Recent article regarding shear strength issues with “smart framing” suggested OSB or site-built shear panels as answers. Is there anything wrong with using let-in 1×4’s? Seems easir than shear panels. Is this an oudated technique?
Discussion Forum
Discussion Forum
Up Next
Video Shorts
Featured Story
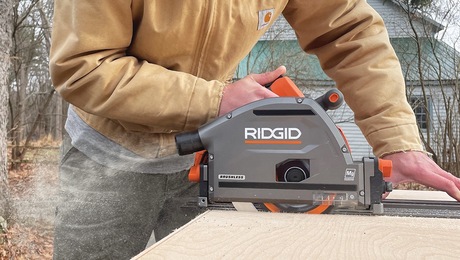
The best tool for straight, splinter-free cuts is made even better without a cord.
Featured Video
How to Install Exterior Window TrimHighlights
"I have learned so much thanks to the searchable articles on the FHB website. I can confidently say that I expect to be a life-long subscriber." - M.K.
Replies
Everything I read says that sheet goods are a lot stronger than let-in bracing, steel strapping or diagonal planking.
Makes sense to me as the sheet goods spread the racking loads across a wider area and provide multiple redundant load paths as the nails have to rake laterally through the sheeting or pull out for the wall section to rack.
Given the common nailing schedules this means a lot of nails have to rake through a lot of wood or pull out. Many more than any diagonal brace.
Given the current, and given the recent events likely to get stronger still, emphasis on improving the standards for building integrity sheet good seem the best way to go. IMO the rack strength can be further assured long term by using plywood instead of OSB. But given the superior rack strength of a shear wall produced with well nailed, glue for even better performance I understand, sheet goods OSB may be more than sufficient.
thanks, i was just thinking i could use 1" exterior foam exclusively, and not have to use 1/2 sheet and 1/2 foam at the corners, but have learned enough to proceed as instructed!
Don't know the details but at least one house I have worked on had icocyanurate foil-faced foam board applied to the entire outside and the inside was sheathed in 1/2" plywood for rack strength. In this case the interior plywood was skim coated with bonding agent fortified finish plaster. I was told this puts the insulation and vapor barrier on the outside, it is a warm humid environment so this seems to make some sense. On the outside the electrical boxes do not compromise the foam and they ended up with a well insulated house with low losses from the framing. Not sure I liked the system as it leaves the exterior soft and vulnerable to flying debris during a storm. Always a concern in Florida. It also cased some concern with the guy hanging the siding because it limits hit options for nailing to 16" OC and preinstalled blocking as the foam can't be fastened to.The plasterer was pushing for some sort of mesh to be nailed to the plywood and a three coat plaster system, scratch, brown and finish but they went with two finish coats. I have also seen it the other way round, sheathing covering the entire outside and foam board covering the inside with drywall over it. Makes for a thick system which means I have to mount my boxes farther in, use adjustable boxes or extension rings. This means all the electrical, cable, telephone and computer network boxes are holes in this insulation layer. All told about a quarter of the stud bays had at least one penetration for boxes or pipes. There was talk about foaming in around my boxes or providing special boxes with insulation and seals but it didn't happen. On the other hand the siding guy was happier as he could use the sheathing as a secondary nailing surface if needed and the inspector knew immediately what was going on as it is the usual configuration. The ply also provides a relatively hard shell against penetration by debris.One thing I have seldom seen around here is the use of sheathing for rack strength at corners but the majority of the stud bays having no ballistically resistant materials in them. Must be a northern and western thing where the emphasis is on energy efficiency rather than wind or earthquakes. Round here some form of structural sheathing is a whole house thing.A few low end builders used foil-faced cardboard, Thermo-ply, as sheathing for rack strength but this was limited when it was suddenly discovered that rain and high humidity, which reduce the cardboard to mush, were regular events in Florida. Who knew?Just as an experiment on a wall with water soaked particle-board claps exterior, damp drywall interior and Thermo-ply sheathing we learned that you could punch your fist through the wall as long as you missed the stud. One helper put his head through the wall. A second about knocked himself out when he misjudged the location of the stud. A good time was had by all knocking holes in the wall due for demolition. We were all surprised there was so little resistance to penetration. Especially the carpenter who claimed the Thermo-ply was great stuff and he intended to use it on his own home. He had changed his mind by the end of the day. Who says carpenters can't learn.Nice to know a burglar need not mess with windows or doors. With little more than enthusiasm he could kick his way through the wall in seconds. That ought to give the HO a warm fuzzy feeling as they shelter from a hurricane.
If it makes you feel any better, builders here in coastal Alabama are still using thermo-ply for exterior sheathing, even in light of recent events.
What a crock of poop!
Keep up the good work!Jason Pharez Construction
Framing & Exterior Remodeling
Re: "builders here in coastal Alabama are still using thermo-ply for exterior sheathing"I suspect that given the Katrina and Rita experiences this might change. Couple of thousand houses fail and even the slow to change construction standards might change. Of course the builder associations and their lobbyists will be shoveling money out the back of a dump trucks trying to obscure the need and prevent any stiffening of the requirements. Same thing went on here in Florida after Andrew. They fought tooth and nail to prevent any changes. Given the rhetoric you would think adding some steel, eliminating staples and actually nailing down the sheathing and roof decks was going to put them out of business. Funny thing was it didn't. They started building sturdier houses and their profits went up. Last year we saw a lot of homes built according to the newer standards exposed to hurricane winds and, for the most part, they held up well. At least those that followed the rules and were competently built. They still don't survive a direct and unshielded encounter with a category 5 eye wall or a microburst but most homes in the path of a hurricane don't get hit directly. And those showed vast improvements in integrity. In a lot of cases it made the difference between losing shingles and losing the roof. Closer to a direct hit it was the difference between having a heavily damaged house, with people who stayed behind alive and a lot of the furnishings salvageable, and coming back to a bare slab, people injured or dead and everything gone. In most cases the additional costs were a few hundred to a thousand dollars. Cheap insurance.
Your post mentioned staples....My crew normally staples roof sheathing as we have found it makes for a much better connection on the roof sheathing...on the walls, it's either staples or 8d gun nails, depending on the situation, but we have 2/3 OC edges/field patterns that I follow religiously.
OTOH, a roof replacement we recently did, we had to renail the entire deck because most full sheets of roof deck had less than 10 8d gun nails per sheet. Go figure.
I read recently that Florida has made it a standard to use ring shank nails for sheathing. Is this true? I would gladly use the new Bostitch Sheather Plus nails if they made them for a coil nailer---cost is normally the last factor in my jobs; however we cannot afford to be inefficient.Jason Pharez Construction
Framing & Exterior Remodeling
As I understand it, I'm on the electrical side so fastening wood is less central, staples are not allowed any more in Florida for any structural connections. Most of the testing I have read about say that stapling is a weaker connection than nailing. Gluing and screwing is, according to at least one expert, the gold standard.
> Gluing and screwing is, according to at least one expert, the gold standard.
Here it's gluing and nailing. Nails are ductile, while glue and screws are both subject to brittle failure.
-- J.S.
Re: ..."while glue and screws are both subject to brittle failure."Depends on which screws and glues used. Your correct if you use drywall screws and the cheapest available glue brittle failure is possible. Even then if enough are used it may not be a problem if a few fail. The glue and many screws making for many redundant load paths and a structure that spreads the load over very wide area.A quality APA, or other, properly selected adhesive well applied and high quality screws, made of a quality alloy and stress relieved, particularly if they have wide truss heads that resist pull through, simply aren't brittle enough to fail catastrophically under any load the house would likely survive. There is also some resistance to brittle failure in larger assemblies that is not seen in simple testing of smaller components. In a large assembly the wood itself tends to absorb shock loads by flexing. This aided by the rigidity of glued sheathing which tends lock the joints rigidly to force the entire structure to flex. As opposed to concentrating stress at the joints.Some of the bias against screws IMHO comes from the use of cheap drywall and deck screws of questionable origin and from a comparison between a #6 drywall screws versus a #8 common nail. Of course if the material cross-section of the screw and nail were made more equal the screw, even cheap ones, are on much more equal in resistance to failure. Advantage often going to the screw because the screw is many times stronger in withdrawal. The screw also pull the assembly more tightly together and maintaining tension under the buffeting loads of wind and earthquakes. Once the joints loosens the nails can bend and loads shift from shear to withdrawal. Most better builders seem to always screw down the wood on decks, a structure designed for recreation and not vital to the residents survival, but resist screwing down roof decks on a structure they live in and depend on.Common nails don't have any real standards other than external dimensions. The alloy used is usually the cheapest mild steel available. Nails vary widely in their particulars of hardness, ductility and fatigue resistance. Nail to nail and batch to batch. Long ago, back when forms were put together with Estwings and Plumbs hitting nails not compressed air, the differences beween batches were obvious. One batch was so soft that even the old hands were folding them.Wood screws have a wide array of standards. Everything from the lax standards of bulk drywall and deck screws shipped in from China to engineered and rated jobs used in more critical applications. So it isn't about nails versus screws. It is about nails versus the particular screws used.
Yup, the best possible screws are clearly better than the best possible nails. But of what's widely available, the worst screws are also worse than the worst nails. So, how's an inspector to know the good screws from the bad?
Glue can be excellent. It can be stronger than the wood. You don't need anything stronger than that. The problem is that it gives you just so many pounds per square inch, so you need fairly complete coverage. Again, it's QC, knowing how much area is lost to voids, that makes it problematic.
If you take a closer look at what happens in earthquakes and storms, it's not so much that wood gets broken. It's mostly that wood gets disconnected from other pieces of wood.
-- J.S.
Re: ..."it's not so much that wood gets broken. It's mostly that wood gets disconnected from other" Short of a truck driving through a wall or tree sitting on the roof I don't think I have ever seen a wall or roof assembly shatter or split with the wood failing. Wood has long been the product of choice for shock loads as it tends to bend and return. A good example of this was some of the command bunkers built by the British during WW2. Both steel and concrete were available but they went with wood that had to be imported.As I understand it the ideal solution would by connections that match the stiffness and elasticity, modulus, of the wood itself. This is the old problem with 'flitch' plates where steel is sandwiched between pieces of wood. On the surface it sounds great but, in the end, it is usually a waste of both the wood and steel. The wood is elastic and takes virtually none of the load until the steel fails. At which point the wood has to handle the entire load without the aid of the steel. The load is allowed to defeat each in turn because they don't truly act together as a unit because of the different modulus of elasticity.This is much like the old trick of tearing a telephone book. If you try to do it square to the face it is impossible to tear by hand. The trick being to bend the book so that you essentially tear one tear the pages one at a time. By taking on the individual pages in shear even an average person can tear the book in half. What I would like to see would be strapping and reinforcements that more closely match the elastic nature of the wood. Plastic? Maybe Kevlar reinforced to allow for nailing might work. Might have an advantage in a corrosive coastal environment. This would reduce stress concentrations and allow the entire structure to work more like a unit. Domes tend to do this not so much by materials compatability or matching but geometrically.
When I built my own house, I used both shear panels w8d 3 in oc , plus let in 1x4s. in earthquake zone, high wind as bad.
Also, roof joists/trusses not set on plates with ties, set on let in 1x4 with studs nailed to sides of rafters. Would go to that effort on anybody else's hours though, probably would not want to pay the differential labor.
I doubt a let-in 1X4 provides much shear strength at all. You simply can't get enough nails in it to accomplish much of anything.
So yes, I'd say it's an outdated technique. It simply isn't up to modern building standards.
Let-in 1 x 4's offer virtually no shear strength. A number of years ago there was an article in, I believe, the Journal of Light Construction in which an engineer discussed the shear strength of a number of different constructions, giving the shear resistance numbers for them. It was surprising to me that let-in members do very little, so much so that they are not worth doing at all. A shear panel provides considerable shear strength.
thanks.
the more i look into the information in fine homebuilding articles, the more i find it less than helpful as a "how-to", and more relevant simply as "new ideas to research independently". with a complete set of the magazines i have found huge numbers of conflicting standards and techniques.
for example, in the article on smart framing the author states "the traditional solution is diagonal bracing, either a metal strap nailed to the wall frame or a 1x4 let in to the wall studs." from the answers i've received to my question he should not have said the "traditional" (that makes me think it is still valid) but "the old, unsafe and inadequate way".
Not true fabian.
We have three million homes in the Metro Detroit area. Probably half have been erected using let in braces or metal t straps with foam sheathing.
None have failed yet.
We aren't in earthquake or hurricane zones, so the framing technique works perfectly.
blue
thank you for the input. really.
please don't take this the wrong way: so who is to be believed here? the eight people who say the technique doesn't work for a variety of reasons (including the truss "engineer" at the local lumberyard and the building inspector) or you.
as the owner builder trying to sort out the wide variety of information, it seems that it shouldn't be nearly so difficult and complex.
The only way to compare the shear strenghth of various alternatives is to look them up in published reference materials based on laboratory testing. An engineer can do that for you. Opinions are not data.
Let in brace is adequate in Northwest Indiana. fill in your profile for more relevant answers
Back before the 1933 Long Beach earthquake, they used diagonal 2x4 blocking to try to hold things square. The blocks would run in a straight line, about 40 to 50 degrees, from plate to plate.
Let-in 1x4 replaced that, and is what we were doing when I was a kid and my dad was building, in the 1950's. It was a lot stronger than the diagonal blocks.
Sheathing with 1/2" Struct #1 and s--tloads of 8d nails is the current way. LADBS did some tests on nailing schedules, and basically found the more the better. 2" OC is better than 3" OC. Unfortunately, they didn't try adhesives.
-- J.S.
If you read the article closely they also talk about a inset shear panel.
Page 55 Issue 174