how do I go about pouring a slab over an existing one, I have not been to the property yet, but from what I understand the slab is below grade outside, they don’t like the effect following a rainstorm. I would think I’ll be raising the floor atleast six inches. I was wondering if I was to use a 3/8 gravel on top of the old slab would that be sufficient separation? I thought sand but It would likely wash away. I’ve thought to maybe remove it entirely, but it is a 20 x 20 slab and a I would like to put it into a bin, however there isn’t really a spot to put one. I live in Toronto, The pad would be subjected to freezing, if you have some advice I’d love to hear it.
Discussion Forum
Discussion Forum
Up Next
Video Shorts
Featured Story
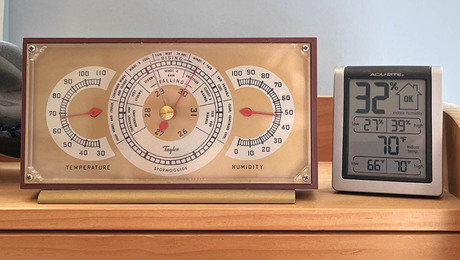
Source control, ventilation, and filtration are the keys to healthy indoor air quality. Dehumidification is important too.
Featured Video
How to Install Exterior Window TrimHighlights
"I have learned so much thanks to the searchable articles on the FHB website. I can confidently say that I expect to be a life-long subscriber." - M.K.
Replies
So, what will hold the sides of this news slab? Existing walls?
Or, are you planning on lifting the entire structure and raising it up?
What is the exiting exterior wall made of?
I'm really hoping the walls are block, I will pour between the walls not under them.
nick
Add insulation.
Just thought of this:
--Nail permanent treated form board to studs.
--One foot in from perimeter, set another form board, this one drilled for horizontal rebar ties.
--Set rebar in at least the perimeter of the existing slab to tie in to new.
--Pour full-thickness (to properly grab rebar) perimeter slab.
--Strip inner form board, add pea gravel, and pour remaining bulk of slab.
The perimeter slab should keep the main pour from blowing out the garage walls, and its full thickness makes for a better bond with the existing slab.
AitchKay
I'd scarify/scabble/bushhead old slap about an 1/8". Should be able to rent a machine at any good equip. rental place, not a HD store.
Not totally necessary but if possible cut a keyway in perimeter of existing slab.
Drill for 3/8" to 5/8" candycane rebar dowels anywhere from 1 - 2 1/2' centers.
Sweep old slab and keyway of all debris than ensure clean with blow pipe using same compressor for scabbler.
Epoxy dowel holes for added measure and place rebar dowels.
In keyway or just on cleaned slab, laydown a benonite waterstop, size for added slab thickness. Too big of water stop can blow new concrete. You also won't find this stuff at a box store or hardware, your concrete supplier can point you where to go.
Just before you pour, if you really want to never hear a problem from this job for as long as they own it, get a 2 part epoxy resin concrete bonding ajant and brush/squeegee on 1/2hr. before placing concrete.
If you don't do the above than at least mop on a slurry mix before pouring. You can mix any high cement content mix (i.e. anchoring, hydro, or grout mix) real soupy in 5gal. buckets and splash on slab spreading around. Doesn't take much as long as it isn't dried up before placing fresh mud.
Tie new mesh to candycane dowels. If you don't use bonding agent or slurry, tie mesh whenever but still moisten slab at least before pouring. If you do opt for bond or slurry wait to place mesh it'll be lots easier.
Finish top and chemically seal or wet cure for 15days if you can. Burlap bags/straw/canvas traps soaked wet and cover in plastic.
Skip wire mesh if using fibermesh mix, personally I'm not sold on fiber mesh. Other option with fiber is use more dowels or combine with lengths of rebar tied to dowels instead of mesh.
TA - DA, 2 slabs are now one ready to park an abrahams M-1 tank on, seriously, did a National Guard post with above methods, and waste water treatment tank bottoms same way too. It'll still crack, that's just what crete does but the benonite and epoxy bonding will be a huge factor for keeping water out from between the two slabs and freezing.
ncproperties ideas are good: it might not be a bad idea to skip the pea-pebble, and just throw money at the job by way of using extra concrete.
But address the form-blowout issues, which ncproperties doesn't mention.
Probably a combination of our recommendations is the answer, using my minimal perimeter pour to box things in.
The last thing you want is to see the garage walls splayed out and sitting in the backyard, with fresh-poured concrete setting up around the bottom plates.
AitchKay
Separate pours will add cost in forming material, labor, placement, and minimum load charge or at least extra delivery charges.
I don't think he'll need to be worried about blowing the perimeter. He said the existing is already below grade and thinks it's going to be a block rat wall. Even if existing TOC is just at exterior grade he said he'd be adding 6". To play worst case even adding 12" above grade against block he'd be fine. For peace of mind, on the out side of structure run form boards against block and kick it off.
We routinely run 24" thick footings, machine pads, and the like with no blow outs with nothing more than stacked 2x12"s, stakes every 16"-24" and kicked off. These are always vibrated to boot. Often the base grade is 1"-2" or more off the bottom form and this just gets some back backfill tossed against it to minimize oozing out the bottom.
Now you do bring to light two points I missed. One assuming the perimeter is block I forgot to mention ofcourse to place expansion joint on block. The second is I had not considered if the new pour would be above the height of the existing sill plate and studs. If that's the case you wouldn't want to pour between the studs anyway. Under 3" thick the exterior sheathing would still hold up but it wouldn't be right this way. Better to run 3/4" ply on inside to new TOC grade or fill stud cavities with blocking.
There's a fine line here of what would be right without seeing a picture or further detail on where the TOC falls and what's the grade like outside. Especially without knowing about any of this the whole project could be costing way more than it needs to and the answer is really to just run a curb and drain on the outside of garage.