*
I plan to slip form 11′ high concrete retaining walls in 4′ increments. Any suggestions, helpful hints or horror stories?
Discussion Forum
Discussion Forum
Up Next
Video Shorts
Featured Story
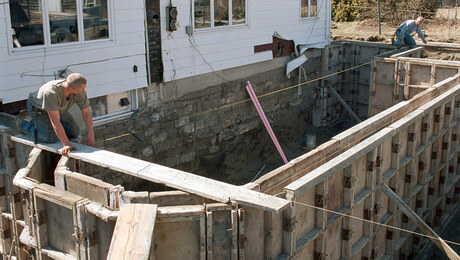
There are a number of ways to achieve a level foundation and mudsill.
Highlights
"I have learned so much thanks to the searchable articles on the FHB website. I can confidently say that I expect to be a life-long subscriber." - M.K.
Replies
*
Many years ago I worked on several slip form concrete pours including a silo that was probably about 100' tall (it could have grown somewhat in my memory...). We had no problems. I wonder, however, with the complexities and extra costs of slip forms, jacks, hi-early concrete, etc. what the advantage is of building a 4' form and jacking it up vs just builing an 11' form in the first place?
*I don't intend on moving the forms as I pour. I plan to pour 4' of the wall, let it harden and reform the next 4' section higher.
*Your method will compromise the strength and structural integrity of the wall.
*Kurt,it's a pity you can't pour it all in one -- as jc said, it will be weaker.However,When you've poured a section, as soon as all surface water has gone from the concrete take a soft brush and water and expose the aggregate on top of the pour to improve the bond at the construction joint. Careful just to expose the aggregate and not to dislodge it.For the first two sections be careful with your vibration that you don't bring fines to the top because that'll give you a weak joint too --- keep the poker about 18" down.If the finished wall needs to be water-retaining then you'll have to use a dumbell water-stop in the joints.
*Not really a slip form just breaking up what should be one pour into 3 different pours with 2 cold joints, to boot.Don't know the lenght, thickness, strenght, purpose or expected lateral loadings.Do know that it will be weaker than a single pour.Will need more steel to compensate, will need waterstop to seal.I think all in all I would rethink the plan, doesn't sound that great.Gabe
*It sounds like Kurt is working alone ar with a small crew to do a big job. The man's got courage. I hear him saying that for whatever reason, he's already decided to do it this way. I wouldn't go this way but if he is then let's give the advice he needs. An elevn foot high wall will pace a lot of pressure at the base while pouring. It will take a better than average form and just might be beyond his capability to build. So he likes the idea of slipforms. No they're not going to give him as good of a wall. He will need more steel but that's the cheapest part of a good concrete job. And maybe his soils and climate don't call for worrying about the waterproofing as much.So Kurt - the idea of rinsing the aggregate out might help the cold joint but it might be even better to use a trowel and scoop out a keyway along the top of the pour at each lift or ripp out some key forms to pound in from scrap lumber. Say 2x2" ripped at a 11 - 15 degree angle on two oppsite parralel sides - so you can take it out again for the next pour to lock into.
*Kurt,I tend to agree with Gabe's posted recommendations. The others all have pieces of good information, but realize that with compromise, there are associated "costs".I wouldn't worry too much about the cold joint bonding. If you have a proper amount of steel reinforcing the need for keyways and bonding agents is moot. If the wall must be watertight, then add a waterstop. It is more important, for a number of reasons, to eliminate excess hydraulic pressure from behind the wall, than to hold it back with waterstopping.You can choose to disguise the cold joint by installing chamfer strips on the inside of the forms.I'm not sure what the magic behind using 4 feet as your pour increment (plywood size maybe?) but if you could pour at least 8 feet on the first pour, you could top-out with a three foot pour. This would leave you with the cold joint higher on the wall, two set-ups instead of three, and a more managable second pour. You'll need a tremie (can't free-fall concrete over rebar more than four feet) and at least a four inch slump mix. Vibrate sparingly and pour slowly (in layers)unless your formwork skills are bulletproof.I'm curious what others, besides Gabe and me, that regularly pour large scale projects have to add to this.Eric
*Kurt,Do not 'vibrate sparingly' -- consolidation of the concrete is even more important with a retaining wall, which is subject to lateral stress and water penetration.Any voids left due to poor vibration can allow water to penetrate and corrode the rebar -- to say nothing of the loss in strength.Vibrate thoroughly, and make sure your formwork design will cope with thorough vibration.
*Ian,How much do you think you have to vibrate 4 inch slump concrete, when properly poured in lifts?I'll give you a hint; a lot less than most people think.As many form blow-outs can be attributed to over-vibration as can be attributed to poor form construction.But it is after all a free forum, and you are entitled voice to your opinions.Eric
*Eric,I don't consider a 4" slump an alternative to proper vibration.If the formwork blows out it is either due to bolt failure or poor formwork design.As to vibration, for a 12" wall I'd be looking for at least a 3" poker.To advise that a retaining wall, or indeed any structural concrete, should be 'sparingly vibrated' is bad advice.
*As a former concrete vibrator "hand" on many commercial/industrial projects I submit my 2 cents worth:Watch the vibrator's "field of action" in the concrete and adjust spacing of vibration so that the fields overlap.For deeper/wider walls use a larger vibrator. A "hi-cycle" vibrator will make the job easier than a 110v pencil vibrator.Fill the form with 3' of concrete before vibrating. Do not move the concrete horizontally with the vibrator as this will cause it to separate. Depending on your forming methods--add 3 more feet of concrete when the first layer begins to stiffen. Vibrate through the added and penetrate into the previously vibrated layer by 8" to prevent a cold joint. All concrete contains entrained air. The job of vibrating is to consolidate the concrete mixture and eliminate voids. Some air will rise when vibrating which indicates that the concrete is consolidating. Over vibrating (when the vibrator is allowed to sit and hammer in one place) will cause segregation and create air pockets.For the final authority on vibrating see the American Concrete Institute's publication ACI-309 "Guide for Consoldiation of Concrete."In my area any concrete retaining wall over 3' high needs to be engineered. Hopefully yours is and the engineer can give recomendations for cold joints, etc.
*Mike,What you describe is what I was trying to convey to Ian as my idea of a vibrator used sparingly. I have always followed and required adherance to ACI for all my jobs.For some reason, when the average laborer gets a vibrator in their hands, its like hooking them up to a morphine drip; they just can't get enough. They're moving concrete across the forms with it, leaving it in one place too long and trying to use it as a finishing tool, etc, etc, etc.Your post is full of correct and important information.Eric
*There's no need to convey the correct method of vibrating concrete to me -- it's the bad advice you've given to Kurt that I dislike.Had you given the detail that Mike did that would be fine but all you said was 'vibrate sparingly' which is capable of misinterpretation.
*This is what happens with no vibration. An 18 wheeler, loaded with 45 million dollars in artwork, drove over this electrical vault while delivering to an art museum. In the picture notice the lack of vibration and notice the exposed rebar and (and the leaves not cleaned before placing concrete).
*
I plan to slip form 11' high concrete retaining walls in 4' increments. Any suggestions, helpful hints or horror stories?