a comparison of installing a correctly sized HVAC system in an energy efficient house versus what it costs to heat and cool the average stick built house of comparable size in my area.
The "average stick built house in my area is not going to win any energy star awards if you know what I mean. I've lived in and visited several of them and there is no need to open a window to feel a nice fresh breeze. The $258.00/month estimate to heat and cool one of those houses at 2400 S.F. is not unreasonable.Kevin Halliburton
"I believe that architecture is a pragmatic art. To become art it must be built on a foundation of necessity." - I.M. Pei -
>It's not a comparison of the difference in installing five tons in a SIP house versus installing 3.5 tons in a SIP house
But an X ton in a SIP house draws the same current as an X ton in a non-SIP house, no?
Then it gets into run time. Do you expect to run the 3.5 in your house less than the 5 in the conventional house? [And truth be told, I'd be more comfortable discussing this relative to some anonymous house, rather than yours--the topic interests me immensely in the abstract, and I don't want to focus on any one house.] It's mathematics to me. For a power bill to be less, you need to use less kWh. For that to happen, you need to run either smaller stuff, or run it less often, or both. Just having a smaller (by 30% or so) compressor and air handler, while definitely a good thing, doesn't account for an avg reduction in the utility bill of 68%. You'd have to use it a lot less, too--to the point of never turning it on, it would seem--to get that reduction. To achieve a 174 average monthly savings at an average monthly cost of 7.1 cents per kWh (I'm assuming that your 5.6 and 8.6 are half year each), you'd need to use 2450 kWh less each month (2023 if 8.6 cents year round) commpared to the conventionally-built house. My 4 ton GSHP, for example, will use only 2160 kWh if run 24/7, so by turning it off completely for the year, I couldn't reduce kWh enough to achieve those savings. Don't know what a 5 ton and your 3.5 draw, so don't know if the 2000+ kWh/month are there or not. Fun with nuumbers...
OK everyone, Mr. calculator has busted me! I'm wiping the egg off my face as I type.
Man Cloud, you're a wiry one with that calculator of yours. I really appreciate all the thought you are putting into this. As I analyzed my report a bit more closely I realized that I was giving you the guaranteed numbers off of the sample guarantee that Richard Rue included in my report. The sample guarantee is a bit of name dropping on Richard's part. It's a copy of his contract with Barry Switzer, former head coach of the Dallas Cowboys, who is one of his clients. I don't know if he realizes this or not but that may not carry a lot of weight here in Texas.
My projected energy consumption is actually for an average utility bill of $97 / Month, not $84...
My energy analysis is several pages long so I don't really have time to scan and attach it right now but if you're interested I would be happy to shoot you a copy of it in the mail if you want to contact me on the side and hook me up with your address.
The bottom line on Kwh consumption is as follows:
Energy costs were calculated at an average of $0.070 per Kwh.
My SIP house with an air heat pump is projected to consume an estimated 13,318 Heating Kwh/yr and an estimated 3,274 Cooling Kwh/yr for a total of 16,592 Kwh/yr.
A home built to conventional specifications with an air heat pump is projected to consume an estimated 37,582 Heating Kwh/yr and an estimated 6,682 Cooling Kwh/yr for a total of 44,264 Kwh/yr.
That is a difference of 2,306 Kwh/month or $161.42/month on average. Obviously I'm going to have to be using my system far more efficiently and a whole lot less to achieve that kind of savings. That is still a hard number to swallow so I see where you are coming from with your skepticism. Coming from you, a guy who regularly deals with another form of energy efficient structure, I give your skeptical annalysis a lot more weight.
At any rate, to compensate for the increase in mortgage payment to offset the cost of building with SIPs I would need to be saving between $10 and $15 per month on my energy bill. That is very, very easily doable. Even if the numbers are severely inflated I've got a lot of room for error before I start loosing money on the proposition.
To me, that is the biggest advantage of SIPs over the other forms of energy efficient building such as concrete filled ICF's. Those forms of construction have many advantages over conventional construction as well but they are a lot more expensive and far more difficult to build.
For sheer bang for the energy and building buck, coupled with the ease of constructability, SIPs save homeowners more money than anything else I know of.
Kevin Halliburton
"I believe that architecture is a pragmatic art. To become art it must be built on a foundation of necessity." - I.M. Pei -
Edited 6/15/2003 12:21:06 AM ET by wrecked angle
I was trying to understand the information presented; not offend, challenge, or compare. I'm sorry for addressing it...
Seriously Cloud, I was not offended in any way. I genuinely appreciate the time and effort you put into checking out my numbers. The fact is, you were just flat out right and I was just flat out careless and wrong. Don't apologize for bringing it up - I'm really glad you did.
I hope I didn't come across as being upset at all in my post. (picking up a slight sense that you might have read it that way) Everything I wrote, especially in bold, was intended to be self deprecating and even just a little bit humorous.
You rock man! I'm glad you helped me correct a serious error. What good is a thread intended to be full of useful information if the info isn't correct? Thanks - and I mean that!
Kevin Halliburton
"I believe that architecture is a pragmatic art. To become art it must be built on a foundation of necessity." - I.M. Pei -
Peace, bro. Carry on.
You guys both are educating alot of us that are just reading and following. Please, keep it up. I can beat both of your heating and cooling bills though, just move to the tropics and leave the windows open. Initial startup is pretty costly, but the bills have been pretty low!! Are we sure that termites won't eat the strand board? If no bugs, we need a SIP plant in Hawaii. To heck with the energy bills, it's the repair and chemical bills that are a problem here. Keep up the good reading.
Dan
Hey, Kevin, glad to help.
We are 2/3 of the way through putting the room on our new house. 10.5 in SIPS, with 1/8 T&G pine applied to the ceiling at the factory.
The panels are great, delivery on time, and placement mostly accident free. We did have to have a big crane, as the panels were 800+ pounds and the opposite side of the house almost 80 feet from where the panels were stacked.
We had a considerable difficulty putting the panels together, as a 22ft long groove in the T&G didn't go together easily. We finally ended up cutting the top finger of the groove off, using large ratched straps, and banging the hell out of them with a 16#sledge.
The panels held up ok as we had 2/10 lumber splines instead of OSB, etc. The factory glued them on one edge of the panel, and the other panel was supposed to "slip" into place.??????
We started off by having welding shop make lifting plates out of 12x12 steel with 20 screw holes. It worked fine when the panels were cold, but as the day progressed and the panels warmed up the screws started pulling out. That was pretty exciting, but fortunately in happened quickly, so the panels were only a couple feet in the air. After that, we went to large eye bolts, with lumber top and bottom on the panel, and lived with the holes in the ceiling.
A friend who was helping us told us of his teenager shooting a hole in his roof with a 410 shot gun, and placing wine corks in the holes for an invisible repair. We shall see.
My first time trying to attach files, here's hoping.
Regards
Stef
Well, my attempt at attaching files didn't work. I'll try another tack.
ok, Igive up
any help is appreciated
stef
To attach a picture, first follow the forum instyructions...don't try to get fancy like the John Deere tractor guy advised :) He's an expert on trusses and bird houses, that's for sure!
Click on Attach Files at the bottom of the page, click on Browse, find the file, click on it, then click on Upload and get a cup of coffee...usually takes 1-2 minutes. Finally when you think you've done something wrong, the screen will flicker and it will list the files you have attached...but you have to go through the process for each file separately, even though you can attach several to a thread. Click on Ok or Done or whatever, and it will bring you back to a familiar place. Go find Irfanview, a free downloadable program the shrinks file sizes with affecting (too much) the quality. Irfan will make the pictures less than 100k and much easier to load.
Do it right, or do it twice.
Edited 6/16/2003 12:48:02 PM ET by ELCID72
We finally ended up cutting the top finger of the groove off, using large ratched straps, and banging the hell out of them with a 16#sledge.
Hmmm, interesting technique for cutting the top finger of the groove off. Most folks would have used a saw or a router. :-)>
the other panel was supposed to "slip" into place.??????
Oh man, cracking me up there! Here I thought it was just me that was getting all red in the face by the time I got my panels "slipped" together. They do take a bit of persuasion don't they?
It's really not all that difficult on my smaller panels - three pound sledge with ratchet straps has been sufficient so far but just barely. I did construct a special beater plate from a scrap piece of 2x4 and a short piece of my treated bottom plate. The 2x4 slips into the groove on my panel while the treated bottom plate portion bears fully on the edges of the OSB. I haven't smashed up any of my OSB yet. I am planning to buy a little bigger sledge. I've got a few larger panels in my future that may need it.
Another useful tool that I discovered in the book I recommended earlier is called a "wall dropper." It is made by gluing, nailing and strapping a short piece of 2x4 to the end of a 6'-0" or 8'-0" 2x4. Once the panel is sitting over the bottom plate the wall dropper can be used to pop down on the top of the panel to persuade it to drop into place. I tried just nailing the short piece on for my first attempt. Smack! Look at her fly! Entertaining but hardly effective.
I can't recommend that book enough Building With SIPs - Chock full of useful info. It is the first resource I would recommend to anyone interested in SIPs. For what it's worth it has a little more conservative HVAC numbers in it than most SIP designers use too.
Based on his convincing arguments, and a little honest soul searching, I'm thinking Cloud is probably right about the stick built numbers in my report being a little exaggerated but the info in the book validates the SIP performance numbers pretty well. I know of several of Richard Rue's clients who are very happy with less than a ton of air per 1000 S.F. in their SIP homes. My loads are a little more demanding because I punched so many big ole' holes in that wonderful insulated barrier to take advantage of the beauty of our site. What can I say? Nobody likes living in a cave... I'm with John Denver - sunshine on my shoulder makes me happy...
Kevin Halliburton
"I believe that architecture is a pragmatic art. To become art it must be built on a foundation of necessity." - I.M. Pei -
Edited 7/13/2003 3:01:25 PM ET by Wrecked Angle
Hi Wrecked -
I just thought of a couple of items about dealing with the panels.
Peter Germano, who erected my shell used two types of attachments for lifting them. One was a hook with an eye, the hook being inserted into a hole drilled or bashed into the OSB and then rope and strap attached to the eye and then the Lull. The other was a through eye bolt that used a nut and steel plate on each side and was tightened up before attaching the rope and strap. In both cases the holes were filled later with polyurethane foam squirted in.
At the juncture of panels that used splines we had v-grooves formed that were to receive poly foam to complete the seal at the joint. On the earlier panelled buildings I saw, foam was squirted into the grooves and then the panels were assembled. Peter found, after having disassembled a panel or two that the foam in the joint and groove had collapsed when the panels were pulled together.
His current proceedure is to drill holes through the joints at the assembled panels at 16" on center in as far as the v-grooves. Then poly foam is squirted into the holes until it appears at the next adjacent hole. These holes are not filled with anything more than the foam i.e., no plugs.
A better choice for a plate is Trex which outperforms pressure treated by years and is not toxic. Most of the pressure treated decks built around here five or more years ago have rotted out and are gone. The pressure treatment is usually used on third growth Southern Yellow Pine which falls apart due to the water-wet-freeze cycle and after a season or so of rain loses its toxicity so that the bugs and organisms move in and it goes faster than untreated Cedar or Doug Fir.
ronw
Saw a reference in the message from ronw and a similar reference in an earlier message, possibly from you, about bashing a hole in the osb with a hammer for a lifting point. Please tell me that's a figure of speech. I would expect that the hammer blow would splinter the osb and damage the panel.
Do it right, or do it twice.
Nope, you read it right. The foam serves as a backer preventing excess splintering and damage when you smack it.
It looks fun. I might have to do it on one of my panels just to see what it feels like.Kevin Halliburton
"I believe that architecture is a pragmatic art. To become art it must be built on a foundation of necessity." - I.M. Pei -
Hi Sid -
The hammer blow technique, rough as it seems, is how its done. When the OSB is backed by the foam the hole is as clean and precise as if it were drilled. Occasionally it might be a bit messy if more than one blow is required, but an experienced man can do a very nice job. Try it on a scrap yourself.
Wrecked -
I'd seen worse with panels being "adjusted" with sledges against 2 x 6s to apply a little persuasion on other jobs.
Trex is made in standard lumber sizes as well as the 1 1/8" decking material; it usually has to be special ordered at a dealer but they're quite prompt with delivery. However, like you I learned too late and ended up using Doug Fir.
So far I haven't noticed any reference to the panel screws used to assemble corners, roof to wall and roof ridge joints. Those things are amazing. For instance, an 8 1/2" roof panel might be attached to a glulam purlin with 12" screws that are hammer driven through most of the panel and then driven into the structural member with a hefty screw gun.
I have timber framing to do on my building for an attached porch and plan to use those screws to connect things. I'll pre-drill the member being attached and then drive the final 3" into the supporting member using the threaded end of the screw.
ronw
Those panel screws are the main reason I bought my Panasonic Multi-Tool with the impact mode. I have really been wanting to get back to this thread with a continuation but I have been paying dearly for the week I took off work while my father and Brother-In Law were here.
Yes it is almost 2:30am here in Texas and I am sitting at my office desk. This is about the time I left the office yesterday and Saturday too. I haven't even seen our house site in a week, much less done any work on it. I am really looking forward to getting back to a nice relaxing day or two of manual labor.
More updates will be coming - appreciate everyone's patience. In the mean time ronw, GCJohn, frenchy or others with experience building with SIPs, feel free to carry on where I left off if you have the time. All of your information has been great!
In addition to corner make-up it's probably about time for a discussion on how to get wires pulled through the panels and what to do if you have to run a vent pipe or load bearing column inside a panel. We had to deal with an embedded steel column on the last panel my BIL and I set. I will post a few pics and the method I'm using as soon as I can.
If no one picks up for me I'll be back in a few... Thanks again for all the interest and valuable info.Kevin Halliburton
"I believe that architecture is a pragmatic art. To become art it must be built on a foundation of necessity." - I.M. Pei -
Thanks again ronw. That is exactly the type of info and experience I was hoping people would contribute here. Wish I'd had that trex idea about three weeks ago. Little late now. One advantage of using the 1 1/8" material is that you can use a standard 8'-0" panel on top of it to equal the height of a standard stud wall with double top plates.
Every pro that I've talked to uses lifting plates punched through the panel exactly like you described. There are several pictures of them in the book I keep recommending and they seem to work great. One of the main rules in panel errection is Don't Pick Up A Panel By Its Top Skin! It can cause delaminating of the panel. The best way to lift them is to get a grip on them with a through bolt that tightens a couple of steel plates against both sides of the panel to distribute the load. Then of course there is always the old strain your back method with a large crew but most builders would have a hard time making a living with that one.
I'm curious, did you know it was coming when your builder grabbed his hammer and punched a hole in that first panel? I'm sure it could make a home owner think about taking a swing at his builder when he sees him smack a hole in his high dollar panel for the first time. Especially if it looks like the builder did it just cause he felt like it. A warning is probably in order. Kevin Halliburton
"I believe that architecture is a pragmatic art. To become art it must be built on a foundation of necessity." - I.M. Pei -
No offense to anyone...just attach the pics like most folks do, and let us open them if we want to. Boss' procedure seemed a little involved for you, and it doesn't seem to be working reliably (kinda like that John Deere tractor in his garage). I use advanced view. FWIW sometimes I see pro-deks logo, and sometimes not. His response to a countertop question dated today only has a small x. Must be bad karma ghias in the atmosphere (but I likes the karma ghia...cute little car).
Do it right, or do it twice.
Edited 6/14/2003 1:41:15 PM ET by ELCID72
No problem. From here on out, even if I do include a picture directly in a post, I will also include it as an attachment. I see the thanks I'm getting for listening to a farmer/truss designer and a guy who admitedly has his head hidden in the clouds.Kevin Halliburton
"I believe that architecture is a pragmatic art. To become art it must be built on a foundation of necessity." - I.M. Pei -
Well, I discovered the problem on my photos not displaying. I checked my image hosting site and discovered the following message:
This account is locked for the remained of the day for exceeding the daily bandwidth limit of 5.00MB
Glad to know a few of you are following this thread... guess I'd better figure something else out.
Might play around with Boss's technique some more but... I'm thinking he may be pulling my leg for posing him with a John Deere sign in his three generation pic thread.
Has anyone else been able to make Boss's technique work?Kevin Halliburton
"I believe that architecture is a pragmatic art. To become art it must be built on a foundation of necessity." - I.M. Pei -
I can't understand what I'm typing here but maybe you might.
You reply to me about the pic in #48.
I print the post w/ your help note and discover that you have your name and a tag line in the post. [printed because I want to make no mistakes with your instructions]
Go up to #48 and the picture is there. Huh? Wasn't there before.
#45 - the pics that were there from the start are still there.
Go up to #41, [that one has the red X]. Try out your instructions.... This page can not displayed rigamaroe. Try again... Same thing... Refresh... Do it again... This page............Wwwwwwhot?
Attached photos are fine. Print 2 ramdom post of yours. Tag line visable on paper but not screen. Find a Boss Hogg post, print, tag on paper but not on screen.
If I miss out on posts and pictures from this thread I'm gonna be PO'd.
Kevin you have and excellent thread going. Don't know what is going on. What the promblem is or how to fix it so just consider this a FYI posting.
My picture hosting site has me locked down for the day because I generated too much traffic. That is probably why everyone has been having trouble with my posted pics. Wish I could go back and edit all of my posts to include the pictures as attachments.
Anyway, the signature problem is probably because you have "Hide Signatures" selected under your person prefs in your user profile. Just click on your name to bring up your profile, select personal prefs at the top of the dialog box and scroll down until you see the hide signatures box. If it doesn't have a check mark by it, I'm stumped.Kevin Halliburton
"I believe that architecture is a pragmatic art. To become art it must be built on a foundation of necessity." - I.M. Pei -
How about that... Instruction that I understand and can use.
Thanks.
Drive on.
Dear Wrecked
A much better foam cutter can be made by mooching a piece of orthodontic wire from your kid's orthodontist. Nichrome is the material, and is the same stuff in a toaster element. It heats with little electricity, and being quite small diameter (compared to a coat hanger anyway) cuts through the foam quite easily, cleanly, and with little effort.
Stef
Stef,
Cool! My wife was the Dental Missions Director for The Medical Care Mission before she decided to become a full time Mom so I'm betting she can hook me up with a contact or two where I can snitch a little Nichrome. Thanks for the tip!Kevin Halliburton
"I believe that architecture is a pragmatic art. To become art it must be built on a foundation of necessity." - I.M. Pei -
AFM sells a heat element that is designed to do the job. works slick evan at 20 below.. Costs about $50.00 if memory serves me.. I know every single panel I had I used it..
Who is AFM? I'm interested! You are pretty much done with the SIP portion of your home now aren't you? Interested in unloading your foam burner rather than decorating a shelf with it?Kevin Halliburton
"I believe that architecture is a pragmatic art. To become art it must be built on a foundation of necessity." - I.M. Pei -
AFM is the SIP manufactorer I used.. they use a trade name of Poly foam.
No! I'm only a third of the way done with the SIPs. When finished the whole house will be SIP'ed (and timber framed)
Call Nancy at Polyfoam 320-395-2702 She'll sell you one..
FYI Frenchy - I called Polyfoam about that foam cutter you recommended and it wasn't such a great deal after all. $150 - not $50! and one more thing, you gave me their fax number. Their phone number is 320-395-2551. Thanks anyway... :-)>Kevin Halliburton
"I believe that architecture is a pragmatic art. To become art it must be built on a foundation of necessity." - I.M. Pei -
sorry about the phone number, but I'm fairly certain about the price I paid.. maybe it was a deal since I bought the panels there or something..
I can tell you that without it I couldn't have built this house since most of my panels were cut on site..
Going back to the discussion about whether SIPs have an outside and an inside face. IF this works, it will be a picture of my helper sitting at a temporary desk in a SIP house under construction (probably adding up the donuts & coffee order). The picture of the window opening shows how the slot used to cut out the electric chase should face the interior of the house.
D&L
Well I'm certainly not impressed with the panel mfgr and their trucks. Where's the plant...Ft Worth? Maybe I'll send a copy of the pic to OSHA...love those safety shoes your BIL is wearing! Looking forward to the rest of the story.
Do it right, or do it twice.
The trucking company was an independent outfit hired by the panel manufacturer. The manufacturer is Chapman Building Systems in Kerville, Texas and, with the one exception of missing a stack of panels on the first order, they have been outstanding. The fact that they were running a seven week backlog says plenty about their reputation. They told me I was looking at a minimum of six weeks when I ordered so the delay was purely my fault for not getting my drawings and order in sooner.
I can't say enough good things about C.B.S. in spite of the inconvenience of having to order my second shipment of panels early. I would also say you can tell a lot about a company by the way they handle their mistakes. The second I called them about my missing panels they were on the phone to a trucking company and had the whole order sitting within a mile of my house by three o'clock the next morning. We all make errors- I felt they did a good job of covering themselves on this one. Their representative, Thad Chambers, has been one of the best assets I've had in this whole venture too.
Would I use them again? Yea, in a heartbeat!
As to my brother-in-law's shoes... he wore them one day and his toes came out just fine. He did get a finger mashed pretty good though. He was in from Colorado and my father was in from Arizona for a week. They spent their vacation time helping to get me under way and I'd use them again in a heartbeat too. Hope I've still got a few friends and family members that will speak to me when this is all over with. Kevin Halliburton
"I believe that architecture is a pragmatic art. To become art it must be built on a foundation of necessity." - I.M. Pei -
Hello,
This is the Bother-in-law who was only in the picture because I didn't realize it was taken. I'm a computer geek by trade and I just wanted to help Kevin any way that I could. I did wear better shoes in the following days of the work. It is exciting to see the work on the house. I wish I had more vacation time to make more progress. If I have a house built, I will definitely ask the builder to use these panels.
A true testimony to these panels was the strength of winds that whipped the walls around, knocked the bracing loose, but the walls remained in place. The walls remained close to plumb and we continued to place other panels the following day.
Shayne, CO Rookie
Computer geek...well that explains the high-tech safety shoes. Don't know how you (and Wrecked) took the comment, but it was just meant to harass him a little ...like, is that the best you could get from the temp labor pool?Do it right, or do it twice.
Hey CORookie! Glad you chipped in- here and at the house. Thank you again for all your help - your efforts were a God send.
You mention a point that bears repeating. We set several panels on Monday on the East side of the house and braced them off with 2x4's. Monday night and early Tuesday morning we had some severe thunderstorms. We don't get rain in Abilene, Texas, we get drought occasionally broken by "severe thunderstorms" accompanied by 60 mph gusts of wind.
When we waded into the site the next morning we found all of our bracing torn loose and lying on the ground with the panels standing there defiantly asking for more. They took two more severe weather beatings without flinching in the same week. In fact, they stood up to the weather better than our crew. We finally pulled off for a full day just to let things dry out a little. What a mess!
Here is a shot of what things looked like Tuesday Morning. The dark cloud was that all of our bracing was on the ground. The rainbow was the fact that our panels weren't.View ImageKevin Halliburton
"I believe that architecture is a pragmatic art. To become art it must be built on a foundation of necessity." - I.M. Pei -
Kevin,
Glad to see you finally got something up on that slab!
But I still don't trust an Archy to build something :)
Seriously though.... Good luck and I look forward to watching the house go up.
Neil
P.S. I'm still thinking about that grad school thing....
Never be afraid to try something new. Remember, amateurs built the ark, Professionals build the Titanic.
P.S. I'm still thinking about that grad school thing....
Glad to hear it - now quit thinking and start planning! :-)>
By the way, since you've been pretty vocal about your disappointing experiences with the big box stores I thought I would post a couple of comments and pics of the outstanding quality and service I've been getting from my "contractor's choice" local lumber yard. I've thought about calling Lowes about twelve times since I started dealing with these guys and have been making Lowes my first stop when I need to pick up a stray item or two. The lumber yard I selected is not impressing me so far.
The other "contractors choice" local lumber yard I took my plans to didn't even bother to take a second glance at them. I called them the day before I told them I had to have lumber on site and they said they didn't know how to figure the takeoff since I was using panels. I said, "that's why I left you a phone number to call me with questions over a week ago." His response, "just bring me one of the other guys take offs and I can figure it from their pretty quick." I told him he could probably find a trash can around there big enough to put my plans in - I wouldn't waste the time on him it would take me to come by and pick them up.
Between repeatedly having to return completely wrong stuff and dealing with #2 lumber that I would hesitate to use for firewood I'm amassing quite a credit at the second lumber yard but hey, at least I'm not using one of those big box places... :-)>
Not only was the stack of scattered plywood in the second photo the wrong stuff they were obviously in a hurry when they delivered it. I went ahead and restacked it before they came back to pick it up and drop the right stuff.
I am beginning to remember why I don't do this stuff for a living any more.Kevin Halliburton
"I believe that architecture is a pragmatic art. To become art it must be built on a foundation of necessity." - I.M. Pei -
I don't see a grade stamp on the lumber.
All of the 2x4's around here are STD&Better (lower grade than #2).
I don't see a grade stamp on the lumber.
All of the 2x4's around here are STD&Better (lower grade than #2).
Actually, I looked at my receipt more closely and all of the lumber is #2, as I specified, except for the 92 5/8" studs in the photograph. Most of the lumber is pretty decent but the studs are terrible! I may have to spend some of my available credit on 8' - #2 2x4's and just cut them down to stud height. I can't see building a straight wall out of what I have. Kevin Halliburton
"I believe that architecture is a pragmatic art. To become art it must be built on a foundation of necessity." - I.M. Pei -
I should have included a few links early on. Here are a few spots in cyber space that I have found invaluable in preparing to build with SIPs:
http://www.sips-chapman.com/ - My panel supplier - far and away my best resource.
http://www.sipweb.com/ - very comprehensive resource
http://www.sips.org/ - Home of the Structural Insulated Panel Association
I would also highly recommend the following book:
http://www.amazon.com/exec/obidos/tg/detail/-/1561583510/102-0074215-0299370?vi=glance
If you haven't taken a look at SIPs please do. IMHO they are the home building product of the future. They are making serious in-roads in the commercial market as well. Kevin Halliburton
"I believe that architecture is a pragmatic art. To become art it must be built on a foundation of necessity." - I.M. Pei -
Since I'm new to Breaktime what does IMHO mean?
Insanely Moronic Home Owner, I think...
I know lots of them.....LOL
Edited 6/11/2003 12:56:57 PM ET by tickyboy
Edited 6/11/2003 12:57:44 PM ET by tickyboy
Ah, don't listen to Qtrmeg... He's old enough to remember the antiquated definition he gave you but the online jargon dictionary changed it a decade or so ago.
IMHO: In some folks cases it can mean "Incorrigible Malicious Halfwitted Obstinacy" :-)> but it generally means "In My Humble Opinion."
Course... IMHO, it is the individual interpretations of these things that keep our virtual world interesting.Kevin Halliburton
"I believe that architecture is a pragmatic art. To become art it must be built on a foundation of necessity." - I.M. Pei -
hunnh???
I always thought the H stood for honest?
Damn Architects, always messing things up..... ....... .......
Never be afraid to try something new. Remember, amateurs built the ark, Professionals build the Titanic.
Edited 6/12/2003 6:37:49 PM ET by CAG
That's why I keep pushing you so hard Neil. You just don't realize how much fun it is to have the power to change the rules. I'm still just an intern so I only get to change the rules every once in a while.
IMHO, you're going to be a great architect yourself one of these days. Course, when you get there you will have to change it to "In My Hardnosed Opinion" if you want to fit in. Keep hitting those books - we need the talent.
Kevin Halliburton
"I believe that architecture is a pragmatic art. To become art it must be built on a foundation of necessity." - I.M. Pei -
Thanks for the words of encouragment
And I do hit my books, I pound on them everynight, but it just doesn't seem to do me any good....maybe I should open them...Never be afraid to try something new. Remember, amateurs built the ark, Professionals build the Titanic.
Ok, IMHO it's time to get back to SIPs
I've been out of town for a couple of days on a photo shoot so I haven't been back on the job yet. Let me finish bringing everyone up to how we got to the point we are at now.
Once the base plates were laid out on the slab and glued and bolted down the next step was to mark the location of panels on the base plates and lay out the panels for the walls on the slab. I made a run into town to wrap up a few loose ends while my father and BIL finished up on the plates and carried all the wall panels for the East and West walls into position.
The 4 1/2" panels I'm using on the walls weigh about 2 Lbs/S.F. and the 5 1/2" panels weigh about 2.33 Lbs/S.F. so two people can handle most panels pretty easily. Panels can be fabricated in huge pieces that have to be lifted by a crane but it is more common to build from smaller, more manageable panels. Even so, most production builders will still put sections of wall together on the slab and lift a complete wall into place by some form of mechanical assistance.
We choose to build the wall in sections small enough to be lifted into place manually. Once the panels were roughly positioned where they would be lifted we cut all of the 2x4 material that would fit into the pockets in the wall and labeled the boards to match the panels.
The large 8'-0" window panel we started with consisted of a sill panel, a header panel and two panels on each side. Each of these panels consists of a 3 1/2" thick panel of Extruded Poly Styrene (EPS) sandwiched under pressure with structural adhesive between two sheets of 7/16" (1/2") OSB. The EPS is cut back at the factory with a hot knife or router to form 1 1/2" deep x 3 1/2" wide pockets on all four sides of each panel. These pockets will either hold a 2x4 or a factory built spline that will lock adjacent panels together depending on where they fall in the configuration.
The bottom pocket slips over the 2x4 base plate, the top pocket holds a long 2x4 top plate that locks all the panels together and forms the nail base for the overhang joist hangers. The side pockets hold the equivalent of king, jack and trimmer studs or a 3" wide "spline" that fills the side pockets of two adjoining panels to lock them together. There are other variations on this but I will concentrate on the style we are using.
A bead of structural adhesive is applied to both sides and the bottom of the pocket and the appropriate piece is inserted and nailed off with 8 penny nails or 1 1/2" staples at 6" on center. This takes a ton of fasteners and requires oiling your gun at least twice a day. It also takes a solid forearm or a pneumatic calking gun to apply the adhesive.
Here is a shot of the first panel raised, leveled and braced off with a couple of 2x4's. My BIL is applying the adhesive to insert the 2x material for the next panel.
View Image
Notice that the 2x4 top plate has not been installed yet. The top plate should be as long as possible to lock all the panels together. It is the last thing to go in on a wall.
You can also see an example of a short piece of "spline" lying on the slab behind him. We learned a lot on this first panel.Kevin Halliburton
"I believe that architecture is a pragmatic art. To become art it must be built on a foundation of necessity." - I.M. Pei -
WA..
What method(s) have you used to cut thru any panels?
OSB being strength orientated. Does the orientation at both horizontal and veticale [as in your first panel] compromise anything?
What method(s) have you used to cut thru any panels?
Glad you asked. There are several ways to cut Structural Insulated Panels including using special shoe plates bolted to a chainsaw, a Prazi beam cutter, a deep cutting circular saw or cutting both sides with a standard sized circular saw and finishing the cut through the foam with a hand saw or sawzall. Since I had all my cutouts and openings fabricated at the factory all I have to be concerned with is the occasional trim here and there.
The panels have a habit of growing in length as walls are put together. This is generally due to connections not being super tight to allow for OSB expansion and contraction. This expansion is not a particularly big deal but it may require you to adjust the width of a panel or two here and there by a fraction of an inch to stay on layout. This is one of the reasons it is a good idea to mark the layout of all of your panels on the base plates before you start putting them up. When you start covering up your layout marks it may be time to measure from the edge of the installed panel to the next layout mark and trim the next panel to that width.
To trim a panel just measure over to the new width and snap a chalk line down the edge. Trim off the excess with a circular saw on both sides. View Image
The dilemma you are faced with then is that the foam is too close to the edge of the panel and has to be cut back to 1 1/2" deep. If you have a special hot knife it is no big deal but such a specialized tool is not really necessary.
Foam routes easily. Think of those cheap, white, temporary coolers you haul to the beach and how easy they are to cut. The EPS in the panels is essentially the same stuff. The trick is getting the pocket cut to a uniform depth. A handy trick for this is to use a stiff 3" wire cone brush on a grinder. Foam goes everywhere but it makes a nice clean route. (Thanks to Thad Chambers for that tip) I didn't have a grinder and wire brush at my disposal when I needed to trim my first panel so I used the 1 1/2" fostner bit I had been cutting holes in the panel splines to line up with the built in wire chases with. (I will get to wire chases a little later on)
I just marked the depth on the bit and held it steady as I worked it down one side of the panel and back up the other. View Image
I then ran a bevel cut 2x4 down the pocket to clean it up. The results were a little slow but plenty satisfactory.View ImageKevin Halliburton
"I believe that architecture is a pragmatic art. To become art it must be built on a foundation of necessity." - I.M. Pei -
OSB being strength orientated. Does the orientation at both horizontal and veticale [as in your first panel] compromise anything?
I'm not sure I understand your question but let me answer it according to my interpretation. The answer, I believe, is no - the orientation of the panel has no adverse affect on its structural integrity.
Correct me if I'm wrong but it is my understanding that, because of its cross directional layup, OSB is equally strong in both directions.
From the web site of Structural Board Association http://www.osbguide.com :
View Image
How is OSB made?
View Image
OSB is manufactured from sustainable, fast-growing trees such as aspen poplar, southern yellow pine, mixed hardwoods, and other suitable species.
Logs are cut to length, debarked, and processed into precise strands ranging from 3 1/2" to 6" long and approximately 1" wide.
The strands are dried, sorted, and mixed with wax and a waterproof exterior-type binder and formed into large continuous mats. These mats are oriented in cross directional layers for increased strength, then pressed at a high temperature and pressure to form panels.
Throughout this highly automated and fully engineered process, panels are monitored, tested, and certified to meet stringent quality standards for strength and uniformity.
I did get the exterior side of the first couple of panels facing the interior (notice the red R-Control stamps on the inside - they should be on the outside) and I'm not sure if that will present a problem or not. The texture is slightly different inside and out but since the waterproofing in OSB is essentially integrated I think I will be ok anyway. As I said, we learned a lot on that first panel.Kevin Halliburton
"I believe that architecture is a pragmatic art. To become art it must be built on a foundation of necessity." - I.M. Pei -
Kevin, kudos for trying SIPs! I done a little research on them during the past decade, ever since I watched This Old House pseudo-renovated a Barn in Mass. intended to be someone's homes. They used timber-framing because of the shear size of the project, but all panels (and I believe also the roof panels, too) were SIPs.
What surprised me the most was that by the time they got to a stage where the exterior and roof panels were in place and the windows and exterior doors installed it was Winter. Well, that wasn't the surprising part, but rather the show's hosts commented on how a crew of 4-6 men working inside the completed 'shell' provided all necessary heating to work comfortably in while it was cold outdoors.
I guess this is the aspect of SIP construction in that it presents a tight weather envelope, and a lot of SIP projects requiring an air-exchangers in order to dump excessive heat both in Winter. But I digress (as always) and have a couple of questions for you:
1.) Your panels are pre-cut at the factory for door and window opening. What was the additional charge for this, if any, and what size panels (4'x8', 4'x12', etc.) and their thickness are you using? I've stumbled up some websites that made the panels up to 4'x24' and up to 12" in thickness.
2.) Probably the most important and unanswered question to the 'curious-minded' individual that doesn't want to call someone, what the heck did those panels cost you? Was their a fixed product rate for a 4'x8' panel at 4" thickness? BTW, I got read what you said about delivery costs and will keep that in mind.
You can make your own foam cutter for the edges. Just get a reostat (?) and some thin, flexible wire (stainless steel is good) a couple of surgical clamps and voila, a hot wire foam cutter. Connect it all up, dial up the voltage until the wire is hot enough to cut, have a partner grab one end (with the clamp), you the other and just guide the wire down one side of the OSB, pull to the other side and out, nice clean cut, no mess of foam all over the place and the slices can be used to fill in other gaps.
RobertRobert
Kartman0,
Excellent questions! I was wondering when someone would get around to asking about costs. The answers may vary from region to region so I hesitate to put hard numbers to your questions but hopefully I can answer them to your satisfaction. Let me touch on your digression first because you make another observation that is very important.
I guess this is the aspect of SIP construction in that it presents a tight weather envelope, and a lot of SIP projects requiring an air-exchangers in order to dump excessive heat both in Winter.
The number one, single, top of the list, most important thing to stress here is DO NOT OVERSIZE YOUR HVAC SYSTEM!!! I hired an engineer who specializes in energy efficient homes to do my energy analysis and calculate my HVAC loads - Richard Rue of Energy Wise Structures in Fort Worth, Texas. http://www.rrenergywise.com) The cost was $300 and it was some of the best money I spent in the design phase. I strongly recommend that you hire an HVAC consultant who knows what they are doing when building with SIPs. Richard Rue is one of the best, if not the best, in the industry.
My house is about a 2400 S.F. two story and will only require 3 1/2 tons of air. My Energy Wise analysis also included a guarantee that my average utility bill for any given year would not exceed $84.00/month or Energy Wise will pay the difference. The guarantee is based on the current utility rate of $0.086 per KWH (summer) and $0.0560 per KWH (winter) for electricity in my area. That can be compared to the average cost of heating and cooling a conventional stick built home at $258.00 per month. That is an average savings of $174 per month!
Probably the most important and unanswered question to the 'curious-minded' individual that doesn't want to call someone, what the heck did those panels cost you? Was their a fixed product rate for a 4'x8' panel at 4" thickness? BTW, I got read what you said about delivery costs and will keep that in mind.
I take your second question out of sequence because it relates directly to the first point you brought up. If you look at the reality of how much it costs to build with SIPs the answer is NOTHING. Whatever additional cost there is compared to conventional methods of construction is offset by the fact that you are pocketing money every month in utility savings. Even if the panels cost enough to add an additional $50/month to my mortgage over building conventionally, (which over a 30 year mortgage would be a huge difference in cost) I am still coming out an average of $120 per month ahead. I'm also saving a ton and a half of dough by utilizing a downsized HVAC system instead of the 5 tons worth of air I would have been putting in a conventional home.
The reality however is even better because SIPs are really not that much more expensive than conventional framing. If I've run my numbers correctly, I am somewhere around 2% to 3% higher on material costs for the panels than I would have been with conventional stick framing, sheathing and insulation. That cost could easily be made up in labor savings alone if I were hiring a builder to construct this home for us. (Another downside - some areas, such as mine, do not have builders experienced in this form of construction) One of the main reasons I am handling the SIP portion of this home myself.
Your panels are pre-cut at the factory for door and window opening. What was the additional charge for this, if any, and what size panels (4'x8', 4'x12', etc.) and their thickness are you using? I've stumbled up some websites that made the panels up to 4'x24' and up to 12" in thickness.
You can buy stock sized 4x8 panels or even jumbo sized panels in 8 foot widths by whatever length you want for additional savings if you want to do all of the fabrication yourself. Panel thicknesses are all one inch wider than dimensional lumber stock (4 1/2", 6 1/2", 8 1/2", 10 1/2", etc.) I am using 4 1/2" panels on the walls and 6 1/2" panels on the roof.
There is a charge of something like $20 per cut for custom fabrication at the plant where I had my panels built but again, that may vary from region to region and supplier to supplier. In my case it was worth it because I didn't have to invest in the special fabrication equipment and spend the time getting it fabricated correctly. I'm only building one of these.
For someone looking to go into production it would probably still be wise to have your first project or two fabricated at the factory and then see if you think you want to tackle the fabrication yourself. It's not that difficult but there is a learning curve and you will need a shop big enough to handle the job.
One final point - not all panels are created equal. Make sure the panels you select are UL rated. Far too many are not and the ones having delamination problems and other issues are almost always the ones that do not meet UL specifications in fabrication. If your panels do not have a UL stamp on them take a hard look at whether the savings you may or may not be getting are worth the risk.
R-Control is my panel of choice because of their excellent customer service, UL rating, and the use of "Timbor" treated foam which helps control insect infestation. R-Control is the only panel manufacturer I am aware of that utilizes this important barrier. Termites do not eat foam but the do tunnel and nest in it. The natural Timbor mineral helps prevent termites and other wood boring insects from ever becoming an issue.Kevin Halliburton
"I believe that architecture is a pragmatic art. To become art it must be built on a foundation of necessity." - I.M. Pei -
to add my perspective to a SIP home..
I had panels made that were 6 1/2 inch thick and 11 1/2 inch thick
they averaged $3.25 per sq.ft. I picked up the panels myself so there wan't any real costs other than some fuel (22 miles each way) I cut my own window openings myself. A circular saw (7 1/4 inch) plunge cut into the panels then a sawzal with a long blade cut thru the foam quickly. That way they can take the panels right off the assembly line..
my average delay was at worst three weeks and often I could order one day and get a day or two later..
My worst problem was the splines that join the panels together are a snug fit. if they've soaked by rain and the panels have soaked it's hard to get them to slide together. I finally wound up running the splines thru my planer to get them back to original thickness.. Next time instead of the OSB splines the mfg. sells I would use plywood spline I cut myself..
Wow! WA I've found this thread to be right there. Your replies have been exceptional. Thanks.
I asked about the strength orientation of a panel because every sheet of OSB that I can remember handleing had arrows stamped on it denoting the strength axis. The first picture shows the OSB orientation as both verticle and horizontal. Since I believe that you are using your panels as load bearing [or are they curtain] I wonder if this mattered or was illrevelant.
Thanks IMERC,
My panels are load bearing. I've never run into the arrows you describe but then again, maybe I just haven't been paying attention. You've inspired me to check into this a little more.
Any feedback from others on whether or not the orientation of load bearing OSB panels is critical?Kevin Halliburton
"I believe that architecture is a pragmatic art. To become art it must be built on a foundation of necessity." - I.M. Pei -
Don't understand your spline description...The EPS is cut back at the factory with a hot knife or router to form 1 1/2" deep x 3 1/2" wide pockets That sounds like you need a 4x4 for a spline, but you say These pockets will either hold a 2x4 pls explain.Do it right, or do it twice.
I'm still trying to figure out the home made fork lift.
In the case where 2x4's are used you have a pair of 2x4's glued and nailed together. You glue and insert a 2x4 in the first panel and nail it off then run a bead of adhesive down it and nail the 2x4 for the next panel onto it. When the next panel in erected it slips over the second 2x4 and is nailed off standing up.
Headers and sills for openings are worked into this scheme to provide bearing surfaces for both. The header and sill panels have trimmers inserted at the sides and a 2x4 plate at either the top or the bottom that runs full length over the ends of them. The header plate on the bottom side of the header panel extends an additional 1 1/2" into the adjoining panels on either side and rests on the top of the 2x4 nailed into that pocket. An additional filler 2x4 is added above the intersection of the header plate and trimmer
Maybe this will make it a little clearer - Header and Sill plates are shaded in red and the trimmers are shaded in blue:
View Image
The sequence of this assembly is to build all of the dimensional lumber framing around the header and sill plates and then slip the adjoining side panels over the protruding 2x4's.
Did that answer your question?Kevin Halliburton
"I believe that architecture is a pragmatic art. To become art it must be built on a foundation of necessity." - I.M. Pei -
The header/top plate and sill always made sense, and the theory of the splines is ok, I'm just a little out on the actual spline. In the pic of BIL caulking, you mention a scrap of spline on the ground...looks like a mini-sip. And if you use two 2x4's in tandem that makes sense.
Hey...your pics are not showing up on my pc. The first couple, as attachments, worked ok. Then you did one or two as inserts and attachments at the same time...couldn't see the inseret but the attachment worked. The latest 2-3 posts have only inserts and I can't see them. Any idea why?Do it right, or do it twice.
Your description of the spline as a mini-sip is pretty accurate. The foam in the panel sandwiches is 3 1/2" thick so that standard dimensional lumber can be inserted between the OSB panels when the foam is relieved. The splines are just like strips cut from a standard panel except that their total thickness, including the OSB, is 3 1/2" just like a 2x4. The dimensions of the OSB splines is the equivalent of a pair of 2x4's glued and nailed together. The advantage of the foam and OSB splines is that you do not create a thermal bridge with the solid lumber that can transfer the outside temperatures to the interior face of the wall.
There are other types of splines, such as the ones Frenchy is using, that are just the OSB strips. The panels have 1/2" wide grooves cut into the foam just behind the OSB that the strips slip into. That version is sort of like a pair of very long biscuit joints if you will. The version I am using is a little more expensive but they are much easier to work with. Especially if you radius the OSB with a router to make it easier to slip into the pocket. The adhesive beads are applied close to the edges of the pockets so that they are smeared into the pocket as the spline or dimensional lumber is inserted.
As far as my pictures not showing up, in post # 41, I tried Boss's method and apparently screwed it up because my insert doesn't show up on my computer either. As to the rest of them, such as post # 45, I don't know what could be wrong. My inserts are showing up fine there. I think you can right click over them to check their properties and copy the address to where I have them stored into your web browser's address field to look at them on the site where I stashed them. Come to think of it, I had a message on my answering machine last night that my BIL was having trouble seeing them too.
Hmmm... Is anybody else having trouble seeing my inserted pictures?Kevin Halliburton
"I believe that architecture is a pragmatic art. To become art it must be built on a foundation of necessity." - I.M. Pei -
Yes, I can see none.
Stef
i saw your pic that you did as an attachment.. none of your others post on my computer.. all i see is a little box with a red x .. and a lot of white space where the pic. should beMike Smith Rhode Island : Design / Build / Repair / Restore
I didn't get the pic either. This is like some one ripping ramdom pages out of super good novel.
Can a plan "B" worked up?
A spendable elsewere voucher or cash refund?
A radical discount? Because your "yard" is wasting your time, energy and money and hand select what you need [no matter how mant bunks you have to crack open] and have them deliver.
Raise hell about the delivery body and put a stop to that BS.
Not to be sarcastic, but I just finished cutting up 900 SYP 2x6x8s "culls" into fire wood. Many looked better than what was delivered to you.
Edit: Been watching. Nice work. I've been considering SIPs to use as curtain walls in a new shop. With what your thread has contained and the links I believe this is the way to go. Thanks.
Edited 6/10/2003 3:44:03 PM ET by IMERC
Hi Wrecked -
Thanks for the good words on my SIP project. The machine is called a "Lull" and was rented for the duration of the job which cost less than what it would have cost for a crane. These panels were BIG! 6' and 8' x as much as 24'. The walls are 6 1/2" thick and the roof is 8 1/2". To lift a panel they smacked a hole with a hammer, inserted a big hook and lifted it with a strap over the Lull's fork.
Cloud -
There's a house in Easthampton (Long Island) built by Bill Chaleff, who did my panel drawings, with lots of curved SIPs. Most of the roof of the house is made of curved panels. Worked really well. I think he also did a sort of dormitory with curved roof panels.
ronw
"...I have decided to expose myself to potential ridicule..."
Yup - We ought have fun with this one.........(-:
"My first mistake was not getting the panels ordered early enough."
Ain't you been readin' my posts ??? Truss and wall panel manufacturers ALWAYS lie about lead times. That's the first thing they teach us when we start in the business. Pay more attention next time.
Seriously - Hope your house goes well.
Remember my "Spec House From Hell" thread ??? I opened myself up for a lot of abuse there, but got almost none. I wouldn't worry about it too much.
Q: Why don't roosters have hands?
A: Because chickens don't have boobs.
"Remember my "Spec House From Hell" thread ??? I opened myself up for a lot of abuse there, but got almost none. I wouldn't worry about it too much."
Boss Hog,
I can't find this thread when I try searching it. Do you have the original message number so I can go straight to it?
Fez
Spec House from HellThe early bird gets the worm? That's just about the worst incentive program I've ever heard of
Kevin,
I don't see any seal between the osb and the concrete. Hopefully it's just bad eyesight..
Since water can wick up concrete and the cardinal rule is to seperate the OSB from the concrete. It's a detail I paid a lot of attention to..
I don't see any seal between the osb and the concrete. Hopefully it's just bad eyesight..
Well, this brings me to the next step - setting the bottom plates. I used a double bottom plate with treated 1 1/8" plywood cut to the width of the panels topped by a non-treated 2X4 that slips into the groove in the panel. Both are sealed to their respective surfaces with structural adhesive and the top 2x4 is nailed to the treated plate with 8's. The panels slip over the 2x4 and rest on the treated plate which separates them from the concrete and provides an even bearing surface for the structural part of the panels to rest on.
I then drilled through the stacked plates into the slab with a Hilti rotory hammer and anchored them with 7" expansion bolts. I initially tried pinning the treated plate to the slab with a Hilti PAF before nailing on the top 2x4 but I couldn't buy hot enough loads to sink the fasteners in my slab. I used a water reducer and a 5 1/2 sack mix so my concrete is a little harder than normal. Apparently, in Texas, you have to have a contractor's license to carry the loads I needed to compensate for the harder concrete. (So says the rental place where I got the PAF - then again, they didn't have the hotter loads anyway)
Ultimately I just carefully lined up the plates on my chalk line before I drilled for the anchor bolts, then lifted the plates, set the bolts, ran my adhesive bead, dropped the plates back down and tightened the anchors with my cordless impact.
As to the splines, I went ahead and ordered my splines from the factory but rather than plane them, as you did, I've incorporated a trick that is helping them pop in a lot easier. I set up a router table and radiused the edges on all of them. They have already been drenched with rain several times but I've had no problems so far. The attached photo is my father and BIL setting one of the bottom plates.Kevin Halliburton
"I believe that architecture is a pragmatic art. To become art it must be built on a foundation of necessity." - I.M. Pei -
I see they wear a different kind of work boot down there.
Excellence is its own reward!
Kevin
About time, was wonderling what was going on, you must be tickled pink to be under way.
Look forward to seeing more pics of the progress.
Doug
Kevin, what's with all the caveats? "Oh, it's not my day job." "Ohhh, don't be hard on me." Ha ha ha. Seriously, it'll be fun to follow progress. Maybe get Brian to move this to the Photo Gallery where it'll be easier to track.
And maybe we can get you to post in-line pictures. For as many as you'll be posting, it's easier to see them if part of the post rather than that yellow icon.
I'll probably have other demands as you go along, so keep a list. Just kidding. Glad you're making progress. Break a leg.
Kevin, what's with all the caveats? "Oh, it's not my day job." "Ohhh, don't be hard on me."
For the record I'm not too worried about how people perceive me and my abilities and I didn't ask anyone not to be hard on me. I just asked that the deserved smart-alec remarks be kept to a minimum so the focus could remain on SIP construction techniques.
As you have been an outstanding proponent of dome construction I am enthusiastic about SIPS. My interest is not in showing my house but rather in giving honest and usable information regarding SIP construction so that others can hopefully take something of value from my experience. As such, I posted under "construction techniques" instead of the "photo gallery" on purpose.
The only reason I pointed out that this is no longer my day job is so builders with more experience will not assume that SIP construction is a time consuming process. In my case it will be but as a general rule SIP houses go together substantially faster than conventionally framed houses. They are also much stronger, more energy efficient and more environmentally friendly.
I'll considered the idea of including the pictures directly in my posts. I will probably have to get some more storage space in cyber space to do that but it would make the thread a little easier to follow. Thanks for the feedback.Kevin Halliburton
"I believe that architecture is a pragmatic art. To become art it must be built on a foundation of necessity." - I.M. Pei -
Posting pics in your thread is no big deal. Just takes an extra step or two.
First, type out whatever text you want in the thread. While you're typing, attach a picture to your thread as you normally would.
Once the pictures are attached, hit the "preview" button and wait for your browser to go to the next screen.
When you see the picture attachment at the bottom of the preview, right-click on it and pick "open in new window". While that window is loading the picture, hit the "revise" button to come back to your original screen.
Then paste this line in your post while the picture is loading:
<IMG src="http://www.webserver.com/folder/picturename.jpg">
Then Click over to the other browser window and copy the URL out of the little box at the top of the screen. (It will be a long one) Then click back to the original thread and replace the text between the quote marks with it.
This is how it works for me in Netscape, anyway. Hope it makes sense.Those who watch time never see it.
Boss,
Thanks! That is a whole different technique than I've been using. I like the fact that the picture is uploaded to Breaktime rather than some other site. I'll give it a try the next time I post a picture. Looking at my last post I think I will make them a little smaller too.Kevin Halliburton
"I believe that architecture is a pragmatic art. To become art it must be built on a foundation of necessity." - I.M. Pei -
Glad I could be of some help.
Don't know why I'm helping you though - After that pic you posted with that JD sign...................)-:Those who can, do. Those who can't, get patents.
View ImageKevin Halliburton
"I believe that architecture is a pragmatic art. To become art it must be built on a foundation of necessity." - I.M. Pei -
Realize I'm just funning ya! Like one day I'm likely to ask where your curved SIP's are. :) Boss's way of posting pix seems to work great. Harder to do on a Mac be/c some of the buttons and options aren't the same. Only advantage I can think of from some alternate storage sites is some create thumbnails automatically, but that's just an observation and not a quibble. I _do_ look forward to learning about SIP's as long as there's no test at the end.
NICE rainbow--it's an omen!
Edited 6/10/2003 10:12:21 AM ET by Cloud Hidden
Hey Kevin,
Your mother sent me this link and I enjoyed learning about your house building process and the pictures.
I'm glad to see you are using SIPs for your new house. We built a large mechanic shop building for one of our customers, with the same kind of panels you are using, about 1 1/2 years ago, with 16 foot ceiling height and loved them. We are now in the preliminary stages of doing a new house with panels, but a different type of panel from before. The ones we are going to use this time don't have OSB on either side, are 71/4 inches thick, with an R value of 32. They have tubular steel members on both the inside and outside of the panel to attach siding and drywall to and weigh about 30% less. Using stucco on the outside as we are going to do, all the stucco contractor has to do is install his wire and stucco. We also plan to do all the inside framing using steel and further eliminate the headaches of working with the lower quality lumber that we are forced to use these days. Anyway both are good and as builders, we perfer to work with the panels over conventional construction any day, for all the same reasons everyone here has already pointed out. The drawback as you have also noted is having to work with yet another company to get them and having to wait for them, but that just requires more 'in advance' planning and scheduling and the end result is worth the extra effort. I'm attaching a couple pictures of the shop building we did.
I look forward to following your progress and wish I could be there to lend a hand also.
Your uncle John in Az
Hey John, what a pleasant surprise to log on and find you posting here!! You have no idea how much I wish you were close at hand. It's been a lot of years since we were banging nails together under Grandpa's guidance. I think the last time we worked together was on the house Mom and Dad built in Sierra Vista. You've certainly gone on to bigger and better things. I understand you are doing some beautiful homes in Northern Arizona these days.
If I'm not mistaken, the steel stud panels you referred to are by Thermasteel Corporation http://www.thermasteelpanels.com. I gave them a pretty strong consideration myself but the bid for them came in a little further out of budget than I wanted to go. The one thing I liked about those panels most was the fact that the finished wall was a standard dimensional thickness so doors and windows didn't require custom jamb and sill extensions. They are also a little lighter to handle making the erection process go a lot easier. Watch those fingers on the exposed metal edges though!
Let me be the first to welcome you to Breaktime. I've thought several times about inviting you to log on and participate in this forum. There are some great guys and gals here that help each other out a lot. Your vast experience and knowledge would sure be welcome if you feel like sticking around and contributing elsewhere.
It's been way too long - great to hear from you!Kevin Halliburton
"I believe that architecture is a pragmatic art. To become art it must be built on a foundation of necessity." - I.M. Pei -
Wow, that is some shop.
At first glance I thought it was a standard garage, and the toyota was some kind of tool, like a compressor or generator.
A good heart embiggins even the smallest person.
Quittin' Time
Can't see where the compression strength comes from.
Very interesting discussion, I'm enjoying reading it. I've built two houses so far with SIP's from the R-Control people out here in Almost West Virginia. The question was raised in this thread - is there any problem with having the SIP reversed so that the outside skin is on the inside skin? My answer would be "No, so long as any horizontal electrical chases line up perfectly with the adjacent side panels."
In my experience, you should be ok. The only difference in the panels I used between the outside of the SIP and the inside is that the hot wire used to bore the electrical chases was pulled from the "inside", so that there is a tiny gap in the foam at that point. Putting that on the inside of the exterior wall makes the house a little tighter. If your SIPs were drilled using the same method, you'll be able to see a tiny slot when you look at the edge of the panel.
You may have already mentioned doing this - Are you putting pull strings in your horizontal runs and marking the vertical electrical drop locations on your decking?
best wishes,
Dusty and Lefty
I am marking all chase locations on my panels, vertical and horizontal, but I hadn't thought about pulling a string as the panels go together. It should be no problem to pull wire with a fish tape later but the string idea might have been easier.Kevin Halliburton
"I believe that architecture is a pragmatic art. To become art it must be built on a foundation of necessity." - I.M. Pei -
I think it was IMERC that asked about how important the orientation of OSB panels are to the strength of a wall. I did a little research and apparently it is pretty important. Here is a technical bulletin published by R-Control that covers it pretty well. I checked and some of my window sill panels break the rules. Probably no big deal there but I'm going to be watching my header panels like a hawk from now on.
(By the way, in case anyone is wondering, I did get written permission from R-Control to post their material in this thread. Please be mindful of the fact that it is copyrighted if you use it elsewhere. Anything I write personally is yours for the taking. -Thanks-)
OSB Direction
June 1988 (Revised March 1999)
subject:
date:
technical bulletin
sip no. 2010
AFM¯ Corporation Box 530 Excelsior, MN 55331 Phone 800 255 0176 Fax 952 474 2074
http://www.r-control.com
AFM R-Control¯ original structural testing on R-Control SIPs was completed using panels manufactured with waferboard skins. The wood flakes used in production of the waferboard had no specific orientation. Random orientation of the wood flakes caused the manufactured panel to have similar strength characteristics in all directions.
Since the time of our original work, the engineered wood industry has further refined their product through processing changes. These process changes have created a better panel, but at the same time changes have occurred in the strength characteristics. Oriented Strand Board (OSB) has replace waferboard.
OSB does have a definite strength direction. That is, the panel is stronger in the machine direction versus the cross machine direction. The machine direction is easily discernible on most panels, as the majority of the flakes visible will be parallel to the machine direction. Some manufacturers indicate with markings which direction the strength runs in a panel.
Thus, R-Control SIPs are to be used in the machine direction. For example, a 4 x 10 foot panel is manufactured with the OSB machine direction parallel to the 10 foot length. This ensures the performance of R-Control SIPs as derived in the R-Control Load Design Charts. Kevin Halliburton
"I believe that architecture is a pragmatic art. To become art it must be built on a foundation of necessity." - I.M. Pei -
Kevin, grab a dust mask. SARS has invaded Cental Texas. Namely Abilene. That stuff is scary!
Yea, caught that on the news this AM. Of all the places in America where there could be an outbreak of SARS... Abilene! Must be the Air Force Base. Not too many world travelers around here besides those fly boys.
Never lived in a place I felt safer - you just never know...
The last I heard they had not definitely identified the cases as SARS but the symptoms are all the same.
Thanks for the heads up!Kevin Halliburton
"I believe that architecture is a pragmatic art. To become art it must be built on a foundation of necessity." - I.M. Pei -
Kevin,
I, too, just got back to the site.
Our panels have 1/6 t&g applied to the under side, so we were reluctant to use through fittings. I asked the company how they handle it and they said" Hayhooks".
Having been raised on a farm, I knew what they were, but couldn't see their application here. Company said, Screw a 2/4 across the panel, bash hole through the OSB, and grab it with a hay hook. Yes, the same device used on a farm.
I couldn't bring myself to be so crude, so as I said in an earlier post. We ended up using hugh eye hooks, with 2x4s on each surface of the panel.
I'm going to try some more pictures tomorrow. I think my problem was they took too long to load, and I'm not known for patience.
I'll try Irfan-ing them after I learn how to load them.
Bear with me on the large file sizes.
Stef
Stef.
As requested, I asked the GC that is going to build us a house out of the SIP panels he makes if I should post his name here and he said to go ahead, that if anyone has any questions on the SIP panels he makes and builds with, he will be glad to answer them, so here it is:
Jim Clarke, Hereford, TX, 1-806-364-4881. One of his sons is also a builder but Jim is the one that fabricates the panels.
I hope that this helps those that have any questions, like about the shingles recomended for those kinds of roofs.
Sorry about SARS being in your area. Be careful about mixing with big groups of people. Hopefully they will contain it well and soon.
Here goes trying to send some pictures of flying our panels.
Looks like I finally figured it out.
Here are the rest. See how we went from the plates to the eyebolts. With the plate we did have one panel fall off the roof. Pretty dramatic to see 24x8 panel sliding like a snow sleigh.
Stef
Very nice Stef! Thank you for that great series of installation shots.
Now, do you have any shots of the valleys and hips going together? It looks like you were using double dimensional lumber splines to connect the panels together. In the interest of education would you mind detailing the step by step procedure of setting those panels?
I'm guessing you probably glued up each connection, slipped the panels together, nailed off at 6" on center both sides and then pinned them to your beams with panel screws at 18" or 24" on center. Also, How long did it take for the crew to complete the job?
That is a great looking house! Looking forward to some finished pics too.Kevin Halliburton
"I believe that architecture is a pragmatic art. To become art it must be built on a foundation of necessity." - I.M. Pei -
I'll get some pictures of the valleys going together this week. We were pretty much in the dark as to how to cut the valleys, inasmuch as the east and west wings aren't at right angles to the north and south wings and we got no help from the panel manufacturer. So it was pretty much trial and error. Didn't end up being a very elegant fit.
We used 2x10 dimensional for the splines. The factory glued them to one edge, and we bashed them together. We did use glue, but no screws. However, we placed the 14inch panel screws at 6in centers along ridge, purlin and plate logs. We also glued along the plate log. We drilled holes at 8in along the applied side of the spline, and foamed them. At the peak we kept 1/2 to 1 inch space so we could foam down to the ridge log.
It took that crew 4 days to place the panels, and then another 6 days with just my son in law, wife, and me to place the rest. Plenty of crane time. The first crew was my sons, my brother, and a high school chum. Cheap but motivated labor.
Stef
Edited 7/12/2003 1:48:55 PM ET by stef
Interesting thread. Especially seeing as SIPs are what I count on to pay the bills. Thought you might like to see what we use to fabricate in the field. My crews have two sizes to better accommodate different panel thickness. The saw is a Sthil (electric). It beats flipping a panel by a long shot.
In addition, I make my own panel hooks designed to lift panel sections as large as 16' X 24'. They work in pairs with two high and two low. A buckle allows you to set the slope of the panel to match the roof. I'll dig up some pics of them in use and attach them soon.
Hope this helps,
Al
I appreciate you taking time to join this discussion. My panel supplier gave me the name of a guy who builds machined aluminum saw plates that bolt to the bar on a chainsaw like that when I was considering doing all of the fabrication of my panels myself. I asked him to send me a picture of it and he sent me the actual shoe plate instead. I really liked the design but decided to have my panels prefabbed so I took it to my panel supplier and he found a buyer for it. I'll see if I can dig up his information and post it. All I can remember is that his first name was Brian - yea, real helpful I know...
I would like to see some of your other fabrication equipment too if you don't mind posting a few more pictures. Particularly the foam cutter. I've had to make enough modifications to my panels now that I'm getting pretty comfortable working with them. If I ever build another SIP house I will probably handle the fabrication myself. I'm not too crazy about the tolerances of several of the factory foam reliefs on my panels. I'm using up a lot of spray foam filling gaps.
Look forward to learning more from you. Thanks again for jumping in with a professional perspective. Kevin Halliburton
"I believe that architecture is a pragmatic art. To become art it must be built on a foundation of necessity." - I.M. Pei -
Great tool !
Would it be possible to get a couple of shots of that plate without the saw ? One oblique like you have already done, but closer, and the other, kind of looking down the throat of where the chainsw goes. I'd kind of like to get an idea of how the chainsaw is held in there.
Here are your pics resized, so people don't have to scroll. If you have the other shots, I kind of like the big pic size you posted. I'll resize and repost if need be.
And how about that panel hook of yours ?
: ) A good heart embiggins even the smallest person.
Quittin' Time
LUKA!
do you have patent infrigement in mind?
ROFLOL
No way hosey !!!
I may be dumb, but I ain't stupid. (Nor am I unscrupulous.)
I was thinking I could use that as inspiration for a sort of tablesaw made from a chainsaw. For squaring out some small logs. What I would make wouldn't end up being a whole lot like this, but this gives me the idea. The connection to the chainsaw being the one thing I most need to figure out... A good heart embiggins even the smallest person.
Quittin' Time
The plate I was sent required you to drill two holes in the bar of the chain saw and bolt it to a machined aluminum block that was attached to a steel rod that pivoted where it mounted to the plate at both ends. (that's not a very good word picture is it?)
Basically your answer is to offest and attach whatever you build directly to the bar of the chainsaw, not the motor.Kevin Halliburton
"I believe that architecture is a pragmatic art. To become art it must be built on a foundation of necessity." - I.M. Pei -
Inverted worm with a Prazzie.
Help me with sizing my pics and I'll post any number of thousands of them.
What do you want? Details, tools, mistakes, how-to's
I'm passing the 200 mark on number of installs and would be happy to share my experiences. Just help me solve this pixel/file size issue.
Thanks in advance,
Al
Panelwright,
Do a google search on Irfanview.
It is a graphics program. Free.
Get the program installed on your computer, then use it to resize your pics. It lets you control the pixel size of the pic, as well as the amount of space it will take up on your hard drive.
I still do prefer the bigger pics. I can see the detail in them better.
Do you have to drill holes in your chain bar. Like WA said ? It seemed to me that yours was more adjustable than what I would have if I drilled holes in the bar. eg, the legth of bar below the plate could be adjusted. A good heart embiggins even the smallest person.
Quittin' Time
Thanks for the assist. Hope these attachments are user friendly to all.
This saw guide is the latest one we have in inventory. It uses two bolts which pinch the saw bar. Care should be taken so that the pinched bar doesn't prevent free movement of the cutting chain. This is an issue of positioning. It can be loosened and adjusted up or down the bar's length to accomodate for panel thickness and how much bar you want protruding thru the panel. I have found that some amount of slippage could easily be prevented by drilling small indents into the bar with a 1/2" bit. However, I'm looking into a design change that will use a bolt with a barbed point which will penetrate the bar slightly. (back to the McMaster Carr catalog) The small blocks on the corners are to prevent the thin plate from slipping under a straight edge.
The cost? I sell a guide for $350.00 (I knew someone would ask)
Thank you.
Yes, those are more user-friendly. And exactly what I needed.
If I use any part of the idea at all, it will be that bar clamp. Only one, and only for a sort of table saw.
My chainsaw does not have the dog holes anymore. They were broken off before I bought it. So, I couldn't use any ideas for bolting it to a table that way.
I will probably mount it with the chainsaw suspened above the "table". Possibly clamped again under the table. This would keep the body of the chainsaw above the chips, and the extra bar clamp below will lend a lot more stability. Needed, since the log is being shoved past the bar, and not the other way around.
Would it be good to put barbed points on the spacer block on the other side, as well ?
Thanks again.
: ) A good heart embiggins even the smallest person.
Quittin' Time
Thought I would show you all what a set of SIP Fabrication Drawings look like. These are AutoCad Drawing Web Format (DWF) files of the SIP Shop Fabrication Drawings and will require Autodesk Express Viewer to review them. It can be downloaded for free here. I tried to produce image files that would be easier to view here but they were too grainy to be of any use. Hope you don't mind the extra steps of downloading the files and viewer.
Sip-1 and 2 and 3D-Views are the fabrication drawings for the SIPS only so the model does not show the wrap around porch or garage that protrudes from the Northwest corner. I've also included the first and second floor plans for reference.
Most SIP suppliers will produce the SIP fabrication drawings for you (except for the 3D views) off of a standard set of plans. My SIP supplier charges about $800 to produce Shop Fabrication Drawings like these. The supplier must have the separate fabrication drawings in order to make the panels so if you are having your panels factory built be sure to include these drawings in your budget or design/drafting specifications.
Kevin Halliburton
"I believe that architecture is a pragmatic art. To become art it must be built on a foundation of necessity." - I.M. Pei -
Edited 7/16/2003 6:34:08 PM ET by Wrecked Angle
AAAAArrrrggggg!!!! You 'puter nerd types. Couldn't open.
Edited 7/16/2003 3:07:26 PM ET by IMERC
Sorry IMERC - I'm not trying to be fancy or difficult, this is just the only way to publish a legible version of a 22"x33" Autocad drawing on the internet. It's pretty easy to install the program I pointed you to. Just click on the link and follow the directions.
You will have to download the drawing files to your computer too. First you have to right click over the attached files and select "save target as" from the pop-up menu. Direct the files to a folder you can find again on your computer, install the Autodesk viewer then launch it and open the files with it. If you have any trouble with any of these steps let me know and I will try to be more specific.Kevin Halliburton
"I believe that architecture is a pragmatic art. To become art it must be built on a foundation of necessity." - I.M. Pei -
You do things differantly than I do.. I built the timberframe and measure what I'll need and then go to the factory and have them make it for me.. actually I just measured up what I'd need and ordered.. while I have some offcuts and waste there is no more than if I had drawings done first.. They can't cut a panel at a 27/12 pitch nor could they cut the window openings for me any cheaper than I did.. In the end I had a bunch of window size panels to give away.. excellant for dog houses.. little too small for Ice houses..
Just an interesting side note...
They have used the same picture on their index page as UPS global does.
I wonder if one or the other is a copyright infringement, or if it is simply some sort of clip art ?
http://usa.autodesk.com/adsk/servlet/index?siteID=123112&id=2404513
http://www.ups.com/content/global/index.jsx
A good heart embiggins even the smallest person.
Quittin' Time
Luca
Typically, advertising/layout people buy photos through a "stock photo" agency. What they typically buy is a non-exclusive one time use. I.e., you can use the photograph for a single advertising campaign or a single magazine article for the set fee. The photo agency is then able to sell the use of the same photograph to other users. For example, my mother sold one time useage rights for the use a photograph of Celilo falls in a textbook. She has also used the photograph in her own book and is free to sell additional usage rights to others.
Black Star is a pretty famous stock agency:
http://www.blackstar.com/stock/index.html
Another (of which I am not familiar but in which it is easier to browse their collection) is
http://www.tssphoto.com/
That makes sense.
Do they get to change the picture, and/or change the name as well ? A good heart embiggins even the smallest person.
Quittin' Time
I don't know what the stock contract specifies, but I suppose with enough dollars up front, you could negotiate whatever you wanted...
200 installs?! Wow, you've been there. I've been pressing Taunton to do a SIP article for the magazine. You may be just the guy for the article if I can talk them into it.
This thread is intended to be a resource for the professionals that frequent the site that want to know more about Sips. My house project just gave me the opportunity to showcase the technology a little.
As an Architectural Intern, completely sold on their value, I'm basically serving as a panel cheerleader and semi informed answer guy till someone that really knows what they are doing comes along.
Hello! Glad you came along. :-)>
Thanks for your willingness to educate us a little. If you don't mind, I would like to give you the floor for a while, while I sit back and learn something from a pro. Just look at us like a bunch of experienced builders that want to expand our capabilities into Sips. What do you think we need to know before we jump in?
I guess for starters, would you mind covering some of the specialty tools that you find invaluable and either where you bought them or how you made them?Kevin Halliburton
"I believe that architecture is a pragmatic art. To become art it must be built on a foundation of necessity." - I.M. Pei -
hello everyone,
yes I'm a newbie. Please forgive me if I am jumping in at the wrong place; I would really appreciate the comments of some of you that have been using SIPs for a while.
I built a cottage about 10 years ago using SIPs and I was/am really sold on them. I used them in the walls and for a sloped ceiling/roof deck. As I was building the cottage, I had too many irons in the fire, and the cottoge was finished by someone else. QC went by the wayside. The roof panels were nailed into the 2x10 paired joists from the top side only, and drywall was omited from the underside. As a result, over the years,the ceiling/roof sagged rather noticeably between the paired 4'oc joists. The joists did not sag, just the OSB skin between them. Shingle roofing was nailed straight onto the deck as opposed to using a cold deck sleeper system.
My questions are these:
1a) has anyone else had this problem, and 1b) could the sagging be attributed solely to the inadequate nailing, as opposed to say the lack of drywall, or lack of an underside vapor barrier, or even putting the shingles straight onto the deck?
2) Are SIPs really suitable for floors as AFM would lead me to believe? The cottage was built on a concrete slab.
Thanks...
I can only address one issue regarding the use of SIP's and roofing. They make cedar breather to ensure that the shakes don't fail due to trapped moisture.
My opinion regarding sagging, if you used the screw/nail schedule that AFM recommends, I suspect that the lack of drywall and vapor barrier is prime reason for your sagging. While there has been some issue of foam creep, it's seldom enough for any visable sagging..
How much are we talking about?
nailed into the 2x10 paired joists from the top side only
That's OK?
SamT
Not according to AFM it isn't! They need to be nailed to the spline on, I think, a four inch nailing schedule and then they need to be screwed in place with those long screws every 4 to 6 inches. Your builder did use the proper amount of the adhesive they sell didn't he? I can look it up in my build book if you'd like me to verify.
Or you can call direct, Their number is 320-395-2551 ask for either Nancy or Dave..
I am replying to several posts here.
Fiberglass shingles on tar paper was the roofing, not shakes.
The sag was about 3/4" over the 4' span. 8d cc @ 5-6" spacing were used as well as the long screws at the high end and low end of the panel. Lots of R-control adhesive was used, and may have kept the damage from being worse. After the roof planels were placed, every one was so enamored with the system that they forgot to come back and nail the panels from the bottom/inside.
I have the R-Control book, and obviously my installation did not meet their current guidelines, so I am not faulting them. I would still like some assurance from some of you who don't have ties to the manufacturer that these panels perform well over time and don't sag in the ceiling or floor.
The story continues: I would like to use SIPs at the coast, but I am concerned that the frequent high humidity salt spray would eventually weaken the bottom skin of the floor panels.
It isn't too convincing for me to try to use this cottage as an example of how wonderful SIPs are, even though I may actually believe that.
I can't speak for others, but I sell construction forklifts (Ingersol Rand) for a living. I'm a customer of AFM just like you and did a lot of research prior to selecting AFM and SIPs in general..
regarding the issue of skin exposure to moisture.. I'm inclined to believe that it's a no-no! (I spent a great deal of time with the factory on this issue) what they recommended where there might be a problem of exposure would to either cover it with something capable of not wicking into the OSB such as plastic,Vinyl, cement, etc..
Occasional wetting isn't a real problem.. There are plenty of houses built with SIPs that sit in the snow until it melts with no injury.. continuance wetting should be avoided with any wood product..
One thing I did do with my house is to place the SIPs in the horizontal rather than the vertical..
much easier to assemble correctly and far easier to glue and then shove in the splines..
In addition if you read the AFM assembly book there are strength issues gained in the horizontal rather than the vertical..
My memory is dim, but I think there was a story a couple of years ago about SIP houses failing quickly in Juneau Alaska. As I recall they said it was the result of improper installation combined with the very high humidity there. The installation in such conditions had to be absolutely perfect, no mistakes, or the things would fail.
Of course, some of those brain cells have moved on to storing other information, so I could be totally making this up.
Your SIP sag is almost certainly due to the fact that the bottom stress skin was not correctly nailed. The nailing criteria is not a suggestion - it is absolutely critical. The structural integrity of the entire system hinges on the adhesive and fasteners. It is also fairly important that all panel fasteners be installed before the adhesive sets. Might as well leave the nuts off the bolts holding a steel beam up.
I'm sorry homey - This is not a small problem. Get a rep from the panel factory on site as quickly as possible. Hopefully they will be able to come up with a good solution or a competent attorney. I'm afraid you may end up needing both.Kevin Halliburton
"Do you see a man skilled in his work? He will serve before kings; he will not serve before obscure men." - Solomon
"This is not a small problem. Get a rep from the panel factory on site as quickly as possible. Hopefully they will be able to come up with a good solution..."
Since drywall was not initally installed, I was able to come back and and pull the separated bottom skins back up to the 2x10 splines with many, many (3-4"oc) stout deck screws. And then drywall was finally added. The sag is still, and always will be, noticeable from the roof side, but not the from the inside. At least the structure is somewhat more secure.
But again, that was in the past, and now I am trying to project to the future based on the collective experience of all of you who do it right the first time.
Guys
Promised some more pics of our SIP roof, so here goes
Sorry,
Wrong view-I'll try again.
STef
Sorry guys
I resized them but obviously not enough
I'll do better next time
S.
For those of you not lucky enough to have highspeed
Never be afraid to try something new. Remember, amateurs built the ark, Professionals built the Titanic.
CAG,
thanks for fixin those for me
STef
The compression strength comes from the strength of the three materials being bonded together with structural adhesive under pressure. Compression forces pushing down on the top of the wall will try to flatten it by bulging the middle of the wall out in both directions. As the wall is loaded up that force, acting essentially on the center of the wall is dissipated over a very large area.
You may be thinking that OSB isn't very strong if you stand it on end and apply a compression force down on it from the top but it's only because 7/16" thick OSB panels have no way to resist buckling. When they are sandwiched together with the foam it creates a rigid panel that resists buckling very well. Essentially you end up with is 7/8" thick insulated framing members at 0" on center.
A good example that comes to mind right off the top of my head is foamcore for mounting prints before framing. Visit your hobby store and pick up a piece of it. All it amounts to is a couple of sheets of paper glued to a thin foam core. None of the components on their own has any real strength but when they are bonded together they are incredibly strong.
One more analogy. Think of a wood I-beam with an OSB web. Among other things the two thin strips of wood at the top and bottom hold it rigid and prevent it from buckling. When OSB is held rigid like that it has tremendous resistance to compressive and sheer forces.
Here is a .PDF file showing the design loads of R-Control panels. You will need Adobe Acrobat Reader to read it. If you don't have it you can get it here for free.Kevin Halliburton
"I believe that architecture is a pragmatic art. To become art it must be built on a foundation of necessity." - I.M. Pei -
Got it. This scarey, you wrote wll enough for me to under stand. Was thinking in terms of individual components vs a unit.