*
I am building a new deck with posts in the ground, not on sonotubes. My question is should concrete be place wet under posts and allowed to set before placing posts or set post first then concrete around them? Some guys in my area place 1/2 bag concrete dry then post and the rest of bag dry, is this common?
Discussion Forum
Discussion Forum
Up Next
Video Shorts
Featured Story
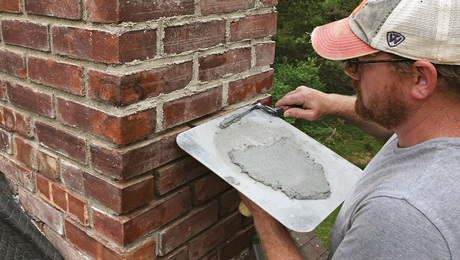
Old masonry may look tough, but the wrong mortar can destroy it—here's how to choose the right mix for lasting repairs.
Highlights
"I have learned so much thanks to the searchable articles on the FHB website. I can confidently say that I expect to be a life-long subscriber." - M.K.
Fine Homebuilding Magazine
- Home Group
- Antique Trader
- Arts & Crafts Homes
- Bank Note Reporter
- Cabin Life
- Cuisine at Home
- Fine Gardening
- Fine Woodworking
- Green Building Advisor
- Garden Gate
- Horticulture
- Keep Craft Alive
- Log Home Living
- Military Trader/Vehicles
- Numismatic News
- Numismaster
- Old Cars Weekly
- Old House Journal
- Period Homes
- Popular Woodworking
- Script
- ShopNotes
- Sports Collectors Digest
- Threads
- Timber Home Living
- Traditional Building
- Woodsmith
- World Coin News
- Writer's Digest
Replies
*
You should not be burying your posts. Even Pressure treated lumber WILL rot when buried. You can install them above ground as shown in the picture attached to this post. I just fill the hole 1/3 with water and pour in quickcrete to the top, no mixing needed.
Pete Draganic
View Image
*Sorry Pete, must disagree. Although that is an acceptable footing a post above a sonotube will rot as well. Would you suggest the same footing for a fence? We drop 2 shovels into the hole then the post and fill the hole half way. Fill the hole to grade with 3/8 or 3/4" crushed stone. To reduce rot we slope the soil away from the dwelling and cover with vapour barrier (6 mil), and a 2" layer of gravel atop the sheet. No more moisture problem. Keep the vapour barrier tight around the post. Again sonotube footings are an acceptable method but you may have to factor in some diagonal bracing to compensate for the pivot point in the footing. There are many acceptable methods but keep in mind a deck should last for 20 years.
*It is common to place the dry concrete in the hole first. I prefer to mix it first but see no problem with burying posts. Good pressure treated lumber lasts a long time, even underground. Sure it will rot eventually nothing lasts forever.
*
Petes diagram plus a post anchor attaching the post to the pier is typical here in NY.
*The method that I was taught was to keep the post off the concrete footing with a steel spacer. If the post rests directly on the concrete there is the (small) possibility of rot starting. Those rougish fungiis like to live where it is damp. By keeping the wood wet all of the time or dry there is the least chance of decay.Tom
*By the time those buried posts rot away, (assuming they are ground contact PT lumber) the decking boards will be long gone. And if rotting below grade is a problem, why do they permit treated wood foundations for houses in many areas?
*
First, If you read the warrantee tag attached to many brands of PT lumber, you will find that burying it voids the warrantee.
Secondly, in the case of fencing, burying the posts are a neccesary evil in order to keep it standing upright.
Third, Wood foundations are only in contact with soil on one side of the wood and are usually coated or protected from direct contact with that soil.
Fourth, 4x4 and larger posts do not get treated to the core. if you cut a 4x4 in half, you will notice the lack of treatment in the center area. burying this post will cause it to act as a wick which draws moisture from the ground and into it and with little or nearly no post to open air contact there is little opportunity for moisture to disipate therefore introducing an increased likelyhood for rot.
I figure that it's better to be safe than sorry. Also, it is far easier from a labor standpoint with my previously posted method and greatly reduces the chance of permanent errors in post placement or in post movement before the concrete sets.
Just giving advice...you don't have to take it.
Pete Draganic
*
No matter what we all decide is "right", the local inspector will decide how it gets built. My plan included concrete posts, Simpson supports, and everything I thought was right for all the reasons in Pete's post. The approved plans called for 48" deep minimum holes, 8" minimum concrete, then PT posts burried in dirt. Reasoning was that he didn't want concrete next to the wood because water gets in there, freezes, then cracks the concrete away from the wood, and the dirt provides lateral support (even though my deck was captured on 3 sides by ledger boards) lacking in the post/strongtie.
*
"simpson" manufactures an excellent product called and elevated post base specifically for this application. Keeps the post above the concrete, and has alittle fudge factor built in. Somewhat pricy if you've got alot of posts though.
*The local inspector will determine if you need the concrete or not and to what depth, no matter what you think or want (assuming you're permitted and inspected). The elevate post foot seems like good insurance. Simpson makes two types. One is pressed, galvanized steel. The other cast aluminum. The c.a. looked more substantial to me. In earthquake areas the inspector may also want the post anchored positively to the vertical rod, not just riding atop it and relying on gravity. I think there's a third design of foot that get cast into the concrete and then attached to the post to accomplish the latter.
*As usual the building department and the field of architecture doesn't take all the factors into account when deciding what code should be. Not every architect or inspector has looked into or even built their own deck. As contractors you should all look at the situation and environmental factors associated with your project in particular. In the northwest you would be foolish to install a pressure treated post in the ground. However in the central states it isn't a problem...solely due to days of rainfall per annum and soil conditions. When clay swell is a factor the post and buried concrete method is the wise choice. A sonotube footing will lift in those areas. Lets hope the building department catches up some day!
*Pete's method is the best, possibly with the addition of a metal post anchor or "spacer" as mentioned above. This is also pretty much the most expensive (read labor intensive) method. If the soil drains well in your area, you may be able to get by with burying the bottom of the post, but whatever you do, do NOT pour concrete around the post, which will insure premature rot out if it rains at all in your area. For me, the easiest method is to dig the footers, build the basic frame of the deck, and "hang" the posts (with post anchors) over the holes, supported by temporary supports, perpendicular to the posts. Then pour the concrete up around the bottom of the post anchors. The concrete will shrink a bit, so, plan for that. The concrete will form around the post anchors, so as to prevent the bottom of the posts from being knocked off the footings, but the posts themselves will not be in contact with the concrete.Personally, I think that using the dry concrete method is only appropriate for fences, and other non-structural applications.Concrete must be mixed in proper ratio with water in order to obtain proper strength. This cannot be accomplished with the dry method.
*We have a lot of buried 4 x 4's and 6 x 6's in hot, wet, rot producing soil. A common method is 3-4 foot hole, 2-3 bags of sakcrete, 2 or 3 shingles on top of concrete, PT (.70 ) post coated from bottom to 6 inches above grade with tar or non fibered roof sealer. and then backfilled. I dug around a couple that are 5 years old, wood is solid and tar coating is intact so far, so good. Scott
*Don't think those .70 posts are available in most locals. I've seen them in coastal areas, but none in the areas where I have lived.Interesting building method though. I wonder why "non-fibered" roof sealer.
*I just replaced a wooden porch column that was rotting out at the bottom. The new column's instructions said to coat the inside of the bottom of the column "as far as you can reach" with "non-fibered roof sealer". That stuff proved difficult to find...everyone has fibered.I wonder why "non-fibered" too. Anyone have an answer?Rich Beckman
*Matt G.Good point on the .70, didn't think of the inland people.Non-fibred sealer for a couple of reasons:1. It is much thinner and soaks in a little bit better2. It can be put on heavy and fast with a brush instead of a trowel. Time for two coats3. The ends of the posts can be soaked in the can without a big glob of fibre on the end4. The fibre would serve no purpose in this application5. $1 a gallon cheaper# 5 might be # 1 :)Scott
*Rich non-fibred will actually "dry" with time or at least thicken to a plastic like coating. It will stay inside your column instead of oozing onto the porchQuestion to all. We mix and pour the sakrete and then let cure for a day before setting the posts. Does the dry method settle or is it ok? Last time we did some posts we had no mixer and ended up with a shovel and a 5 gallon bucket. I would have prefered to just pour it in the hole dry! :)Scott
*Pete;Have to agree, with some comments:Pressure treating comes in various "flavors". There is differing grades based on the percent of liquid which remains in the lumber. Here in CA you can get 0.22 pcf and 0.4 pcf. the later is rated for permanent ground contact.You are absolutely correct that cutting a post destroys the protection that PT provides. I see this all the time, post looks fine but is just a shell with a rotten core! Set the cut ends in a pail of a copper-based preservative (the longer you can wait the better.)I really like the Simpson Adjustable Post Base Anchors. Set a j bolt in the concrete +/- 1", come back later and the base allows adjustments. It also provides quite a bit of hold-down. The heavy duty ones are impressive. They also have a built-in 1" standoff to keep the post from any standing water.It also keeps the tasks separate: concrete and anchors one crew, carpentry with another.
*scott,The dry method is a breeze. I usually fill the hole 1/3 with water and them pour in quickcrete fairly slowly. It will force the unneeded water out of the hole. It will also set up in no time. would usually be ready to build on by next day although I usually give it 2 or 3. As odd as it sounds, you usually wind up with a fairly dry mix in the hole when you are done (one might assume it would be very soupy)Pete
*I would be concerned that the concrete that goes into the water first would quickly separate. the Quikrete folks make a special post-setting concrete that you treat this way -- it's a good deal more expensive than regular quikrete, anyone know why?I've been placing the posts on a few inches of gravel, Weatherwatch patch on the end of the uncut post, a bit of Sakrete, then full to grade plus a bit for drainage, wood float. For troublesome things like decks, prefer a sonotube at least 6" above grade to make life harder for termites, plus post anchor with standoff. No problems in the last few years. Would appreciate an easier way of course.I've been under the impression from what I've seen recently that wood in contact with -soil- rots a whole lot faster than wood in contact with concrete, all other things being equal.
*
I am building a new deck with posts in the ground, not on sonotubes. My question is should concrete be place wet under posts and allowed to set before placing posts or set post first then concrete around them? Some guys in my area place 1/2 bag concrete dry then post and the rest of bag dry, is this common?