I’ve been asked to bid a siding job that is a little different than any we’ve run into before.
It’s a large commercial project that involves applying Smartside engineered wood siding over a gypsum sheathed, 14 ga. steel stud wall system. It must be screwed with a self-drilling screw. The screws will be hidden as the 6″ siding is blind fastened at the top edge. Has anyone out there had any experience with this? It’s a huge project, about 950 squares of siding coverage, at prevailing rate. I’m not sure how much more time consuming this will be than normal installation. By the way, it’s also 3 story walls, so that will slow things down a little too.
I’m also curious as to what people may be charging for 6″ clapboard siding in other areas of the country. I’m in NY. prices here run $150- 250 a square labor.
Discussion Forum
Discussion Forum
Up Next
Video Shorts
Featured Story
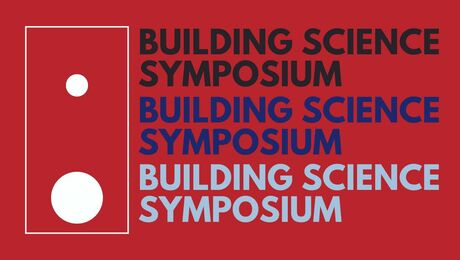
Fine Homebuilding is excited to be the official media partner of the 2024 Building Science Symposium series! This event offers builders, tradesmen, architects, designers and suppliers to discuss topics ranging…
Featured Video
How to Install Exterior Window TrimHighlights
"I have learned so much thanks to the searchable articles on the FHB website. I can confidently say that I expect to be a life-long subscriber." - M.K.
Replies
What keeps the siding from curling up if it is fastened at the top. Can't you nail with ss ring shank at bottom thru the sheathing ?
arrow,The siding they are using is a composite clapboard that the manufacturer recomends fastening blind at top. I have used this siding before on conventional wood frame homes and not had any curl problems. As for nailing, there is no wood sheathing. This project is sheathed with a gypsum board exterior sheathing, with Tyvek over that. Our contract would not include the sheathing or tyvek. That is being done by the steel framers as part of their contract.
If you can find a low profile panhead screw with with the wings and drill point tip, that should work.
We tried a mockup today using a 16 ga. stud 5/8 gypsum and composite siding over that. The wafer head screws my supplier gave us were a # 10 without wings and a larger size #12 with wings. The # 10 screw worked faster and seemed to suck in flush but still took about 8-10 seconds apiece. The larger screw worked also but because it was drilling a bigger hole took another 3-4 seconds. This was using a cordless drill on the high speed. I don't want to have to use a corded drill or driver 30' up on scaffolding. I'm wondering how these new cordless impact drivers would work? No matter how you look at it, the siding is going to go on much slower. I don't know if a cordless drywall gun would work better or not. Time is money, in this case even more so, as this is a prevailing rate job.
I am assuming you are bidding this.
14 gauge studs with gypsum sheathing
yikes, sounds like a nightmare. self drilling screws are a real pain in anything over 20 gauge steel. are there areas where you will not be able to hit studs, such as sloping roof lines meeting siding ? if so, how are you going to fasten in these areas ? can blocking be added inside walls ? will there be an exterior membrane such as Tyvek or felt paper ?
I can't give you labor costs to use, but I would think it would be double the cost of a standard nail job.
I would get some material and do a small test wall if I were pricing for 950 square.
carpenter in transition
I'v never fastened siding to lightgauge structural steel but I have fastened ply wood. The problem with fastening using a regular self driller is it drills through the wood quickly and when the screw hits the steel it slows up. Most of the time before the screw can cut the metal the fiction from the screw turning in the wood causes the screw to lose its temper and the screw just fails. This means you need to predrill a drop hole in the ply which takes time and two drills or bit changes. But there is a screw called a ply-metal that has two "wings', cutters that predrill a drop hole relieving the friction thus allowing the screw to do its job. I just went through two twenty five pound boxes. They seem, at least in the hands of my helpers, to drive much better with a cordless than an electric screwgun. The slower rpm made stripping them out less likely. My metal stud supplier was able to get them fairly quickly. #10 wafer head ply-metal is what to ask for.
I think we will do a mockup before bidding. I have used the winged type screws before and you may be right. They may work best. I just picked up some samples this afternoon of different screws to experiment with. As for blocking, I did advise the GC that there will need to be blocking in a few areas, but the framing goes to wood at the roof lines so there will be normal nailing up the gables, and at soffit/fascia areas.