*
We are going to try things out on a 6 foot straight vanity top. Fiber in the mix, a little mesh, a little light rebar around the sink opening, steel trowel the top, edge the front and end with a little roundover. We will form it up on sawhorses in the adjacent room, use a little vegetable oil on the ply forms for release, and carry it in when done. We want sort of a leather look in the color, red-brown with some variegation. We were thinking of a concrete stain, then a clearcoat of moisture curing urethane. Any experienced folks, please comment. If it doesn’t work out we will just bury it in the yard and go buy a slab of granite.
Discussion Forum
Discussion Forum
Up Next
Video Shorts
Featured Story
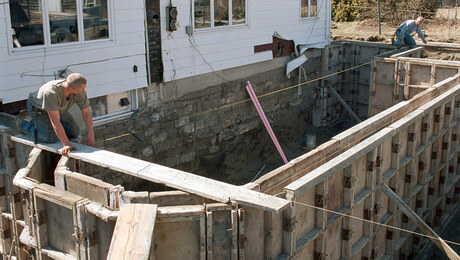
There are a number of ways to achieve a level foundation and mudsill.
Featured Video
How to Install Exterior Window TrimHighlights
"I have learned so much thanks to the searchable articles on the FHB website. I can confidently say that I expect to be a life-long subscriber." - M.K.
Replies
*
I'm pretty sure Larson makes a line of concrete stains, and Stain-Crete from Increte Systems makes them. The last concrete top that I did I used a TAMMs product for the sealant, and I loved it. It was buildable, and food safe. I don't remember the product number, but the trade mane was Luster (or Lester?) Seal. Great stuff, and sandable with a palm sander to remove dust and bubbles.
Nate
*Fiber in the mix is not gonna look too good unless you like the Chia pet look.....vegetable oil will go rancid eventually. Joe H
*i used kemiko acid stain of my floor
*I was thinking the fiber would look bad too, unless there's some way to hide it I don't know about, which wouldn't surprise me much.MD
*We are going to hand trowel the show surface dead steel smooth. The side against the form will be the downside, laid on the cabinet tops. We'll do a hole for a top mount sink, and use stone drills with core bits to place faucet holes. I read somewhere that some outfit in the concrete countertop biz used fiber-reinforced mix to eliminate cracking. When I was back in commercial construction, we used it all the time for floor slabs in all kinds of manufacturing plants. I never recall seeing any fiber show on a steel troweled surface. Quikcrete's web page touts the use of their non-shrink precision grout as the thing to use to cast countertops. What are you guys using? In the Kemiko line of concrete stains, what color gives a leather look?
*You guys with concrete countertops - they look pretty good when they're new, but do you have a problem with stains? Particularly from food acids?
*I never had any problems with staining, and if you really want to be sure about the staining, you can have Berylux added to the mix. It's about $3.00/yd adder. There are several companies making a "Stealth Fiber" that is very fine, and lays down nicely. Even if you do get some hairs coming up, they can be burnt off with a torch, and everything will look fine. Good Luck.Nate
*Gene- Why not block out with appropriately sized pvc pipe for your sink fixtures instead of drilling? You can pour a base coat half your pour thickness with the fiber and then switch to white cement for your pigment mix without the fiber. Pour a little Daraweld C bonding agent in the mix and brush the bottom coat before pouring on top. Cracks won't necessarily develop all that quick if they're gonna.
*OK, I will lose the idea of the fiber-reinforced mix. Quikcrete's website tells me that their "Precision Grout" mix is the right product for concrete countertops. This little vanity top "trial run" that we will do will require, at 150 pounds per cubic feet, about 7 fifty pound bags of mix, plus water. We are figuring to form for a 1-1/2 inch thick top. What do you guys think should be the product, or recipe, to be used for the mix. It is too small a job for a call to the redi-mix plant for a truck. The spec for the Quikcrete product rates it as a nonshrinking product, developing in excess of 14000 psi at 28 days. Does this sound right, or should we just use a plain "gravel mix" recipe?
*Gene, I'll fire of a little info sheet to you that has a batch recipe in it. I highly encourage you to mix your own and not use bagged pre-mixes. The info sheet is a little messy, but may have some useful words in it.If you're going to trowel, I also encourage you to set a couple of pieces of properly sized dowel where your plumbing penetrations will go. Make them, say...1 1/4" tall...so after your pour you'll have about 1/4" of mix over the top of the dowel. You can make them a bit taller should you choose to. This way the dowel will save you a bit of concrete drilling, and it won't interfere with your troweling. Attach them to the form by screwing them from below, through the bed of your form.You can drill through the concrete, get to the dowel, use a wood bit to core the dowel then break the rest of it out. Another option...which is what I do...slightly taper the dowel with a beltsander or something similar, then "pop" it out with a mallet.If you're good with a trowel, just make the dowels the full thickness of the slab. One good thing about the dowels...it keeps you from goofing and placing rebar where the plumbing is to go. It's mighty tough to drill rebar.Ensure that your plumbing fixtures have enough thread to be installed in a 1.5" slab.Your 6' slab, less the sink cutout will weigh around 195 pounds. You may want to consider leaving the sink blank in the slab until after the slab is moved to its final position.
*As long as you don't make the mix too wet, you shouldn't get any cracking.Careful with the cure (cover w plastic, mist each day) so the slab doesn't curl.The FHb issue a couple of years back that had an article about a cast-in-place top...where the mix was delivered from a redi-mix truck...they detailed an acid-stain, leather-look finish.