OK, so it dipped to -1 last week here in eastern Kansas. A subcontractor to our contractor is out there in 5 degree weather, pouring concete by hand (Sakrete) for some small footings up against a concrete wall. Footings are about 6″ x 24″ x 48″ tall, with rebar. No blankets or heaters. The 24″ side is against the 8″ foundation wall, which has not been backfilled yet.
Should I worry about the quality of the concrete given that it was poured in such cold weather ? Is it just going to disintegrate when it warms up, or be weak that it’ll fail in a couple months ? Should I have the contractor rip the footers out and repour them this week, when temps will be in the 50’s ?
Discussion Forum
Discussion Forum
Up Next
Video Shorts
Featured Story
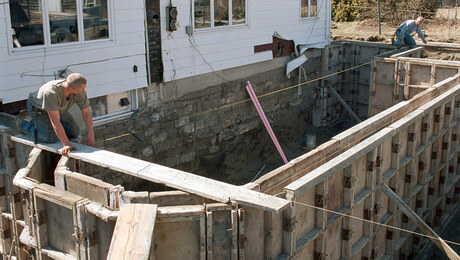
There are a number of ways to achieve a level foundation and mudsill.
Highlights
"I have learned so much thanks to the searchable articles on the FHB website. I can confidently say that I expect to be a life-long subscriber." - M.K.
Replies
Probably
Point it out to the contractor in wwriting with your request. That way you have documented conditions etc if he refuses and it comes to be a problem later.
These sound more like pilasters than footers. what's the purpose?
Welcome to the
Taunton University of Knowledge FHB Campus at Breaktime.
where ...
Excellence is its own reward!
Correct, pilasters. My flub. They are placed on either side of the 4' foundation wall and will be supporting the porch columns that in turn support a partial overhang of the second floor as well as the porch roof.
During the hydration process which is a chemical reaction between the water and the cement in the concrete, for the first 12 hrs or so some heat is generated. Concrete is more susceptible to freezing after this initial set period. Still, freezing of the water in the concrete can be very detrimental anytime during the process. Unfortunately, cold weather concreting is a fact of life, but it can be done successfully if some precautions are taken. Negative 1 degrees Fahrenheit is quite extreme though. Sometimes admixtures (additives) are used to accelerate the hydration process for cold weather concreting. Calcium chloride is a common accelerator admixture used to decrease the time required for hydration. It doesn't sound like this was part of your situation though.
If the footers are not backfilled in a week or 2 I'd test their strength with some firm taps from a hammer. They should be up to at least 70% strength in a week, and for this kind of application 2500 PSI would probably be the minimum strength concrete used. The concrete should not be easily damaged by the moderate hammer impacts. Not to make you even more paranoid, but hand mixed concrete is not the best product... If the concrete was mixed in a machine, that helps, but personally I think bagged concrete gives inconstant results due to the fact that all bags may not be of the same ratio of cement/fine aggregate/coarse aggregate. Piffin's way to CYA is a good, but if the footers are obviously faulty, it will be much easier to get it corrected before backfill and a house is sitting on them. Matt
I would worry more about the fact that he was using Sakcrete than the fact that it was cold. sakcrete is a pour excuse for concrete when its 70 degrees outside.
Agreed. But it does make good fill as long as you don't need the drainage.
sakcrete is a pour excuse for concrete
Especially if you don't read the labels. The "sidewalk" strength stuff all too often being the biggest, cheapest, pile at the big box gets used all too often. Per their own bag, it's only like 1500-1800 psi test. There's supposed to be a 2400 and a 2800 psi bag, IIRC (and I'm just not up to googling to find out), which are the actual 'structural' mixes.
The real problem with most sakcrete is in the water. All of the other proportions are "perfect" to the mix in the bag, until the water is added. Ten gallons where six would do (or worse yet, 15 gallons . . . )
I'd rather see a sub use a mason's mixer and "throw" by-the-shovel recipes than most bag mixes. But that may be due more to respect for someone who knows a "recipe" (i.e., might actually know why it's concrete and not "cee-mint"). But I also require everybody to follow "my" rules, too--that means test cylinders. That extra couple of hundred can make everybody much happier.Occupational hazard of my occupation not being around (sorry Bubba)
The reply you got about hydration was on the right track, but he left an important part out- heat. Concrete cures by heat of hydration. In other words when water is added to concrete ( portland cement, small agregate 'sand' and large aggregate 'stone') heat is the reaction. The problem is that this reaction of heat doesn't happen if it is offset by the low temperatures you are talking about.
The add mixture, calcium, will bring the temperature up to allow heat of hydration to occur, and initial set is very important. Most of the concretes strength comes quickly,50% of design strength in 7 days, total design (or what the mix was engineered for, say 3500 psi) strength happens in 28 days. The amount of water has a serious effect on strength, as does the aggregate size and amount of portland cement.The more water the lower the heat and strength. The heat created causes a binding ( a pulling together) of the aggregate. The bottom line is this: if the heat wasn't there, the process that binds the ingrediants didn't happen.
What you have now is frozen water, sand, stone, and portland cement not the curing concrete you wanted.
One thing you're not telling us is where the top of the footing is relative to grade. If the footing is in a hole, and tops out a foot or so below grade, then generally the heat of the earth will keep things fairly warm.
I would think at -1 F and no heating or blankets, then even bleed water would freeze on the concrete surface. At the very least this means crazing and powdering at the surface exposed to air. Not acceptable in structural work. Document and ask contractor to prove the pilasters are at design strength or replace with new work that is.
Sad thing is, it's easy to protect and heat small vertical work like this. It should have been done and the work would have been fine.
Wally
Regardless of the curing within the formed set itself, the foundation wall he was laying it too was also a lot of mass at that cold temp. I can gaurantee that it frosted the water in the mix upon contact and there is absolutely no bond between the new pour and the original wall, even if by some freak of nature, the new mix actually cured.
Welcome to the Taunton University of Knowledge FHB Campus at Breaktime. where ... Excellence is its own reward!
piffin's last post left me wondering if the rebar in these pilasters is tied into rebar protruding from the poured foundation wall the pilasters rest against...
Edited 12/30/2004 10:55 pm ET by Pierre1
Wouldn't matter if it was tied into the existing fdn, the new conc will fail anyway. But in the replacement work, yes it should be tied in.
WallyLignum est bonum.
Bingo!
You really believe a hack, pouring Sakrete in subzero temps is going to be using rebar?
Welcome to the Taunton University of Knowledge FHB Campus at Breaktime. where ... Excellence is its own reward!
As soon as they thaw out, put some gloves on and pull them apart.
Samt
MarkJ, you said it dipped to -1F, but that the pilasters were poured in +5F weather. Maybe the pilasters did not freeze.
Did Temp ever dip back to 32F or less since the Sakrete pour, and when relative to the pour date? Maybe, just maybe, your Sakrete had enough time to hydrate before the freeze came.
If any of the Sakrete bags are lying about, can you figure out what their psi rating is?
All: IIRC, the magic temp for properly mixed concrete is about 25 degrees F. Below that it freezes, above that, any reasonable mass will properly cure - if it is covered adequately to keep the surface from drying out.What has always concerned me is the upper temps. I recall that the Army Corps of Engineers requires mixing w/ ice at some magic temp - to keep it from starting to cure too soon. I saw some ammo bunkers being constructed in Saudi - they built an ice plant adjacent to the mixer so they could work in 120 degree F air temps. I got some ready mix here in Etlanner that was mixed at the plant at about 80 degrees. By the time it got to my site45 min later a=fter the driver got lost, it was 95 deg. By the time the pump finished placing it, it had gotten hot (not warm) to the touch & set up in the pump's piping. Took them two days to clean out the pipes. Wife & I spent 13 continuous hours cleaning rubble out of our ICF's. Got finished just in time for them to physically remove me from the scaffold so they could pour the last bit of new mix a week later - at their expense.That's why I really treat ready mix w/ suspicion in the heat of summer.DonThe GlassMasterworks - If it scratches, I etch it!
When Hoover Dam was built they built a network of pipes into it so that cooling water could be run through to keep the concrete from overheating.
There's a lot more to concrete than cursing, ragged clothes and big arms.
Toured the Glen Canyon dam...guide told us the pour had gone on 24/7 for 8 years! That was around the time Hoffa disappeared...