Anyone know anything about this? I have seen a few slab homes built the following way. A backhoe digs the footings. two or three courses of block are layed on top of the footing. Plumbing, electrical etc. put in place. Gravel or sand dumped in and leveled to within four inches of the top of the blocks. Concrete floor poured level with the blocks and the block cavities filled. Reason I’m asking, I’m thinking of doing this.
Discussion Forum
Discussion Forum
Up Next
Video Shorts
Featured Story
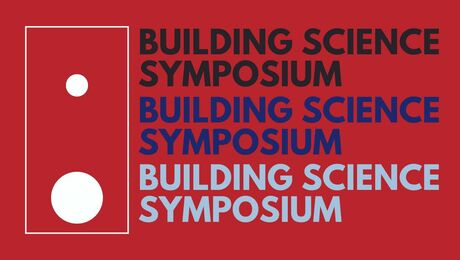
Fine Homebuilding is excited to be the official media partner of the 2024 Building Science Symposium series! This event offers builders, tradesmen, architects, designers and suppliers to discuss topics ranging…
Highlights
"I have learned so much thanks to the searchable articles on the FHB website. I can confidently say that I expect to be a life-long subscriber." - M.K.
Replies
The one single, most important, absolutely unavoidable person/department that has every precise, indisputable answer to this question and more can be found at your local building inspectors office.
Anything else is wasting your time and setting you up for failure.
Of course, that's just my opinion!
When I was in the door biz with ThermaTru, I did a mandated monthly field trip, rotating through our territory sales managers so as to visit distributors, dealers, and customers (builders and homeowners) in just about every part of the country.
I was amazed to find out that vast areas of the country, while perhaps under some kind of national or state building code, had no permitting nor inspection as part of the process of building a new home, or remodeling one.
View Image
"A stripe is just as real as a dadgummed flower."
Gene Davis 1920-1985
I understand. But without a known area provided, someone had to provide the ubiqitious disclaimer sometime. I simply beat the others to the punch!
That's how they do it in MI.
That is typical stemwall construction. It is a great way to build when you have an uneven grade, want to raise the level of a house and use less fill or want to avoid doing a monolitic slab.
You can build the stem wall with regular blocks, or with specialized chair block which helps to lock the lsab into the stemwall.
That is done here in Florida to get the finished floor above FEMA elevation. There is also thinking that a stemwall house like that is better in a flood condition because the footing is better able to resist undermining than the regular slab on grade..
I did it to my house,its great.
We do that here in Alaska for garage floors all the time.
You must be in a relatively warm area. You could not have footings that shallow in most northern areas, where the frost can go down to four feet or more.
Don't confuse this with a monolithic slab foundation.
I've built several stemwall slab homes... except that I put brick vaneer on the exterior. What's the question? And, what's your climate - ie - what area of what state (etc) do you live in?
Southeast Kansas, frost level is about 12 inches.
Not to be a wise guy,,,, but is'nt Kansas a good place to have a basement,,,, do to tornados.Harry
A lot of tornados in OK and TX but not many basements!
Doug
I've had a basement the last twenty years and have not had a tornado yet. Seriously though, I plan to put a small tornado shelter in the middle of the house in a pantry with a trap door just in case. Something about the size of a small tent to hunker down in if necessary.
"Southeast Kansas, frost level is about 12 inches."Are you sure of that?I am in the KC area where it is listed as 30-36".I would expect somethign in the area of 18-24"..
.
A-holes. Hey every group has to have one. And I have been elected to be the one. I should make that my tagline.
I have a similar question to pose to the audiance. What is the cost difference in doing a foundation/slab as suggested in the original posting, and doing the stem wall as posted, but then using floor joists in lieu of the concrete. Also ,please include pros/cons of each system.----------WW57 (Dallas Tx. area)
It depends on floor finishes and how much elevation change you are looking at.
About 2' elevation change from the existing grade. Primarily wood floors, some tile. Also thinking about radiant heat, your thoughts on that.
Matt covered a lot of the considerations accurately, I'd say.One he did not mention is that if you are in North Texas you'll want to find out if expansive clay is a concern. If so, that changes everything. If you are in expansive clay you will want to make adjustments to your design.If you are planning to use radiant, then a slab on grade becomes more attractive. Sure, you can put lightweight or gypcrete over joists, but the cost savings have evaporated by then.Bear in mind that if you build on a slab, the plumber is running your schedule for a significant part of the critical path early in the project. Add to that what the consequences of a plumbing problem might look like later on, and the importance of choosing a good plumber becomes clear.There was a trend for a while to use the slab as finish floor with integral color or stain. Protecting the floor throughout the course of the project can get tedious, and the cost savings have in this case been questionable as far as I can tell.
My house is built that way. Rather than use stained concrete, I saw cut the slab into 3 ft squares and filled with colored grout. The only protection I used was a layer of tyvek, and the only damage was a couple of small black stains where the plumber dropped solder. Saved enough to use maple throughout the upstairs.
>> doing a foundation/slab as suggested in the original posting, and doing the stem wall as posted, but then using floor joists in lieu of the concrete. << Also known as a crawl space....
>> What is the cost difference in doing a foundation/slab as suggested in the original posting, and doing the stem wall as posted, but then using floor joists in lieu of the concrete. <<
Generally, for a fairly flat site with a somewhat minimal frost depth the cheapest foundation/floor system is a monolithic slab, the second cheapest foundation/floor system is a stemwall slab (topic of this thread). Third cheapest is crawl space foundation, and most expensive is a basement.
>> Also ,please include pros/cons of each system.----------WW57 (Dallas Tx. area) << Someone could write a book on that... but I'll take a quick stab (and I'll cover all 4 basic types of foundations):
Mono slab: quick, only one subcontractor. (2 if you include the plumber's extra trip) Requires a fairly flat site and often earthen "pads" are prepared prior to the commencement of house construction. Cold and hard floors, (assuming no radiant heat) . Popular with builders and entry level home buyers these days because they are quick and the builder can deliver more house for the money and most homebuyers don't seem to care (or know the difference) about the down sides of slab houses. If you want hardwood floors, generally you have to go with an engineered product which is basically just plywood. Slabs make running mechanical and electrical systems under the floor much less feasible. More trouble to run plumbing systems under the floor although generally, you have no choice.
Stemwall slab: Similar to mono slab but you can deal with grade changes better, and you have the option of adding brick veneer so it can look better. Stemwall slab is actually like a basement with no sub-grade walls added.
Crawl space: You don't get the cold hard floor thing since you have a food framed floor so better occupant comfort. Cheaper than basement. You can deal with almost any site grade. Can be prone to water problems on some sites if not constructed correctly. Less prone to radon problems than slab houses.
Basement: extra (cheap) living space and a good storage space for all that stuff that you should actually put in the yard sale. Prone to water problems on some sites if not built very well. More popular in the northern USA as the footings have to go at lease 4' or so deep so you are already 1/2 the way there. Less popular in the southern US for the same reason - only shallow footings required. Less practical for costal areas that may have high water tables.
I did a cost analysis for a neighborhood: CS vs mono slab house. What I came up with was that the break even point was $6k meaning I could spend up to about $6k for site work to build pads for mono-slab houses before it became more cost effective to build a crawl space.
So, in summary, the choice of a floor system comes down to money, occupant comfort, the grade of the site and geographic location.
Further, there are other types or variations of foundations too such as frost protected shallow footing slabs, houses constructed on pilings, curtain wall CS, etc, and hybrid foundations where, say a stemwall slab and CS foundation or even basement might be combined. The later being extremely common for houses with attached garages in the northern US and Canada.
Assuming I opted for the stem wall/floor joist system aka crawl space, I am also assuming you would need several interior stem walls to help carry the joist load and not have these joists 2' in depth--exagerating here--but you know what I mean.---WW57
>> Assuming I opted for the stem wall/floor joist system aka crawl space, I am also assuming you would need several interior stem walls to help carry the joist load and not have these joists 2' in depth <<
normally it would be some interior piers and a girder of some sort - probably a built up wood beam - say made of 3-ply 2x10s. Piers might be 8' apart depending on load above. re the joists, find a joist span table on the internet. Weather dimensional lumber (solid sawn boards) or engineered (probably I-joists) the tables are easy to find. Be conservative when looking at the tables. Maxed out spans don't give good performance. BTW - Really the spans of dimensional or I-joists are similar, it's just that I-joists commonly come in taller sizes than solid boards. I-joists come in longer lengths which is more of just a convenience factor as these long lengths still need intermediate support (girder(s)). I joist venders will normally do the floor system design for you free (excluding the piers & pier placement).
There are lots of areas in Texas that have soil problems that prohibit simple foundations like that..
.
A-holes. Hey every group has to have one. And I have been elected to be the one. I should make that my tagline.
Which one of the foundations were you refering to?-----WW57
Either one.I know in some areas that expansive soils are a problem.And in soem areas that they use pier and beams..
.
A-holes. Hey every group has to have one. And I have been elected to be the one. I should make that my tagline.
Does a vapor barrier fit in there somewhere? If so, where? Just curious...
"Does a vapor barrier fit in there somewhere? "Yes. Also insulation..
.
A-holes. Hey every group has to have one. And I have been elected to be the one. I should make that my tagline.
Order of construction.
1. Grade slab area to accept footer
2. Dig footer and install steel including uprods to tie wall block (if not framed) . To eliminate bringing extra fill dirt in, make sure spoils from digging footer are thrown inside slab area(no footer/steel across garage door opening to allow access for equipment. The rebar is left long to tie into later) Inspection if AHJ requires
3. Pour footer
4. Stock and lay stemwall block.
5. Backfill to 4" below top of block and cut garage stepdown
6. Install U/G plumbing, drainlines, a/c chase and electrical chases (Inspection if AHJ requires)
7. Prep slab. backfill plumbing, dig any interior bearing footers, termite pretreat, visqueen, WWM and form garage curb and footers. Inspection if AHJ requires
8. Pour slab to top of stemwall
There are advantages to building the block wall stem walls verses mono pour. Mainly its Compaction and amount of concrete. You can ramp up dirt to compact the dirt under the slab with a bobcat, without blowing out the sides.
Typical slab-on-grade construction in NJ- they've got a 3' frost line, so they did down 3', pour a 12" footing, put 4 courses of block on top and pour the slab- it's a no-brainer.
Why bother with block, just pour a 3' foundation wall. You're already pouring concrete footings and slabs, that's the way it's usually done on most jobs I've seen.
That's just the way the masons worked in my neck of the woods- none of them wanted to shell out $$ for forms, so they laid block instead. Sometimes ya just can't teach an old dog new tricks, ya know? There was only one company around that'd even do poured walls for basements- they'd all still use 12" block with a few courses of 8" once you got closer to grade. Down here in GA you won't find anyone laying block for foundations- they've got trucks set up with the loads of panels in various sizes on custom stakebeds and they'll form and pour a basement in a few hours if the inspector cooperates."Brilliance!! That's all I can say- Sheer, unadulterated brilliance!!" Wile E. Coyote- Super Genius
Not sure about GA but up here in the NY / NJ area they usually pour foundations these days.
FWIW, Ive done a few. - Ohio.
My sop is dig a trench, fill it up w/ crete, set 1 coarse of block in crete as its setting up.
More cost in crete - but HUGE savings in labor and time, backfill, etc etc., no overdig.
Remodeling Contractor just on the other side of the Glass City
Sounds more like a grade beam, or a slab haunch, do you put in reinforcing?
Sometimes.
It's still a 16" wide trench - to get the footer width. So It's pretty over kill on the strength side of things.
As long as the initial grade is decent I don't need to form anything.
I go in and cut out any organic material from the inside with a skid steer after the block sets up, grade the stone and use the block as slab forms.
I can do the whole she-bang by myself. It's pretty painless.
Quickest way Ive found to get up out of the ground, and get moving.Remodeling Contractor just on the other side of the Glass City
Time is money and overbuilding is better than under building.
My shop is built that way, and I am a few days away from doing it again - off my house for an attached garage.
I feel real sorry for the guy who buys this place if he thinks he's gonna' tear out my stuff.
My shop is 16" x 36" with steel, quite a bit. It'll take quite a bit to get rid of that found ation.Remodeling Contractor just on the other side of the Glass City
Hopefully the guy will like the shop and leave it be.