I am pouring a slab in for a garage, but the floor needs to be supported by 11 feet of fill dirt. I’m getting several recommendations from local Georgia builders and would also like some from this discussion. Questions of Dry dirt v. wet dirt, grade beam, etc. Thanks for your help.
Discussion Forum
Discussion Forum
Up Next
Video Shorts
Featured Story
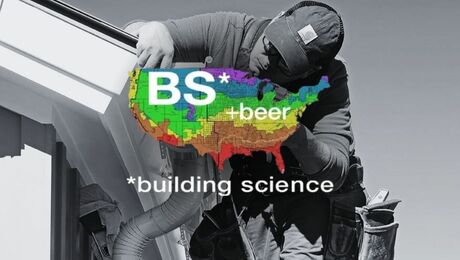
Fine Homebuilding is excited to be the official media partner of the 2024 Building Science Symposium series! This event offers builders, tradesmen, architects, designers and suppliers to discuss topics ranging…
Featured Video
How to Install Cable Rail Around Wood-Post CornersHighlights
"I have learned so much thanks to the searchable articles on the FHB website. I can confidently say that I expect to be a life-long subscriber." - M.K.
Replies
Why not use pre stressed concrete beams
slcbuild
Man! What do you guys build on in GA?
Dirt is what we dig up on our politicians. It's unstable for building on.
Dirt is what I wash off my hands before I eat. It's unsanitary.
Dirt what my wife sweeps up off the floor unless I just tracked it in. Then it's called something else and I sweep it up.
Dirt can be used to grow a poor crop in.
Don't you guys have any sound soils or gravel? If I were building on eleven feet of fill, it would be something like bank gravel base topped with inch minus, compacted in six inch lifts. I like my houses to stay where I put them.
I built a 30 x 36 garage 3 years ago and had the same concerns. I had about 8 ft of fill dirt inside 8 inch thick 8 ft high poured walls with a reinforced 4" slab over and backfill in front.
I made some concrete columns that rest on undisturbed earth by placing three seven foot 12 inch drain pipes along the center line and filling in around them. I left a 1 ft thick x two ft wide trench across these running the length of the building.
I put 6 mill poly over the whole area, cut holes over the columns, then put four re-bars in the trench with 6x6 wire mesh over the whole area, then poured the concrete to form the columns, the beam, and the slab, at the same time.
I used regular old Georgia red dirt and did not compact other than the bobcat running around on it.
I had a lot of discussion about this in this forum at the time and it was scarry, since some people predicted disaster if the dirt was not compacted to the n th degree and some said that the act of compacting would by itself cause the walls to balloon outward. Of course by the time I got this bad news I was too far into the project to change anything. You may still find this discussion in the archives but with all the website changes I'm not sure.
I use the place for a shop and park my truck in it and so far I have had no problems not even hairline cracks.
I filled in about 4 feet for my garage. But I used the "redneck compaction method". (Not necessarilly suitable to be considered as "fine homebuilding")
I brought the dirt in with a grain truck and dumped it. Then I used a farm tractor and blade to spread it out. Then took off in the truck and got another load. While the truck was still loaded, I drove back and forth over the dirt (with the loaded truck) until there were wheel tracks everywhere. Then I dumped the dirt, spread it out, and repeated the process about 15 times.
Worked great, but I don't know about filling 11 feet. Seems like a lot to me. No cracks in my slab since it was put in 8 years ago.
If we are here to help others, what are the others here for?
Ok. guy. At last I can answer a question on what I do daily. soil engineering
11 feet of dirt is alot of fill. It needs to be compacted or you will have structal problems. If the soil is going inside a block wall to support slab. You can use a clean sand, backfill in foot lifts compact with water. Fill the block with concrete before starting or you will collasp a wall. if it is an area fill . use a red sand clay mix ( southern dirt) or a non swelling clay with alot of sand in it. If it sticks to your feet do not use it. Do not use anything with organic in it, topsoil or sub soil. compact in a six to eight inch lift. Yes a pickup will do it if the lifts or not thick. Bob cat will not. Moisture of dirt around 8 % no wetter. Beat the hell out of it. Spend some time compacting about an hour per lift.
11 feet of fill you really need to talk to a local soil engineer testing lab. I wish I knew where you was.
Reply to Neal as he is the original poster. He could sure use that info.
I think the most important opinion you have recieved is to compact in lifts. I have done this too, but on a smaller scale, say for 3 to 4 feet. Your fill should be compacted every 6 to 12 inches.
If you are filling what are you doing about the down slope of the fill. A retaining wall? Or just run out? If a wall what kind? make sure it is "tied into" the fill. Many different ways depending on the type of wall, stone, concrete block etc.
With that much fill I would suggest looking at a completely different design option.
SUSPENDED FLOOR.
Put in a wallout (driveout) basement under the grage floor.
Cheap cost for twice the space.
SUSPENDED FLOOR.
Gonna take some engineering but what a cool idea.
It would take SOME engineering, but is not too tough.
I've seen it done before several times with spancrete.
Do Lipton Tea employees take coffee breaks?
Not that much engineeriing.
I have a 24 by 24 attached garage. The floor is 6" (I think and I am too lazy to find the prints) of concrete with a reasonable amount of rebar. And a single beam down the center with a post.
No engineering, just the specs on the design drawing.
How they did have to errect a lot of temporary supports for the pour. It has been a long time, but they used plywood and steel bar joist.
I know of several other house in the area that have similar construction.
In other parts of the country they use prefab tensioned slabs.
It is one of those things that everyone assumes is very hard (expensive) to do. But once you figure the cost of all of the fill and compacting and like one person did the piers and grade beam the extra cost is not that much. Specially for the amount of space that is gained.
Johnnie (Brownbag) is right on the money, Neal, and you'd do well to heed his advice. 11' is a real lot of dirt.
If you don't hit about 95% to 98% at optimal moisture content, you might be sorry in a few years. A couple percent of 11' is still a lot of settling when we're talking about a slab.
The guys talking about a deck are also giving you good advice. Reward wall systems has a product called C-Deck that you could easily make a concrete garage floor out of, and maybe even use the space below.
DRC
spancrete gets my vote....
what a cool space below. !Mike Smith Rhode Island : Design / Build / Repair / Restore
Yep, Spancrete is cool, too.
Given the amount of time and money we spend creating useable space, the idea of filling it full of dirt seems . . . well, I don't know, I guess it sounds like a potential workshop or something cool like that.
I couldn't bear to fill it full of dirt.
OK, I guess I could for the right price. <G>
BTW, Neal, if you do choose to fill it in, make sure the first lift of fill sits on a level bench. Backfill compacted over a slope is also asking for trouble.
DRC