Hi All. I am faced with the atypical task, at least in my area of managing a hard wood floor project that will consist of super wide reclaimed boards. The board are at this point surfaced two sides and are 7/8″ thick, 18″ wide and about 14′ long. I just got through a meeting with some potential installers. They seemed to have a game plan but there were in my opinion a few red flags. Here is a quick rundown of their approach. They will have the boards jointed and have tongue and grooves milled. Also they will have a slight bevel ran at the top edges. The ends will be grooved for splines. They will deliver the boards to the (conditioned) site and stack them with “stickers” to separate the boards to allow air flow and allow the boards to acclimate for a week. To take from an unconditionioned to a conditioned space and expect the boards to acclimate in a week seems to me a too abrupt temperature/humidity change in too short of a time. Then they will install by gluing and nailing through the tongues. The gluing is a red flag. It was my mistake not to find out more about that procedure during the meeting. To give them the benefit of the doubt I am assuming they are spot gluing where the glue would take the place of a face nail rather than trowelling the glue under the entire board. Also the chamfers were a red flag because this would indicate that the would not be sanding in place. And this of course would mean each board would need completely sanded before installation and very consistent board thickness would be required. Also there are two floating staircases on metal frames with the treads attached with four 3/4″ X 5/16 lags at abour four inches from each edge. They suggested showing the end grain rather than mitering in returns. Does anyone have experience with this type of install? These treads I fear, as I fear the wide boards ingeneral, are in danger of cupping. The stock is oak reclaimed from a cider mill and I am assuming it is very old. The job is very high end. The boards at this time have nail holes with oxidized iron stains. I know my client well. He may like the character of these boards but he will demand a pristine installation. Any thoughts or further questions are more than welcome. Also I’d like you add that this is a great client of mine who is very reasonable.
Discussion Forum
Discussion Forum
Up Next
Video Shorts
Featured Story
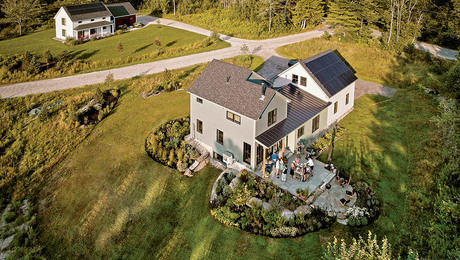
By considering things like energy-efficient mechanicals, window orientation, and renewable energy sources, homes can be evaluated to meet the energy codes. Here's what the IRC has to say.
Highlights
"I have learned so much thanks to the searchable articles on the FHB website. I can confidently say that I expect to be a life-long subscriber." - M.K.
Replies
Your flooring lumber will only change dimension (and perhaps shape) with changes in moisture content. Rougly 1% change in dimension for every 4% in moisture content change. Acclimation time and temperature are not the most relevant factors; it depends mainly on MC delta. If there is no delta, then there is no acclimation time needed. Continuoulsy control the moisture content and you control the stability of your flooring. With 18" wide stock at 7/8" thick, that's easier said then done. If you don't own a good moisture meter and hygrometer, then buy 'em. You'll need them. I also hope that you client has complete annual control of the dwelling's relative humidity. You'll need that as well. In short, It's an incomplete game plan if you don't plan to document and monitor MC & RH every step of the project-- and warranty period.
Hi again. As I think about this, how would one quantify 1% change I dimension? Shrinking? warping? Both? Is that a lot or a little. Thanks again.
Thanks for the good advice. The humidity in the space is regulated by a steam unit as part of the HVAC system. I will definately be aware of the moisture content. To my surprise he purchased the stock yesterday in Waynesboro Pa.
Perhaps a steam unit can regulate how much moisture gets introduced to the conditioned space, but how are you going to regulate R.H. if it needs to be reduced?.
I talked to him today about the humidity factor. If the above is correct 1% dimensional change per 4% RH change and the humidity range from winter to summer is 45% to 60% that's 4% dimensional change after install. Let alone bringing the humidity level down from a unconditioned warehouse to the conditioned home. I saw a couple samples of the stock today that were planed down to 7/8". There were still band saw marks visible. I am not sure they can even get 3/4" inch out of it. We'll see. I am trying to walk the thin line between naysayer and cautious pragmatist.
The 4% change is in moisture content, not relative humidity. Two different animals. So, for example, if your warehouse conditions have the wood at 10% M.C. and it acclimates to 6% in the home (not unreallistic), then your width dimensional change is 1% of 18". Or, iIn other words, over 1/8" in potential shrinkage for each plank. Add that up for each plank across the floor and (depending on your installation technique) you have a receipe for disaster in terms of wood stress being resolved at fastening points, checking, or gappage at each plank.
If you're a pragmatist, you'll start documenting existing conditions (both the wood itself and environmental conditios of the warehouse and conditioned home) as soon as possible.
I don't see how you can get a sound installation of planks that wide without face nailing.
Just one week?
My 2 1/4" red oak floor sat for two weeks in my home before it was installed. Your wood is almost 9 x larger.
IMH DIYer opinion, I would want a lot more time than just a single week.
Good luck.
Thanks to everyone for your thoughts!
Quick
http://www.woodweb.com/cgi-bin/calculators/calc.pl?calculator=shrinkage
I wouldn't think it reasonable to use 18" wide oak boards as flooring and not expect some issues down the line no matter how careful the science used in mosture management.
If the client is even a little fussy I'd predict dissatisfaction sooner or later.
Wood is a natural amazing substance and needs to be appreciated and respected for what it is.
Thanks for the input. I have talked to him several times about what he can reasonably expect from the stock. He says he understands and will accept it for what it is.
Thanks for the input. I have talked to him several times about what he can reasonably expect from the stock. He says he understands and will accept it for what it is.
As an update to the original post. I found out the installers were planning on troweling the glue under the full board with this product. wakol ms 290. He says he used it successfully before. I need to research it but thought if anyone has experience with it they can chime in.
maybe...
I've never glued a wood floor so I can't really say but it seems if there was some magic adhesive that was flexible enough to move back and forth with the boards maybe it would work. I don't know of such a magic substance and would be suspicious of claims.
But what do I know? Once a client wanted me to put down a floor with 9 and 11" boards. I told him it probably wouldn't work well but if you insist....
The boards were reclaimed old growth fir [ that improved the odds] and we splined each edge, face gun nailed it with a framing gun and filled the nail holes with custom colored filler. It came out great and still looks good 12 years later. So maybe I am wrong now and then......
Myself and just about everyone I know feels the same way but I felt I should explore the adhesive the installers recommended. It is called Wakol ms 290. I talked to some venders in Vermont and New Hampshire where I am assuming wide planks are installed more often. The consensus was this was a great product to use. I talked to the rep in my area and he was convincing too. There spec sheet covers relative humidity change in the home and it wasn't the normal range . Our goal is to get the moisture content to within 2% of the existing subfloor before installation. After all the discussion I had I am leaning toward having grooves milled on both sides and using splines. Using screws ran through a plywood block to pull out any cups or warps and removing the screws after the glue is set.
Two somewhat contradictory observations:
It's my impression that the seasonal change in lumber dimensions (driven by humidity) is reduced somewhat (perhaps by half) as the lumber ages. So using reclaimed wood might conceivably reduce the concern about seasonal change (though if this wood is ripped from beams vs being simply planed from old lumber then it would have some of the attributes of "new lumber").
With wide planks there is a danger that shrinkage could amount to more than the length of the tongue, resulting in adjacent planks coming totally disconnected from each other.
They're not contradictory because the first one is false. Wood does not lose the abiltiy to shrink and swell with moisture over time--unless it is rotten.