Cellulose or ‘glas – best choice blown?
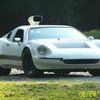
I’ve got clients in an old house, early in a massive restoration, agonizing over insulating the walls (not a job for me). The house is a late 19th century frame 2-story, 4K sq. ft., original clapboard, original windows, near Atlanta. The exterior is some years away from a thorough “tightening up” and painting, and probably 15-20 years since the last time – i.e., it’s probably leaky in a heavy rain.
They want to blow in something in the exterior walls, and not gut the inside plaster. They have been getting conflicting advice from insulation subs. I know infiltration is really driving the train, but I wondered what advice you guys might have over the relative merits of blown cellulose vs blown chopped fiberglas (or 78,000 cans of Great Stuff) in this application.
Thanks
Forrest McCanless
Replies
I would think that the cells would be the first choice . the 97000 cans of great stuf would be a problem . you would have to drill more than 48,ooo holes because the foam puffs up and stops flowing before it would reach the bottom of the cavity.
I'd say cells too, but are you saying you think water is being blown into the stud bays?
Doesn't sound a good candidate for any insulation that is going to get wet and then stay wet in there.
Joe H
"or 78,000 cans of Great Stuff"
Have they SERIOUSLY looked at using foam.
No, not truckloads of Greatstuff.
But rather companies that do use low expansion foam sepecifically for insulatiing existing buildigns.
Dense pack cells is good stuff, but it has to be dry first for any insulation.
Atlanta is a tough climate to deal with.
Thanks for the input - given the undoubted moisture issue, does anyone have experience with the foamed-in-place insulation (injected through holes in the sheathing)? Will it push loose plaster sections?
I recall that when I bought my big old house (very little done since 1886), GA Power came down with a thermal camera to do an "energy audit". Given that I wanted to restore the 30-40 original double-hungs, weights and all, and no ugly storms, the guy said that infiltration losses, and conduction through the large weight pockets would outweigh any wall insulation benefits.
He recommended skipping the wall insulation, seal and insulate the 2nd floor ceiling plane as well as possible, VB on the ground in the crawl, and 7" batts under the floor. (I also believe in sealed, one-duct conditioned crawls) Spend the most on efficient, zoned HVAC.
It's been 13 years, and the solution worked out. The house (about 5100 sq. ft.) has two condensing gas furnaces downstairs, the big one with four damper-controlled zones. Upstairs is a 4-ton heatpump. With all the thermostats programmed, I usually spend less winter or summer than my father down the street with a 2600 sq.ft. 60s brick ranch with new windows. And my windows look great!
I think my client should do the same. . .
FMcC
Or you could fix the moisture problem. Even with foam, you do not want wet wall cavities. Insulation or none, seems that would be a good move.
It's true that sealing and insulating the attic plane has the best cost/benefit ratio. Certainly the place to start.
Personnally I'd only consider filling the walls cavities with insulation if:
1) the wiring in the outside walls is not knob & tube and/or
2) I could avoid covering such existing wiring with insulation.
The potential problem - heat build up in K&T wiring.
Rookie
Forrest,
Any wet insulation is really no insulation (with the exception of foam) both fiberglas and celluloise lose all R value when wet while getting foam wet doesn't affect it's "R" at all. There are companies who do sprayed in foam in existing walls. My only requirement would be that a thermal photo is taken after the foam is sprayed in but before the bill is paid..
In addition air movement thru fiberglas is pretty well documented (go look at your furnace filter for an example) thus unless the walls are well sealed up the fiberglas will achieve nothing.. celluliose when it gets damp has been known to cause rot so I'd be very carefull about specing celluliose..
If water can get in the wall and you add insulation to the cavity, the drying potential will be greatly reduced and the wood will stay wet for a long time. It may never dry. Homes have been lost by insulating in the absence of an effective drainage plane. Foam is just as dangerous as other insulations. The drying potential is a function of air movement and heat movement. Insulation of any type will inhibit both.
Fix the water infiltration or limit the wall improvements to interior air tightening. The attic insulation and crawl air sealing will help a lot.
Any prescriptive measures undertaken on the basis of advice recieved here in the absence of a thorough and comprehensive energy plan "can" be dangerous. An example is if the walls are balloon framed and the air flow through the wall is the factor that makes it possible to survive a leaky wall that regularly gets wet and dries back out. It is impossible to diagnose all the possibilities from here so you may get many bum steers.