Hello All, I am building a new home and reaching the insulation stage.I am familiar with fiberglass, but have got a price on Icyene insulation. Any recommendations on Icyene. At more than twice the price of fiberglass I wonder if it is worth the extra price.Thanks for your input
Discussion Forum
Discussion Forum
Up Next
Video Shorts
Featured Story
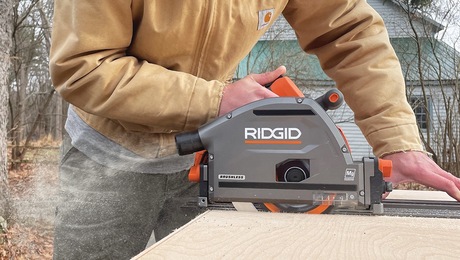
The best tool for straight, splinter-free cuts is made even better without a cord.
Featured Video
SawStop's Portable Tablesaw is Bigger and Better Than BeforeHighlights
"I have learned so much thanks to the searchable articles on the FHB website. I can confidently say that I expect to be a life-long subscriber." - M.K.
Replies
I think you mean Icynene. They are the market leaders in the open cell half lb density spray foam insulation market.
Do a search here and you will find mostly positive opinions about foam in general. I own a spray foam insulation company in Massachusetts. Of course I feel it should be put in any space you breath the air in or pay to heat or cool.
Talk to differnt foam companies too!! Contact Corbond for a company nearest to you. They are the market leaders in the closed cell foam.
Good luck!
Stu
Can you expound on closed cell vs. open?
Basically 1/2 lb is open cell. "open cell" means there is less then 90% fully closed and complete cells in the foam structure. typical 1/2 lb is around 50%. The important thing about this is that the foam complete cells hold regular air or carbon dioxide. Those gasses are good insulators. The R value is about 3.7 per inch, so a 2x6 wall = R20. This foam is about the consistency of angle food cake.The closed cell is approx 2 lb per cubic ft density. Also known as polyurethane foam or Corbond (brand). Completed cells here are around 93%. Most foams at this density are expanded (blown) with a chemical that creates a gas that is a very good thermal insulator. This gas is trapped in the foam inside the closed cells and results in R values as high as 7 per inch. Less than 3" for R19. The closed cell is also rigid and actually solidifies the structure of the building.I put the closed cell Corbond in my own house. It cost a little more but it is the best you can buy. When have you ever regretted buying the best?Stu
I've read here about problems with foam pulling away from the framing, etc. Is this more prevalent with closed cell or open cell?
Also, I guess open cell is more air/moisture permeable. What are your thoughts as far as how this effects building envelope performance and longevity?
Do you know anything about the soy based foams - or was that more of just a "flash in the pan"?
Thanks.
Proper processing will ensure the foam sticks to the framing and does not pull away. A recent discussion with voids is the same problem, processing parameters, and maybe spray technique as well.
The denser foams stick better, in my experience, and have less problems pulling away from framing.
I install open cell in most homes I service. The key is stopping bulk air movement. Big moisture problems start with moist air infiltration through old fashioned type fiber insulation where condensation happens in the insulation itself. Then mold and mildew happens after it can't dry out due to vapor barriers, etc.
The foam permeability is more on the molecular level of diffusion. Kind of like water evaporating out of a glass vs. leaking out. A much slower process.
The soy foam is fine. That is what I use and have had no problem. The chemical reaction is all the same. The soy part is using soy oil in place of petroleum oil to get the polyols for the chemical reaction, that's it. Using one oil in place of another. The big benefit is that it supports Americans instead of foreign oil!!!
Big moisture problems start with moist air infiltration through old fashioned type fiber insulation where condensation happens in the insulation itself. Then mold and mildew happens after it can't dry out due to vapor barriers, etc.
Foam has been around for years also!!! It may be a bit old fashioned!!
It has been found that condensation mostly does not occur in the insulation itself but on the "first condensing surface" which is usually the cold sheathing. In the wall, the phenomenon appears to be that: the heat release from condensation into the low mass fiberglass matrix, heats the glass fiber and condensation does not occur until a surface with sufficient mass to absorb the heat is found.
There were some problems with older loose houses with improper interior house ventilation and other moisture problems (wet houses). If you cleaned up the ventilation and moisture issues the wet attics/ moisture problems went away. These example bad fiberglass houses were built before "building science " was a term that any of the building industry nor public had ever heard.
Now that we know what causes these problems, they are easily solved. The vast majority (probably 95-98%) of Canada's low energy R2000 houses are built using fiberglass as wall insulation, but no problems are showing up in these walls after 20+ years. This program is licensed to Japan (1992) and other countries have imported R2000 houses. Many of the principles that Joe Lstiburek espouses and builds upon were from the R2000 program where he was an early employee.
You should buy and read "Energy Design Update". Two articles in the past year mention high levels of moisture in Icynene to the point of severe rot in one house. This product is not the end all and be all. People are being drawn to it by some of the same tactics used by the P2000 insulation- not addressing all aspects of air leakage, energy efficiency and best use of funds to provide the highest level of efficiency at the lowest cost.(the old maximum/minimum equations) Claims are made but never do I hear of a truely comparative study where 2 exact houses with the same amount of nominal R value glass or cellulose and foam are installed, with the same air leakage characteristics and then monitored for a year or two. Then we will see where it is best to spend the $$$$!!!
This gas is trapped in the foam inside the closed cells and results in R values as high as 7 per inch.
What "aged" R values should you be quoting? Without a very good diffusion barrier like foil used on some board foams, the gases are going to diminish over time.
The closed cell is also rigid and actually solidifies the structure of the building.
Do you have any testing by someone like Forest Products Laboratory on the extra strength. The house should have already met code for framing by the time you get to spray it.
High density foams are really specialty products. Hard to justify the cost when cheaper products such as fiberglass and cellulose will get you much better paybacks. You can use the saved $$$ to buy better windows where the R's are low, insulate under the slab (up north), put in a better HRV with a larger range of control options, increase the attic insulation with much cheaper cellulose. Also spray foams do not do all the sirsealing needed in homes as implied in ads.
To most of us, energy efficiency is all about paybacks (lower heating bills) but we forget about the Law of Diminishing Returns. At some point , it's better to leave your money in the bank (or don't borrow any more), since there's no reasonable payback. Sure you can reduce the energy bills to $0 or be "off grid" but if it costs $100,000 more, is it worth it? Interesting to have a look at the Florida Solar Energy Center study on this subject!! See the "Economics" section:
http://www.fsec.ucf.edu/bldg/pubs/cr978/#Economics
Edited 6/6/2006 9:12 am ET by experienced
http://www.resintechnology.com/TB-RT3041_1.7-2.0.html
R value is 1/K. Aged K = 0.15. R=6.67
Corbond has an aged at cold and hot temps. The avg is ~7.0
From the info sheet:
"1. This information is intended only as a guide for design purposes. The values shown are the average values obtained from sprayed laboratory samples. The test methods were performed per the ASTM Book of Standards. 2. K Factor varies depending on age and use conditions. NOTE: THESE PRODUCTS ARE INTENDED FOR INDUSTRIAL USE ONLY "
Like people been saying about fiberglass, you don't get the same conditions in the field.
Why are these products "for industrial use only"?
Edited 6/6/2006 11:35 am ET by experienced
Here we go!!!
Show me a better product and I'll use it.
Till then you can keep using the FG with the CANCER warning on every bag. You did know there is a CANCER warning on every bag right? I suppose the aged vs. unaged K value is more important than that.
Hate the game not the player.
Stu
I'm just getting to the insulation part of my new shop, per Building Sciences recommendation I would like to use a vented roof. What would you recommend for baffles that won't be crushed by the expanding foam?Thanks.
Steve.
Skip the vented roof.
But foam sprayed into an open cavity won't crush your baffles.
Joe H
Not to take sides here, but based on my most recent read on the topic, the cancer warning in FG is likely just boilerplate. I wish I remembered the source, but recent studies indicate that FG is not a human carcinogen.
That's not to say there aren't better products out there, but let's not go causing a panic where none is needed.Andy
"Never try to teach a pig to sing. It wastes your time and annoys the pig." Robert A. Heinlein
"Get off your dead #### and on your dying feet." Mom
Till then you can keep using the FG with the CANCER warning on every bag. You did know there is a CANCER warning on every bag right?
The only reason this is on bags is that they reduced the size of the fibers to make the product more user friendly (less itchy). With smaller fibers, there is more of a chance of inhalation. The warning is not a "cancer" warning but a warning to wear dust mask, tight clothing, etc to prevent skin and respiratory irritation. It is recommended that cellulose installers wear masks also. And do not your installers wear masks and protective clothing also? Oh no must be a cancer causing product....look how they're dressed to protect themselves.
Let your product sell itself on its own merit and pricing, not on running others down by innuendo and down right scare tactics!!!
I had asked a few other questions but no answers???
Edited 6/6/2006 10:50 pm ET by experienced
Believe me friend my product does stand on it's own merits. That's why i'm too busy to answer the same questions on a computer every couple months.
I only try to educate and people shooting darts at me from cyber space.
Don't be a hater.
As you will note I have never said that foams are bad products but have questioned some of the claims!!! I think the foam is a good specialty product in certain uses.
As mentioned earlier, this has been a commercial/industrial product where higher R's in a reduced space are needed such as in trucking "reefers". Loss of space to insulation means loss of revenue!!!
I would never advocate installing batt or blown fiberglass in a conditioned (or cathedralized) attic application. Foam with vapour barrier (in cold applications) wins easily.
If the rim joists are to be airsealed from the interior using sealed poly or XPS board, then use spray foam (if the price is right). But there are much cheaper and better methods if rim joist airsealing is "built in" at the framing or siding stages. Hard to imagine- getting a better job at lower costs.
Amen!
By the way, did you know that drinking water can KILL YOU!! SEriously, it is a fact!
Show me a better product and I'll use it.
My analogy: I'd like a "Rolls" (1 car for life) but I can't afford one. Show me cost effective products and I'll use them.
Edited 6/7/2006 10:57 am ET by experienced
Cancer? Like asbestis (spelling) if it is locked away there is ZERO problem. Fiberglass insulation LOCKed behind drywall is ZERO problem. So what was your point again?
When air infiltrates into the house it goes through the walls and ceiling. That is where the FG is. Little FG particles travel along with the breeze that comes in the electrical boxes on the exterior walls. You've felt it right?
People with foam houses report much less dust than in previous houses they've lived in. Just the facts. Sorry.
Ain't buying the bull. ANd seriously you can die from drinking pure water!
People with foam houses report much less dust than in previous houses they've lived in.
People with R2000 houses with fiberglass in the walls (and sometimes attics) also report much less dust than in previous houses they've lived in. What's the reason for this?
The "previous house" you mention was probably built in the 50's-80's before air tightness and HRV's were part of a house. A lot of the dust came not from the fiberglass but from infiltrating air through the old, very loose house. You can see this in old fiberglass that is just black with dirt/dust exactly in areas with air leakage first through the walls and then the batts. With most of the needed air in a new home pre-filtered through an ERV/HRV, most house dust is now internally generated or may be brought in on clothes or shoe bottoms and next to none will come from exterior wall insulations. ( Note: You'd be surprised how much dust you bring into the house on your clothes/shoes. In healthy homes for environmentally ill people, it is recommended to remove shoes in a separate vestibule before entering the home.)
Most new homes have exterior sheathing membranes (typar et al) usually taped to give an exterior air barrier. This stops air from infiltrating into batts from the exterior and then going into the house or back out the same wall it came in. This has markedly improved the performance of batts in walls. The membranes should be done well as they are also part of the wall's drainage plane.
At the interior wall surfaces, we also have sealed interior air/vapour barriers or airtight drywall which further improves the airtightness of the home and performance of the batts. So not much air is going to enter through the fiberglass in a new home. Nowhere have I seen in regular "Healthy House" literature (not being built for someone already sick), that fiberglass should not be used!!
More scare tactics: fiberglass particles rushing into your home!!
If you want to scare people about what's in their homes, send them this website!!!!!
http://www.ewg.org/reports/inthedust/part1.php
From another report: Ordinary house dust is a complex mixture of pet dander, fungal spores, particulates from indoor aerosols, soil tracked in by foot traffic, VOCs and traces of metals.
ABSTRACT Pesticides, polynuclear aromatic hydrocarbons (PAHs), lead(Pb), and other metals accumulate in home soil and house dust. Exposure of infants and toddlers to Pb by dust may be greater than other pathways. Many pollutants found in carpet dust are protected from degradation and accumulate over time. Greater numbers of pesticides are found in house dust than in indoor air. Pb and PAH concentrations appear to be magnified in house dust when compared with midyard and walkway soil samples. Studies using methods developed by the U.S. EPA show evidence of track-in and/or carry-in of Pb, PAHs and pesticides on clothes. Preliminary results of an eight-home study report PAHs in house dust at 1 to 100 ppm and suggest track-in as a major source of PAHs in house dust.
Another Study: Chemicals identified as endocrine-disrupting compounds (EDCs) have widespread consumer uses, yet little is known about indoor exposure. We sampled indoor air and dust in 120 homes, analyzing for 89 organic chemicals identified as EDCs. Fifty-two compounds were detected in air and 66 were detected in dust. These are the first reported measures in residential environments for over 30 of the compounds, including several detected at the highest concentrations. The number of compounds detected per home ranged from 13 to 28 in air and from 6 to 42 in dust. The most abundant compounds in air included phthalates (plasticizers, emulsifiers), o-phenylphenol (disinfectant), 4-nonylphenol (detergent metabolite), and 4-tert-butylphenol (adhesive) with typical concentrations in the range of 50- 1500 ng/m3. The penta- and tetrabrominated diphenyl ethers (flame retardants) were frequently detected in dust, and 2,3-dibromo-1-propanol, the carcinogenic intermediate of a flame retardant banned in 1977, was detected in air and dust. Twenty-three pesticides were detected in air and 27 were detected in dust, the most abundant being permethrins and the synergist piperonyl butoxide. The banned pesticides heptachlor, chlordane, methoxychlor, and DDT were also frequently detected, suggesting limited indoor degradation. Detected concentrations exceeded government health-based guidelines for 15 compounds, but no guidelines are available for 28 compounds, and existing guidelines do not consider endocrine effects. This study provides a basis for prioritizing toxicology and exposure research for individual EDCs and mixtures and provides new tools for exposure assessment in health studies.
Do a search on house dust and see what else we should be worried about. You won't see much if anything about fiberglass!
Ditto on the economics.
Some people, see that they can save $50 a year and figure that it is worth almost any price to get that savings. If you can invest money at 10%, a $50 savings received FOREVER is worth $500. (This is business school stuff). But remember you have to recieve that $50 FOREVER. If you home or die the savings is worth less. There is a diminishing return factor here as well in that the impact of savings in years 15 or 20 are worth less so in reality you don't really need to consider the far out years.
A reverse of this is that if you spend $5000 more to insulate a house you must save $500 each year forever.
This said, I am in no way saying that sprayed insulation is a poor investment. I don't know. I would need to know, and would very much like to know, what it costs to insulate a 2500 sq ft house with fiberglass vs spray and would the heating costs of both would be.
My point in this post is that anual savings is only half the story and that not all operating savings are worth the upfront costs. Some people are just willing to throw almost any amount at the upfront costs for minimal long term savings.
It's kind of a 'pay know,pay latter' situation. The stuff is great and great things tend to cost more. A lot of people just look at the return in the investment side of it only. But you should also consider the personnel comfort factor, sound deadening, and resale benefits too. If it was my house I would do it. I hate giving money to the energy companies.
Take it from me- contrary to popular belief, merely paying lots of money is no guarantee of either a quality product or quality installation. It applies to foam insulation every bit as much as to anything else in life.
One recommendation from my own hard experience: get the installer to sign a rider to their contract: if the foam has a perceptible odour after ventilating the space for one week then shutting the doors and windows for one day, they'll come back in, rip it out and replace it free of charge. A proper installation will be odourless. An odour after a week remains because it's been sprayed with unconverted (excess) resin. If they won't sign that rider, choose an installer who will, or choose another product. Icynene warrants their chemicals only, and the installer should have insurance to cover installation problems. If they don't, look elsewhere.
I have about 1500 square feet of icynene in my garage/workshop which still has a strong odour some four months after the installation. The installer has made it clear that I'll have to go after him in small claims court if I want anything out of him aside from some courtesy work on the balance of my job. Nobody can tell me how long this odour will persist, but one thing is sure: the same property of stopping air movement has trapped in this odour so the only way it's leaving is via diffusion- that's a long, slow process.
Bad installation aside, it's a great product- but it's debatable whether or not it's worth the money. Unless you're doing the work yourself or can personally assure that the detailing of the framing, air barrier and vapour barrier is done perfectly, don't use fibreglass. If I had mine to do over again, I'd go with a hot roof and dense-packed cellulose- unfortunately not a method I could find a contractor to do for me in this area.
Pipe,
We have switched over to complete Icynene installations on our new projects. We recently completed a total gut and remodel of a 3000 sf ranch style doctor's office. Prior to our work, the monthly electrical bill was $600 to $800 per month. Post remodel with a 3.5 inches icynene on the walls and 7 inches under the roof, the building has $200 to $300 electrical bills.
Granted, new HVAC and new glazing (limited area) were installed as well but an average of $500 per month savings quickly paid off the $6000 difference between FG and the Icynene.
That is all the cost benefit analysis I need for this product. BTW I am not an Icynene vendor or installer, just a very satisfied GC with a great installer.
Bruce
My bills for heat and air were over $100 a month and that was with fiberglass in. I tore it out and had it sprayed with icynene. I had 1460 square feet installed at a cost of $2080. Last month my utility bill was $9. This is for a 650 sq ft garage apt. with icynene sprayed on the vaulted ceilings, walls, crawlspace and floors, forming a virtual cocoon. With the AC running I don't expect my AC bill to go more than $25 a month during the summer. The fiberglass I took out of the crawlspace was sagging badly. It would have been too much work to detail it for the same level of airtightness that a sprayed icynene job would offer. When I gut the main house and remodel it, I am going to use icynene. I own both the garage apt. and the main house and live in the garage apt. and rent out the main house. I will never, ever use fiberglass again. It is too breathable (as in air infiltration).Handyman, painter, wood floor refinisher, property maintenance in Tulsa, OK
Pebble,
That's great. The other great benefit of the product is the noise reduction. Nothing scientific, but the doctors were ultra concerned about noise reduction and eliminating audible sound between exam rooms (HIPPA requirements) and they have been ecstatic about the elimination of room to room noise reduction.
The old exam rooms were 1/2" drywall with R-13 FG between studs. The new rooms have 5/8" drywall with Icynene. When we were trimming out the rooms and installing the floors, you had to stick your head out the door to call out measurements-never had to do that before.
Bruce
Yes, I forgot to mention that a highway (I-244) runs behind my house probably 100 yards away. That is one other benefit of achieving this level of airtightness, the noise reduction factor. Even This Old House magazine had an article a while ago where Tom Silva remarked at how much more noticeably quite the traffic was after the product was installed. I asked the guy that sprayed my install to spray the interior wall between the bedroom and the bathroom if it was not too much of a big deal (not included in the bid). He did and I can tell how much of a difference it has made. The bathroom feels compartmentalized... you would have to listen carefully for the shower and the toilet flushing. And this is within a 650 sq ft garage apartmment.Handyman, painter, wood floor refinisher, property maintenance in Tulsa, OK
who won this argument?-----------------------------------------------------------------------------
WWPD