Site-built wood stairs and their skirts
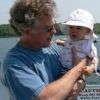
Having done these with the carriages set inboard enough so you can get a straight plain skirtboard in there first, and then finish with the risers and treads cut to fit tight, I’m wondering . . .
. . . Is it better done by templating and fitting the skirts on last?
Risers and treads go on with a whole lot less work, if you do.
The joints between skirt and treads are horizontal, not vertical, and if open slightly, are less likely to offend one’s view of details.
I recall our famous Breaktime brother, Mr McDesign from the great state of Georgia, who showed us how to template the whole thing out with some paper and tape, and am wondering how that goes, time-wise, when compared to all the cut and fit that goes with tight-fit parts at the treads and risers.
Replies
I've done a couple recently where the treads and risers are cut to fit and you end up cutting most of them square and to the same length anyway, so it's not much of an ordeal. Cutting notched skirts could be done, but I seriously don't see the advantage.
Latest JLC has a nice article on this. House the treads & risers in the skirts. One side is routed deep so you can set the tread/riser in and slide it over into the other side. Tighten everything up from the back side with shims/screws.
Nice article -- made me wanna do one!
Mike Hennessy
Pittsburgh, PA
Everything fits, until you put glue on it.
I’ve posted pics of this shoot-board jig before -- it makes it pretty simple. With a sidewinder, it’s front-to-back on the right-hand end, back-to-front on the left. Wrap the left bullnose with masking tape to avoid tearout.
View Image
Note that the ends are angled a bit to get into tight corners. I also slipped a strip of flashing in and bent the ends over to keep it there. I helps keep the telescoping arm from getting chewed up by the locking screw.
I would have made it with pieces of Festo rail, but back then the saw covered the entire rail, making it difficult to make custom jigs with it. Their redesigned rail would work perfectly.
AitchKay
Nice, Aitch. I use the store-bought kind, take care of the nose end as you do, and belt sand away some of the bottom back behind the nose to try for a scribed light squeeze.
The store-bought "Stair Gage" tool has tapered edge scribing edges on the end tees, nice for making the cut marks with a knife.
But I want to learn an alternative, and just sent away for the latest copy of JLC. Maybe the guy has a good way.
View Image
"A stripe is just as real as a dadgummed flower."
Gene Davis 1920-1985
Hi, Gene,Thanks. Just to clarify, that's a saw guide, not a marking guide. Since it works the way a zero-clearance insert for a tablesaw does, there's no need to knife the line, just take care of the exit at the nosing.AitchKay
I've done both ways, and would far rather set skirts first, then the risers and treads
Welcome to the
Taunton University of Knowledge FHB Campus at Breaktime.
where ...
Excellence is its own reward!
I notch the skirts over the risers, then shim between the back of the riser and the stringer to get a tight fit to the cut in the skirt. (skirtboard ends up looking like an upside down stringer)
I then use a jig to scribe the treads between the skirts.
The advantage of this method is that the treads can be cut a couple whiskers long for a nice snug fit, with no chance of them opening up the riser/skirt joint.
I got this idea from an old (early '90s) FHB article. It's a lot simpler to do than to explain.
It does take some time to notch the skirts, but not having to scribe risers probably makes it a wash timewise and ends up making a much nicer stair, IME. I've been doing it this way for sometime now, with no problems.
AitchKay - a tread marking gauge made from Festool tracks is a brilliant idea! Now I mark the treads along the template with a knife and lay the Festool track over the knife mark - this would definately save a step.
Mike
That article was authored by Bob Syvanen.
"Bob Syvanen"There's a blast from the past for ya!AitchKay
Do you know the Festool stuff? I don't.
Would this subassembly of plate and rail be the start of a stair-tool template/cutting guide? The ends would have to be mitered back a little so as to get into corners.
View Image
How much clearance does the saw allow on that side where the fixer plate would get bolted on? Horiz and vert.
I figured that one of their 32" guiderail lineals would do, cut in half, each of these about 13" across the cutting end.
View Image
"A stripe is just as real as a dadgummed flower."
Gene Davis 1920-1985
I don't have that new-style rail, unfortunately, but I know there's enough clearance to do exactly what you've drawn. That's what I wished I could have done with the old-style.And for the telescoping part, I started by buying a scrap of rectangular alum. tubing, and ran some scrap wood through the planer to fit inside the tubing.FHB published my lauan version a few years back, and gave me $150 for it!AitchKay
I'll bet you could reconfigure your stair guides similar to these. If you go all the way through the thread, there are pics of two different homemade parallel guide setups (just some rail connectors and scrap birch ply) that would do the trick. No clearance issues at all, it seems.'Man who say it cannot be done should not interrupt man doing it' ~ Chinese proverb
View Image
Yeah, as I said, I sure wish Festo had already come out with their new rail design when I built that jig!My rail lacks the upward-opening channel, and sits completely under the saw, so you can't even drill and screw a mod.I guess Festo received enough calls like the ones I made to them to finally redesign the rails for more flexibility.The jigs in that link are great, but woodworkers should consider breaking away from their labor-intensive routed-groove systems -- the aluminum-tube-type system is so fast to build, and so easy to elongate/shorten/modify: Take the telescoping mech that I used, drill oversize holes in the top so that you can reach through to drill and countersink the bottom, and Bingo, there's your bench mount. No stop-routed slots, no toilet bolts. Make six of those couplers while you're at it, in little more than twice the time it takes to make one. And if you really want to tweak out, how about rigging a Festo rail like a cable-rigged parallel rule drawing board? Instant panel saw!One of these days I'll have to upgrade my rails. In the meantime, my custom jigs will be made from lauan.AitchKay
Steve, I've posted a jig that's similar to hk's, but much lower tech... and, IMHO much more useful<G>The stretcher can be any length. I can hot glue, screw or nail scribe strips to it, I don't even care if they last<G>Worm drive is great, but I'm into a little more finesse...Just scribe 'em off on the material, then cut 'em with Gabi's Kapex<g> http://www.tvwsolar.com
We'll have a kid
Or maybe we'll rent one
He's got to be straight
We don't want a bent one
He'll drink his baby brew
From a big brass cup
Someday he may be president
If things loosen up
Holly,Funny, I was just looking at that Stair Hackin' thread yesterday.Thanks for posting the jig. Assume you make different end plates for the risers/treads that correspond to what their height/depth should be?Yeah, let's see if Gabi has a Kapex waiting for her under the tree this year :) Best,
Steve'Man who say it cannot be done should not interrupt man doing it' ~ Chinese proverb
View Image
<Assume you make different end plates for the risers/treads that correspond to what their height/depth should be?>Steve, I have a whole collection: treads, risers, window sills, beam and wall caps, etc. The stretchers can be any length. We've used pieces of base to go 16'.I've just found the shooting boards get too sloppy too quickly... but a festool rig might work, since bevel cutting doesn't eat up the edge... and I haven't cut too many treads that didn't need a bit of a bevel. They just aren't all the same.http://www.tvwsolar.com
We'll have a kid
Or maybe we'll rent one
He's got to be straight
We don't want a bent one
He'll drink his baby brew
From a big brass cup
Someday he may be president
If things loosen up
Thanks Holly,
Now that I've been looking over your jigs, it seems that the Swiss carpenters suffer from the same issue as their cheesemakers, their products are full of holes :)
View Image'Man who say it cannot be done should not interrupt man doing it' ~ Chinese proverb
View Image
It's the PA Dutchman in me... I reuse those holes, too.http://www.tvwsolar.com
We'll have a kid
Or maybe we'll rent one
He's got to be straight
We don't want a bent one
He'll drink his baby brew
From a big brass cup
Someday he may be president
If things loosen up
So you wear wooden shoes when making them, then.I wondered if the holes were set that way to correspond to other repeat uses.'Man who say it cannot be done should not interrupt man doing it' ~ Chinese proverb
View Image
PA Dutch are not Dutch, or even a reasonable fascimile thereof, I won't even wear crocs<G>Happy Thanksgiving!http://www.tvwsolar.com
We'll have a kid
Or maybe we'll rent one
He's got to be straight
We don't want a bent one
He'll drink his baby brew
From a big brass cup
Someday he may be president
If things loosen up
Happy Thanksgiving HollyGot a question about your stair hackin thread. There were some stringers in there with the corners chamfered (at the riser - tread intersection). Any idea why that is? Maybe it makes it easier to get a tight fit?Thanks,
Steve'Man who say it cannot be done should not interrupt man doing it' ~ Chinese proverb
View Image
It's not coming to me right now... danged CRS, can you point me to the post?Time to coffee up before cleaning the turkey fryer, oh boy!Happy Thanksgiving to Allhttp://www.tvwsolar.com
We'll have a kid
Or maybe we'll rent one
He's got to be straight
We don't want a bent one
He'll drink his baby brew
From a big brass cup
Someday he may be president
If things loosen up
Holly,
Hope you had a great Thanksgiving and didn't have to resort to carving up the bird with that Kapex :)
Here's the photo below and the post is http://forums.taunton.com/tp-breaktime/messages?msg=54504.101
Thanks,
Steve
View Image'Man who say it cannot be done should not interrupt man doing it' ~ Chinese proverb
View Image
<Hope you had a great Thanksgiving and didn't have to resort to carving up the bird with that Kapex :) >Took a tip from cal, and used the slicing blade on the multi-master!Those stairs weren't mine, I'll try to call in Allen Schell, I'm pretty sure they were part of his work.http://www.tvwsolar.com
We'll have a kid
Or maybe we'll rent one
He's got to be straight
We don't want a bent one
He'll drink his baby brew
From a big brass cup
Someday he may be president
If things loosen up
Hey Allen, weren't you guilty of that stairectomy Fatroman posted?http://www.tvwsolar.com
We'll have a kid
Or maybe we'll rent one
He's got to be straight
We don't want a bent one
He'll drink his baby brew
From a big brass cup
Someday he may be president
If things loosen up
me guilty, it's unmistakeably true
So, what's the wisdom behind the chamfered stringers?Thanks'Man who say it cannot be done should not interrupt man doing it' ~ Chinese proverb
View Image
They're not chamfered, they're just 2x10s.If he had used 2x12s, the "chamfer" would be filled in.And if he had laid out right from the top edge, leaving a 90º corner, he would have had to weaken the 2x10 too much.AitchKay
Ah, that makes sense now. And if I had been smart enough to pick that up from Svenny's post above I wouldn't have asked twice.Thanks for the clarification'Man who say it cannot be done should not interrupt man doing it' ~ Chinese proverb
View Image
they are 2x12, we pull our layout off the inside point from a line.this gives the carriage more strength, it actually could be a lot bigger but we put temp treads on for construction use, hope that helps
Sometimes I'll have that if there's only a bit of difference between leaving the chamfer and going up to the next size lumber.John Svenson, builder, remodeler, NE Ohio
“Steve, I've posted a jig that's similar to hk's, but much lower tech... and, IMHO much more useful<G>”OOOHH!! Fightin' Words!Well, if, by “lower tech,” you mean, “more easily composted,” I’ll give you that. Sorry, next time I’ll try to find a more “organic” product to use than aluminum tube.But I guarantee you that lopping off a length of aluminum tubing without measuring, then eyeballing (again without measuring), drilling and tapping one hole is a heckuvalot less high-tech than setting up a router for multiple slots -- That's what I call lower tech.****“...IMHO much more useful<G>Any time you've achieved the same result with less effort, your product (that would be mine, in this case) is by definition "much more useful."****“The stretcher can be any length.” Check, BTDT. That was one reason FHB gave me that $150 for my design.****“I don't even care if they last<G>” Hey, I’m using lauan scraps! $.25/sq. ft!! Can you think of something MORE disposable? You wanna up the ante, you better design yours out of mud and/or grass clippings!****“Just scribe 'em off on the material, then...” Oh, but you’re already too late, Snort! -- In about the same amount of time that it took you to take out your pencil and run it along your guide, I’ve picked up my saw and run it along mine. And while you are walking over to, “cut 'em with Gabi's Kapex<g>,” I’m setting my finished treads in place.****You wanna Festize this operation, go straight to the 2nd-generation Festo rails to tweak my design. But skip the extra, unnecessary step of using the Kapex.AitchKay
<Check, BTDT. That was one reason FHB gave me that $150 for my design.>I hear they gave the guy that screwed sheetrock buckets to his boots $151, ha.http://www.tvwsolar.com
We'll have a kid
Or maybe we'll rent one
He's got to be straight
We don't want a bent one
He'll drink his baby brew
From a big brass cup
Someday he may be president
If things loosen up
Don't forget the guy who hung the tennis ball from the garage ceiling. I think the rule is they only allow three guys per decade per magazine to claim that one, so ya gotta hit Popular Science, Handyman, and all the rest pretty regularly if ya wanna get published.AitchKay
Gene,Here is how I used my Festool MFT and a scribing guide to cut the risers and treads on a stair i was working on http://blip.tv/file/483127 . The video was done some time ago and my son Joseph was the camera man ;-)
View Image
http://www.josephfusco.org
http://www.josephfusco.com
http://www.constructionforumsonline.com
Thanks, Joe. Nice film.
I took the time to detail out Gorsco's tread and riser fixing method with a Sketchup model and notes, and here are a couple of screencaps to 'splain it.
Thanks to all the other contributors. We've been taught some good stuff, here.
View Image
View Image
View Image
"A stripe is just as real as a dadgummed flower."
Gene Davis 1920-1985
Hi, Joe,Nice flick. I’ve got an MFT, too, so I know how easy it is to cut oddball angles on one. Easier than on most miter boxes. I’ve not tried the double-laser Kapex that Snort uses, so I’m not sure how the two of you would do in a race. But I’ll leave it to you guys to decide who gets the Silver, and who gets the Bronze:I just went out and cut a tread with my jig. With a tread lying unclamped on a pair of sawhorses, I pushed the button on my stopwatch, picked up my blue tape, taped the LH bullnose, set down the tape, picked up my jig, set it on the tread, spring-clamped both ends down and to the sawhorses, and made my cuts. About 45 seconds start-to-finish.I was using a 30-year-old Milwaukee sidewinder with a used 14-tooth blade, so, to achieve a clean cut, my actual cuts themselves took a tiny bit longer than yours. I could probably shave at least 2-3 seconds off of that time with a better saw/blade combo.At your scene-switch, you pick up with your jig already in place, and your knife already in the process of scribing your first cut, a 5-10 sec head-start. You go to re-set your depth-of-cut, to get ready to cut the tread, at about the 52-second mark, about 7 seconds after my tread was completely done. Your tread was done in about 1 min, 49 sec, but you get a 6-second credit for time spent changing the depth-of-cut.As I said, I’ll leave it to you and Snort to decide who gets the Silver, and who gets the Bronze.But thanks for the video. I always enjoy them, and I enjoy your approach to your trade.AitchKay
If it was all about speed, I'd use a chainsaw... and I won't have a Kapex 'til Gabi let's me test drive hers.http://www.tvwsolar.com
We'll have a kid
Or maybe we'll rent one
He's got to be straight
We don't want a bent one
He'll drink his baby brew
From a big brass cup
Someday he may be president
If things loosen up
"If it was all about speed, I'd use a chainsaw."Uhh... Yeah.But it's not. It's about ACCURACY first, combined with speed. So, if you can get a better fit while more than doubling your speed... What's Not To Like?It's a basic fact that every time you transfer a pattern, error creeps in. So avoid extra steps: set your template, duplicate it EXACTLY using its built-in jigging, and you're WAY better off than if you trace that pattern onto your stock and then attempt, freehand, to follow the line that you've just drawn.If you trust your own jig to transfer an exact pattern, then by definition, you have to trust my jig to spit out a perfect-fitting finished product. Shooting boards are not some radical, new concept, after all -- many of us out there use them every day, following in the footsteps of hundreds of thousands of our predecessors.AitchKay
AitchKay,Thanks for the comments on my video. . . I would agree that speed is an important aspect of many tasks in construction and woodworking, but if speed were the only test then you'd need to cut 200 more threads and come up with an average time. I don't think cutting a "one off" is a good gauge of the time it would take to cut "many".That said I like your jig and Gene's concept an I'm thinking about making one ;-). If I do, I'll post the results.
View Image
http://www.josephfusco.org
http://www.josephfusco.com
http://www.constructionforumsonline.com
Hi, Joe,Gene’s rendering of my Festo version is pretty much what I had been envisioning -- got to learn to generate drawings like that! As I said, when I wanted to make one, the only thing that was out there was the old-style Festo rail. If only they'd made the rails like the ones you have now. I complained to them about the lack of jig-attachment points, and I'd guess others must have been thinking along the same lines, because they’ve now added that top channel.********** Off the topic a bit, watching you knife your cuts made me think of cutting veneers: I often -- not always -- reach for a lauan shooting board for ply, just so that I can knife the line with it. I always use the Festo on flush doors, since I know I’ll be doing a fair amount of easing of those edges. But I don’t think I’ve even tried that rail on melamine, which chips if you look at it. How do you deal with those cuts? I’ve thought of gluing a thin strip of plexi to the Festo rail rather than the soft rubber so that I could knife my cuts, but I know I’d have to replace it more frequently then.**************** Back to our jigs, I understand an initial gut reaction (like Snort’s “chainsaw” comment) that if it is faster, it must be sloppier. But we’re all three using the same type of jig to do the same thing, right up to the point of marking and cutting.I focused on the speed aspect because after we’ve all copied angles and length, the difference in speed really is dramatic -- having the saw guide already exactly on both cutlines makes an amazing difference. I’d agree that one cut by each of us is not statistically valid, but eliminating a couple of unnecessary steps always speeds things up. I’d guess it’d be safe to say that the jig makes the marking and cutting process about twice as fast, saving maybe a half hour per flight.As for quality, which I know all three of us put first, I’d think that over those 200 cuts you propose, you’d see the most variation with the miter-box cuts, and the least with the jig, with the Festo rail system coming in a close second.BTW, Joe, how many movies do you have on your site? Pretty impressive!AitchKay
Hi AitchKay,I don't think that speed translates to "sloppiness", I'd just like an accurate expression of just how fast it would be to actually do "something". Cutting Melamine is always a pain in the a$$ and there are a few techniques I use. First and foremost is a good blade. Then I like to use tape, but not blue or masking, I like to use clear packing tape. Then there is the "two pass" or score method, Set your saw to cut about an 1/8" into the Melamine and make one complete pass then adjust the saw to through and make the second pass. This method always proves to be the best, but does take twice as long ;-). But, hey better then ruining the work. . . .I have about 40 or so videos, some better then others, but they have been slowly getting better over time.
View Image
http://www.josephfusco.org
http://www.josephfusco.com
http://www.constructionforumsonline.com
I've got another jig I'd like to try with either a lauan or a Festo rail:A panel saw rigged like a parallel-rule drawing board, the kind with the criss-crossing cables. Should be pretty easy to build. Biggest problem would be cables in the line of the cut, and the easiest way around that would probably be an extra-long rail with fail-safe end stops.I'm between shops right now, hoping to break ground still this season. Maybe when I'm finally in, and warm and dry...AitchKay
AitchKay,
It's funny how you talk about making luan
jigs. . . It's one of the topics of this months article on my site. Although I think the jig you describe would kinda defeat the concept of a track saw system, it might be fun to make.
View Image
http://www.josephfusco.org
http://www.josephfusco.com
http://www.constructionforumsonline.com
Edited 11/27/2009 7:43 pm ET by Joe
Install the skirts along wall behind stringers (carriage). Then install and level risers. Use 3" screws through the stringers to suck the skirts tight to risers. Back beveling risers slightly helps make a tight fit. Pre drilling, will stop the stringers from splitting. Once risers are tight, fit treads.
Fitted tread is set into place, reach over riser and use pencil to mark underside of tread for front riser/stringer locations. Remove tread and glue/nail blocks into tread on riser line.
Use PL on stringers, and run a bead along back of riser and side of skirt. Set tread into place and tap with rubber mallet. Nail through riser just under nose of tread into block. This fastens the front of the tread. Kneel on tread and screw through riser into back of tread.
Moulding covers nail holes under tread nose. Tread is now secured, in glue, with no visible fasteners. I have not had one squeak since I began this installing method.
That sounds like a good program for this, Gordsco. Thanks for the detailed description.
Since you may tend to suck the skirt away from the wall finish a little, when doing the screw-thru-carriage-to-draw-skirt-tight-to-riser-end, may I presume you are capping the skirts with a small molding?
What kind of mini-gun are you using to drive those screws through back low edge of riser into back tread edge? Things are getting tight in there.
View Image
"A stripe is just as real as a dadgummed flower."
Gene Davis 1920-1985
You guys sure like to make extra work for yourselves...........I order stairs as soon as the second floor is framed and have them delivered for install as soon as the structure is dried in. Cover and protect them well. Or use temps till the finish set is ready.
I don't get the efficiency of this method at all.
Last couple of sets I built could not have been manuevered into place fully assembled.... but I have installed a couple of easy straight runs that were shop-built.
I agree with you
to build beautiful stairs just to have them ruined during wet weather and be open for later recall because they squeak is not an option for me.
We use temp stairs until the roof is on and the building is closed in;have the stairs pre manufactured in the shop. In many cases it is even more economical than building them on site.
Depending on the finish- covering them is a must
>> You guys sure like to make extra work for yourselves...........I order stairs as soon as the second floor is framed and have them delivered for install as soon as the structure is dried in. Cover and protect them well. Or use temps till the finish set is ready.I don't get the efficiency of this method at all. <<We also have stair companies to build the stairs. Half the material and half the labor. It's amazing how much work goes into building stairs the way they do. The framers using 2x12's or lvl's which you don't need at all and then the trim carpenters have to finish them.Joe Carola
Edited 11/23/2009 9:18 am ET by Framer
I cover gaps at the wall with 2 mouldings. One flat to cover the plywood edge, the other, a small 1/2"cove to cover the gaps at the wall. I also use the 1/2" cove under the tread.
The screws behind the tread can be driven with an angle drill. I have a Milwaukee close quarters drill but I have switched to a 10.8v Hitachi driver, it's about the smallest in it's class and it can also easily drive the 3" X #8 screws needed to tighten the riser/skirt.
Gene,
You might not know that Gord is a stair specialist. He does more stairs in two weeks than I do in two years.
I have just adopted his technique wholesale. I would never have thought of drawing the skirt board into the riser ends like that.
Thanks, Gordie.
Ron
Plywood skirts, plywood risers, right? Makes sense to me.
Is solid lumber used if the skirts are longer than eight feet?
View Image
"A stripe is just as real as a dadgummed flower."
Gene Davis 1920-1985
Unless you are old enough to own a board stretcher, yes.
If the skirts are longer than 8' I try to match grain the ply and join near the nose of a tread. Less exposed skirt at that point. A couple of #20 biscuts helps a lot.
Solid lumber is never completely flat and it is tough to get tight risers and treads at the skirt without some scribe fitting.
I like that glue block trick, thanks.http://www.tvwsolar.com
We'll have a kid
Or maybe we'll rent one
He's got to be straight
We don't want a bent one
He'll drink his baby brew
From a big brass cup
Someday he may be president
If things loosen up
Gordsco, if one wanted to go for no visible fasteners in risers, would one want to face-fasten them only at tops to carriages, in the same area up along top edge that scotia mold would cover? Three nails or screws, plus all that great goo-glue, should keep things fixed for the next generation.
None at bottoms, as fixing of risers is assured by those screws driven into tread backs using that nice little impact driver.
View Image
"A stripe is just as real as a dadgummed flower."
Gene Davis 1920-1985
A picture is worth a thousand words?
The little Hitachi I have is not an impact, just a driver. Impacts give me a headache, and I can never tell audibly when the screw is set.
Yes, the face nailing under the nose of the tread (through the riser and into the cleat) holds the front till the glue sets.
The screws through the back of the riser and into the tread holds the back of the tread.
The only visible tread nails are in the top tread. I have created some locking cleats that hold the back of the top tread under the top riser, but for the sake of 2 16ga nails in an entire stairway, the 2 nails and filler are much quicker.
View Image
View Image
View Image
Gordsco,
Just to clarify, do you only place glue blocks at the front of tread/top of riser intersection? At first I thought that you were using glue blocks at the rough stringer to tread joint as well, but your pictures did not show that so maybe I misunderstood.Thanks for describing your technique by the way.
The glueblocks are nailed near the nose of the tread and fit tight to the back of the riser.
The risers are glued and nailed to the stringers and the nails are hidden by the tread at the bottom and a moulding at the top.
Thanks for the clarification. A really nice technique that you've got there.
may I suggest forget templates and try this??
http://forums.taunton.com/tp-breaktime/messages?msg=54504.65
I apologize for however much of this is repetitive, I haven't yet had chance to read this entire thread.
I've most always been able to set the skirts in first followed by the risers and finally the treads. Risers and treads always butting to the skirt board.
I too have found, on more than a few occasions, that if the skirt isn't sucked perfectly tight to the wall the treads can push the skirt out of alignment with the risers upon their installation - no fun to fix. I have two fixes to this: One has been to start gluing the skirts to the wall surface with PL and screw them into place rather than nailing them. I'll also try my best to get in and add blocking between the studs so there's plenty to fasten to. My second solution has been to revert to notching the skirts around the risers only. I install the risers first and shim them all plumb. I've found that alone makes things much easier on me as I can then - gingerly - walk the staircase. I always wind up tacking the skirt into place to mark my plumb and level cuts top and bottom anyways so after those are all marked I take a few minutes to scribe the riser locations up. Then it's over to the saw with a pitch block to finish marking everything. Notching does take a bit longer, but I think it makes for an easier installation overall whereas you can shim the risers tight AND have a joint that is essentially hidden from sight. Also, the treads now can be cut for a nice tight fit without fear of knocking the riser-skirt joint out of alignment.
So, I've now resorted to notching most of my jobs. I'm sure some here will argue otherwise, and to each their own, but I'm finding that this method really works much better.
Now that I think of it, this might make for a good photo thread next time I trim a stair case...
Nick
That would make for a great photo thread.