*
I would think that with the right adheasive you could easily make your own panels. OSB is easy to find and the adheasive comes from Ashland Chemicals, but I cannot find 6 inch expanded polystyrne yet. Does anyone know how to make these things or have you met someone who has made them Before? A guy from a panel company says you only need 7 1/2 lbs/per 2 inch for pressure, so that is easy enough to do with a couple of torsion boxes of MDF and a clamping system (like a big veneer press. I want to make my shop out of them and if it easy enough, a house eventually….
Discussion Forum
Discussion Forum
Up Next
Video Shorts
Featured Story
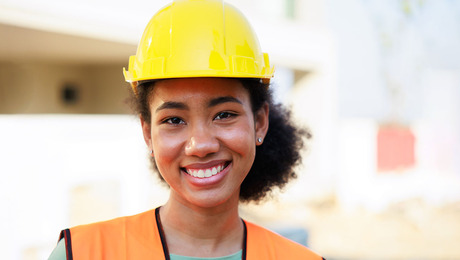
The "She Build" initiative is empowering women in Seattle, WA by ensuring they have safe, healthy homes.
Featured Video
How to Install Cable Rail Around Wood-Post CornersHighlights
"I have learned so much thanks to the searchable articles on the FHB website. I can confidently say that I expect to be a life-long subscriber." - M.K.
Replies
*
J Kent;
I ask this same question 3 months ago with no success.One web site I visited did talk about their system using an adhesive called "isoset".
I believe a better way to force the panels together during curing might be by vacuum.I believe "Finehomebuilding" covers the manufacturer that offers this procedure but I could not locate the issue.
My thoughts were to adhere large sections of plastic together to create a bag large enough for the panel.Once the panel is inside the hermetically sealed bag you need a vacuum sorce.Mine would have been a tool sold by Harbor Freight using compressed air and using a principle called air ejection to create the vacuum.Simple process using a $25.00 tool.Atmospheric pressure I belive would have generated the pressures required.
I never tried the procedure but it was a plan !!!
Good luck:
Don L.
*
J Kent & Don
Having never done the panels, I cannot intelligently comment on your desired results, so I won't, other than to place a WAG at the end of this post. That being said nothing in this world is impossible (except for skiing through a revolving door :) ) providing you find the right info. Trying is what made this country great, but the R & D part of the equation is rarely economical for a one or two time deal. That being said heres's a couple of thoughts from an industrial oriented person. Do with them what you may, just don't hurt yourself, or kill the family, in the process.
The "air ejection" deal you talk of is a venturi. It's really a simple concept, but uses extreme amounts of air. Venturies are only reasonable if you have many many CFM's of free compressed air. You need WAY more vacuum to glue 4 X 8 panels. I am guessing here since I don't know the adhesive you'll be using, that you'll also need the vacuum quicker than the venturi will produce with a "normal" sized compressor. Since you only need 50% vacuum to achieve the 7-7 1/2 psi clamping pressure (pressure claimed in previous post), you might be able to try a shop vac.
The Industrial way of handling this, taken from working on air and vacuum piping in sign shops, is a reservior and a small vacuum pump. To do the large signs, Like HD or Mickee D's arches, they have a vacuum reservior attached to the clamping table. During their setup, a small vacuum pump is pumping their tank empty. When they have the plastic hot enough to make a shot, they place it over the pattern, seal the edges, and open a large valve from the reservior to the table. After the shot, while they heat the next sheet, trim the plastic, set the patterns, etc, the vacuum pump goes back to evacuating the tank. This is a much more economical system. It would be time consuming, but small vacuum pumps are often reasonably priced.
Now, My WAG on the commercial panels:
I think a little research might show that the panels aren't "glued" in the normal sense of the word. I have a feeling that the panels are fabricated by injecting and expanding the polystyrene or whatever between the two panels. It is actually cast in place, and bonds to the wood layers as it sets. Very similar to spraying the "Great Stuff®" foam between two pieces of wood, in a very controlled process. It is very likely that this is done as a continuos process on a linear machine that feeds the panels, and foam onto rollers, then sizes them as they continue down the line.
Scott
*I don't understand why you want to try to make your own panels. You will not save much in material costs. Stress skin panels are structurally rated because the foam when it expands between the panels is actually forced into the surface of the OSB not just glued onto the surface.
*
I would think that with the right adheasive you could easily make your own panels. OSB is easy to find and the adheasive comes from Ashland Chemicals, but I cannot find 6 inch expanded polystyrne yet. Does anyone know how to make these things or have you met someone who has made them Before? A guy from a panel company says you only need 7 1/2 lbs/per 2 inch for pressure, so that is easy enough to do with a couple of torsion boxes of MDF and a clamping system (like a big veneer press. I want to make my shop out of them and if it easy enough, a house eventually....