*
I am contemplating about finishing my attic. I went up there
and took a close look. It looks like it is pretty clean except
some wires criss crossing all over which I can re-route and the
air conditioning/heating ducts that lay on the floor over the
joists. The latter is going to be my problem. How do you deal
with these? I want to keep the same outlets to the rooms below.
So I don’t want to remove them. The ducts are round and about a
foot or so in diameter. I saw one remodeled house where they had
raised the ceiling except that they had left a 1 foot wide channel
in the perimeter and they ran all the air ducts in that channel.
That seems like a good solution except that it raises the attic
floor by a foot which means I would lose a foot in head room.
On top of that it requires major reframing. Is there a way to
deal with these air ducts without reframing?
Thanks…
Discussion Forum
Discussion Forum
Up Next
Video Shorts
Featured Story
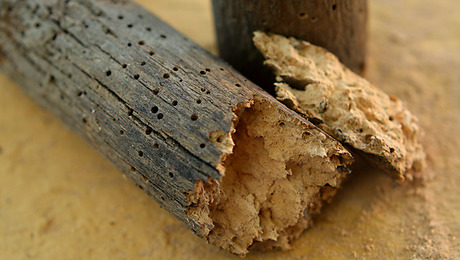
Learn how to fight wood-boring beetles and prevent home infestations with expert advice from Richard D. Kramer, an authority in pest control.
Featured Video
How to Install Exterior Window TrimHighlights
"I have learned so much thanks to the searchable articles on the FHB website. I can confidently say that I expect to be a life-long subscriber." - M.K.
Replies
*
One possible solution would be to transistion to rectangular duct that can be run withing the joist bays. Run then all to one side of the space then run the trunk line is the kneewall area.
*Remember your ceilings will have a lot of added weight when you get the attic floor decking on and start storing your bowling ball collection up there--be sure the joists are deep enough to take the extra load. If you have to sister deeper joists alongside the old to take the load, you may have more room to run the ductwork in the bays.
*Great idea Bill! That seems like the only solution.I was about to give up on the whole idea but nowyou got me thinking this can be done after all.SG, the joists are 2x6's. I was going to just lay down 4x8 plywood sheets and nail them to the joists and cover it with carpeting. How do I figure outif I have enough loading capacity with the currentjoinsts and if I need to beef them up? I don'thave the slightest clue about what the standardbuilding codes are for this.
*There is much more to consider than the depth of the joists. You must now consider them floor joists instead of ceiling joists and go to a different span table. I am attaching one from an old book i have, so don't take it as gospel. "Modulus of elasticity" (E) in layman's terms is "bounce": the greater E, the floppier the floor. As you can see, the spacing of the joists is also very important: floor joists are most likely on 16" centers, whereas 24" centers is common for ceiling joists. For instance 2x6's on 24" centers can only span about 8' without annoying bounce. Another consideration is the quality of the wood itself--can you see a grading stamp on the lumber that was used? If not, is it fairly clear? Small knots or knots near the center of the board aren't as important as big ones at the edge, for instance.So, clear as mud, eh? I suggest you find your joist spacing, measure the span (bearing wall to bearing wall; partitions don't count), get familiar with this span table, go to a lumberyard (NOT Home Depot) after they've finished loading up the contractors in the morning rush, and look for one of the older guys to advise you on what he would do if it were his own house. They'll have up-to-date codes as well, and grade-stamped lumber.
*Modulus of elasticity, E, is actually the ability to resist bouncing, or deflection. As you look at the top row of the table, there are E values in millions of psi. The higher the E, the longer the allowed span. Low E is high twang, and vice versa. The "E" column you should use depends on the species of tree and grade of lumber. For instance, #2 Doug fir has an E of 1.3 million psi.These tables are based on deflection, using the standard limit of one 360th of the length, usually called L/360. That's just one consideration.Another very important one is maximum extreme fiber bending stress, called Fb. That's the number under the span in these tables. The Fb number in the table is the amount of force in psi trying to rip apart the fibers on the bottom edge of the joist. For each species of tree and grade of lumber, there is a maximum safe value for Fb, and there are correction factors you have to apply depending on whether the load is temporary or permanent. For instance, #2 Doug fir in permanent applications has an Fb limit of 810 psi. If the number on the second line is under 810, you can use #2 DF. If not, you need a better grade of lumber. There are also things like bearing and horizontal shear, but with joists they're usually not the limiting factor. They get important with beams that are short and very heavily loaded.Bottom line, your joists have to be OK both for deflection and Fb. And "OK" depends on the applicable code in your location.-- J.S.
*If you have no clue.....put down the hammer, and let your fingers do the walking. No sense destroying you home just because it looks easy on TV. Jeff
*Yeesh, John, where did i learn to read and write, eh? Thanks for catching the E:bounce gaffe, and for expanding on the "lumber quality" part of my post with the Fb discussion. I think i'll go crochet something now...(slink, slink)
*Thanks a bunch SG for taking the time to scan that page and providing me ( and hopefully others who need it )with this invaluable information. This is way beyond what I expected to get out of this forum! I think I got enough to work with now.I understand the concept of modulus of elasticity and strain and stress and the sorts from a materialslab course I took a long time ago in college but I admit I have never actually applied them to lumber. I assume that if I followthe local code or the guidelines from the table you provided I'dbe OK. I tend to overdo things a bit and in this case I was wondering if there would be a case where I would have too rigid a structure that would compromise the integrity of the building againstearthquakes? This is Northern California we are talking about.Maybe I am getting too much into the nitty gritty parts of this thingbut for the sake of knowledge it doesn't hurt to know.Oh by the way Jeff not to worry...I claimed I don't have a clue about building codes but once I look it up I can build to perfection. I don't do this full time for a living but it isnot my first time taking on a project.Regards,WackyCustom Carpentry for Private Use Only! :-)
*It is a very good idea to have a structural engineer review your project before you start building.They are experienced in many nuances of what you are looking to do and you only have one chance to get this right (pretty steep learning curve for you).While you may have the patience and good intentions to do a very good job of the construction, you probably still will benefit greatly from an experienced structural engineer's review of your design.I recommend it.(I recently did what you are proposing and am so glad that I spent the $500 or so for his input because he confirmed some of my plan and corrected some other really important things and had some great time / money saving ideas that I never would have thought of!)
*Wacky, i've never had to build for quakes, but got the tour of how my friend retro-fitted his three-storey Victorian remodel in San Jose and he was making it pretty darn rigid: continuous tie-downs from foundation to top every four feet, shear walls everywhere you looked, lots and lots of bridging, tons of iron in the concrete. That said, i used to live around the Bass Lake/Oakhurst area in the Sierras were we had the quakes out the Mammoth Lakes area in the early 80's, i think it was. Anyway, the subdivisions were going up very fast and ugly, one nail per end of a stud and lots of decking where nails missed the joists, but when the houses were hit, they twisted instead of breaking apart like the better-built homes. It was odd...CalTech has the Earthquake Engineering Library if you really have nothing better to keep you up nights worrying. Also, Journal of Light Construction has a couple of on-line articles on tying a house together; though not specific to your case, they would flesh out your building-for-earthquakes IQ.http://www.jlconline.com/jlc/archive/framing/tying_down_house/index.htmlhttp://www.jlconline.com/jlc/archive/foundations/seismic_support/index.html
*> the greater E, the floppier the floor. Uhhhhhhhhhmmmmmmmm. ya got that one backwards, splinter. a higher value means it's more resistant to deflection. The number under the span is the minimum fiber bending value required. It would probably be better to go to the lumberyard, find out what sizes and grades are available, and then ask them for the span charts for that lumber. No sense calling out something that you can't get locally.
*Sorry John - I didn't see that you had already posted regarding that until I had already posted my explanation. Wasn't trying to upstage you..................(-:
*i ya got that one backwards, splinter. Yup, check my mea culpa below. :)
*
I am contemplating about finishing my attic. I went up there
and took a close look. It looks like it is pretty clean except
some wires criss crossing all over which I can re-route and the
air conditioning/heating ducts that lay on the floor over the
joists. The latter is going to be my problem. How do you deal
with these? I want to keep the same outlets to the rooms below.
So I don't want to remove them. The ducts are round and about a
foot or so in diameter. I saw one remodeled house where they had
raised the ceiling except that they had left a 1 foot wide channel
in the perimeter and they ran all the air ducts in that channel.
That seems like a good solution except that it raises the attic
floor by a foot which means I would lose a foot in head room.
On top of that it requires major reframing. Is there a way to
deal with these air ducts without reframing?
Thanks...