I have a friend who need some bookshelves built around a big screen tv.
He wants to paint them, do ya’ll think that MDF spanning 42″ with a 1×3 front a back will be okay at that span. trying to do it as costa effective as possible because the whole cabinet will be 18 feet wide.
Thanks
Discussion Forum
Discussion Forum
Up Next
Video Shorts
Featured Story
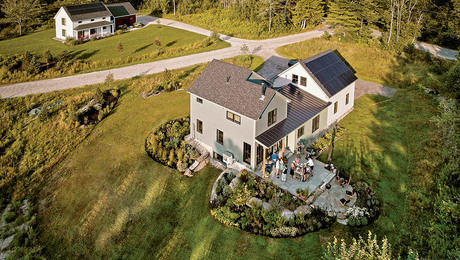
By considering things like energy-efficient mechanicals, window orientation, and renewable energy sources, homes can be evaluated to meet the energy codes. Here's what the IRC has to say.
Featured Video
How to Install Exterior Window TrimHighlights
"I have learned so much thanks to the searchable articles on the FHB website. I can confidently say that I expect to be a life-long subscriber." - M.K.
Replies
We use painted MDF all the time.
We always apply a 3/4 x 1-1/4 hardwood lip on the front. This will help with the deflection and it gives the shelf a sturdier look. The rail on the back can be whatever.
Thanks, for the answer. Do you think I should do away with the 1x3 and go with a 1x2 instead?
Type/size of TV ? I just bought an LCD for my father: 23", very light; OTOH, our big plasma weighs about 150# - size the "lip" for the weight of the TV.
<!----><!----> <!---->
Phill Giles<!----><!---->
The Unionville Woodwright<!----><!---->
The tv is just going to go between shelves it is a rear projection or an LCD I don't remember which, but the shelves a being built around that, the tv will rest on the floor.
you do appreciate the weight of MDF, even liteweight MDF? and the dust mess it makes in working it?
bobl Volo, non valeo
Baloney detecter WFR
That's a large span for MDF.
It'll be stiffer is the sides are captured instead of simply resting on shelf supports, it'll be stronger if the back edge of the shelf is attached to the rear of the cabinet, it'll be stronger if the front edge is given a hardwood edge.
Not knowing what's going on the shelf, I'd plan for the worst.
I'd try to capture both sides and the rear of the shelf.
I'd use a wood like poplar (poplar is good paint grade material and economical) as a front trim piece on the shelf.
42" is a fairly long span for MDF, to keep the shelf in scale maybe make the poplar edge piece 2-1/2" wide, rabbet it, and glue/fasten it on the front edge of the 3/4" MDF shelf.
That leaves 1-3/4" of free space behind the poplar edge, in which I'd install a 1-1/2" piece of angle iron or square steel tub as an additional stiffner.
Nothing uglier or more embarrassing than a sagging shelf.
Mongo
I was going to rabbet and glue in a 1x3 premium grade pine front and back of the shelves and the end will also be in dados. all he said would be on them is dvd's.
Any furniture built out of MDF or chipboard is destined to go to the landfill sooner rather than later.
If you are going to the trouble of building a unit 18 feet wide, make your friend spring for better materials. I am sure you will be giving him a good price as you sound like you are just beginning to build.
If you are going to build furniture, make stuff you can be proud of 30 years from now.
Oh please!
He said painted....do you recommend birch plywood?
If so, the purist before you insisted on glued up panels. And so on.........
We've done numerous pieces all three ways and if it's getting painted, we use MDF. Not chipboard or partical board. MDF is a different animal.
why? Because it's the most stable, economical and will last. I would go as far to say that it would be just plain stupid to use anything else. You can join it, raise a panel, run it through the molder.........just have the very best dust collection system.
Crazy Legs even did some stair treads with it.
I think building furniture in solid wood or ply is far from stupid. I do not have much regard for formaldehyde glued together sawdust. Does it still outgas for 10 years or more? I believe the non outgassing MDF is not widely available. I would definitely suggest birch plywood, especially because he would have more options than just painting. Plywood might be a better choice for a beginner also.I was also assuming he was going with a painted finish to save money for the customer, a few hundred dollars more for a large project might be better in the long run.
<<<I think building furniture in solid wood or ply is far from stupid. I do not have much regard for formaldehyde glued together sawdust. Does it still outgas for 10 years or more? I believe the non outgassing MDF is not widely available.>>>You're right about using precautions when you are milling MDF -- dust mask, dc, goggles --but you should use those same measures when cutting anything these days. The rep that MDF has for outgasing is a tempest in a teapot. Virtually all the gas has dissipated 30 days after manufacture, which is about the time it arrives in your shop. After that, the outgasing is negligible. If you're concerned, one just has to make sure all surfaces are at least primed -- sides, back, etc. If one is concerned about formaldehyde, there are many other products that represent a significant risk for those who are sensitive. But painted MDF is not one of them.********************************************************
"It is what we learn after we think we know it all, that counts."
John Wooden 1910-
Hey, I like quality wood products, and working with birch ply is ok, but mdf can be great , and as far as offgassing, the museum industry uses medite and medex all the time, (an archival version of mdf)
its stable and needs no extra prep besides paint. Plywood on the other hand requires vapor barriers to take care of volitity to certain art materials.--If Van Eyck couldve bought medite, he would have, and his paintings would look as good as the poplar panels he used 600 years ago.-art guy
I was going with a painted finish because that is what they wanted. I they wanted it I would bend sheet metal for shelves if they would psend the money.
I have had good results with butt and end joints using biscuits and glue. However, the painting piece is more difficult - trying to get the surface to feel 'flat' is hard. Rollers leave the orange peel and brushing can leave stroke marks. I finally got smart and found 3/4-inch MDF with mellomean on both sides. If you like white it's great, if you don't, it takes a primer & paint pretty well. Or you could laminate a finish with a Formica.
Offgassing is basically a non-issue now with most of the particleboards.....the companies have done a huge amount to reduce the offgassing.....plus, the decay curve is steep, and given the time it takes to get delivered to your shop, emmisions are very, very low when you get it. Once you seal it, even less....I've got a new research report on my desk that looks at the effectiveness of different barrier coats including paint and they do work.
A friend of mine brought an air quality guy into his commercial shop....they took no special precautions, they wanted to know what the emissions were under normal conditions, cutting the materials they normally worked with. They had the sniffer set to 1/10 of the 'safe' level, which itself is buffered.....couldn't get a sniff all day. The commercial shops are having to deal with LEED buildings now where the architects are speccing no-formaldehyde materials.....which have to get right across the continent to us here.....when low-formaldeyhde materials are very safe.
I agree with the others; very fine quality work can be made from MDF.
To the original poster: here are some shelf deflection numbers to ponder from the AWI manual...all are for a 1/4" deflection by total distributed load in pounds...
3/4 medium density particleboard, 12" x 42"=43 lbs
3/4 MDF, 12 x 42=54lbs
3/4 particleboard with 3/4 x 1 1/2 solid lumber dropped edge=152 pounds
they don't have a number for MDF with a lumber edge, but compare the raw particleboard and MDF numbers, and it would be higher than the 152 lbs.
You can also add a lumber edge to the back of the shelf if you want.
Cabinetmaker/college woodworking instructor. Cape Breton, Nova Scotia.
So what would you use to attach into the MDF? My experience has always been that mechanical fasteners are somewhat limited in usefulness. Biscuits and glue? A few finish nails to keep it set? I've heard of special MDF/particle board screws, but haven't tried them.
Biscuits and glue work great; double the biscuits (one above the other) for more strength. Confirmat screws or some of the other knockdown fasteners are incredibly strong; you see very high quality furniture built with them in Europe. I also use particleboard screws a lot (sometimes called Hi-Lo, Lo-root, etc.). There is a world of difference between them and regular wood screws. Any cabinet supply house will have them.Cabinetmaker/college woodworking instructor. Cape Breton, Nova Scotia.
We let the shelf into the back (even a 1/8" dado will support MDF) and it's good for about 150# for 48" span with a 1.5" bread-board front edge. For more than that we 'bond' a 1/2" of styrofoam between 2 x 1/2" sheets to make a 1.5 inch shelf.
<!----><!----> <!---->
Phill Giles<!----><!---->
The Unionville Woodwright<!----><!---->
I know what a breadboard end on a glued up solid wood top is....what's an "1.5 breadboard front" on an MDF shelf?
A piece of solid wood added to the edge of an MDF or ply panel.
<!----><!----> <!---->
Phill Giles<!----><!---->
The Unionville Woodwright<!----><!---->
My friend has a shop that makes high end casework for some of the wealthiest folks in Baltimore. Some of his nicest stuff was made out of mdf with a lacquer finish. Absolutely, out of this world, gorgeous.View Image
I have some wealthy customers also, one of them had a container load of teak delivered to his house 30 years ago. I have just about used it up on many projects over the years. There are 7 or 8 boards left, 18 feet long 3 1/2 thick and 36 inches wide.Maybe I am a wood snob but I don't think MDF has any intrinsic value. Those teak desks and tables I made should last 300 years or more while the MDF will have long decomposed in a landfill some where.
And your point is?? Lighten up some on the other guys!
You are right, I regret voicing my opinions about what other people do as far as woodworking. All craftsmen are engaged in honorable work.
As a guy who cuts up way more plywood than teak or MDF, I would like to turn the argument into onfe concerning the enviromental impacts created by cutting all of those teak trees down, and shipping them to your location. Quality is always something to strive for, but economics sometimes limit the choices of materials.
My suggestion would be to put front and back trims on edge, and make the customer promise to limit the weight to a reasonable amount, put the heavy stuff on the other shelves.
Dan
The teak I was working with was shipped here 30 years ago. It is super expensive now and hard to find anyway. Putting in dividers would help by cutting down the spans.
Holy Crap! He said he needs to make some painted shelves and some of you are telling him to build something that could go into the Smithsonian. To the original poster:MDF works fine and gives you one of the smoothest finishes. If a divider can be used in the center, attached to the top, it won't sag, especially if it's in a dado. Add the 1"x2" to the front edge, rout whatever profile you want and make sure the raw edges are well sealed. Poplar works great for this, as was mentioned before although it's stringy, sometimes. Nothing a little filler won't fix. If you can spray the finish on this, it'll look best- otherwise, use really good paint and the best brushes you can get. Wear a good dust mask whether you have a collector or not. You won't find dust that's much finer than this. If you haven't made anything like this before, there are some good books out there that deal with shelving units and cabinets. If you'll be using a face frame, do that before you make the carcass.
"I cut this piece four times and it's still too short."
Quote"All craftsmen are engaged in honorable work." As are you my friend.
MDF works great for shelves, but not for the span you stated.
Many who climbs on the mdf bandwagon fail to recognise that mdf will slowly sag for a significant amount of time so just because it's straight today doesn't mean it will stay that way 5 years from now.
I have build cabinets that spanned slightly over 3' with MDF but that's only with oak on the front and rear edges.
I've worked with MDF for a year, but all my painted cabinets and shelves are now back to birch ply. Ply will just take more abuse.
There are some projects that are good for mdf, but 42" shelves just aren't one of them.
32" would be much better and if the shelves are going to hold books 24" is better still.
Beer was created so carpenters wouldn't rule the world.
We've built a lot of stuff out of MDF and often times we will double the MDF up to make shelves, heavy as hell but they dont sag. 42" is fairly wide, is it possible to shorten that width?
Doug
Everywhere you look will say 42" is to far to span with MDF.
Could you add a 2" center stile in each span running top to bottom. It will effectively break the span in half.
Still face the front of the shelves.
Just because the person says they will put CDs on those shelves doesn't mean someone else won't put books there later. 42"? That's clearly too long a span for 3/4" material. I have always thought 30" was just about the maximum span for 3/4" 9 ply plywood. MDF? No way I'd try to span 42".
I did some interesting tests a few years ago and was surprised that over a month 3/4" MDF actually sagged less than 9 ply birch plywood under the same load of magazines. I still have reservations about using it for shelving, though -for the long term sagging issues someone mentioned earlier.
Another option I didn't see mentioned, that works with any sheet goods, is to build a box beam. Use whatever thickness you want, 1x1, 1x2,1x3, lattice arrangement sandwiched between 2 sheets of MDF or whatever. The shelves can be made any thickness using 1/4 or 3/8 MDF skins and should be much stronger than 3/4 MDF with a 1x2 or 1x3.
Be sure to use the same thickness and material for the skins or they will warp. Glued and screwed together you could span 8 feet with the right thickness core. The possibilities are endless. Time and materials will be more but as an amateur I don't care.
>"...build a box beam. Use whatever thickness you want, 1x1, 1x2,1x3, lattice arrangement sandwiched between 2 sheets of MDF or whatever. The shelves can be made any thickness using 1/4 or 3/8 MDF skins and should be much stronger than 3/4 MDF with a 1x2 or 1x3."Nota, I call that a "torsion box". It might be more work than the O.P. wants here, but it is a cool thing to know about. I made a low profile platform for my bed ("california kingsize") using 1/2" ply ripped to 1" strips arranged in a 1 foot grid. I skinned it with 3/16" pegboard attached with brads and gorilla glue.Without the matress it looks like an air hockey table, but it's amazingly rigid. the head is attached to the wall at two points 18" from the floor, and when visitors look underneath they see that it's supported by a single stack of books near the center (casually aranged, for effect). It blows their minds when I stand on the outside corners with no deflection. RE: the original post- MDF should be primed with a solvent based product because water based paints can cause it to swell. For shelving I would topcoat with a durable alkyd (oil) paint.