Electric House Made With Cross-Laminated Timber
Integrating cross-laminated timber, wood-fiber insulation, panelized construction, and a solar-tile roof for Passive-House performance.
Wedged between a public road and private lakeshore in rural Connecticut, this all-electric house is proof of concept for the team behind Maine-based OPAL Architecture. It was the firm’s first time combining cross-laminated timber (CLT) structural sheathing with wood-fiberboard insulation and a Tesla solar-tile roof. Integrating those products and systems was a tall and rare order that company founder Matthew O’Malia and his team were excited to fill.
The current buildings replaced a heavily modified 1500-sq.-ft. seasonal cottage in poor condition. To satisfy shoreline restrictions on redevelopment, OPAL designed the new house to fit within the existing nonconforming structure’s foundation as well as the previous volume. The resulting combination of building forms, in addition to the client’s objectives of Passive House–level performance and lowest-possible carbon output, helped inform the materials and methods used.
CLT meets wood fiber
Prefabrication has always been part of OPAL’s model. On this project, the team spec’d CLT wall and roof panels for the material’s dimensional stability, structural capacity, and carbon-storing properties; it also lends itself nicely to factory cutting. The CLT shell is encased with exterior wood-fiber insulation, ultimately reaching an airtightness rating of .78 ACH50, close to Passive House performance.
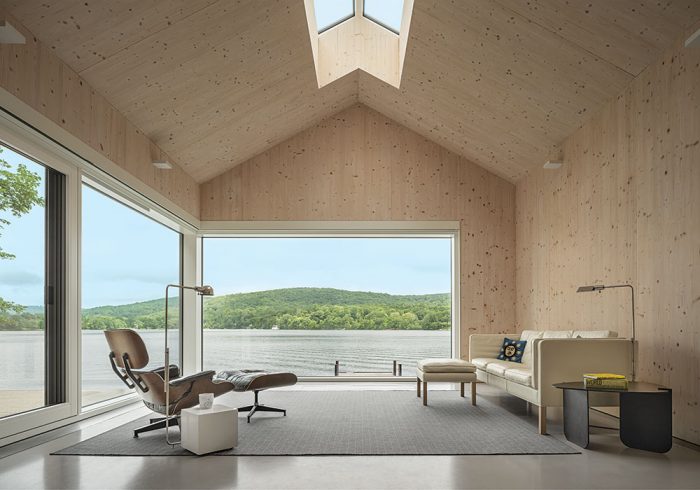
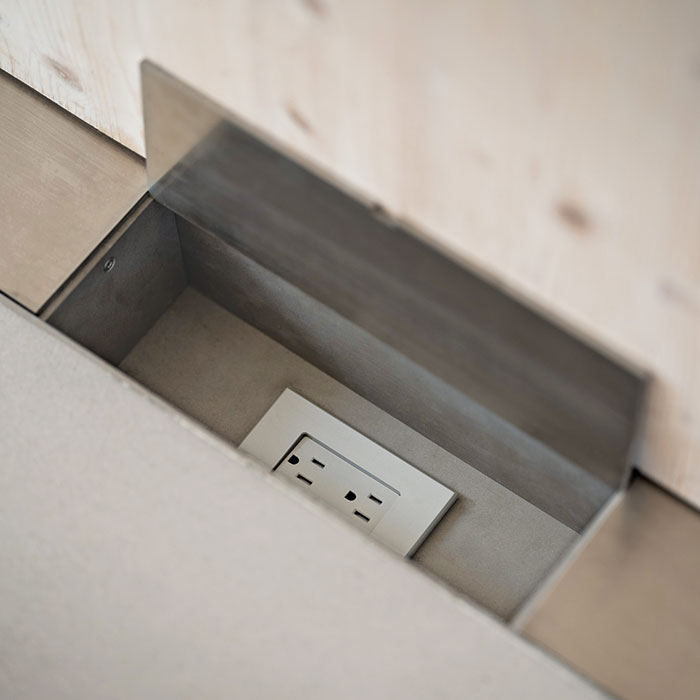
According to O’Malia, once the team settled on CLT construction, which meant the interiors would have exposed structure, they had to think carefully about the rest of the envelope, which needed a dimensionally stable, vapor permeable exterior insulation to allow the assembly to dry. Wood fiberboard made sense—plus, it’s another carbon storing product.
Combining the two materials resulted in an aha moment for the team. As O’Malia explains, the CLT was super-exact; its specifications came from computer modeling software that resulted in millimeter-perfect panels—but when it came to the insulation, old-fashioned hand labor was needed and took a long time. The team realized that in the future they could use the same technology to cut the wood fiberboard, and that on upcoming projects they should automate the structural and envelope systems together. With this approach, anything cut in the factory that won’t be used in production can be ground up and made into insulation products for a zero-waste operation.
With strict attention to air-sealing, panelized CLT structures can result in about one-third the typical amount of heating or cooling energy associated with a conventional build. This translates to better thermal comfort and lower utility bills. CLT keeps its structural strength at high temperatures too. It can be heated to 518°F before it begins to char, at which point the exterior charring acts as a protective layer for the structure to keep burning in isolation. This is similar to the process of shou sugi ban, a traditional Japanese method of burning wood siding to create a fire-retardant, rot-resistant surface board. (At similar temperatures, concrete can spall and crack, and steel loses its strength.)
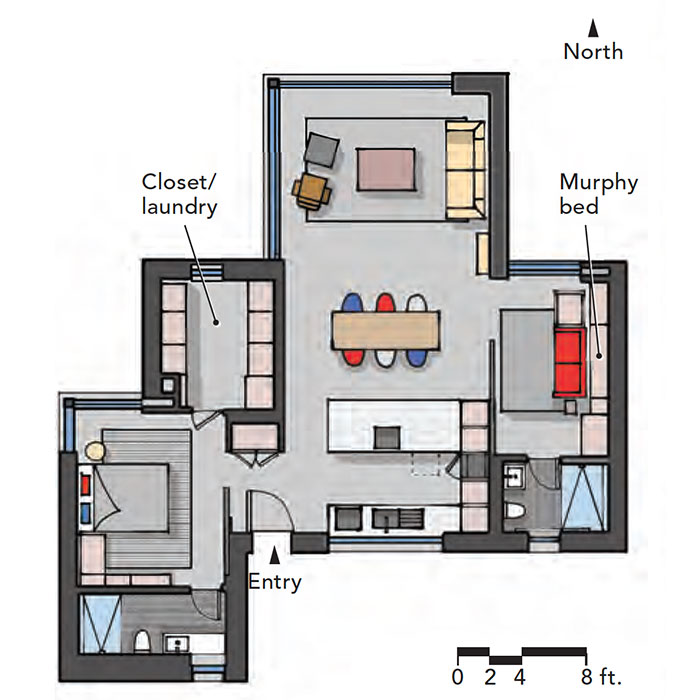
Streamlined for space
The single-level plan concentrates the kitchen, dining, and living volumes in the main part of the house. The master suite occupies the west portion of the building, and a study/guest room with a second bath is in the east section. The layout ensures privacy in the sleeping quarters, and every major space includes a lake view.
Specs
Bedrooms: 2
Bathrooms: 1-1 ⁄ 2
Size: Main house, 1299 sq. ft.; boat house, 108 sq. ft.; garage, 328 sq. ft.
Completed: 2021
Location: Connecticut
Architect: OPAL Architecture
Builder: Country Home Construction
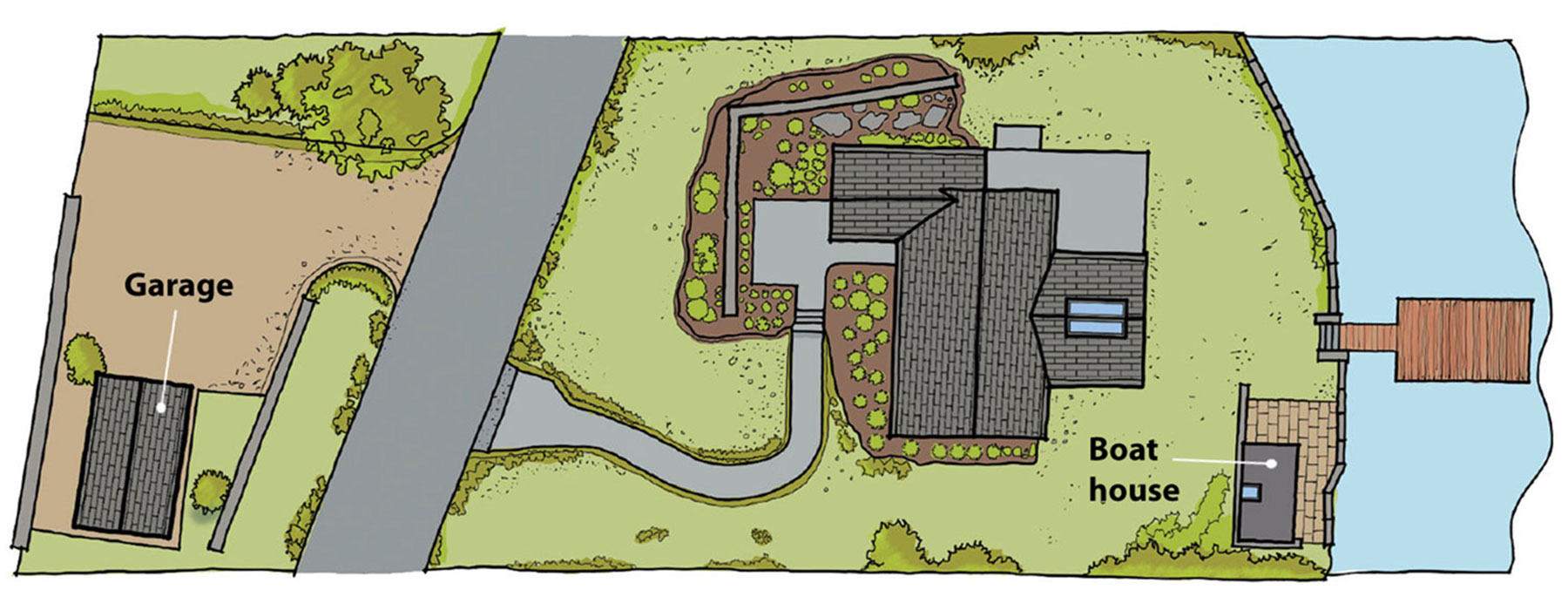
Integrated solar-tile roof
The client’s goal of net-zero energy performance meant minimizing operational loads with a tight shell and producing energy on-site. Maximum solar production was critical, but the small, complicated house shape did not allow for more than a five-panel conventional PV array on the roughly 1300-sq.-ft. roof, which would have fallen short of what was needed.
At the same time, Tesla happened to come out with its integrated solar-tile system. (This was the third house in greater New England to install it.) The system covers all roof surfaces; it includes active, energy-producing panels and dummy or “blank” panels that can be cut to fit valleys or the end of a run. The small module volume allows for optimization of active panels. The dummies make up about 10% of the total roof; they fill in around the active panels for a cohesive look.
Industrial-strength hook-and-loop fasteners secure the panels to a rack system with a drainage plane underneath. According to O’Malia, they will generate almost four times the output of a conventional array on this house due to solar gain from all roof surfaces versus that from a south-facing roof only, which would not have worked with this house’s orientation.
The downsides to the Tesla tile roof are high cost and labor-intensive installation. It takes days to daisy chain all the individual panels. (Tesla has since increased the size of the modules to help expedite installation.) It’s worth considering, too, whether smaller components and more of them create greater risk of failure than conventional panels.
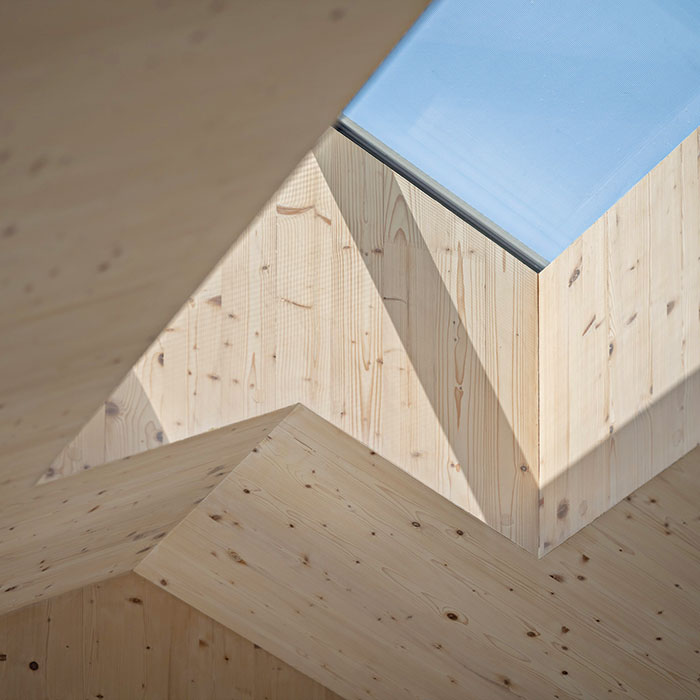
Asked if he would spec the Tesla system again, O’Malia said, “Yes. As an architect, I value the good look of this next-generation solar roof.”
Planning for resiliency against power outages is important. For this project, the team had planned on a backup generator, but the site prohibited installing one in a location that met zoning regulations for its decibel rating. Plan B was a battery system, so four Tesla Powerwalls were installed in the garage.
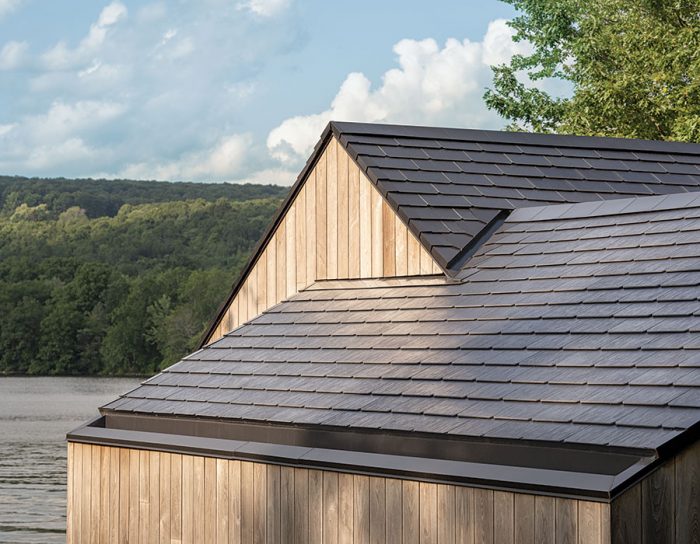
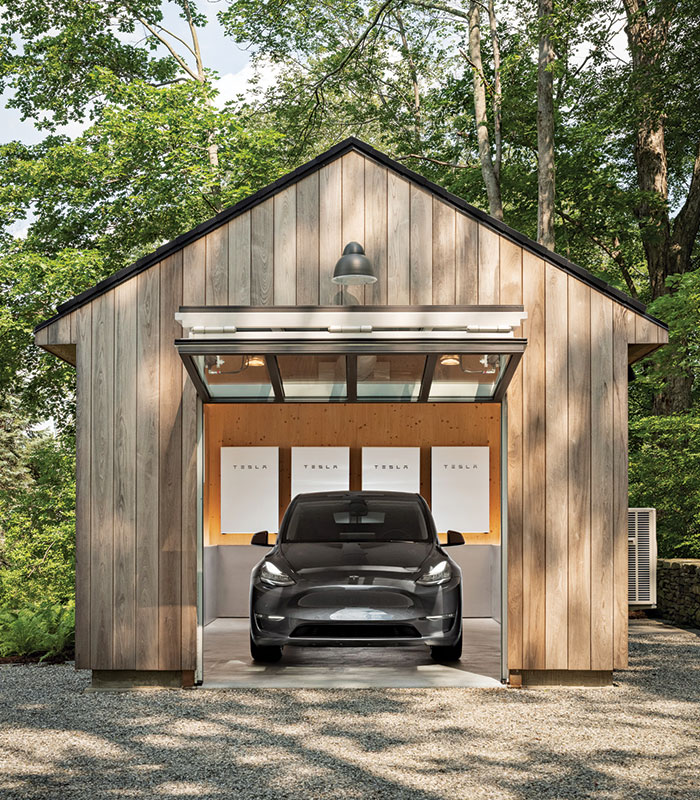
The case for cross-laminated timber
Among CLT’s touted benefits is how it streamlines the framing process. The solid-lumber panels are custom-built to meet specifications and then craned into place on-site. The CLT installer on this project was structural engineer Daniel Wirth, an Austrian native with a long career in mass-timber framing. He is proficient in the European technology and brings to the table best practices for handling and manipulating the panels. Wirth lauds the ease with which the product goes together—in as short a time as a day and a half. He admits that this house, with its small rooms and unique geometry, was a little more complicated. It took four days to complete. Nonetheless, he is 100% sold on the product and process. “In Europe, we have been working with CLT for almost 20 years,” he says. “Right now, CLT residential construction in the U.S. is not as efficient as it should be.”
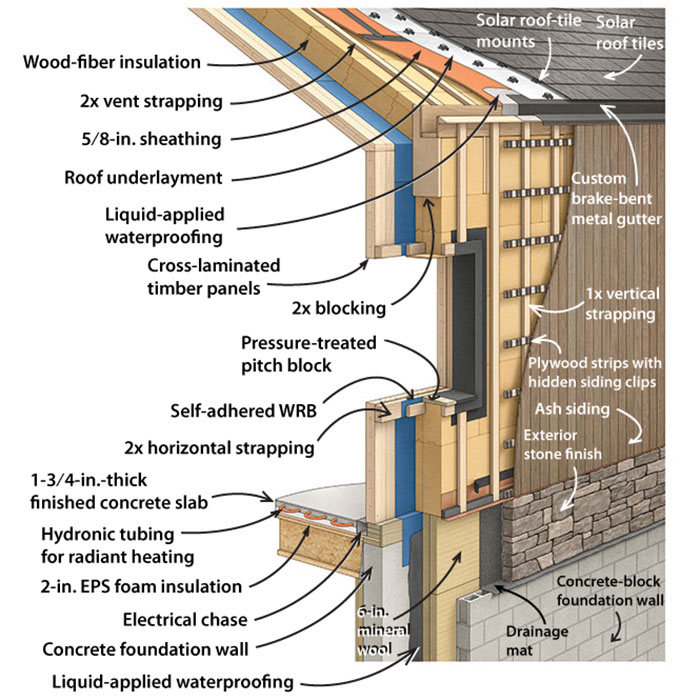
On the affordability front, Wirth recognizes how difficult it is to work CLT into the budget of a straightforward 2×4 or 2×6 build, but he advocates for its value-engineering. “I hope when people have the idea to build with CLT, they contact people who know what they are doing to get the most out of the material,” he says, noting that roughly 30% of Europe’s timber buildings—including residential homes—are made with CLT.
HVAC in a low-load house
Typically, O’Malia’s team stays away from radiant heat in slabs because it is rarely needed in a Passive House. They are so well insulated and air-sealed that the primary heating and cooling system is sufficient; the low energy demands make it hard to justify adding a secondary heat source. However, in this case, the radiant floor is the primary heat source, and a ducted heating and cooling system provides AC and any required supplemental heat. The design thinking was that the house doesn’t have the benefit of passive solar gains due to its orientation, which makes hydronic tubing in the slab a good option for base-level heating. (Hydronic radiant heating is not the best idea for homes with passive solar strategies, because the already-warm slab won’t absorb additional heat.)
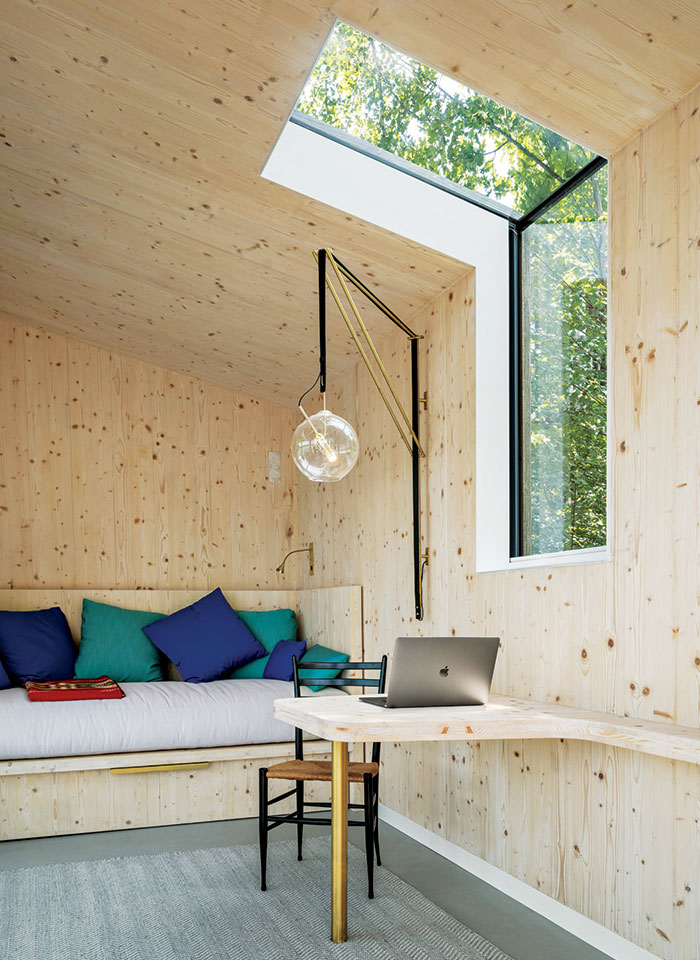
An air-to-water heat pump heats water for the hydronic system in the slab, as well as for the domestic water; it also powers the forced-air cooling system. A Zender ERV handles ventilation. Of this, O’Malia says, “If you are going to do a mini, tight building, it is critical to put a ventilation system in— it is irresponsible not to.” He likes the term “architectural malpractice,” as poor indoor-air quality is dangerous to human health.
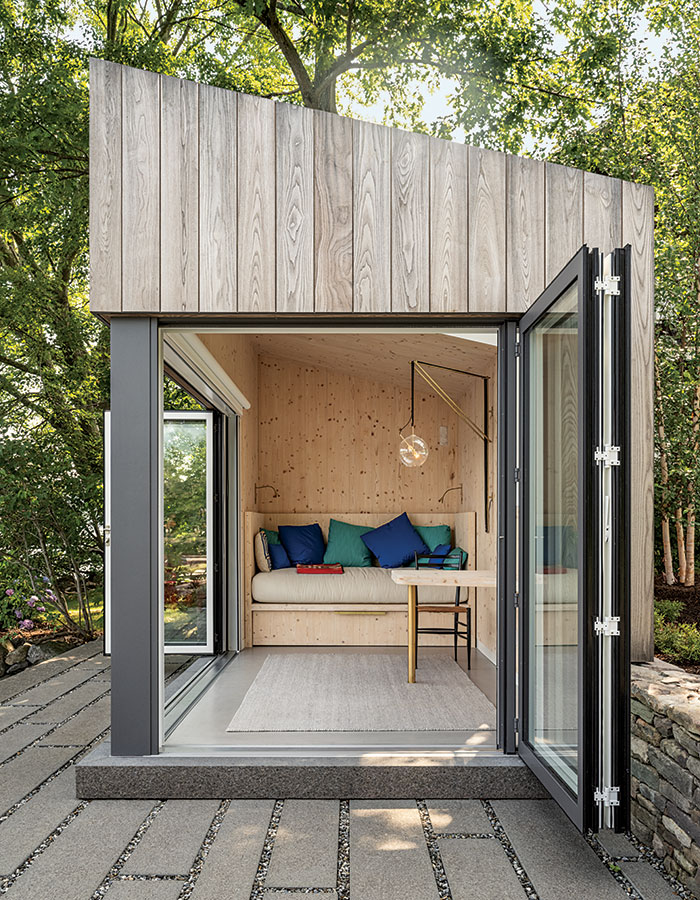
Building sensibly and sustainably
Of course, the homeowners did not need to use such cutting-edge systems and technologies to build a sustainable home. They had options for its execution but chose to invest in a supertight envelope made with innovative materials and technologies. They admire what they call a “European sensibility,” whereby houses are built with a level of care and attention that ensures they will last and remain within a family for generations. They also view the European approach as one that includes a deeper awareness of and appreciation for a climate-driven demand for efficiency.
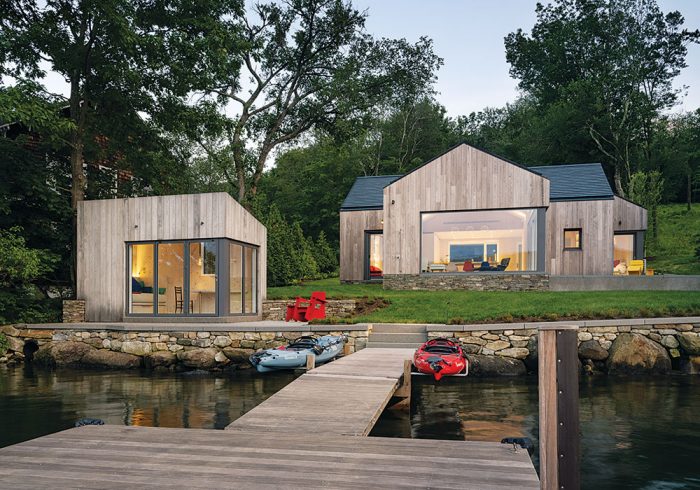
That sentiment drove many of the homeowners’ decisions—including the use of CLT, which they had not heard of previously. “For a little project like ours, these things don’t necessarily matter,” says one of the homeowners, “but symbolically it was important to us to do as much as possible. None of this stuff is perfect, but CLT as a technology, wood fiber as an insulation product, and the ability to do prefabrication— I think if homeowners were to learn about these things, they’d be excited about them. They just aren’t widely available yet.”
The homeowners and O’Malia see this house as a prototype for how to do things in a way that will advance sustainability for multiple generations, while freely admitting the costs and headaches that come with it.
“We ran into every possible obstacle,” says the owner, recalling issues with the town and utility company. He attributes many of the hurdles to the fact that most agencies are unfamiliar with these products and practices. However, he concludes: “There’s a lot to be learned from technologies that are better for the environment.”
—Kiley Jacques is senior editor at Green Building Advisor.
Photos by Trent Bell.
From Fine Homebuilding #315
RELATED STORIES
View Comments
Price per sf please….or % increase over a well insulated tight (ach 1.0) stick framed house ….whether one is green, hi-tech, or just a patron of good architecture, etc any building without acknowledging costs , while entertaining, and interesting, is a quixotic and not especially helpful exercise. There are clients and owners at all price points of costs, but what IS the price range of this house? is this a $1,000 psf house, or a $500 psf house for example. Readers want -and need-to know…
The glazing alone probably cost more than my entire house. Clearly the clients are very well off, and I appreciate that they spent their money intentionally to reduce their carbon footprint.