I’m about to pull out what little hair I have as I try to tune up my old 10″ Craftsman table saw. Referring to an FWW article on table saw tuneups, I loosened the six bolts that connect the blade carriage to the table top and trued up the saw. However, when I very slowly and carefully screw down the top (using a 1,3,4,2,5,6 sequence – 1,2,3 and 4,5,6 on each end) I consistently end up with a cut which is about 1/16″ off in 12″ of cut. It appears to me that the bolt holes in the carriage are just slightly larger than the bolts so there isn’t much room to play with the adjustment. I also tried mis-adjusting the top with a 1/16″ offset in the hopes that once it was tightend down, it would end up square, but no such luck. I’m thinking of enlarging the bolt holes to give me more room to play. Any suggestions? Thanks.
Discussion Forum
Discussion Forum
Up Next
Video Shorts
Featured Story
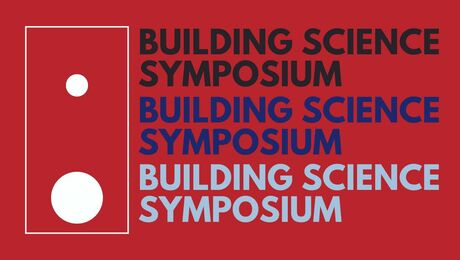
Fine Homebuilding is excited to be the official media partner of the 2024 Building Science Symposium series! This event offers builders, tradesmen, architects, designers and suppliers to discuss topics ranging…
Featured Video
SawStop's Portable Tablesaw is Bigger and Better Than BeforeHighlights
"I have learned so much thanks to the searchable articles on the FHB website. I can confidently say that I expect to be a life-long subscriber." - M.K.
Replies
This is based on the assumumption you are referring to a Craftsman belt driven 10" saw and not one of their smaller tabletop saws. If that is incorrect you can stop reading now.
I'm not aware of the details of how FWW article describes truing the blade the but I can share the instructions for truing the blade parallel with the miter gauge groove from the Craftsman Owners Manual for the 10" table saw. I've used this system to keep my blade in true for the 10 or 12 years I've had the saw. If you don't have the owners manual let me know and I will send the instructions along.
That is the saw that I have and I don't have the instruction manual. Any instructions you can send on are appreciated.
Thanks!
wmax;
The first step in the instructions is to check whether the blade is parallel to miter gauge groove using a combination square against a single blade tooth at front and rear of blade. Obviously you've done this and know it is not parallel.
The following is copied from the owners manual for the saw. Some of it may sound simplistic---no insult intended or implied. I'm just copying verbatim now.
Adjusting Blade Parallel to Miter Gauge Groove
If tooth does not touch the same amount, the mechanism underneath must be adjusted to make the blade parallel to the groove.
The rear trunion must be moved toward the combination square if there is space between square and the tooth at the rear of the blade. If the square is pushed away from the edge of the groove the rear trunion must be moved away from the square.
Loosen all three screws that hold the rear trunion and all three screws that hold the front trunion.
Using a wooden block and mallet move the rear trunion to right or left as required to realign the blade. If necessary, shift front trunion in similar manner but do not move front trunion unless necessary. Recheck alignment of blade the tighten all six trunion screws.
A couple of things I've learned over doing this.
Remove the saw blade insert to to get to the trunions to tap them.
Don't loosen the screws much. Just enough to allow the trunions to shift under pressure.
If you're totally resetting the blade, as you are. Set the front trunion to the correct spacing, snug up the screws then adjust the rear trunion. You may have to do this a couple of times to get it set correctly.
Removing the motor make it easier to get to the trunion bolts. Also tilting the blade to 45 degrees makes it easier to get to the left front trunion screw. It has to go back to 90 degrees to check its setting. I don't tighten in sequence. Tighten front center trunion screw first, then rear center trunion screw, then outside two screws in front and outside two screws in rear.
The owners manual is available from Sears parts. Use the link below then enter your model number to get to the parts lists.
http://www3.sears.com/
Good luck and don't pull your hair out quite yet. Sorry to be so long winded but hopefully this will help.
Russ
Russ, and everybody else who contributed advice - thanks to all. I finally got a chance to get back to the saw this evening and was finally able to get the accuracy I wanted. Although I was basically on the right track, I missed an important detail that made it impossible to fix the adjustment. I had thought that tapping the table itself was needed to make the adjustment, but (and I'm a bit embarrassed to admit this) I had it backwards! After I started making my taps on the carriage, I was able to get it right. I also found it worked best to tighten two bolts fore and aft and then tighten the flanking bolts to minimize the drift.
Thanks again, everyone!
If you start with a 1/16 offset and it still goes 1/16 off the other way, sounds like maybe there's a groove or some wear spot that makes the carriage return to the same place. Have you tried to remove the carriage completely and clean all burrs and crud from the mating surfaces?
I'm sorry, I thought you wanted it done the right way.
Ed,
As Russel asked, I do have a belt driven saw that he has instructions for that he can send on. But I will also take your suggestion and take the whole top off for a closer inspection. Thanks!
Wit the top in place, the fully extended blade must be parrallel to either edge,left or right, of your tablesaw.
Tighten the bolts in sequence as you did but without torqueing down fully. With a dead blow hammer(or other) tap the top until it is aligned. Torque the bolts to their setting. Then check the fence is also parallel to the blade, adjust if necessary. Done.
>>> the fully extended blade must be parrallel to either edge,left or right, of your tablesaw.
Don't mind me for being a stickler, but this is not necessarily true. Blade must be parallel to the miter groove, that's the reference that usually gets used with cross-cutting sleds. Common sense makes us assume that the left and right edges should be parallel to each other as well as to the groove, but that may not always be so. If one is concerned about accuracy, why not refer to the edge that's most relevant in this case ie the miter groove.
you're correct, the miter guage is a better reference for parallel. But the miter guage itself should be parallel to the tablesaw edge. If it's not machined that way, the extension bolted on will introduce new problems.
Edited 6/21/2005 9:09 am ET by jackplane
There is a product on the market referred to as PALS. They are 90 degree angle brackets with set screws that go on the rear trunion and will allow for fine adjustment. Not a lot of $. Go to http://www.in-lineindustries.com web site.
>>> the miter guage itself should be parallel to the tablesaw edge.
Agreed, it should.
>>> If it's not machined that way, the extension bolted on will introduce new problems.
I'm sorry Jackplane, I still don't understand what the new problems would be if it isn't. The table edge (as well as the extension's edge) needs to be square to the face, so that when the 2 are bolted together, their tops are co-planar.
The edge(s) can be still be off WRT the miter grooves (i.e. not 100% parallel) and you can still cut accurately as long as 1) you adjuct the blade to be parallel with the groove, and 2) as long as you use the groove when cross cutting with a homemade sled.
If you want to use the edges as a reference for cross-cutting (it's possible) then you need to 1)adjust the blade to be parallel with the edge, 2) hope that's also parallel to the groove if you want to use the miter guage.
Really not trying to be argumentative or disrespectful, just wish to learn what I'm missing if any. thanks.
What I'm saying is, the table edge should be parallel to the mitre groove. If not, a standard extension bolted on for the fence will be out of square. Of course, this can be cut at a slight angle to offset this, but then that brings into question the overall quality of the saw.
The table edges are not used as a reference for either cross cutting or ripping.It really does not matter what they are in reference to the saw blade.They can be scolloped. the only reqirement is that for the front edge is that there be some place to mount fence rail.And on the sides that it provides a place for the extension tables to mount and be colplaner.
Workbench mag this month has a good article on tuning up a TS
Caution: This message may contain "For Official Use Only" (FOUO) or other "sensitive information" is not intended for non-official disclosure. Do not disseminate this message, except to persons who require it for official Breaktime purposes, without the approval of the individual originating this message or other authorized official of the Taunton University. If you received this message in error, please delete it.
I second the Inline-Ind accessory for alignment.I saw that guy years ago at a trade show, and complained to him about trying to follow Sears instructions to get a cut as good as his show demo. Then he reached underneath for a box of parts. The kit adds a set screw on both sides for adjustment. His belt & pulley are great too, as is his mitre guide.
Good to hear.
He sent me his video that showed him installing a couple of grease fittings to the blade lift and tilt gears. Have you added them? I've got all the parts...just wasn't looking forward to disassembling/reassembling the saw.
JIM
Jim, I did not know that grease fittings are available -- but it's definitely a great idea for that old Craftsman TS. I have occasionally vacuumed out the inside and sprayed the threads with WD-40. Helps for a while. I think I'll look at their website. I think when I upgraded my saw there was no internet, have things changed or what ...
I bought the grease fittings and tap in a regular hardware store. Jerry Cole recommended 90 degree angle fittings. I got 45's and 90's. Very inexpensive. Automotive parts stores carry them also. You can also buy a single tap instead of a whole set. The video shows how he recommends doing it....very simple. I spoke to him on the phone and he said that he can raise or tilt the blade with one finger and it saves wear and tear on the bearings. I'm a believer.