*
Last fall I had a driveway replaced. Within 6 months tiny hairline cracks started to appear. Now they are a bit more noticable. The 10’x10′ section of the drive are effectively cracked down the middle in BOTH directions (cutting them in 1/4 pieces). Five out of the six sections are cracked.
The contractor did a really nice looking job. He first laid down the brick boarders (along the edge and across the middle), effectively splitting the drive in 10’x10′ sections. He then laid rebar between the bricks (before grouting them in). After grouting them in, he poured the drive using a high strength (3400 psi?)concrete, and a pump mix (pea gravel), as he needed to pour a slab around the rear of the property. I recall the weather for the next few days was hot. I watered it down several times a day, for the next week or so to keep it cool.
Needless to say I am not happy about the cracks. I realize that I’m probably going to have to learn to live with them. I’d like to learn from this experience (and perhaps make some suggestions to the contractor, on how he can prevent others from suffering my fate). Any thoughts on what went wrong would be most appreciated.
Discussion Forum
Discussion Forum
Up Next
Video Shorts
Featured Story
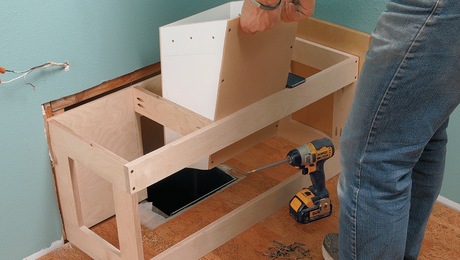
Learn how to plan, fabricate, and install a chute to conveniently send your dirty clothes from an upstairs bathroom or hallway to your laundry room below.
Featured Video
SawStop's Portable Tablesaw is Bigger and Better Than BeforeHighlights
"I have learned so much thanks to the searchable articles on the FHB website. I can confidently say that I expect to be a life-long subscriber." - M.K.
Replies
*
A buddy of mine once told me: "there's only 2 things you need to know about concrete is 1) it gets hard and 2) it is gonna crack"!
Seriously though, to properly cure concrete it is necessary to prevent the water from evaporating too quickly, especially in hot weather, which is what we refer to as the curing process. Of nearly equal importance is to insure that the concrete cures at a constant rate: if you are gonna keep it wet, keep it wet for the whole first week (day and night). Curing compounds are available, but they can get a bit pricey - say $20 for enough to do 150 sq ft. - or maybe about $200 for a good sized driveway. I've used one called Cure & Seal
Any know of a "home remedy" type of curing compound? - commonly available and inexpensive material? Or, perhaps a less expensive type of curing compound?
*
The best and most effective thing to do in hot weather is to put your lawn sprinkler in the middle of the driveway and let it run just enough to keep the concrete wet while it's curing.
*
when anyone figures out a surefire way to stop concrete cracking let me know. I will patent it and split the profits. I have poured slabs in this 90 deg + heat and turned on the sprinklers for 3-4 days immediately when the finisher leaves. Still numerous hairline cracks. I researched a little and found some information to indicate the cracks actually occur while the concrete is drying(but still in a fluid state) due to fast evaporation of water. The best luck i have had to mimimize cracking is slabs poured in cool weather with a lot of water on them. Even these slabs had some fine cracks in them
*
Brian, I don't think there's one simple answer to the problems of pouring concrete in very hot weather but here are a few suggestions:
1) Pour as early in the morning as possible and try and wait for a cloudy day if possible. Low humidity, wind and sun are the real culprits.
2) Do smaller sections at a time if it's hot
3) Soak the area to be poured and put plastic down to prevent as much water as possible from leaving the concrete out the bottom of the slab.
4) Don't over tool the surface. Screed it and darby it as soon as possible after placing it. Then broom it immediately.
5) DO NOT add too much water to the mix. This is tempting in hot weather because the stiffer concrete wants to set up so fast.
6) Moisten the surface ASAP and keep it that way for several days. ( Not just once in a while )
7) Use fibermesh concrete. It is very effective and allows you to finish the surface much quicker.
8) Cut control joints no more than 10' apart if possible.
9) If you can't water it, get the best quality D.O.T. Grade sealer that you can by and apply it immediately after brooming.
*
There are two kinds of concrete "cracked and concrete thats gona crack". In MN it expands and cotracts with the seasons. It also gets moved by frost heaves. (exterior that is). Knowing this we cut the slab into equall sections with a diamond blade in a cutsaw. The depth of the cut is about 1/3 the thickness of the slab. It makes a controlled crack. On my driveway I filled the cut with 1/4 inch backer rod (a foam type rope ) and a Bead of urathane caulk to prevent weeds from growing and water from seeping through.
*Hi Fellows,A tip from one of the old timers on this board,Use cheap rolls of burlap, spread it over the concrete and then use the sprinkler for a few days.Gabe
*Same technique here, Gabe.
*
My contractor recently had my basement slab and garage slab poured. Because of the hot weather (if you can believe we actually get hot weather here) he put the Kure and Seal product on it. The basement site had plastic put down after compacting, plus wire mesh. It also had a number of footings. The garage had no plastic but lots of rebar. The basement floor has a number of cracks in it and the garage floor has none. My contractor tells me that the plastic tends to cause cracking--and footings make the curing process a little trickier. I'm tempted to believe him because the garage floor looks great with no cracks at all (just some dodo bird's footprints). The basement probably got a little hotter during curing. We did not use any water during the curing on either slab. If you get a concrete sealer, get a decent one like the Kure and Seal--I tried some Home Depot stuff once earlier and it was a really pathetic product.
*Since I posted the message I have done a bit of an informal survey of newer looking driveways in my neighborhood (So California area) and I can say that cracking is not the norm. There are examples of larger slabs (well in excess of 10') without control joints that are cracked (no surprise), and older driveways that have something lifting them up. My neighbor for instance, had his driveway done 6-8 years ago...not a crack to be found. The contractor is going to come by and have a look some time this week...stay tuned. From your postings I now suspect that the cure was too fast.As an added note: they used lots of rebar, no plastic underneath, they wet the area before pouring and the mix was on the dry side.
*
Ok old guy....:)
How about burlap wet then straw 4 to 6 inches then wet then plastic sealed in dirt at the edges. I'm not that old and made a lot of overtime staying late to keep slabs wet during the summer months
I'don't agree about the cracking in slabs. If you want concrete to stay and not crack then you have to spend the time and money to place it right. Most times concrete will crack because of poor curing, impropor placement of steel.(we're not talking fiber or wire mash here) or no compaction of site or use of grade beams for slabs. Most guy's think that by running the "loader over the site a few times will "compact" everthing just right...... Wrong, compaction is done in lifts that a soil enginer will well you about after he test the soil you're going to use. I've said it before and I'll say it again most people who work and place concrete in residental aren't uip to speed on what got to be done.
*
Bill, I agree with you. If you know what you're doing there is absolutely no reason to have concrete crack in any place except a control joint. And there is no reason to have random surface cracking either.
Anyone who says otherwise is making excuses for a poor job. I live in an area where it is very hot in the summer and very cold in the winter. We don't have ANY (zero) problems with random cracking of slabs.
Many State concrete supplier associations conduct training seminars on how to use their products properly. We attend them regularly and I learn something new each time. I'd suggest anybody in this business check on this in their area.
*If you cover the concrete with plastic before it sets up and keep the edges tight it will continue to stay moist and cure for up to a month.The longer it cures the stronger it gets.I sure agree with the guy about compaction. Like to use crushed, concrete a( 1/2"or smaller for my sub-base. Some of you might benefit from getting copies of CONCRETE CONSTRUCTION, HECK GO TO THE World of Concrete convention, usually in January, but is Febr next year.
*
I always wanted to try the cover the concrete with poly thing but was always afraid that it would leave "tracks" on the slab. So how do you tell when it's hard enough to cover with poly, etc?
Also, can you please give some more specifics about the _Concrete Construction_ book? I looked around and could not find it.
*Spraying the ground without first putting plastic down is a waste of time; the water evaporates into the soil and the concrete moisture also evaporates into the soil. Should have used plastic. I also agree that ground compaction is the key; along with the use of expansion material.Scott, did the contractor use any kind of expansion material between the brick and the concrete? I would have used 1/2 inch Dow Chemical brand foam board against the brick. After the concrete sets up, you can always tear out about 1/2 inch of the foam board's top edge with a knife and then either use a grout or a colored silicone sealant to fill in that top void. The brick and concrete might expand and contract at different temperatures and this expansion material would help "cushion" this pressure.By the way, a friend of mind used Thompson's Water Seal on a concrete sidewalk he had just poured. The walk had been screeded off and most of the bleed water had evaporated before he sprayed this on using a garden pump sprayer. He saturated that walk real good and walked away. Owner put water on the walk one or two times total a couple of days later. That was 17 years ago. This is the first year that I have noticed a couple of cracks; just hairlines, not too bad.Maybe Thompson's Water Seal is the answer? Anybody else use it for this?Davo.....Where the winters are bad here in Pa. and the road salt KILLS our concrete.
*
Matt, CONCRETE CONSTRUCTION is a trade magazine
put out by The Aberdeen Group 1800-323-3550 also try http://www.supernetwork.net, you have to register, but if you are interested enough it is only a little effort. Should be able to get back copies from your local ready mix supplier. Mine pays my subscription. As for plastic, either clear or black leaves stains, never can remeber which, blast all, when to put it on? certainly before the concrete is dried out, should be OK if you can step on it without making an imprint. good luck. have fun.
*
would someone please define a "crack". I have never seen a driveway, slab or other concrete pour without at least a "hairline crack". This is what I am speaking of. Cracks that open to the point where dust can be swept into them is another story. This would indicate poor compaction, settlement or fast curing. I have seen many a concrete slab, both commercial and residential, and all have some sort of faint hairline crack in them. In fact, in my area, larger cracks are more common in commercial buildings. I agree that control joints can be placed in concrete but you still have a surface crack. It is just at a controlled point rather than at a semi-predictable random place. Also in residential work you have a lot of step downs for porches, carports, etc. which makes for a more difficult scenario. I have poured concrete, my own house in fact, over non-plastic soil where fill dirt was compacted and tested to 95% standard proctor. Then the pour was made on a cloudy, 60 degree max. day and cured with water, covered with visqueen for 5 days. The subgrade and forms were sprinkled with water prior to the pour. After a few weeks I had one or two faint hairline cracks. This is why we use rebar- to prevent the cracks from opening. You still have a crack though. I would like to come look at some of these "crackless" slabs. Also two other observations: 1) square pours, such as driveways, are less likely to show cracks due to no changes in direction 2) I beleive the addition of fly ash in lieu of cement causes a lot of the cracking and the quality of concrete is not what it used to be unless you step up to a 3500 psi mix
*
Brian, ALL concrete cracks as it cures. Thus the need for properly placed control joints. There are basically two types of cracking: Structural (thus the need for re-bar) and surface ( thus the benefits of fiber-mesh products). We pour under the most extremes of conditions and do not get either. If you are experiencing this, I suggest you pour thicker slabs, use at least 6 bag mix w/fiber, follow all recommended procedures and probably get a new concrete supplier. Curved slabs will always crack out from the tightest inside radius, so you have to cut joints appropriately. Other restrictions to shrinkage, such as being caught on a corner or something will also results in cracking. As I said before, do your homework and order good concrete and 99.9% of your troubles will disappear! We poured over 5000 yds of concrete last year and I could take you out to any site and you would not see what you are describing.
*
G.LaLonde:
When you say "6 bag mix", what does that translate to in terms of PSI? PSI is the common spec that we use here in Raleigh NC when ordering concrete.
Also, what type, how much, etc of plastisizers or other admixtures do you specify to make the concrete very workable so that the "crew" won't want to be adding a bunch of water to make their job easier? I'm thinking in terms of driveways, and sidewalks poured at temperatures between 60 and 80 degrees F.
TIA
*
Matt, " 6 bag mix " is the old 6- 94# bags of cement per yard of concrete. This is an easy formula for someone mixing his own concrete. It is commonly known now as 4000 p.s.i. concrete. The conditions you pour in are ideal for concrete. We use air entrainment, water reducers, plastisizers , and fiber for most of our summer pours. Check with your local supplier and have them explain the reason for using each of these. Quantities vary depending on a lot of different situations. Aggregate size is a big factor in how easy the mix works. They must also be careful that the aggregate is not too hot or wet when they mix. Go talk to them....if they're on top of things,they will tell you a lot. Also contact your State's concrete producers association and find out when or if they conduct training seminars.
*
G.LaLonde:
Conditions are not always that way here, but I'm planning on having *my* ~2500 sq ft driveway/walk poured in about 1.5 months. I got a sub that does a nice prep and finish job for $35 a yard, which I consider cheap. He does like to put the water in it though. I always order fiber, usually a 4" slump, but have never used over 3500 PSI, nor have I ever specified any other admixtures, partially because if conditions are adverse, I just wait for a nice day. On the other hand, if I can get the 'crete loose enough to start, my sub won't water it down so much.
*to keep finishers from adding water to the mix have the concrete pumped in. There is no reason to add water when pumping concrete. Uh Oh the pump may cost $1000 but at $10-15 a yard more for fibermesh and 4000psi concrete whos keeping count. If you can afford it fine. If not have a slab with a few fine hairline cracks like everyone else..
*
Brian, I'll mark you down as skeptical....I can tell you are much more concerned with the initial cost than the quality of the job. I don't know where you live, but I can tell you that any cracking in the surface of concrete in climates where you have severe winters, is the beginning of the end for your slab. Water will get in these cracks and freeze and your slabs will spall and deteriorate rapidly on the surface.
The point of using rich mix is not necessarily the psi rating , but the quality of the surface you get.
*
G la londe....i live in louisiana.....we are lucky to get a frost here what more freezing weather....if it snows if is a once a year occasion..yes i am concerned about quality....but to this day....in 33 years i have never seen a slab that did not have a surface crack......mine and others.....these cracks may be so faint as to not be open enough to even insert a micro organism in but they are visible to the naked eye if looked upon closely. Maybe we are all unsure of our definition of a crack. I call a crack anything you can see with your eye. Even if it is only a thousandth of an inch and measurable only with a feeler gauge it is still a crack. Please let me see your slab......i bet i can find one in it....Also winter weather is of no concern to a house that is covered with roof. How will water get into the cracks in your living room without a leak in the roof. Maybe on a driveway but our construction here makes us form porches, carports, etc. with drops in elevation of a monolithic pour. You cannot do this without some "cracking". Maybe up north yall pour a slab with expansion joints abutting a concrete wall but down here almost all of our pours are monlithic. Let me know what you think. Fighting off alligators....till then
*
I think you're safe.....From concrete problems, that is!!! You wouldn't get me near an alligator or a moccasin........How can you guys even work in that heat???? It's been 90+ up here for almost 3 weeks and we can barely work. You Cayjuns must be tough!!
*
G lalonde
It stays 90 plus here from may to september and the humidity just makes it worse. I probably couldnt handle working in one of your winters though. We go in at 6 am and work till it hurts. If the job is close by we sometimes stop at 11 and go back in late in afternoon. Lately though we have only been able to work 6 hr days due to the heat. Laying in the swamp with the gators.....
*
It sounds like the concrete is doing exactly what it should do. The slab is likely 4 inches thick. In a 4 inch slab, the internal stress are such that cracks appear every 5 to 6 feet. Your slab cracked in the middle of a 10' square, right on schedual. This is why sidewalks have crack control joints every 3 feet.
*
Scott, what was the concrete poured on. there should have been good base of sand 3 to 4 inches thick. if it was on top of expansive soil you may be in for a redo.
*i agree with norfleet......unless the cracks are open to the point objects can be inserted in them
*
Last fall I had a driveway replaced. Within 6 months tiny hairline cracks started to appear. Now they are a bit more noticable. The 10'x10' section of the drive are effectively cracked down the middle in BOTH directions (cutting them in 1/4 pieces). Five out of the six sections are cracked.
The contractor did a really nice looking job. He first laid down the brick boarders (along the edge and across the middle), effectively splitting the drive in 10'x10' sections. He then laid rebar between the bricks (before grouting them in). After grouting them in, he poured the drive using a high strength (3400 psi?)concrete, and a pump mix (pea gravel), as he needed to pour a slab around the rear of the property. I recall the weather for the next few days was hot. I watered it down several times a day, for the next week or so to keep it cool.
Needless to say I am not happy about the cracks. I realize that I'm probably going to have to learn to live with them. I'd like to learn from this experience (and perhaps make some suggestions to the contractor, on how he can prevent others from suffering my fate). Any thoughts on what went wrong would be most appreciated.