Discussion Forum
Discussion Forum
Up Next
Video Shorts
Featured Story
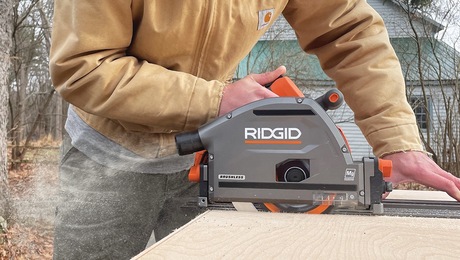
The best tool for straight, splinter-free cuts is made even better without a cord.
Featured Video
SawStop's Portable Tablesaw is Bigger and Better Than BeforeHighlights
"I have learned so much thanks to the searchable articles on the FHB website. I can confidently say that I expect to be a life-long subscriber." - M.K.
Replies
*
i have an excess amount of poplar and was wondering if this would be okay to use to make drawers for kitchen cabinets.
*It sure would, so long as it's true, or you can get it true. Sliante.
*You bet,I'd surface it down to 1/2" and if it has a bow, turn it to the inside of the drawer.Ed. Williams
*I LOVE working with poplar. Machines beautifully, holds an edge, very little edge splintering. Good stuff.
*I like that it's soft enough that i don't have to pre-drill the holes for mounting the drawer slides.
*I sure hope so...it's what I used in my own kitchen. Unlike Ed, I only took it down to 5/8ths.
*I find it interesting how peoples different backgrounds lead to different work habits and conventions. With me, 8-10 mm (3/8"-) is standard for drawer sides and backs unless I'm fitting side mount slides- rare, or the drawer is large. But Undermount slides (Hafele, or Tandem for e.g.) or drawers with no slides nearly always get the thinner material. I'm not fond of poplar drawer sides in traditional drawer work, but for contemporary kitchen cabinets and the like it's generally more than good enough. I just don't like the way the stuff matures into a muddy grey/yellow/brown streaked look. Just for interest the attachment is a typical example from my oeuvre. Yes, I know. Far too labour intensive for yer average modern kitchen! Sliante.
*That's nice Sgian. Elegant but very sturdy looking too. I like that. I really like plain old box joints too.Hey, as long as we're talkin' drawers, do you guys make your drawer backs 3/8, or maybe 1/2" shorter than the sides? Or do you make all three pieces the same height?
*Not too labor intensive for my tastes, too language intensive. Oeuvre? C'mon, you're making me think, and that hurts!
*Tex,I've seen many different carpenters/cabinetmakers make drawers as many different ways. Some like to cut the back short in height and project the bottom flush with the back of the back. Some dado the back and set it flush with the sides. Others cut the bottom less than the sides and let the back set in past the sides. Some router a double round-over on the sides and back and some don't. Some router the round-over after construction and some before. Others don't router the sides at all. Some router a half round-over. Box joints....full dovetails....blind dovetails......front side attached to the drawer front or no box front attached to the drawer front.....glue the bottom or don't glue the bottom.....mitre the pieces or butt joint....routered fronts to accept the sides, or rabbet the front to accept the sides and bottom.......Man, it goes on and on. Maybe FHB ought to do a thing on the varity of drawer construction......maybe they already have. This should be a thread of it's own.Ed.
*thanks
*Cheeky bugger Blodgett. Take a squint at those 'plain old box joints' and tell me how you set the saw to cut 'em! Sliante.
*Jim, Here's a typical traditional drawer layout. It's only one of many. Sorry about the metric. I can't handle Imperial worth a spit, but yes, the back is usually about 4-8 mm less in height than the sides. Sliante.
*i Oeuvre? Sorry about the limp wristed, effete phraseology Mr. Pita. It's just a poncy word for 'artists work.' I guess I spend too much time hanging about around the corner in the tea drinkers paradise that is Knots. Sliante.
*Ed, Fine Woodworking has done a gazillion articles on drawer making. About every third issue it seems like they do another one. I stopped reading them- drawer making articles that is, about fifteen or twenty years ago. I'd be surprised if Fine Homebuilding hasn't tackled it in some way, but I don't read that magazine to know one way or the other. Sliante.
*Sorry Jim, I forgot to mention that the back is set lower in traditional drawer work so that air has an escape route over the top of the back, and out towards the front. One sign of a well fitted nest of drawers is said to be that one or two of the other drawers pop out when you close another one quickly. This sign is not worth looking for in drawers mounted on slides. Plenty of space for air to escape to in this situation, but that doesn't mean the drawers are badly made or fitted of course. Sliante.
*That's pretty good work there. I'd like to be able to do that but I can't hold the paint brush that steady. That's what you meant by cutting in the joints, right?
*I meant that I like to use box joints for drawers. Even though they are plain, as opposed to the elegant joints you posted. That's some mighty fine woodworking you did there.
*I always figured that shorter back was so stuff can slide out over the short back and down into the drawer below, instead of get bound up inside the drawer, causing a person to try to force the drawer open and break something in the process. I'm no student of furniture, but I first noticed this detail in reproduction "antique" drawers several years ago, and it took me quite awhile to reason through it. So Sgian, are you saying it's to allow the air to escpe in real fine fitted drawers? That would stand to reason, too. I try to remember to build all my drawers that way, just to kind of honor the old ways, as kind of a tip of the cap to cabinet makers gone.
*Jim, allowing the air to escape is rather academic when the drawers are loaded if you think about it of course, but in an exhibition piece it's kind of nice to show a potential client a couple of bottom drawers popping out as you slam home a top drawer. It gives them the idea that your work is accurate and that they must be viewing quality. Drawers as snug fitting as pistons in an engine and all that nonsense. Personally, I think the most useful technical trick of drawer making is designing a means that allows the bottom to be slipped in last from the back. If you have another look at the sketch I put up, I think you'll see what I mean. Even in modern kitchens, I still think this is neat for it allows for repairs down the road. Typically nowadays (in kitchen cabinets, for e.g.) the bottom is trapped in during assembly of the box, and a show wood front planted on. There is nothing wrong with this approach, and a new drawer box can be made simply enough if need be. But it's still nice to be able to remove the bottom and replace it if required, or do some repair work to a damaged drawer. Accidents do happen. Naturally this adds a little to the cost, and many punters shop price only. They want it to look like a million dollars on the outside, but couldn't care less about how it's made. It's what I call the "all fur coat and no knickers," or "two cars on the drive, and nothing in the fridge" syndrome.I knew you were refering to drawer making when you invoked finger joints in your earlier post by the way. I was just jerking your chain a little. No offence was intended, and I'm sure none was taken. Have a good one. Sliante.
*The other reason to have a shorter back on drawers in furniture) is to accomdate the drawer stops that are usually on the rail above: the back slides under the stops, but the back of the drawer front comes to rest on them.
*Aye, Jimmy,'At's fyn work.
*Wood drawers? Sounds mighty uncomfortable to me. I prefer cotton briefs myself.