I am about to install rebar in a small foundation for a porch enclosure. There will be four horizontal lengths of rebar in the foundation. The trench takes a 90 degree turn which means the rebar takes a turn as well. Is it a much better practice to bend a long length of rebar than it is to splice a factory pre-bent piece on to the straight runs? Are there advantages or disadvantages to either method? Thanks!
Discussion Forum
Discussion Forum
Up Next
Video Shorts
Featured Story
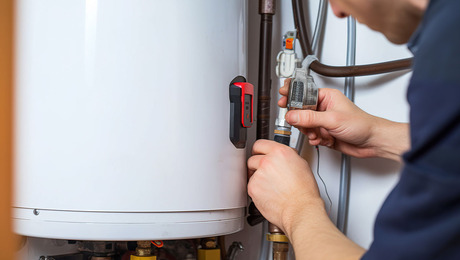
Learn more about the benefits and compliance details for the DOE's new water heater energy-efficiency standards.
Featured Video
How to Install Exterior Window TrimHighlights
"I have learned so much thanks to the searchable articles on the FHB website. I can confidently say that I expect to be a life-long subscriber." - M.K.
Replies
I like to bend my own, less pieces to play with. Alot easier to handle when the mud is flowing.
I take the ball out of my bumper and slide the bar in and bend away.
Woods favorite carpenter
I rent a rebar cutter and it also bends too, only about 20 bucks a day
Carpentry and remodeling
Vic Vardamis
Bangor Me
Bending your own should be fine unless you are using real thick bar that you cant bend by hand. Just do not put any heat on the bar, doing this will make the bar pretty much useless. If you want to buy 90's that's fine too as long as you tie them tight there is really no difference between the two as far as strength.
There will be four horizontal lengths of rebar in the foundation.
I assume you mean two pairs of rebar, one low and one high?
It doesn't matter if you bend or use prebent corners, but it's important that you lap and tie all splices 30x the rebar diameter (e.g. 15" laps for 1/2" bar), and that you cross the corners (see graphic) to prevent inside corner tearout.
View Image
Solar & Super-Insulated Healthy Homes
Edited 1/28/2008 11:36 pm ET by Riversong
We use a slightly different detail than your lower pic. Inside bar on leg#1 becomes the outside bar on #2. Outside bar on leg #1 becomes the inside bar on #2. Bend a 60" piece into a 90 and tie it outside to outside around the corner.
Riversong,Yes, there are two pairs of horizontal rebar, all #4. They all run in one vertical plane. The pair of rebar at the bottom of the trench are placed very close to one another, the pair at the top of the trench are spaced further apart. There are vertical pieces, also #4, placed 16" O.C. At the risk of being dense, could I ask you to really define what you mean by 'crossing the corners'? If I use pre-bent corners, I was told that there is a disadvantage because the splices will line up with one another from top to bottom, and this weakens things. When splicing rebar, is it better (or a myth) to stagger splices, like you would if you were framing top plates? And, out of sheer curiosity -- is there any gain or loss in strength depending on the sharpness of the radius of the corner?
Why is the bottom pair spaced closely? If you have a bar near both the inside face and outside face of the wall, you protect against pressure from either side. Typically, the bar would be placed about 1/4 and 3/4 through the width of the wall.
Laps ideally should be staggered by about 4', and at corners the inside bar should become the outside and vice versa (as in the graphic I posted above) and the radius shoud be tight enough to keep the bar at the same distance from each face of the wall.
But, with the joints properly lapped (minimum 30x bar diameter) and tied with tie-wire, not staggering the joints is not a major issue as the embedment strength of the rebar in concrete should be more than enough to maintain the continuity of the reinforcement.
Riversong HouseWright
Design * * Build * * Renovate * * ConsultSolar & Super-Insulated Healthy Homes
Thanks for the response... I think I understand now. As far as the close spacing of the bottom pair of bars... I really don't know. It was designed by an engineer... When I met with him, I asked just how far apart they should be since it wasn't specifically called out on the plan. At first he said to bundle them, then he changed his mind a bit and said to leave enough space between the bars to allow the gravel, so that's still pretty close. Again, thanks.
With #4 bar and 3/4" aggregate. Your bottom bars should be 2" apart to "allow the gravel". The standard is 20 times the bar diameter, but extra overlap doesn't hurt. 10" on #4 bar doesn't quite look like enough.You can bend #4 with your hands. No need to get a bender. Anything bigger than #4 you need a bender. Just step on the bar a couple inches back from where you want the bend and pull up. You will be amazed at how easily it bends. The only other recommendation I'd add to the above corner details, which are great, is to be sure to actually bend the bar around the corner. I have seen many installations where they just cross the bars in corners and tie them off. It sounds like you already have this covered, just sayin' for the peanut gallery. It's seems trivial and I've had a few "concrete guys" tell me it doesn't matter. Without getting into it in detail, it is important.
Here the standard is 15 times the diameter. I should check that again though. But I always end up past that because there is no point in cutting bar when you don't have to. :-)
30 bar diameters for laps ,and you can bend #4 easily as long as you are dealing with grade 40 bar. Move up to grade 60 and it gets a bit tougher. No bender? If one is going to do corner bars as opposed to long pieces it is easy to use two 3' pieces of 3/4 black iron pipe to make handles for bending. slip them on from opposite ends and stand on one while pulling the other to make the required bend. That will give you a nice tight bend. Renting cutter benders is cheap though IMO.
They can't get your Goat if you don't tell them where it is hidden.
"Move up to grade 60 and it gets a bit tougher."I thought about that, but didn't think 60 would be spec'd for his application. I have never once seen 60 spec'd for res. Although it does seem like a lot of steel. Laps vary. Non engineered rule of thumb for me is 20x. But an engineered foundation should have the lap spec'd. (or welds, or mech. splices. And cheap rebar benders aren't worth what you pay for them.
I still have the same bender breaker that I had 25 years ago. Cost me maybe $100.00 when I bought it. It has cut and bent miles and miles of bar. Just the old hand operated standby unit.
They can't get your Goat if you don't tell them where it is hidden.
You use it for bending #4 40 ?really?
Yes, bending and cutting #4 and #5 schd. 40. It will do schd. 60 but tough on it and the guy doing the work to muscle it. #5 is a job that takes a bigger guy than I am any more through. It is just a simple top cut , lever operated bender/cutter.Paid for itself many years ago.
They can't get your Goat if you don't tell them where it is hidden.
A non-contact splice is also acceptable. It is how bar is spliced in ICF work.
Overlap 40x the diameter with the bars separated by about their own diameter is quite enough.
Ron
I have never once seen 60 spec'd for res.
Hmmm... it's the only rebar I've ever had specified for my houses. #4 and #5 are easy, we use a 4' piece of pipe for the simple bends. Getting up to #7 (yup, still residential) gets interesting and I generally use a tractor loader. Love hydraulics.
My hub cutter/bender is good to #5 grade 60, but it's a struggle. PAHS Designer/Builder- Bury it!
I got a machine at work that test rebar, its pulls it apart, sound like a shotgun when it pops. 60 is all they sell here.two ways to screw up concrete 1) concrete driver 2) concrete finisher
Learn something new everyday. I wonder why they spec the 60? Especially in Virginia.
anyone?
Now that BB mentions it, I don't remember seeing Grade 40 offered. Ungraded is what the home centers generally sell here. It's some strange stuff, what goes into many homes.
I'd love to play with that toy he mentioned.
Take a peek at a Grade 60 spec:PAHS Designer/Builder- Bury it!
I don't know what they sell at the home centers. Guess I always assumed it was 40. I get most bar form a concrete supply yard. He doesn't even carry 60. But he serves almost 100% residential and he wouldn't be selling bar for commercial projects anyway. Now this is reminding me of something the instructor mentioned at last years code update cont ed. But I can't remember what new code provision was requiring 60. No one's changed any specs so maybe that portion didn't go through. It would have been something new in the 2006 IRC from 2000
But he serves almost 100% residential and he wouldn't be selling bar for commercial projects anyway.
That drawing was for a residence, mine.
Not that it should matter to the supplier. My supplier sells to whomever pays the tab. The Grade 60 rebar there is usually cheaper than ungraded at the home center. And I'm not restricted to #3 and #4.
If your place has no call for Grade 60, they'll not stock it.
Take a look next time you're in a home center. I'd be surprised if you saw a grade marking.PAHS Designer/Builder- Bury it!
Yeah, I got you Tom. I'm just sayin' around here if it's going in your house, it's probably 40.
If I need anything bigger than a 5, or a large quantity it comes from a rebar supplier. But the concrete supplier is cheaper and faster for average quantities. And he's a nice guy so I like to give him business. As far as the grade marking I don't think there is any required on 40. only on 60 with the extra line and probably on 75 with two lines I think. I can't remember.
Edited 1/29/2008 11:11 pm ET by redeyedfly
all the rebar in this area is controlled by the rebar supplier, they stop making anything under 60. all the box stores buy from him and resell due to freight price, so anything under 60 is hard to find, the average local home builder doesnt know what a 60 is anywaythat 60,000 tensil strength.two ways to screw up concrete 1) concrete driver 2) concrete finisher
this machine was made in 1932, its a cadallic of a machine, just purrs no strain. its old school machinery.two ways to screw up concrete 1) concrete driver 2) concrete finisher
Here in Etlanner at Home of the Pot, I've seen the most motley collection of rebar imaginable. Some is 30, some is 60. What a shock when I latched onto my first hunk of 60 & tried to bend it w/ a hand bender. Got the crappiest radius imaginable. I found some of it was so brittle that it snapped before the bends were complete. My problems were all solved after I lost my bender, bought a second one & found the first. Two benders, placed facing one another made neat, small radius bends in the 60 w/o causing it to snap. Had my wife hold the one on the ground & I applied the bending force. Never fell A$$ over teakettle once.DonDon Reinhard
The Glass Masterworks
"If it scratches, I etch it!"
You make good point. Grade 60 bar is more brittle than 40 and will break readily if re bent.
They can't get your Goat if you don't tell them where it is hidden.
because the splices will line up with one another from top to bottom, and this weakens things.BSdoesnt matter has long as you have the correct length of splice, but using prebent corners you are wasting 30 inches per bar. steel aint cheap.I use the trailer hitch hole on my truck for bending barstwo ways to screw up concrete 1) concrete driver 2) concrete finisher
Edited 1/29/2008 6:42 pm by brownbagg
#4 you can bend by putting your foot on it and using your muskels... If you want a crisper corner, use a length of steel pipe slid over the bar. Even nicer corners, 2 pieces of pipe. This is assuming that you aren't a 90# beauty queen. If that's the case, I'll be right over... ;-)
Matt,LOL. Well, I weigh in more than 90 lbs. but I would probably cut a more credible figure if I were behind a desk. Nonetheless, what I lack in brawn, I try to make up by being resourceful. If there's a wheel within a 100 mile radius, I will find it and put it to use. After reading all these posts, I've decided to try the 'two pipe' method of bending. Thanks!
Matt,
I use the two-pipe method, too. I got the idea from Jim Blogget's article on pouring a foundation for a small addition. It works great. Thanks Jim, if you're reading this.
Ya gotta get some guns. brute stength.
"It is like hitting yourself in the head with a hammer: it feels so good when you stop"
If you are willing to bend the rebar to an accurate angle then use a rebar bender. It will make your work easier and faster.
We also got buckel