Hey- does anybody do balloon framing anymore? I have never done it, but am curious as we are going to build a house with full first floor and three foot knee wall in the second floor. It seems to make sense to frame those walls full height, notch in a ledger for support of joists, which would be nailed to sides of wall studs any way, go with a double top plate to tie all exterior walls together, frame interior walls, then the floor system, then do it all over again on the second floor. Makes a nice continuous load path from rafter to foundation, with a supported ridge beam and the rafters hung there is virtually no rafter thrust to deal with, and you get a full channel from floor to eave to insulate with no thermal breaks, esp. if you do a Mooney type wall. What am I missing? I have always framed in platforms, the way I commonly have seen it been done, so why does it seem too easy? Anybody else out there lie awake in bed at night trying to sort out pros and cons?
Discussion Forum
Discussion Forum
Up Next
Video Shorts
Featured Story
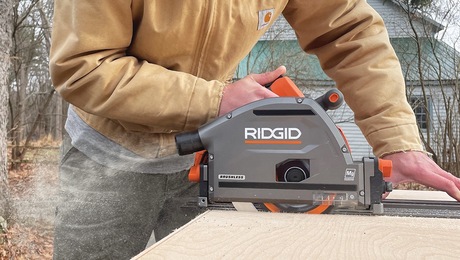
The best tool for straight, splinter-free cuts is made even better without a cord.
Highlights
"I have learned so much thanks to the searchable articles on the FHB website. I can confidently say that I expect to be a life-long subscriber." - M.K.
Replies
I live in an old house with balloon framing. I think the biggest reason you don't see it that much anymore is that 1-1/2 story houses aren't as common as full 2-story houses now. Also, it's more common these days to use prefab trusses as opposed to stick framing a roof, so that may have something to do with it, too.
But if you go with a structural ridge (as you suggest), it seems to be a very sensible approach when builing a 1-1/2 story house.
Maybe you'll get some comments from the framers here -- they should have a lot more to say about it.
Balloon frame is fine for what you describe.
>>get a full channel from floor to eave to insulate with no thermal breaks<<
You would not be permitted to do this here. We can balloon frame but must install solid fire blocking (AKA, thermal break) every 8' of vertical "shaft".
Most commonly the blocking is installed 8' above the subfloor, but I think you can move it - just so you do not end up with more than 8' clear shaft. I would check with the BI.
Jim
Yeah- thanks for reminding me of that- I had it in my mind, forgot to include it in post.
Our home is an 1880-era balloon framed house. It's a full two stories. I'm no framer, but I thought the reason balloon framing declined in favor of platform framing was because, as old growth forests were were used up, it became more and more difficult to find 18 foot straight 2x4s.
Chip
It seems to make sense to frame those walls full height, notch in a ledger for support of joists, which would be nailed to sides of wall studs any way, go with a double top plate to tie all exterior walls together, frame interior walls, then the floor system, then do it all over again on the second floor. Makes a nice continuous load path from rafter to foundation, with a supported ridge beam and the rafters hung there is virtually no rafter thrust to deal with, and you get a full channel from floor to eave to insulate with no thermal breaks, esp.
What about all the thermal breaks your making by notching in a ledger and then nailing all the fire blocks in where the bottom of the joists are? We have to do that here. There goes your thermal breaks.
Frame the walls like normal and sit the joists on top of the plate and then nail your kneewall along side the joists and into the top plates.
Notching a ledger and fire blocking is a lot of extra work. Is this all just because of thermal breaks?
No the thermal breaks were just a pro in there somewhere. It was more just the ability to frame one taller wall as opposed to framing one shorter wall, putting the floor on it and then framing another on top. Those studs are just transferring the load straight down to the ones below, why not make them full height?
I use a hybrid platform/balloon frame which you might consider for your project.
Start with a platform for the first deck. This gives you a working surface. Then build a balloon frame for the 1½ storey walls, with either a let in 1x4 or a lagged on ledger:
View Image
I've built a number of balloon-framed houses and the inspectors have accepted dense-pack cellulose as a firestop. If you're required to use solid wood firestops (they go between each level, not at 8' increments), then you can add blocking as was commonly done.
View Image
A good article on the history and pros and cons of balloon framing is at:
http://en.wikipedia.org/wiki/Balloon_framing#Balloon_framing
Solar & Super-Insulated Healthy Homes
Edited 3/14/2008 3:04 pm ET by Riversong
I don't belive fire blocking is required on outside walls when filled with either fibreglass or cellulose.
We baloon frame tall walls all the time for 2 story great rooms
Fire blocking is definitately required with fiberglass insulation (as f.g. will do nothing to stop fire), and many inspectors might require it in any case.
Riversong HouseWright
Design * * Build * * Renovate * * ConsultSolar & Super-Insulated Healthy Homes
How do you guys lift those tall walls, lots of help or with mechanical aid?
We try to get a crane.
Iwork for a guy that had 3 crews of 6-8 guys. when no crane available, 2 crews could get them up.
Lots of fun
>>they go between each level, not at 8' increments<<
Maybe in VT, not in DE.
Assume a platform framed residential structure. 9' ceilings.
The top plates count as a fire stop for between levels, BUT we install fireblocking at least 1' above the floor or 1' down from the top plate. Can be right in the center of the vertical run.
The local interpretation says " no vertical shaft space taller than 8', interior or exterior walls". They also don't care if the space is insulated or not.
That's why I said to check with the BI.
Jim
Never underestimate the value of a sharp pencil or good light.
The local interpretation says " no vertical shaft space taller than 8', interior or exterior walls".
Is that the wording of the code or just the "local interpretion"?
As a designer, a builder, and a firefighter that makes no sense at all.
Far more important is to firestop open interior soffits, stairways along the stringer, as well as at each floor and ceiling and between attached garage and living space and between multiple units in the attic.
Riversong HouseWright
Design * * Build * * Renovate * * ConsultSolar & Super-Insulated Healthy Homes
>>The local interpretation says " no vertical shaft space taller than 8', interior or exterior walls".
Is that the wording of the code or just the "local interpretion"?<<
Just like I said - local interpretation ---- AKA the way it has to be built if you want to pass your framing inspection.
JimNever underestimate the value of a sharp pencil or good light.
If you decide to go this route we are building our tall walls for great rooms and such out of Timberstrand materials and i think they would be an excellent choice for your balloon framed walls
Those are the osb 2x materials, right? How does the cost compare? I'm sure their straightness accounts for alot of saved time and money down the line.
Up here they are 2 to 3 times the cost of regular lumber in standard lengths but good luck finding SPF in 20' lenghts that is straight and does not shrink.
scramble..
My West Wing is done with ballon framing.. timbers that is.. ballon framed timbers but the principle is the same..
Nothing wrong with it.. (but don't forget to put the required fire break in)..
In your case balloon framing makes sense. I haven't balloon framed since 1960 or so.
Then balloon framing was fairly common. We framed the walls on the floor and stood them up with a small truck crane. We sheathed with t&g 1x6 on a 45° while on the floor.Even the short walls that fit inbetween were done this way. The sheathing on these walls did not extend to meet the long wall sheathing . The corner posts were 4x4's pre bored for wiring around corners.After the walls were up the corners were thru bolted 12" oc.The second floor joists were nailed and bolted, sitting on a 1x2 nailed with one 6d double head nail. The 1x2 was also a ground for plaster.
These old houses will last a long time, if I recall correctly they sold for $29000.00 .
We stopped balloon framing when straight lengths of long framing lumber became scarce. Times have changed a lot. In those days I never heard of compound mitersaws, never used a router or a nailgun. I remember my uncle trying to figure out how to load the magazine on his first nailgun.He said " this piece of #### will never replace a hammer".I can't tell you what he said the first time he tried to screw metal studs with panhead screws, something like @#^& *.
mike
This is a general response to balloon framing, not all of the following will hold true in your particular case. The reason balloon framing is no longer commonly used has to do with why it was done in the first place. Balloon framing was used to minimize cutting when everything was cut by hand. It was justifiable to have less cutting even when considering the down sides of balloon framing. With modern power saws and pre-cut studs this is no longer an issue. Which brings us to the still existing down sides of balloon framing. 1) Fire protection. [Easily fixed] 2) Finding an areas that are large enough to build your 17’ tall walls or even taller on the gables. 3) Raising the weight of your tall sheeted walls. 4) Bracing a tall wall without the second floor installed. 5) Not a big deal but still... your floor joists are no longer a top your studs leaving you with 13” rather than 14.5”. I only mention this for your HVAC installation. Standard ductwork sizes will not work. 6) You have eliminated your backing at your first floor top plate and second floor base plate this backing is a huge asset to stop your drywall from bowing and making taping easier.
I think you're right. I only had to picture myself top plating a 20' tall wall to come to the conclusion that balloon framing would add dramatically to the labor costs of framing a house.
Yeah- the biggest con it seemed was the weight of these walls. Probably somewhere around 38' long, 2x6 with 1/2 ply on the outside. Even with me and my three other guys, thats a lot of weight to get up and plumb.
Balloon framing was used to minimize cutting when everything was cut by hand.
Not true. You make it sound like it was an alternative to platform framing, which hadn't yet been developed.
Remember balloon framing was introduced when water-powered saw mills and machine-made nails made it possible to build much more cheaply than the traditional timber frame. Replacing hand-mortised timbers with small, repetitive members was the innovation which saved time and money.
Which brings us to the still existing down sides of balloon framing. 1) Fire protection. [Easily fixed] A non-issue with cellulose or install blocking.
2) Finding an areas that are large enough to build your 17’ tall walls or even taller on the gables. The OP needs 3' knee walls - that's a perhaps 12' tall wall, and easily managed. The gable walls can be stacked or built in place to rafters.
3) Raising the weight of your tall sheeted walls. Traditionally, balloon-framed walls are braced with let-in 1x4. Steel T-bracing is the modern equivalent. And they are traditionally sheathed after erection, but can certainly be done pre-sheathed.
4) Bracing a tall wall without the second floor installed. A non-issue for a 12' wall.
5) Not a big deal but still... your floor joists are no longer a top your studs leaving you with 13” rather than 14.5”. I only mention this for your HVAC installation. Standard ductwork sizes will not work. 10" or 12" rectangular ducts will fit fine.
6) You have eliminated your backing at your first floor top plate and second floor base plate this backing is a huge asset to stop your drywall from bowing and making taping easier. Backing is uncessary behind baseboard trim, and at the top of the wall is a let-in 1x4 ledger which offers more backing than a double top plate.
Balloon-framing isn't any more difficult than platform framing, once you've done it once or twice, and makes good sense for 1½ storey walls, as it offers far better out-thrust resistance than a kneewall and can make running mechanicals easier between floors.
Riversong HouseWright
Design * * Build * * Renovate * * ConsultSolar & Super-Insulated Healthy Homes
I probably did not phrase that correctly. I was not implying that balloon framing was a better alternative just that platform framing was inconceivable to cut everything by hand. 1) I noted that fire stopping was an Easy fix. 2) The first sentence of my post was: This is a general response to balloon framing, not all of the following will hold true in your particular case. 3) No matter how you cut it you either have a very heavy wall to raise or you have to sheet it after standing. Both of these are easier with platform framing. 4) Again: The first sentence of my post was: This is a general response to balloon framing, not all of the following will hold true in your particular case. 5) I preceded the comment about HVAC with: Not a big deal but still... I may have worded that wrong but I was talking about full size ductwork and return air cavities. They are smaller then standard. 6) Again: The first sentence of my post was: This is a general response to balloon framing, not all of the following will hold true in your particular case.http://www.multichambernailgun.com/b2/
I was not implying that balloon framing was a better alternative just that platform framing was inconceivable to cut everything by hand.
You're still missing the historical development of framing techniques.
Balloon framing was developed in the US in 1833 as a simplification over timber framing. I don't believe platform framing was used until WWII.
Balloon framing wasn't used to reduce the amount of cutting of studs. It was used to eliminate the need for skilled craftsmen to fabricate mortise and tenon joinery, to make building faster and cheaper.
Much later, an even faster and cheaper method - platform framing - was developed.
And I read what you posted. I expanded on some points and explained that most of your critique was invalid and sounded like it was coming from someone with no experience in balloon framing.
Riversong HouseWright
Design * * Build * * Renovate * * ConsultSolar & Super-Insulated Healthy Homes
My 1929 house has platform framing, but there is no bottom plate, the studs on floor n+1 rest on the top plate of floor n. Brick & mortar fire-blocking at the base of each stud bay (I've heard that was a thing with the original BI).
With traditional balloon framing there was no floor on which to build your walls. The walls were built stick by stick, then the floor joists were added . see riversongs post for a diagram.
The advantage to platform framing is just that, having a "platform" on which you can build your walls complete before raising them rather than stick by stick.
There are situations where it makes more sense to balloon frame certain walls in combination with platform framing methods, for example frame your floor the platform way, then balloon frame a wall on top of that, but I would not describe that hybrid method as "balloon framing"
The OP had a perfect situation for balloon framing in combo with platform.
Just my opinion
With traditional balloon framing ... The walls were built stick by stick
I doubt that was true, since there was typically a let-in ledger for the next ceiling or floor which ties the studs together and maintains the spacing. It's certainly not the way I do balloon framing.
The OP had a perfect situation for balloon framing in combo with platform.
That's what I suggested above.
Here's a hybrid platform/balloon frame on my last house, showing the ceiling joists extending out on the let-in ledger to become soffit framing, and the upper beveled let-in ledger for the rafters (no birdsmouth needed):
View Image
Riversong HouseWright
Design * * Build * * Renovate * * ConsultSolar & Super-Insulated Healthy Homes
Edited 3/15/2008 9:46 pm ET by Riversong
Just because I love history: http://www.hereandthere.org/oldhouse/balloon-framing.htm Also fun to google up "history of balloon framing" and look at some of the links to the old farm journals that have step by step instructions for doing it as published 1861.
They can't get your Goat if you don't tell them where it is hidden.
Cool article. Its fascinating to see how construction has changed over the years. Seems like every advance has been made to reduce labor costs, and every advance was probably derided as cheap junk. Can you imagine what an old craftsman who was used to joining wood with mortise and tenon joints thought of nailing a stud with factory produced nails? Or what a plasterer thought of sheetrock? Although we might sneer at new faster cheaper methods ourselves, it is an economic force that has been upon us for a long time. Once only the rich could afford real houses--now we all live in them.
Yep, I own a copy of a 1910's Series on architecture and building. "Radford Cyclopedia of Construction". Even then the author derides balloon framing construction as being the stuff of unskilled labor! The earliest reference to platform framing I have seen places it in the 1920's and claims it got started as a result of the need to use shorter pieces of lumber. I suspect that shipping of materials and ease of construction may well have played a large role in it's rapid spread. One of the coinciding factors in the industry in the 1820-30's was the spread of the circular saw blade in saw mills.
It made the return on labor for smaller pieces of lumber worth while to the mill owners so balloon framing became cheaper from that standpoint as well.
In one of the links containing an description of the process the author describes the ledger as being commonly placed on the outside of the studs and each stud being erected separately with notches either being precut or cut after the studs are stood. Article describes " A Man and a Boy" as being able to erect the frame of the house one stick at a time. I owned and lived in a "Plank House" that used the same technique but used 1 x 12 planks instead of studs for the frame. Ledgers were nailed to the planks for the joists and rafters. Exterior walls were all of 1" thick, cedar shingle outside, wall paper inside.
That place stood for 70 years , intentionally burned down by the next owner to make way for a doublewide mobile. That one would have been hard to "dense pack " ;-)
They can't get your Goat if you don't tell them where it is hidden.
I owned and lived in a "Plank House" that used the same technique but used 1 x 12 planks instead of studs for the frame.
I had to remove and replace a wall that was plank-on-plank construction (no frame), orginally an attached carriage house on an old farmhouse, but which had been turned into a dining hall, had two big holes cut into it for picture windows, and then had a second floor of bedrooms built on top of it (apparently no one bothered to check for load bearing). The sill was rotting and the whole thing was sinking.
You can see the settling of the nearest picture window sill. The thermopane glass panels were set directly on the sills, and when I removed them they had compressed 3/8" grooves into the sills - the glass was load-bearing and hadn't lost its seals (I re-used them in the new wall).
View Image
View Image
Riversong HouseWright
Design * * Build * * Renovate * * ConsultSolar & Super-Insulated Healthy Homes
Edited 3/16/2008 1:33 pm ET by Riversong
Just curious-from the second photo, looks like you have jacks of some kind attached to the bottom of the supports-are they purpose built jacks, made for this use? Maybe you could post a photo of them? Thanks
looks like you have jacks of some kind attached to the bottom of the supports
Yes, they're not just support posts, they're jack posts to lift the building off the sill.
I used antique screw jacks I had collected from yard sales and flea markets.
Riversong HouseWright
Design * * Build * * Renovate * * ConsultSolar & Super-Insulated Healthy Homes
I thought they were probably old.....
Did you modify them to attach to the kickers?......I use bottle jacks, which are fine for straight up and down, but even then I think "one of these days" I'll make a base plate, perhaps just a piece of flat steel with a pipe circle tacked to the bottom, couple of holes to nail the plate to the post, to help keep everything lined up....
No modifications required. They stay in place nicely on wood base.
I also use the big cast iron house jacks.
Riversong HouseWright
Design * * Build * * Renovate * * ConsultSolar & Super-Insulated Healthy Homes
In parts of Atlantic Canada, those "plank houses" are refered to as "full-studded construction". In the nineteenth century, they used 5/4" or 6/4" boards of random widths for a continuous exterior wall. Usually, a 1/2" spline connected or aligned the boards. Clapboard was applied to the exterior and generally wallpaper finished off the interior.
Regarding balloon framing, have you ever found sheething applied to the interior? On our 1880-era balloon-framed home, 1" board sheething is applied to the interior followed by 1" of lath and plaster. On the exterior, the clapboard is nailed directly to the studs. There are a couple of other homes in our neighborhood which are constructed the same way. I suspect that, at the end of the nineteenth century, the jury was still out about putting the sheething on the interior or exterior.
Chip
Edited 3/16/2008 2:42 pm ET by ChipTam
Argh! I had a house like that. What a pain for adding outlets.Not in Atlantic Canada, though. And brick exterior.
Edited 3/16/2008 2:36 pm ET by Biff_Loman
Actually yes I have. In the Radfords Cyplopedia it discussed this very issue. Seems that it was a recommended practice by some . The thinking was that putting the sheathing to the inside would allow air to the backside of the siding and allow it to dry out as opposed to having rot form between siding and sheathing if/when water got past the fished siding. Added features were nailing for inside trims, cost savings because the inside of the walls didn't need a second sheathing applied under the wall paper. Goes to show that building science was being discussed 100 years ago as well.
They can't get your Goat if you don't tell them where it is hidden.
The thinking was that putting the sheathing to the inside would allow air to the backside of the siding and allow it to dry out
The first "rain screen".
Riversong HouseWright
Design * * Build * * Renovate * * ConsultSolar & Super-Insulated Healthy Homes
That photo of the open wall with the interior lit up is the clincher for me on my project. Worth a thousand words, as they say.
One last Q: is the ledger bolted into the rim?
thanks,
k
One last Q: is the ledger bolted into the rim?
In this case, yes it's lagged to the rim because I needed to remove the entire wall.
In your case, I might lag it into the studs near the tops of the wall because you want to lift the wall and not risk separating it from the second deck. But the ledger would have to be very close to the tops of the studs so you don't kick the wall inward with the jacks at an angle.
Riversong HouseWright
Design * * Build * * Renovate * * ConsultSolar & Super-Insulated Healthy Homes
I couldn't agree more, Marson.
Way cool, Riversong. The other day, I was chiseling away at a proud stud in order to install a culture marble shower base, and it got me thinking about jointing methods in framing. Now we have routers that would leave the old-timers in the dust, but we also have air nailers and joist hangers. . . (Ha, I'm not a framer, so don't think that I actually use these things on a regular basis.)
Edited 3/16/2008 12:28 pm ET by Biff_Loman
Having read all the posts up to this point, I will just make one observation.
I was asked (told) to balloon-frame a gable wall on a cathedral-ceiling area. The company I was working for had some issues with the inspector, and they wanted to try the balloon method to see if it would be accepted.
The inspector did not accept the gable and said it would have to be
a) balloon-framed in 2 X 6s, or
b) balloon-framed on 8" centers with 2 X 4s.
I elected to add the extra 2 X 4s, although it added an extra day of work for me. I was building the house alone. I did not really have a choice.
I got no extra compensation from the company.
That was the last time I worked for them.
I don't understand his problem.
Should have made him show you how it didn't meet code.
You don't argue with the building inspector. Kansas is still in the middle ages.
Are you sure it wasn't April 1st?
View Image
Riversong HouseWright
Design * * Build * * Renovate * * ConsultSolar & Super-Insulated Healthy Homes