*
I will say it how I was taught it from the mother…THERE IS A TIME AND PLACE FOR EVERYTHING…I think just because this is the Fine Homebuilding site that that sums it all up for some ….well the don’t call them “starving artists” for no reason. We should get a tow truck and pry the sticks out of some asses around here. Some people will pay for the best, and for them I will shine, some don’t know the difference and won’t pay for it regardless, for them I will hack out what they desire, but in the end I will eat well, and my kids will wear nice clean cloths and have full tummies and be loved regardless of what I did today. Keith C.
Discussion Forum
Discussion Forum
Up Next
Video Shorts
Featured Story
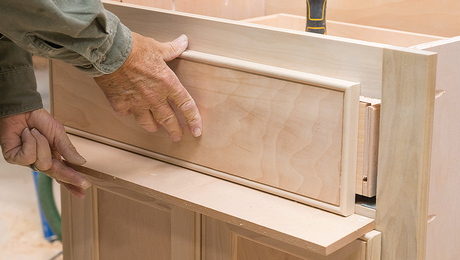
From building boxes and fitting face frames to installing doors and drawers, these techniques could be used for lots of cabinet projects.
Featured Video
How to Install Exterior Window TrimHighlights
"I have learned so much thanks to the searchable articles on the FHB website. I can confidently say that I expect to be a life-long subscriber." - M.K.
Fine Homebuilding Magazine
- Home Group
- Antique Trader
- Arts & Crafts Homes
- Bank Note Reporter
- Cabin Life
- Cuisine at Home
- Fine Gardening
- Fine Woodworking
- Green Building Advisor
- Garden Gate
- Horticulture
- Keep Craft Alive
- Log Home Living
- Military Trader/Vehicles
- Numismatic News
- Numismaster
- Old Cars Weekly
- Old House Journal
- Period Homes
- Popular Woodworking
- Script
- ShopNotes
- Sports Collectors Digest
- Threads
- Timber Home Living
- Traditional Building
- Woodsmith
- World Coin News
- Writer's Digest
Replies
*
I will say it how I was taught it from the mother...THERE IS A TIME AND PLACE FOR EVERYTHING...I think just because this is the Fine Homebuilding site that that sums it all up for some ....well the don't call them "starving artists" for no reason. We should get a tow truck and pry the sticks out of some asses around here. Some people will pay for the best, and for them I will shine, some don't know the difference and won't pay for it regardless, for them I will hack out what they desire, but in the end I will eat well, and my kids will wear nice clean cloths and have full tummies and be loved regardless of what I did today. Keith C.
*
I would love to be able to spend lots of time making everything perfect. I picture the painter/room mate on Murphy Brown. No need to get the job done. Just paid until it's done, no matter how long it takes.
Unfortuantely, I've never met Murphy Brown. I've got to provide the best I can within the client's budget.
*Hate to be the one to break the news to you, Dan. But you've only been gone for three months. Obviously, whoever sold you that six month trip ripped you off.Funny that your back now, I was just wondering about you a couple of days ago.Rich Beckman
*We try to do the best quality for the best price. Sounds like a cop out. Some times we do not make a lot of money. I guess I should say I do not make a lot because my employees always get paid and I can get real picky. See my thread, should employees pay for mistakes.
*Quality work, fair price. One guy. You want more, you get more, you pay more. You want less, hire your brother in law. Referral only. Many repeat customers.How bout those folks that ask you to stop by when you have a lull. You know, come when you're not busy and THEY will help you feed your family. They'll be waiting a while. Hoping the trend to spend money lasts a long while.
*Hey, of course he's a little spacey -- he's expecting his first kid! Congrats, and happy Father's Day!
*I'm with Calvin. The only price variation is materials, never quality. They want shlock, there are other people who will do it. No hard feelings.That's just the way life is.SHG
*Ok, Ok, Mabey I stirred too much doo doo up, or stated it the wrong way. My only true complaint was the price people are paying for the work (house) they're getting. 250 thou. is too steep for the stuff being built with mdf type materials.I understand the theory of "getting what you pay for" and its just my opinion that unknowing people are getting the shaft.Remods are different from the standpoint that you will accually sit down with the person to develop a gameplan or budget to work with and build from there, versus a new home buyer from Ohio (or wherever) who will never meet the developer who's sitting in the Bahamas sucking down cold ones, thinking of the outrageous amount of money he's making per house.Keep in mind were talking about tracts with no less than 500 houses per stage, multiple stages!I guess I'm just used to better built stuff, and not taking the people to the cleaners so hard. Definitely not used to punch lists like we see on a constant basis, and defintely not used to guys just not giving a damn. Sorry for getting such an uproar going on two threads at once, I really did'nt mean to.
*Chris R,
View Image © 1999-2000"More than any time in history mankind faces a crossroads. One path leads to despair and utter hopelessness, the other to total extinction. Let us pray that we have the wisdom to choose correctly." Woody Allen
*I also do a one-man-band type of business. I consider myself fortunate to be able to meet the variety of people that I do, and consider the service I provide as my contribution. It would be nice to think that the better the quality of work the higher the return, but it's the quality that gets me in the door. The market determines the price and unfortunately ( as Joe related ) the selling of the job. I only say unfortunately because the market area that I'm in doesn't allow high markups, but there is always the satisfaction of the job well done. { Did I really say that? } Work hard, be happy!
*
Part of being a good contractor and carpenter is knowing when to worry about a sixteenth variation. I've seen carpenters spend hours trying to get rafters on exactly the same plane. Being a good builder requires us to know how precise we need to be at each stage of construction. Striving for perfection in Northern California .. Happy Fathers Day to all you hard working Dads, Bill Popow
*
I'm not sure how you guys adjust your standards to fit the customer. I try to work to MY standards, and the bar keeps going up. That's the only way I know to build a reputation that will attract the customers who want the quality of work I want to do. If I go home knowing I didn't do my best, I don't sleep very well.
Certainly, there are different standards for different types of work, but one of the main reasons I am in business for myself, instead of working for a real contractor, is so that I can work to my own standards, not someone else's. I always hated that.
*I'm a little surprized by some of the responces to this discussion.The price of any project should not be determined by the quality of one's craftmanship. The diferences in pricing are in the details and size.If I build a deck for Big Daddy big bucks who wants to have cocktails with his friends and every trick and gadget he can think of or Joe the mechanic who wants to bbq dogs for his kids, my carpentry looks the same. Joe's is in pressure treated,Big Daddy got red wood, Joe has 12 x18 and a set of stairs ,Big Daddy got three levels, a hot tub,built in bbq , two sets of stairs and 1500 sq. I'm proud of both projects,one cost way more but both are done to the same standards.Both were priced with those standards in mind. It costs me the same amount of money per day to run my buisness no matter where we are or what we're doing. Quality is a state of mind not a result of price. Vince
*I think we all disagree on what constitutes Quality.The deck for "Daddy Big Bucks" will get routed edges, a trim board installed around the deck boards, decorative finials on the posts, hidden deck fastners, custom made handrails.The deck for Joe Mechanic won't. I think that means the two decks were built with different "Quality".Some of you are saying that these two decks are still getting te same footings, the joints are just as tight, the flashing detail is just as good so these are being built with the same quality. Semantics again.I just saw a rental owner about replacement windows. She was VERY clear that she wants no frills on the window install. I explained how I wrap the exterior of the window with aluminum. She said not to do that. She wants cheap!!!. I gave her a bid for exactly the work she wanted, the "quality" as I define it will be low. I'll still insulate, caulk, flash where needed, make sure the windows are square and the the interior stops are tight. Am I providing quality or not?
*Well said Jim, I'd have to totally agree as my situation is quite similar.
*joe fuscoe.. missed ya.. and it's posts like that that i miss.. and ryan.. yup.. i agree.circumstances, materials and budget (time budget and money budget) all have a bearing on the quality...if the 1830 house yur installing the bath in has a 3 inch dip in the bath floor and no way of jacking up the ceiling below.. how ya gonna fix it ?if yur matching to red cedar courses out of level.. how do you tie in ?nah, quality has to vary with the job.. both in terms of workmanship and materials...this level of expectation has to be communicated prior to starting work so there will be no misunderstanding...remember the guy from ten years ago who swore all he would ever frame with is doug-fir... wonder what he's framing with today ?b bestyacanchagot...
*I'm with SHG,We will buy cheaper materials to try to keep cost down, but that's it.Case in point - We just started the trim and cabinets on a very large home in the most expensive part of town. The builder says to do everything I can to keep the cost down. Instead of "A" grade, I bought FJ stock mouldings. I didn't go as far a buying MDF S4S for base and such, but I did buy poplar instead of white pine. The kitchen will be quarter sawn white oak stiles, rails and doors, but the interiors will be plain sliced white oak instead of quartered. The joinery and construction of everything will be as we always do; the best we can. However, I was able to save quite a bit of money for the customer by buying less than top shelf material. The materials are still good, and will paint and stain up fine, but they weren't as expensive as they could be, and I feel the finished product will be the same. This will make the customer happy.Another case in point - We will start another job in a few weeks where the customer wants everything to be the best money can buy. I mean "everything". #1 fir for framing materials, marine grade plywoods for sheathing, imported exotic hardwoods, handmade finish hardware.......everything. This will make that customer happy. Material is the only place the budget has a fudge factor. The quality of the workmanship that goes into installing the materials is always the same.David, as to your question: We are a subcontracting company in Dallas, Texas specializing in trim and cabinets for high-end home builders. We curently have 20 carpenters on the payroll and a full cabinet shop. But even back when it was just me and two of my buddy's swinging hammers and working out of our trucks, the quality of the workmanship was the same.Don't skimp on the workmanship,Ed. Williams
*Bill, I got an "unknown user" bounce when I tried to e-mail you...I used to live out there, in S.F. and L.A.; now in VA. If you're anywhere near the bay, is work unusually expensive around there? I know about the labor shortage, and the extra work for seismic codes. Just that a friend got three replacement medium-size sliders and a mini-bay -- all vinyl -- installed, plus some rot work around one, for $7,000. Is this "expensive"?Still clueless how people quote things ... the 200 sf. "caboose style" hot dog shack down the road mentioned they got exterior painting quotes ranging from $800 to $3200. They went with $800, I'll see how it turns out.
*
Knew a doctor once with the same attitude.
*
Jim thanks for putting it like You did. I was trying to figure if I was missing some button or after market feature that would allow me to make precise adjustments to quality based on what a job pays. I always try to do my best. In the work I do referals are everything. Quality is the one thing that stands on it's own. I believe you can go over budget ,or miss a deadline and survive but if You don't have the qualtiy you've got nothing. That's my opinion. Skip
*Ryan, routed edges and fancy materials have no bearing on quality. Call it workmanship or whatever but quality shows when Big daddy is looking at poor joinery, planes that are out of plumb or level, while Joe is standing on a solid deck with square cuts even if his lacks the frills. Materials and methods change but principles and qualtiy never do. INMHO Skip
*First of all let me start out by saying, I do not have a magic button that I can press and change the level of quality that I produce. A few more strokes of a rasp of one more trip to the miter saw does not slow me down. I can generally out work any of my crew in both quality and speed. I do not have enough hands or hours in the day to get all of the work done. Hince Employees, every carpenter and helper has a different level of workmanship. If the lessser carpenters want to get better, do I let them run 7" cypress crown, no they run 5 1/4" MDF on a paint grade job. They learn, if they screw up bad not a lot of money wasted, and minor opps get caulked.Many of you said that the only area you would cut cost in is materials. Vincient are you going to build that deck for Joe out of #2 pine. Are you going to have perfectly fitted joints in the masonite siding. Lets not go overboard, this differance in the level of quality is not that great.What do you think people are going to remember, the perfectly mitered exterior trim, or the rotten siding. My clients know that they are not getting redwood siding, but I would sleep better at night knowing that they will get Hardi with slightly sloppy joints(hidden behind caulk) then giving them the highest quality masonite job.When I meet with a client on a tight budget, I know that even if I cannot give them perfect quality, they are still going to have someone do the work. I know that the work I give them will be correct and better than they would get from some hack willing to cut corners. When we cut corners, its the one that get hidden behind caulk or paint, not the ones that cause cracks, rot, and possible hazzardous conditions.Finally, as Ryan said maybe we all disagree on what quality means, but do I go home everyday feeling like I have give my clients my best quality. YES I am fortunate to work with wealthy clients most of the time, but the best referrels I get are from the 27 year olds that did not have a lot of money, but they cannot stop talking about how helpfull we were, and how we helped them choose the right materials, and told them were they could cut corners. These clients get us mom and dads A+ house, or the bosses $80,000 kitchen remodel. Ill sleep well tonight and into the future knowing that our quality is were it counts in all price ranges.
*I have to agree with Vince. Out here competition is tough. With me being a one man operation a large per cent of my customers come from refferals. To build cabinets for an average size kitchen takes me about 3 weeks as compared to 1 week for the larger cabinet shops. Yet, I have some builders that will wait the 3 weeks for me to build them. Their reason? Attention to minor details which produces a quality end product. Whether it be lower cost paint grade cabinets, or fine hardwoods, my quality is the same.
*Mad Dog as a one man operation you have the luxury of knowing that everyone is putting out the same quality. Do you build your cabinets with full tenons, or stub. Do you use nails or screws. Dovetails or dowels, or just butt joints. Very few people build(for profit) a cabinet door with a full tenons, glued face frames, morticed glued backs etc. Some people would say anything less is not a quality product. Your quality may be the same for all of the work you do, but in a controlled shop without employees, that is not a hard task to obtain. As I said rarely does MY quality vary, but the company has to adjust to the work at hand and the hands working.
*My quality does vary on the size and price of the job. When I build those HUD houses with panelized construction, I put the panels up as they are sent. No, I do not waste my time trying to resquare what they sent out that is out of square. When they send the trim package out with the pre-cut mitres, that is what hits the wall, no recuts, no block planes. I will not be the one that makes less per hour fixing others slop. My profit margin will not suffer. The other question I have is how do all of you build for the guy who cannot afford the best stuff. At $10.00/hr, 2 people working only make $40K .Painted finger jointed trim and mdf is all they can afford.This stuff is shit to begin with, I get tight joints as well, but the overall quality of the entire piture is still low.Is it really possible to shine a turd? I don't send good hard working customers away to the hack down the road because they can't afford the best. I do my best, with what I have to work with, I will lower my standards(not tolerances), use cheap materials and have a clean conscience. I'm glad to see that most of you can turn away lower work and only work for the rich and famous that can afford the best.It must be nice to work with the best stuff everyday.I don't.
*I don't work for the rich and famous; some of them are well off, but I've never been on a job with an unlimited budget (though I hear they are out there). I don't understand the guys saying "my quality never changes": how can it not? There's always a budget (in fact I've never ever seen a budget, residential or commercial, average folks or rich ones, that wasn't 'tight'. Everybody wants the most bang for the buck).Say you look at a job. X amount of square footage in a structure, x number of windows installed and trimmed, x linear feet of cabinets, whatever, you come up with a price. Then the budget is doubled. Or halved. You can't tell me the way you approach the technical part of it doesn't change. Every one has their 'production' way of doing it, and their 'just for nice' way. I'm still in the process of learning that lesson the hard way; I've given away a lot of free labour over the years 'cause I wanted it a certain way and the budget didn't support it.The amount of money available to do the job determines the level of the work, it's that simple. I'm reasonably good at what I do, like most here probably. I've never had the chance to pull out all the stops, and probably never will. It's all a spiral anyway, that never stops until the client runs out of money. Hence, the budget.I saw a documentary a few years ago, about the wooden boatbuilding tradition in Maine. The 'state of the art' boat they showed was a cruiser, under construction for years. The only watchword was perfection. They interviewed the cabinetmaker doing the interior (the guy had been there for two years; over six months in some rooms). He had discretion to go back and pull out and redo anything he wasn't happy with. For me, it's about compromise, daily. I don't do work I can't stand behind, but it's all in the context of the budget.
*Check out some of my work at http://business.fortunecity.com/ingram/109
*RE: Bill Popow's post (9.0) I offer only one type of work, well, okay two types--comm TI, down and dirty--and high end everything else.Don't want to pay for what I offer, okay, C ya. (Oh yeah, I say that now, but there were years I would kill for a job.) I have had so many people come to me after the job saying they should have gone with me. Well, tough shit. What'd you think you would get with a guy who is 40% less, you moron.Funny, but it's only this year, my 19th, that I'm starting to get comfortable with the idea of building down to the owner's expectations.
*Hey David, After thinking back a few jobs. I did cut back on quality for a customer. Not because the money was a factor, but because of time. In order to not hold up some of the other subs, I rabbitted the base cabinet drawers rather than dovetail them. The builder did not mind me rabbitting the drawers; however, I felt that I dropped my quality on that job even though no one else did. I guess I'm just a perfectionist and can't get it through my head that the rabbitted drawers were still acceptable.
*Nice looking stuff Mad Dog, I think we are all our biggest critics, and its nice to hear from others that feel that THEY are the hardest client to please. The one thing I enjoy about the cabinet business is the fact that once you have a system in place it is not much more difficult to produce high quality work. It very little more time to do things right. Keep up the good workHere in Baton ROuge, LA almost all cabinet work is custom. Most is nice looking/low quality, but it still beats manufactured hands down.What is your market like?
*It seems most of the bases have been covered, but one term is missing, value for the money spent. Everyone likes the job that they can take the time to do their best work, the best way, with the best materials. Not every customer can afford that, so we make some compromises in materials and perhaps methods to meet their budget. If the customer understands what they are and aren't getting, if, as mentioned, no shortcuts are made in areas that affect structure and integrity af the project now or later, shouldn't customer and contractor be happy?Having said all that, I've seen work done on a tight budget that I would never even think of doing. I guess it all comes down to who is doing the work. You still want a quality minded carpenter doing the budget job. To many hacks out there, and they aren't all doing the low-end jobs either.As Jim said earlier, standards are standards, and after 20 years, my bar always is going up as tools and equipment get better, and there are always new products and materials to use and learn about. But I like to think I always put top quality workmanship into every job. If you can't walk away from a job and feel good about what you've done, whats the point in
*Thanks David. Here in Abilene I don't know of many builders that use store bought cabinets. Most of the builders here like to have them custom built. There are 3 larger shops in competition here along with a few one to two person operations like my own. I recieve alot of work from one local builder and also have a share from indvidual customers and homeowners. This usually keeps me busy and in addition to the cabinet work, I also do trim work. I try to offer work that may go a little above and beyond the norm of the competition and as I mentioned before, it has really helped the business as I seem to have more customers annually through referrals. Lately it seems that entertainment centers have been a popular item as well as custom built fireplace mantels.Do you provide cabinets for homes that you build or does your market go beyond that?
*Three months?Huh.Well then, I guess I'm doing a little better than I thought. wait a minute, where's my...Oh, there it is. what were you saying about being spacey Andrew? Yes, first child on deck. Just got married a few weeks ago (kind of got the order of those things mixed up) The new wife wanted to take me to Dollywood for our honeymoon. Can you believe it? Didn't see Dolly, nor was there a plywood cutout of her to get photographed with (only computer generated stuff), but I did get to spend an entire rainy day waist deep in some smoky mountain river fly fishing.Got a couple of little rainbows (nothing like Montana fishing) and spent the rest of the time in a wonderful little cabin in the woods of east Tennessee with the new little lady (well, she's really not that little at this point in time, but please, try to keep it under your hat).For my first Father's day she gave me Dolly's new Bluegrass album (The Grass is Blue) which is an awsome achievement in the bluegrass music field -- I highly recomend it. Oh yes, and she also gave me a bottle of Gosling's Black Seal Rum which is, even if you don't like rum, absolutely heavenly. Don't mix it with anything, just slug it out of the bottle. Every slug tastes like you're in the carribean. Honest. I don't normally advocate giving booze for presents, but this is different. Honest.Oh, what a lady!
*hey dan... ya don't have to go and get all mushy on us.. fer cryin out loud..about time someone made an honest man outta ya..27 years ... but who's counting?
*I agree with Keith, the poor need places to live too, better than blow-away trailers. So long as the work is competent, safe, and reasonably durable, ok. it's "affordable housing". If it's a deathtrap plagued by lazy work that will cost a fortune to fix down the road, well... As for the McMansion crowd eager to put on airs, too arrogant to seek out advice on a field they don't understand, I think they get what they deserve. Those pretend palaces will generate -lots- of good business down the road. Think of it as redistribution of wealth. :)Do y'all work a bit different depending on whether you like the client or project? I've put in too many hours doing a basement and misc. other work for a friend's townhouse -- the project is way late and interfering with other work -- but I didn't take a lot of the shortcuts people go for in finishing basements because I wanted to experiment and make something interesting ... plus I do like these people.Unfortunately, I undercharged (duh, still learning), plus they're now likely to sell ... so I'm considering buying the place to recoup the cost! (no brokers saves 6%/~$10k ... no lawyers (we both are, anyway) ... no home inspector :) ... rent it out ...) And I know what's -behind- the drywall, more than they do!
*
I believe that sometimes you have to build down in order to fit a project within the budget. I think this is where the use of on-traditional materials can help. Another factor is the creative use of materials to make them seem more than they really are. I've used old, decorative dish plates as an accent on a plain tile back splash. I've used oak veneer plywood to trim out cheap vinyl windows and make them look a bit more presentable. Things like this can go a long way toward a satisfying and profitable project.
*
Gentlemen,
First off, thanks for a great thread that I think has served to allow us all to take a step back and think about exactly why we do what we do. Which brings us to the issue at hand. WHY do we do what we do. I have come up with two options.
1. Customer satisfaction: The look on someone's face as they survey their new kitchen/deck/driveway. I'm sure that the chance to help someone (this comes easier with some clients that others) is part of the driving force behind all of us. They get the usable space that they wanted, while we were able to give them the quality of workmanship that we deemed necessary (as to whether this standard varies from job to job will be covered later). As Ryan I said in 12.0, one should never skimp on details such as flashing or extremely crucial points, such as ensuring that the joists are big enough to hold the load.
2. Now, the other reason to build: Personal satisfaction. I would also think that all would agree that they would love to work on the boat mentioned by Adrian in 19.1. But the reality is all of us cannot. What happens when a client asks you to finish an attic for them that is absolutely necessary because a first child will be here in less that 5 months. Do you demand that every aspect of your work be to the highest standards, the trim cut to >1/32", the finest 5 coat job on the wallboard, and solid-core oak doors be hung throughout (of course, they will be hung exactly with a plum bob and Stabila Stabile or do you pick things up a bit in order to finish on time with a price that the grocery store clerk and truck driver pair can afford? Is it really necessary to shun the MDF trimMDven though the material savings savingranslate between the the father having to put in a half day on Saturday when he was planning to be with his wife. Will they know/care? I'm not saying to sell them junk billed as high quality, but what's the use of imposing your high standards on someone who doesn't care? Do they drive Cadillac's of Chevette's?
But I digress, I'm young, and still have alot to learn.
Jon Blakemore
*Ironic Bill. I just attended a quality seminar by the builder that I am working for. It was a Tyvek and Hardi plank seminar.We were staring at taped step flashing along a gable butting a dormer. Afterward, we happened to be lined up along the plane line of the roof. Interstingly, the roof had a TWO AND ONE HALF DIP IN IT! I REPEAT:2 1/2" dip in it, in a fifteen foot span. I've never seen one this bad.flabbergasted,blue
*I think the original poster was discussing the difference in standards that a rougher and a finisher has to meet.blue
*Jon The why I do what I do is because I still truly enjoy the work. I make a living at it, but I could probably make more as a car salesman. There is to me still the feeling that this is real and essential work. There is a certain competitive and even combatant feel that carries through the seasons and the ups and downs and all the learning processes that I embrace. I like doing my best and laying it out with all the other's best and seeing where it lies. Skip I'm old and I still have a lot to learn.
*
I had a customer specify what he wanted in terms of quality on trim and framing. {-1/16 and -1/8 gaps} in his contract. I think this is what is meant by all work to be completed in a workmanlike manner according to standard practices" at the bottom of my contracts, but I was glad he added that for clarity. Just finished installing two remodel skylights on a 6 in 12 shake roof. What a workout. Bill Popow
*Some very good points from all. Have to agree with Keith C. (post 19 in this thread) about doing the best I can with the materials the client can afford. If they don't need/want all the bells and whistles, I'm not going to try to force the sell on them.I did have the (unique?) experience of working for a higher-end client who wanted the new to look old. Wanted to be able put 1 or 2 coats of paint on the new crown molding and other trim and have it look like it was 70 years old, and painted a dozen times. Liked "soft" corners and such. It took a while just to get used to not having crisp joints, etc., and then applying spackle to new woodwork. Oh well, it worked out.
*
I do this type of work all the time. Have a hell of a time trying to explain to new men and subs that the whole point is to make the work fit into the existing, or to make it look like it was built in the 1920s. A while back, I had a terrible time trying to find someone to build cabinetry in the manner done in the 20s, since methods have changed a great deal since then.
But when it all comes together in a 75 year old manor house, the results are spectacular. Didn't cost less to do, but you would swear that this house was a perfectly preserved specimen of 20s work, a little wear and tear excepted. Getting those irregularly eased edges just broke some guys hearts, but they understood when the job was done.
SHG
*Your asking the wrong guys to make that stuff look old.Next time just fab it up normal, and have me and my boogering crew install it. We'll beat the hell out of it trying to keep it looking new.And at no extra charge!blue
*
I am fairly new to this board, and after reading the post TRACK HACKS, I had to chime in. My company(eight employees, numerous subs) does about 70% high end remodels, and new construction. In our market high end does not mean high quality. I have built my company on the simple concept of doing thing right. People are willing to pay for quality work, but they are few and far between. We have been blessed with clients who want A+ work and are willing to pay for it(We refer to these jobs as Taj Mahals). But I do still do lower priced work, but I let people know what they are getting. There work will be done correctly, just not to as high a standard. There is a place for all levels of work in our business, YOU just have to inform people of what they are getting from you, and others in our area. On the other hand the remaining 30% of our work is office build outs, and remodels. Quality is not the number one issue, speed is. These jobs give our employees and subs a break. Its nice to go into an office and not have to worry about 1/32 of an inch. You can relax and know that you just did a better job than most people in that arena do, and had fun at the same time. Also this helps improve your speed on finer work, because you get to see that rougher than normal framing is ok sometimes.
Quality will always very from client to client, and job to job, but doing things correctly like flashing, caulking, back priming, roofing and informing clients of weakness in certain materials is something we owe to all of our clients, because they are our best source of future work
Now that this is of my chest, what type of work do you all do?
David
*Howdy David,Welcome to Breaktime, well said. I usually sell myself as a quality minded carpenter assuring potential clients that they're going to get it done right, the first time and exceeding the standards of many in the area. Then I ask what the budget is and that's where I calculate the speed vs customization, or exaxcting standards ratio. They're always happy.I work alone mostly, so I do small jobs. Sometimes I get a helper or partner, but not much. I bill myself as a carpenter and cabinetmaker. I started out as a framing "mother**cker" and progressed into finish carpentry and have been dabbeling in cabinetry for the past few years. I just completed my first kitchen -- tore out the old, designed and built the new. Melamine cabs (thanks for the advice Adrian) with applied panels (painted) on the ends and painted face frames, doors and drawer fronts for the lower units and really sweet, stained maple uppers with six lite doors fully inset to the face frame. Double oven cabinet and refrigerator cab in maple, maple crown encircling the room. They came out awsome. I haven't taken pictures yet.I've got a bookcase, deck and two bathrooms coming up and for whatever reason I'm painting the exterior of someone's house right now. Well, I guess I know the reason, I'm expecting my first child, a son, in September, and I'm not turning away work (besides, it's the same guy who's having me do both bathrooms...)Heh, heh, heh, I get to be the first to welcome you aboard even though I've been absent for the last six months...I guess timing is every thing 'eh? Dan