*
We have had very good luck building squek free floors using TJI’s and 3/4″ t&g plywood glued and nailed. The key is in the details. 1. we put a dallop of construction adhesive in every metal hanger. (this stops any movement of TJI in that hanger). 2. We snap, with caulk lines, every joist and pull any nails that miss a joist. This insures that all nails are in a joist. (nails that just miss a joist are the worst for making squeaks. 3. We nail the floor according to the engineered specs, never short nailing. This has worked for us for years. good luck,
Dormer
Discussion Forum
Discussion Forum
Up Next
Video Shorts
Featured Story
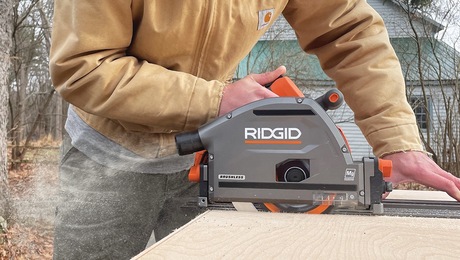
The best tool for straight, splinter-free cuts is made even better without a cord.
Featured Video
How to Install Cable Rail Around Wood-Post CornersHighlights
"I have learned so much thanks to the searchable articles on the FHB website. I can confidently say that I expect to be a life-long subscriber." - M.K.
Replies
*
Chris, Find out who your local rep is for Trus Joist MacMillan (TJI Joists) and give them a call. They GUARANTEE a squeak free floor if the install is done properly. They will provide you with assistance on sizing and a joist plan. Their software can also calculates a stiffness/performace rating for the floor based on several inputs like joist size, decking, ceiling applied to bottom of joists, etc.
*Good article in JLC on the very subject. As Brian mentions, Tru-Joist has software to help calculate exactly the floor you want."... a design that is rated at 55 is expected to be judged as "Good to Excellent" by 96% of the population, while 2% should judge such floors as "Marginal," and 2% should judge the floor to be "Unacceptable." You might be able to cut that $2000 somewhat with the proper calculations and still have a premium floor. 1 1/8 subfloor would be minimum for tile. If you are adamant on the subject, go with your gut and don't let your builder tell you what you want. You'll have to live with the floor you get.Click here for the Journal of Light Construction.P.S. I hope this link works (it's my first), if not the address is below.http://www.jlconline.com/jlc/archive/framing/floor_vibration/index.html
*I just completed a floor system using 1 1/8" Advantech OSB glued and screwed to 1 3/4" flange I-joists. I also used LP Solid Start 1 1/8" OSB rim joists nad LVL's for all carrying members. This is the most solid feeling floor I've ever built. While you'll spend a little more for this than for the typical 3/4" flooring, I'm pretty sure that you'll be happy with the results.
*
... I learn something new every day (which is good, because I forget something old every day too)... someone who took the TJI installation course that was going around, the one I was too busy to attend, told me the other day that joist hangers should never be installed touching the top flange of the TJI, leave them a bit loose to prevent squeaks there... also, a dab o' adhesive in the bottom of the hanger sounds like a plan. We usually screw (and glue) all our floors, if nothing else it sure lets the client know they're getting a quality job. Some subfloor adhesives are way too thick, we use something called Lumber Lock, works well even in the cold. As for stiffness, it's been my experience that going one step higher (closer spacing or deeper joists) than what is specified at L480 will get you a rock solid floor at very little additional cost. Haven't had any experience with subfloors thicker than 3/4", but sounds interesting.
*Chris,I thnk the I-joists are nice but I've never personally used them. You can even stay with standard lumber joists and screw and glue the ply down. use t&g ply for a better job. Don't letr the glue set too long before you apply your ply to it, as it will skin over. Also be sure that you use the glue in warm enough weather.Screwing with glue,Pete Draganic
*I think the glue should be sold like motor oil, with summer & winter formulations. During the winter, PL400 was difficult to gun but allowed a lot (too much?) of work time; during the summer it's a race against time, and the tube keeps spewing semi-fluid goop even after the pressure is off (leaving what my wife delicately calls "glue boogers" or, for big 'uns, "glue slugs")The someone will come out with 5W-40, the all-season solution for high-revving workers.
*Chris, the squeakyness of the floor has more to do with the installation technique than any other factor. I will garantee that I could produce a very squeaky floor using the heavier ply, and stiffer joists!The loudest floor that I ever encountered was the one in my first house. I latherd it with glue, nailed and re-nailed, and the damn thing squeaked like hell.I don't mind squeaky floor though. It's kinda like a built in burgler alarm (I don't lock my doors.) The pooches would go nuts if someone tried to sneak around my house. My current house is noticeably quieter in the summer. Dry lumber shrinks and is naturally noisier.Back to the subject:One of the most common methods of ply installation is probably the worst. The carpenters spread the glue for the entire run instead of sheet by sheet. Some of the glue "skins" before the ply is layed. They also avoid spreading it on the entiore length (they don't want it to mess up their beater board, and ultimately get on their hands).I "grease" each joist as I go. If the joist is a "doubler", I run a bead on each member. I double grease at the vertical joints. I also try to grease the entire 48 width of the sheet. I don't mind a little glue on hy hands because I always were gloves (even in 90 degree weather).One thing that will help that I do not do is fill the horizintal joints. This helps to stiffen the floor. The APA actually requires it, check the specs. I also nail each sheet 12" oc, and 10" on the joints, as I lay it. This ensures an excellent bond. Rarely do I hear squeaks anymore. Since I can plainly see where the joist are, missed nails are rare.I also do not put in cross bridging unless required by code (2x12's). Cross bridging is an owl killing squeaky addition that does nothing.The dab at the hangers sound good, although I only ran into one squeaky hanger problem. The builder later goes through and screws the floor. The system works.Blue, squeak free in MI
*Good point.In winter the glue is often difficult to apply, especially to frosted joist. I let exhaust of the generator keep the glue at the proper temp, or hook up a small heater. One time I had both running inside my van. The glue overheated, and spontaneously combusted. Luckily my partner was walking by as it popped, and we nipped the fore in the bud!I like to stand up one section of joist at a time, and sheet it that day. Of course, that doesn't always work out.Wet joist are tough too. I end up "balancing" the glue on the joist. Your suggestion is a good one. Most other glues have seasonal properrties.Of course, that'd be too complicated for carpenters!blue, goobing fool in MI
*Nail 10-12" oc and glue AND screws? Overkill? I have wondered about all this squeaky floor hysteria among new home buyers. Guess I've always lived in old houses, always ('til now) as a renter, so it just faded from notice. But walking down one of our hallways sounds like a hundred rabid mice in a dryer; that, I will ... eventually ... deal with. Seems the joists are twisting away from each other at the center bearing wall. No, I won't be installing bridging.I "greased" the grooves on the T&G, wondering how that would affect the theoretical 1/8" expansion allowance between the sheets? Dried glue is slightly compressible...Glad to hear there's a builder who will guarantee a squeaky floor?
*Paul, what was your joist spacing? 16, 19.2 or 24" o/c?
*Andrew, the builder goes through prior to carpeting and screws down any squeaky areas. They also put a few screws in each joist just because.The nailing I do is minimum, just to keep the ply tight as the glue sets. The less nails the better.I'd be glad to screw, if they'd be glad to pay the extra $300 (thats what they pay for the screwer).The twisting joists indicate a weak connection over the beam, and low quality lumber. Joists that are properly fastened, or blocked at the beam rarely twist. I have had some loads, however, that start out twisted. That's a pain to deal with. One of the biggest reasons that nails will pop out is also a common mistake. The carpenters let the joist cantilever past the beam. When the center of the joist is deflected downward, the end over the beam pops up, lossening the nails. Gluing the horizontal seam will definitely stiffen the floor system. It also quiets it. I've only done it a few times at the request of a builder, and probably woudn't do it otherwise. Like I've said, I'm way past that need for perfectionism. If your joist are borderline, though, it's a good suggestion.I don't remember ever having problems with expansion even when I greased the joints. I tend to pay attention to gaping though. It takes a bit more time at first, but soon becomes second nature. Most carpenters want to beat every sheet tight, but that is wrong.Ocassionly, I still will hear a squeak while I'm framing the rest of the house. I can usually trace the problem to a missed nail, or some other similar item. Otherwise, my floors are noticably quieter since I've changed my installation technique.One of the worst things you can do (I was taught this way) is to install the bridging prior to laying the sheets. There is always a difference in crown from one joist to the next, and installing the bridging locks that difference in. This allows small gaps to remain that will eventually become a singing canary. The nail doesn't pop out, it just sits tight while the ply rides up and down, singing the blues.Blue, trying to avoid rabid mice
*b.e.d., great insights into the floor-building process. If you're carpeting you're getting a bit of a break from the squeaks, and those that occur will be muffled. It's since we pulled up the carpet that the "problem" has worsened.The joists are face nailed with like 2 nails over the center foundation wall, i.e., not prevented from pulling apart. I can bring them together with a C-clamp, and plan to just throw in a few carriage bolts, maybe toescrew, & be done with it. Blocking is an unrewarding pain! And I don't think bridging these 2x10's would do any good. Remaining squeaks I hope to get by scabbing furring strips up tight with screws & construction adhesive. I don't understand why people care so much about squeaks but turn a blind eye to all the important things wrong with their house.The lumber is great quality, though -- 60 y.o., solid, & wicked strong. The modern stuff feels like cotton candy.
*
Glue and screw, 12 and 10 I do not consider overkill. Code here requires glue and 12 and 8 oc. Screws are builders choice.Alos mentioned was 3/4 ply ( or wafer) our inspectors would not allow that unless we are going over it with another layer. Most of us out here use 1 1/8 especially with I joists. When we deck a place we hae a few guys decking and shooting ringshanks to tack it and another following to screw the deck(ply or wafer). We also only glue for the sheet we are laying, well maybe one sheet ahead. I will also inspect from below any missed nails or screws. We try to over build our floors In these times of conservation engineers and designers will often push things to the limit as far as load and span so if we can use thicker ply or shorten the o.c. of the joists we will. but of course we have to run it by the design team to make sure that plumbing still fits and loads still line out. If a client comes to us wanting a house built and we use our arcitect and engineer then we will not have any questions.. Old houses with squeeks are characteristic and charming. but try building a custom home for a $$$client and have a floor bounce or squeek is not "Charming". We recently went into a newer home(not one of ours) that had drywall cracks near headers, a french door that would not seal and a cold room (duct was blocked) but the owners comments were "Its a well built home feel how solid the floor is". The most common complaint we here from other people about other homes is usually about the floors, bounce or squeek. SO..... if you came to us and asked about the floor I would recomend the bigger IJoists, tight o.c. and the thicker ply. Its cheeper now then fix it later...also for us in a 2400 sq ft house it would not cost a homeowner an extra $2000 unless you had some very very unusual floor plan that left lots of waste material.
Silver Hammer Construction, Oregon
*
Josh,
Are you building homes or bombshelters? I have only used 3/4 t&g 16" oc glued and ringshank gunnailed, for fifteen years... Carpet goes right on top, as does hardwood flooring, tile gets another layer of underlayment. No squeaks, no bounce,...its the least questioned thing I do!
Your guys must all have Popeye arms from carrying 100 pound 1 1/8" sheet goods to build your bombshelters er I mean solidly built homes.
Maybe it's time for this ADKer to move to the land of mist, sailboarding (The Hood River!)and unlimited income clients,
Jack : )
*
11/8" glued and screwed 16"oc glue one sheet at a time, lay it down and then pull it up and lay it down again. Always check for shiners from below. avoid blocking or bridging if possible.
Pat
*AD JackTrue we can run 3/4 on 2x joists on 16 o.c.Provided we are not trying to stretch the spans and we will try to run one size up if possible. Like you mentioned we also then run underlayment or tile backer or hardwood and before you know it your up to 1 1/8 combined if not more. I believe the original question was in reference to TJ-Is and that is where our code calls out for 1 1/8 ply especially with higher spans noted by the deflection. We use TJIs where we have long spans to begin with like over 20 feet. Otherwise out here 2x12 are cheeper in some cases. We do not rely on carpet pad to hide noise.We are not trying to build bomb shelters nor homes of manufactured home quality just homes that will stand up for 100 years and stand up to earthquakes. As we know codes are different through out the country for various reasons like insulation values, footing depths, etc. Maybe our code is a little different for TJI floors.Just a question for grins what or how do your costs comapre. 1 1/8 fir 7 ply is $31, 3/4 5 ply is 17, 1/2 inch 4 ply is 12, 2x12 #2 fir is 90centsfoot 2x6 is 37cents foot.7/16 wafer is $6.50
*As previously mentioned, squeaky floors are strictly a function of installation technique. However, based on past experience with TJI SILENT FLOOR systems, believe me, design with L/600 deflection min spec. You will probably be happier with the TJI-15s (1.5 inch) from both a cost and performance standpoint. The 19.2 spacing is nice, and should yield satisfactory results when used in conjunction with L/600 spec. One very important consideration concerns placement of heavy furniture along walls which run parallel to spanned joists. The dead load floor spec (in excess of the 60lb/sqft. for furniture+wall weight) design requirement we have placed on the flooring system is usually pushed a bit in these areas. Its not the floor will fail (collapse), its more the fact that it will be spongy (especially mid-span) when walked on and you wont be happy with it. I recommend doubly up on joists in these areas. I use 3/4 T/G OSB on these systems and am very pleased with the performance.
*Chris,Joist spacing was 16" O.C. Bearing at exterior walls was on 6" wall (less 1 1/8" rim.) Bearing at interior walls was full length across 6" wall. We used squash blocks at all point loading areas and backer and filler where indicated on our TJI plan. We also used a squirt of polyurethane adhesive in the seats of all hangers before dropping the joists in place. We used a LOT of screws and glue on this job, maybe a dozen 29 oz. tubes of poly and 3000 screws (thank you, QuickDrive) for 1450 sq. ft.
*
I am specifying some of the framing requirements for a new home and am very concerned about bouncy and squeaky floors. My current home's floors squeak and bounce horrendously (2x10s, 16"o/c, 3/4"T&G ply, glued & nailed in the rainy Seattle area.)
My thoughts: 1-1/8" T&G plywood, 2.5"(or better)-wide flange I-joists @ 24" o/c, sized for L/960 deflection. Glued and SCREWED.
My builder recommends 3/4" T&G OSB, 1.5"-wide flange I-joists @ 19.2"o/c, sized for L/480 deflection. Glued and NAILED.
I think my method will cost about $2000 more for a 2300 sq ft house, but probably worth it.
Would I need additional subfloor for any areas to be tiled?
Is this overkill? What are your thoughts?
*Chris - I don't think most "bounce" is caused by the plywood or the flange width of the I-joists. It's more a relationship to the depth/span ratio of the floor system. I generally recommend a span/depth ratio of about 18 to 1. For example, a 12" deep I-joists spanning no more than 18'. In my experience, if a floor system will work at 24" O.C., it probably will not have too much bounce. I think the reasoning for that is that the people that I've deal with want a real shallow floor system. They tend to want to accomplish that by closing up the spacing of their floor system to 16" or even 12" O.C. so really shallow joists or trusses will work. (on paper, anyway)There are formulas to calc the frequency in hertz that a floor vibrates at. I can try to send you that if you're interested.
*... and hang in there for the screws. Nails subjected to repeated pulls and pushes can't help but loosen -- and squeak!I used sell-drilling self-countersinking steel screws from McFeely's that were extremely easy to use. With an auto-feed gun, it would be a trivial task. Screws are much more expensive than nails.
*We have had very good luck building squek free floors using TJI's and 3/4" t&g plywood glued and nailed. The key is in the details. 1. we put a dallop of construction adhesive in every metal hanger. (this stops any movement of TJI in that hanger). 2. We snap, with caulk lines, every joist and pull any nails that miss a joist. This insures that all nails are in a joist. (nails that just miss a joist are the worst for making squeaks. 3. We nail the floor according to the engineered specs, never short nailing. This has worked for us for years. good luck,Dormer