I am working on a vinyl siding project, and after stripping off the old siding discovered there is not a lick of insulation behind the builtrite sheathing. The owner wants to remove the sheathing and reinsulate with fibreglass batts. After that, resheath with OSB and housewrap with tyvek. Any possible land mines in this process of reverse insulating? FYI the house is in Minnesota and in winter the floors freeze when the wife washes them, and we won’t talk about the heating bills
Discussion Forum
Discussion Forum
Up Next
Video Shorts
Featured Story
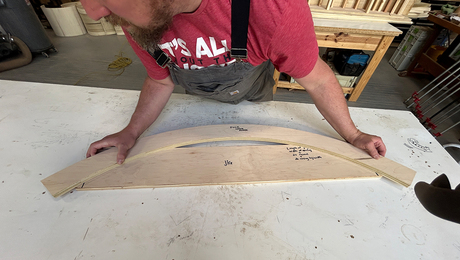
Making mitered head casings is a breeze with this simple system.
Highlights
"I have learned so much thanks to the searchable articles on the FHB website. I can confidently say that I expect to be a life-long subscriber." - M.K.
Fine Homebuilding Magazine
- Home Group
- Antique Trader
- Arts & Crafts Homes
- Bank Note Reporter
- Cabin Life
- Cuisine at Home
- Fine Gardening
- Fine Woodworking
- Green Building Advisor
- Garden Gate
- Horticulture
- Keep Craft Alive
- Log Home Living
- Military Trader/Vehicles
- Numismatic News
- Numismaster
- Old Cars Weekly
- Old House Journal
- Period Homes
- Popular Woodworking
- Script
- ShopNotes
- Sports Collectors Digest
- Threads
- Timber Home Living
- Traditional Building
- Woodsmith
- World Coin News
- Writer's Digest
Replies
Biggest problem is ripping off that sheathing, especially if its stapled on. It can be a real bear to remove. And, of course, there's always some danger of "collateral damage" to the inside walls, but nothing that's likely to create a crisis.
If it were my house I'd leave the sheathing up, insulate with blown cellulose, housewrap, then apply fiber-cement siding or some such.
Yea, the issue of staples is a bugger. Someone told me ther is a handy tool designed to pull them out. Any thoughts
I think it's called a "match".
I have a tool that looks like a wide bladed screwdriver with a notch in the blade, and the blade is beveled and slightly bent so once you get it under a staple you can (supposedly) rock the blade and lift the staple. What usually happens is that one side of the staple pops out. Then I grab either pliers or vice grips and just yank the staple out. Then if there is any part of the other staples out enough to grab I generally just use the pliers and use the special tool to drive under those that are imbedded. Maybe there is another tool that's even better. Anything is going to be time consuming though.
The poster (DanH) who said leave it and blow insulation into drilled holes, then put on cement board had a good idea!
Edited 8/3/2004 4:14 pm ET by Danno
Of course a lot depends on how much money the original builder wanted to spend on staples. The guy that built my house must have had a new power stapler that he wanted to give a good break-in to -- must have stapled every 3-4 inches. (Set them deep, too.)
And that cardboard sheathing stuff just breaks up if you try to pry under it to get at the staples. But when it breaks it always leaves a chunk of crap under the staple that keeps you from getting anything in there to pry.
I'm guessing that it would take the better part of a week, working full time, just to remove the sheathing from our (roughly 2000sq ft exterior) house.
" apply fiber-cement siding or some such."
Don't forget, you are replying to a vinyl installer whern you say that.
Welcome to the Taunton University of Knowledge FHB Campus at Breaktime. where ... Excellence is its own reward!
Don't forget that I said if it was my house.
In my opinion Dan gave the best solution.
If you used FG batts, you'd really want a vapor barrier on the inside of the wall cavity. Not terribly practical. And what you could do really wouldn;t be too effective of a vapor barrier.
Blowing in cells will do a great job of getting in all the nooks and crannies, and you really don't need a vapor barrier with cells.
Before blowing cells, though, check into what type of wiring and plumbing is in the wall cavities.
I'm with Mongo. I just had to remove a bunch of nailed sheathing with a cats paw and that is nasty work, particularly with old-growth lumber studs that gripped the ring shank sheathing nails like a baby its mama.
I would blow in cellulose, wrap and then fiber cement. use furring strips underneath the fiber cement on the side of the house that gets the worst weather so there is a "rain screen" wall as some moisture will get past the siding if the wind is really howling.
also - look for blocking in your stud cavities that will keep the cellulose from filling the whole cavity. some walls may need a couple of filler holes
Wylie
Thanks for the replies. The customer is set on Bat insulation and not blow in cell. Pulling staples is going to be a chore, no way around that.
Tell the customer that you'll knock $100 off the price of the job if he pulls the staples.
I'm sure someone will jump on me for this but here goes. (And I can't/won't comment on the staples). Certainteed makes something they call under-floor insulation. It's a fully wrapped bat with the nailing flange on the side opposite the vapor barrier/retarder.
I completely insulated my 1821 farm house in upstate NY with this stuff several years ago and have been very happy with the results (spelled warmer with half the heating bill). Had similar issue as you do. Was ripping off various layers of siding including cement/asbestos, old claps, rolled roofing, etc. Pulled off the sheathing (lousy wide boards in this case), insulated, re-sheathed and sided, oh, and repaired all the structural damage along the way caused by leaky windows etc. Big issue here was not ripping into relatively sound plaster walls.
Before I took the plunge, I contacted Certainteed and questioned their tech reps up, down, and sideways about using their insulation in a manner different from what was intended. They saw no problem except perhaps for the fact that this stuff is thick, 9" if memory serves, which wasn't a problem for me because the house is post and beam with 8" walls.
My biggest fear was water vapor trapped in the walls and soggy insulation. Since doing this I've ripped into inside walls in different parts of the house in different seasons and never found a problem. FWIW, used housewrap on the outside too.
Hope this helps or at least gives you something to think about.
Tell the customer that he wants the worst, least effective kind of insulation available today. Andf that he is willing to spend gobs of money to put it in. If he really wants FG instead of cellulose, get him soem blown chopped fibreglass instead which ois nearly as effective and twice as good as batts for my money.
For you as contractor, remember that most sheathing is a structural element, wind and shear bracing asa part of the wall assembley. Know that you are gauranteed to have nail pops in the interior sheet rock and possible racking problems rto contend with.
I wouldn't touch it without a signed waiver/disclaimer if he demands that you do the stupid thing. The best would be to blow the cells or BIBBs while leaving the sheathing.
Welcome to the
Taunton University of Knowledge FHB Campus at Breaktime.
where ...
Excellence is its own reward!
two things come to mind, 1 cellulose sometimes contains boric acid which does make life uncomfortable for the bugs, and with a blown in wet cullulose like 'celbar' the r value is higher than with fiberglass and you get all the little odd spaces.
two. the staples. Hire some cheap help give them a grinder and a face shield abd grind off the staples and nails. This is the easiest way to redo an old house, and I 've tried all kinds of ways. Pulling the nails & staples takes too long and they always miss a few. with a grinder and 35grit paper you get everything that sticks out. just be careful.
down here in houston the old houses had a shiplap interior that was covered with a burlap type wall paper that was nailed on with carpet tacks. Trying to pull all those tacks was a long term job. The grinder-sander made short work of the whole thing.
good luck
jwinko