Question: Do you think I should include a nailboard with the 1″ polyisocyanurate that’s going on my walls? Or will the wall sheathing (an inch away from the cedar siding) be enough?
Discussion Forum
Discussion Forum
Up Next
Video Shorts
Featured Story
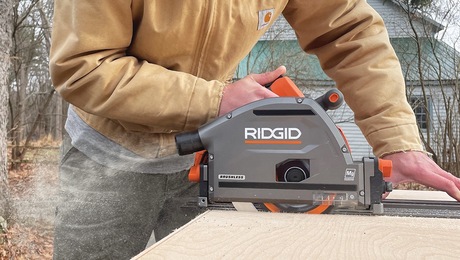
The best tool for straight, splinter-free cuts is made even better without a cord.
Featured Video
SawStop's Portable Tablesaw is Bigger and Better Than BeforeHighlights
"I have learned so much thanks to the searchable articles on the FHB website. I can confidently say that I expect to be a life-long subscriber." - M.K.
Replies
I'm not sure what you mean by the term 'nailboard'. It's also not clear whether you are putting the polyiso on the outside of the wall or the inside.
If you're using foil-faced polyiso, the insulation will comprise its own vapour barrier, so it should go to the warm side (inside, in your area) of the wall. Ideally, the elements should be (from the outside in):
The 1x3 strapping is what will hold the polyiso board to the studs, and will also be what you screw your gyprock to.
Dinosaur
How now, Mighty Sauron, that thou art not brought
low by this? For thine evil pales before that which
foolish men call Justice....
There is sheathing on the outside of the studs. The question is should I add a "nailboard" (just another layer of sheathing, but outside the polyiso).
Here's the buildup from the plans. In bolded red caps I've added to the list what I'm wondering if I should add. No foil on the polyiso, since it's on the outside.
- Western Red Cedar Rough Sawn clapboard, 7"
- 30# Building Paper / House Wrap
- 1/2" OSB SHEATHING
- 1" Rigid Polyisocyanurate Insulation (Celotex or Equal)
- 1/2" OSB Sheathing
- 5 1/2" Wood Studs @ 16" O.C. w/ R-19 Batt Insulation
- Vapor Retarder, seal per Manuf. Specs
- 1/2" Gypsum Wallboard (GWB), painted
Edited 6/13/2009 9:36 pm ET by gb62
Okay, the answer is 'No,' but you've also got the polyiso on the wrong side of the wall.
If you build a wall with a double vapour barrier--one on the inside and another on the outside--you will have serious rot and mould problems very soon. Remember that vapour barriers are not perfect--nothing in building is perfect!--and that some water vapour will inevitably find its way into the wall cavity.
What gets in must have a way to get back out again...and by putting a second vapour barrier on the outside of the wall cavity, you are trying to prevent that happening. Result: the inside of the wall will get wet, and stay wet.
Move the polyiso to the inside, and let it be the vapour barrier. Use strapping to hold it in place and to mount your gyprock so you don't need to use 3" gyprock screws.
Also: Use furring over your housewrap or felt to stand the cedar claps off the OSB sheathing so both the claps and the OSB will dry better and faster when they get storm-blown moisture driven in behind them. OSB doesn't like getting wet at all; take a look at this chimney chase that was sheathed in OSB and had cedar shiplap nailed directly to it.
View Image
Dinosaur
How now, Mighty Sauron, that thou art not broughtlow by this? For thine evil pales before that whichfoolish men call Justice....
I can certainly consider moving the polyiso to the inside. Regarding the concern about moisture getting trapped in the walls, I believe the housewrap on the exterior is not intended as a vapor barrier - wall moisture should diffuse through it. The "Vapor Retarder" is on the interior.
On edit: reading your post again, I think you are saying that the polyiso is the vapor barrier, and that is going to result in moisture trapped between the polyiso and the interior vapor retarder (that is, in the studs and OSB sheathing). Is that right?
Edited 6/13/2009 10:19 pm ET by gb62
Yes, that's right. Even without the foil facing, rigid insulation board tends to act like a pretty effective vapour barrier. With the foil facing and taped joints, you are getting as good a vapour barrier as a sheet of poly plastic.
Felt used as a rain shield is not vapour impermeable, because you don't seal the laps between courses. It sheds liquid water like shingles on a roof, but will let vapour pass quite easily. The commercial housewraps such as Tyvek and Typar are designed to be draft barriers; they too will let water vapour pass through while shedding (most) liquid water. That's why, in the temperate zone, you always put one or the other of those on the outside of the house.
However: In warm, semi-tropical climates such as the southern US, the VB goes on the outside of the house...because in that type of climate Mother Nature produces more humidity than do the human beings living inside the house. When that's the case, your primary water vapour source is coming from outside. In the Northeast, the ambient air is much drier, and most of the water vapour attacking a wall comes from human activities such as cooking, bathing, showering, breathing....
Dinosaur
How now, Mighty Sauron, that thou art not broughtlow by this? For thine evil pales before that whichfoolish men call Justice....
Excellent. Thanks for the guidance. Next question... :)
What do you think of this buildup for the first floor. Below this floor is the outside - the house rests on piers (no basement). I'm guessing this buildup may have two problems:
1. Waterproofing membrane is on the outside when it should be on the inside for reasons you have stated (this is in the northeast).
2. If a spill or a flood occured inside and water got below the floor and into the floor framing, it's got virtually nowhere to go. It may take years for it to evaporate back up into the house.
What do you think?
Main First Floor<!----><!----><!---->
- Finish Floor
- 3/4" T&G Subflooring, glued and screwed<!----><!---->
- 2x12 Floor Framing w/ R-30 Batt Insulation<!----><!---->
- 2" Foil Faced Rigid Insulation<!----><!---->
- Water-proofing Membrane<!----><!---->
- Protective Cladding (Hardie Panel w/ SS Screws)<!----><!---->
There are a couple of different approaches you can use for the floor.
If the building is on piers and the underside is as exposed to the weather as are the outside of the walls--in other words, no skirt around the crawl space--you treat the floor just like you would the walls: VB to the inside; housewrap and some sort of weather-resistant cladding on the outside.
OTOH, that sort of arrangement is relatively uncommon, usually found only on beach houses or other places built upon a flood plain where it is expected that water will flow under the house on a regular, seasonal basis. Most houses on piers have the space under them closed in by a skirt of some sort, and that changes the way you approach building your floors.
The skirt itself should be insulated to allow you to condition (heat) the crawl space. And you do need to heat the crawl, if only to keep pipes from freezing. The skirt (or 'curtain-wall', so called because it hangs from the framing above and does not support anything) must also have provision for ventilating the crawl space in warm weather so that you won't accumulate hot, moist air under the house and cause mould and fungus to attack the floor framing. The usual approach is cross-ventilation by openable, screened windows in the skirt wall, or screened louvered vents which can be closed tight in winter. The choice between those two approaches is primarily æsthetic.
With an insulated skirt wall, the space under the floors is considered to be inside the building envelope, and so the floor is treated differently to an exterior wall--hence, there often isn't any insulation or vapour barrier at all, just framing and subflooring under the finish floors. In general, when you insulate the skirt walls, you shouldn't insulate the floor itself as you want heat generated in the crawl space to percolate upwards into the house through the floors.
That said, some builders use sprayed in 2-part urethane foam insulation on the underside of such floors. That foam constitutes a vapour barrier in itself, but because it rejects vapour from both sides equally and is essentially hygrophobic throughout its structure, it isn't as subject to the trapped-moisture syndrome as are walls with separate VB components on both inside and outside. While the foam does slow down heat loss from the house towards the crawl space, it has the corollary disadvantage of retarding the transmission of crawl space heat up into the house itself.
There are other arguments against the foam approach: For mechanical reasons, I don't like sprayed-in foam because it makes maintenance and repair on under-floor utilities a veritable PITA.
My recommendation would be to build the floor with the usual top-to-bottom arrangement of finish floor, subfloor, framing, and a sheet of poly vapour barrier. Built that way, the VB will prevent dust, bugs, and ground moisture from migrating up into the floor if you don't ventilate enough...and if there is ever a flood from above, you can easily go into the crawl space and rip off the plastic or puncture it to allow the subfloor and framing to dry out.
Alternatively, though very slightly more complex, you could skip the poly sheeting under the joists and lay it directly on the ground, then cover it with a couple of inches of half-inch gravel and some walk-boards or skids. That will give you a dry 'floor' to the crawl space itself--for dead or seasonal storage--and keep ground moisture out of the house.
Dinosaur
How now, Mighty Sauron, that thou art not broughtlow by this? For thine evil pales before that whichfoolish men call Justice....
If the building is on piers and the underside is as exposed to the weather as are the outside of the walls--in other words, no skirt around the crawl space--you treat the floor just like you would the walls: VB to the inside; housewrap and some sort of weather-resistant cladding on the outside.
Indeed that is the situation. The house is on piers and there is no plan to envelop the crawl space. I am leaning to follow your first advice (above) in your post, rather than your advice at the end. I'm also considering leaving gaps in the polyiso and cladding to let any water drain out. I'm afraid without that, I may not know until it's too late that I've got water building up down there. I would put heavy duty screen behind these gaps to keep the critters out. Your feedback on this approach would be appreciated.
With the "VB to the inside", should I lay it on top of the floor joists just before laying down the subfloor? Or might I use a 4x8 subfloor sheathing material that integrates a good vapor barrier (is there such a thing?), and tape the joints?
Regarding pipes, a water pump and all water lines are designed internal to the house except for the water source line from the lake. Septic pipes all run parallel to and within the floor joists, exit through the header joist, and join outside the house and continue on their way to the septic tank. I may add some insulation wrap on the short exposed section of this pipe. So I don't need a heated crawl space for the pipes.
With the "VB to the inside", should I lay it on top of the floor joists just before laying down the subfloor?
Yes. You can use polyethylene sheeting, or foil-faced kraft. Tape the poly with Glasclad tape; tape foil-faced kraft with aluminum duct tape.
I would not use foam board between the subflooring and the joists because it is not a structural material and the point loads of bearing walls on the subfloor above it will sooner or later cause crushing and consequent settling. At the very least, you'll develop squeaks in the floor; at worst all your gyprock will crack and pop and window and doors won't open or close properly.
If you want the high R-value of polyiso in your floor insulation, the way to do that would be to glue it under the subfloor between the joists, in each joist bay, and seal it to the joists with beads of 1-part urethane foam along each edge.
Then lay your FG batts in under that, sheathe it with ply, osb, or tarred homosote, and finish with the housewrap or felt and 1x3 strapping perpendicular to the joists.
Regarding pipes, a water pump and all water lines are designed internal to the house except for the water source line from the lake. Septic pipes all run parallel to and within the floor joists, exit through the header joist, and join outside the house and continue on their way to the septic tank. I may add some insulation wrap on the short exposed section of this pipe. So I don't need a heated crawl space for the pipes.
This is not ideal, not at all.
First: Your supply pipe from the lake needs to have an internal heating wire installed in it, controlled by a thermostat. Pyrotenax is one supplier; you may find others. Under 90 feet long, the heating wire runs on 120V; over that they require 20A 240V service. The wire must be long enough to reach the point where the pipe is deep enough in the lake to be below the thickest ice that will ever form. For your area, my educated guess is that would be about 18" deep, but check with locals who do ice fishing; they will know better than I.
Second: Your pump being inside the house is all well and good from a mechanical point of view; it won't freeze as long as you keep the house heated. However, if you have never lived in a house with a convertible jet-pump cycling on and off everytime someone flushes the can or opens a faucet, you may not appreciate how annoying the noise can be. At the very least, you should ensure that the pump-room in your house is very well insulated against sound transmission.
Another option is to put the pump in the lake instead. That requires power wiring running down along the outside of the supply pipe, much like you have with well pumps. This is fairly common up here (although far from universal); however there is always the possibility that a pump failure could occur in winter and that can be a fairly expensive nightmare to fix.
Still a third option is to build a super-insulated underground bunker as your pump-room; this can be located anywhere between the lake shore and the house itself, but should be easily accessible for maintenance and service.
Third: Septic/drain lines running in the closed and insulated joist bays will freeze if anything prevents them draining completely dry after each flush or other water use. What often happens is that solids (TP, human waste, etc.) aren't washed completely out of the pipe on the first flush, and freeze in place while waiting for another flush to send them on their way. That frozen lump now constitutes a small dam, and any small water use will build up behind it and freeze. Now the dam is bigger. Next flush, some more solids get stuck behind the dam, and it is bigger still....
You can avoid this happening by running all septic lines through a heated, super-insulated pipe chase built under the floor joists. Alternatively, you can wrap all DWV lines in the joist bays with electrical heating tape, but this will probably require you to specify CI piping instead of ABS or PVC. I don't believe the plastics are rated for heating tape (Bill Hartmann could correct me on that if I'm wrong).
Finally, all this leads me to wonder why you are not going to enclose the crawl space, as that design decision restricts and complicates many of the other aspects of your construction project (as should be evident from the above). Is the house being built on a flood plain? Overhanging the lake itself? Is there some other reason you cannot close and heat the crawl?
Dinosaur
How now, Mighty Sauron, that thou art not broughtlow by this? For thine evil pales before that whichfoolish men call Justice....
121293.14 in reply to 121293.10
If you want the high R-value of polyiso in your floor insulation, the way to do that would be to glue it under the subfloor between the joists, in each joist bay, and seal it to the joists with beads of 1-part urethane foam along each edge.
Then lay your FG batts in under that, sheathe it with ply, osb, or tarred homosote, and finish with the housewrap or felt and 1x3 strapping perpendicular to the joists.
This could work. I'd be a little concerned with the joists conducting heat though, since in this approach there is no insulation at their bottom edge. I suppose if I dragged myself through the calculation I might find the heat loss through the joists is minor. I like your idea of holding everything up with the 1x3s.
First: Your supply pipe from the lake needs to have an internal heating wire installed in it, controlled by a thermostat. Pyrotenax is one supplier; you may find others. Under 90 feet long, the heating wire runs on 120V; over that they require 20A 240V service. The wire must be long enough to reach the point where the pipe is deep enough in the lake to be below the thickest ice that will ever form. For your area, my educated guess is that would be about 18" deep, but check with locals who do ice fishing; they will know better than I.
Excellent. Similar to what you describe, what I'd really like to be able to get is a rugged double-walled pipe with insulation between the inner and outer pipes and the heating wire either within or wrapped around the outside of the inner pipe.
Second: Your pump being inside the house is all well and good from a mechanical point of view; it won't freeze as long as you keep the house heated. However, if you have never lived in a house with a convertible jet-pump cycling on and off everytime someone flushes the can or opens a faucet, you may not appreciate how annoying the noise can be. At the very least, you should ensure that the pump-room in your house is very well insulated against sound transmission.
I have indeed lived where the pump was in the house. I tore down that house to start this project. The noise was no problem at all. And the room it was in had no insulation at all. In the new place, the room will be insulated. The entire water system will be readily drainable when no one is there in the winter (which will be most of the time).
Third: Septic/drain lines running in the closed and insulated joist bays will freeze if anything prevents them draining completely dry after each flush or other water use. What often happens is that solids (TP, human waste, etc.) aren't washed completely out of the pipe on the first flush, and freeze in place while waiting for another flush to send them on their way. That frozen lump now constitutes a small dam, and any small water use will build up behind it and freeze. Now the dam is bigger. Next flush, some more solids get stuck behind the dam, and it is bigger still....
You can avoid this happening by running all septic lines through a heated, super-insulated pipe chase built under the floor joists. Alternatively, you can wrap all DWV lines in the joist bays with electrical heating tape, but this will probably require you to specify CI piping instead of ABS or PVC. I don't believe the plastics are rated for heating tape (Bill Hartmann could correct me on that if I'm wrong).
All the septic pipes actually run parallel to the joists, so it has been my intention to build such a pipe chase with extra insulation within the floor. I think you are saying that I should plan on adding some heat to this chase too. I will need a heated pipe chase outside too. This all seems workable.
Finally, all this leads me to wonder why you are not going to enclose the crawl space, as that design decision restricts and complicates many of the other aspects of your construction project (as should be evident from the above). Is the house being built on a flood plain? Overhanging the lake itself? Is there some other reason you cannot close and heat the crawl?
The house rests on the side of a large hill with considerable water cascading down the hill in the upper 3 foot organic layer (below that is hardpan, and nothing gets through that). This makes for a fairly damp region under the camp. If I installed a curtain drain above, this would help but not solve the problem. I prefer just to keep it open. It will look better when open too.
I suppose if I dragged myself through the calculation I might find the heat loss through the joists is minor. I like your idea of holding everything up with the 1x3s.
The heat loss through the joists is minor, and almost unavoidable unless you want to go to the trouble of building a staggered, double-joist floor system with one set of joists holding up the floor, and the other set--to which your bottom sheathing will be attached--1" lower than the first on the rim joist. Alternatively, you could use cedar joists. Cedar has a much higher R value than standard SPF framing lumber...but you'd need your engineer to spec the joist depth as I don't believe cedar joists appear in any of the standard code tables.
You don't really need the 1x3's if you use plywood sheathing and the joists are on 16" centers; you will need them if you use OSB or homosote.
Similar to what you describe, what I'd really like to be able to get is a rugged double-walled pipe with insulation between the inner and outer pipes and the heating wire either within or wrapped around the outside of the inner pipe.
Way too much trouble. The Pyrotenax heating wire goes right in the supply pipe; it is waterproof and designed specifically for this type of application. They are good for 25+ years. The control thermostat is usually mounted in the basement, where the supply pipe comes through the floor slab. In your case, it should be mounted in your pump room, and the sensor bulb (which is on a 5'-long wire) should be strapped to the outside of the supply pipe below the floor, where the pipe will be exposed to the coldest temperatures. You can/should wrap pipe insulation over the pipe and sensor bulb where it is exposed to the open air; the bulb will sense when the cold gets through the insulation and turn on the heating wire to prevent the water in it freezing.
...it has been my intention to build such a pipe chase with extra insulation within the floor. I think you are saying that I should plan on adding some heat to this chase too. I will need a heated pipe chase outside too. This all seems workable.
Yes, you do need to have active heating inside the pipe chase, no matter how much insulation you put around it. Insulation does not create heat; nor does it prevent heat loss. It merely slows down heat loss...and without flow-through ventilation from a heated space in the entire pipe chase--or some active heating elements actually inside it--whatever heat is in the pipes and chase will eventually leak out through the insulation and allow the pipes to freeze.
The chase is what should be insulated here, not the pipes themselves. Leave them open to the heated air inside the insulated chase.
The house rests on the side of a large hill with considerable water cascading down the hill in the upper 3 foot organic layer (below that is hardpan, and nothing gets through that). This makes for a fairly damp region under the camp. If I installed a curtain drain above, this would help but not solve the problem. I prefer just to keep it open. It will look better when open too.
There are ways to deal with that water--mostly by allowing it to run under the house in a way that won't bother you, such as through a gravel bed topped with plastic sheeting--but if you prefer to keep it open, and are willing to do the other things that that decision entails, it's your call.
Dinosaur
How now, Mighty Sauron, that thou art not broughtlow by this? For thine evil pales before that whichfoolish men call Justice....
What is the climate? You only list NE, which can vary a lot from the southern part to the far northern.And where did the plans come from? Or they specific to your area or they generic?What kind of "vapor retarder" where you planing on using.You know that DW can be a vapor retarder if certain specs are followed?I would do some wonder around over at http://www.buildingscience.com.
William the Geezer, the sequel to Billy the Kid - Shoe
House is in southern portion of the Adirondack Park in NYS.
Plans are from my architect with input from an engineer.
I have not yet selected a specific vapor retarder.
When you say DW, do you mean this http://www.insulationsolutions.com/products/radiantshield/information.html?
Thanks for the link!
I am talking about Air Tight Dry Wall. Most moisture movement is through air leaks and not materials. AT DW is a method of sealing the DW so that air and thus moisture does not move past it.One advantage is that it can still dry out via the DW. With something like poly for a vapor retarder the wall can't dry out to the interior and with the polyiso to the exterior.Check the climate maps on Building Science, but your area might not need as much AC or be as humid as say coastal CT..
William the Geezer, the sequel to Billy the Kid - Shoe
I see furring strips on your list - I'd forgotten about that. I could rip from plywood 1/2" x 2" strips (or so) and nail those to each stud through the housewrap and polyiso. Then nail the cedar with a long enough nail to go through the furring strip, through the polyiso, and into the stud. No more "nailboard".