Foam-Free Insulated Foundations
If you want to avoid foam insulation, you can use semi-rigid mineral wool—or you can build your house on piers.
By now, most builders know that in all but the warmest climates, foundations need to be insulated. Whether your house has a basement foundation, a crawlspace foundation, or a slab on grade, foundation insulation is usually a good idea (and is often code-required). Insulating a basement, crawlspace, or slab-on-grade foundation usually requires either rigid foam insulation or spray foam insulation.
But some green builders want to build a foam-free house. (For more on this topic, see “Building a Foam-Free House.”) The cited reasons for avoiding foam insulation vary. Some green builders worry that some foams may be toxic; others don’t like to use any materials derived from fossil fuels.
In this article, I’m not going to debate the merits of these concerns; rather, I’m going to focus on all of the different ways to build a house with a foam-free foundation.
Can your foundation be uninsulated?
In most U.S. climates, building codes require foundations to be insulated. In the 2018 IRC, foundation insulation requirements can be found in Section N1102.1.2 (R402.1.2).
If you are building a house in Florida, or a state with a similar climate, you may be able to build your house on an uninsulated slab. That said, in most climates, slab-on-grade foundations need, at a minimum, some vertical insulation at the slab perimeter.
For more information on ways to insulate a slab-on-grade foundation, see “Determining Sub-Slab Rigid Foam Thickness.”
If your house has a basement foundation or a crawlspace foundation, insulation is usually installed on the basement walls or crawlspace walls.
Is it possible to substitute semi-rigid mineral wool for rigid foam?
Green builders who want to avoid the use of rigid foam or spray foam insulation may be able to substitute semi-rigid mineral wool for rigid foam. This approach works in the following locations:
- On the exterior side of a basement wall.
- On the exterior side of a crawlspace wall.
- At the perimeter of a slab on grade, installed vertically.
- In some situations, under a slab on grade, installed horizontally.
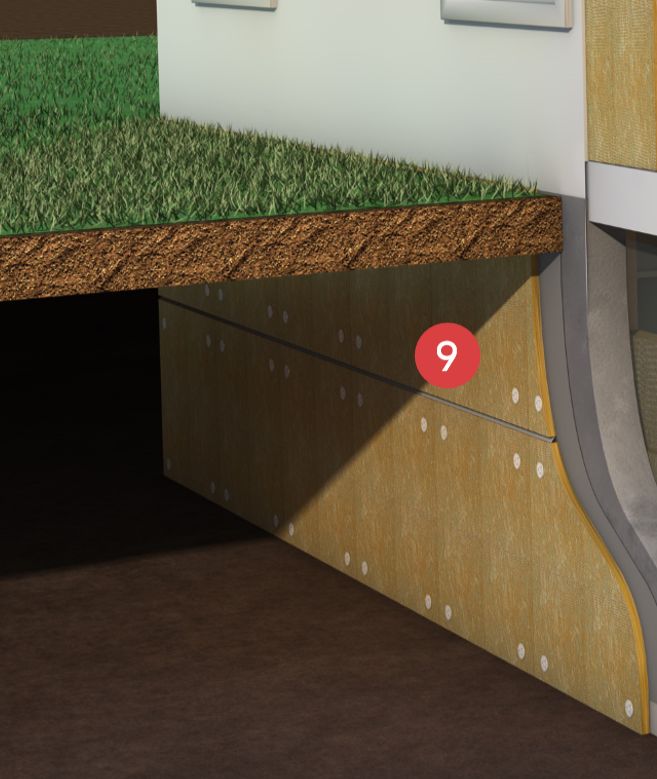
For more information on using semi-rigid mineral wool under in these locations, see:
Note that mineral wool insulation is air-permeable, so it can’t be substituted for rigid foam on the interior side of a basement or crawlspace wall.
Pier foundations
For builders who aren’t comfortable installing mineral wool on the exterior side of a concrete foundation, there’s another approach that works for a foam-free house: Switch to a pier foundation. If you build a house on piers, you can build an insulated wood-framed floor with deep floor joists and fill the joist bays with dense-packed cellulose, blown-in fiberglass, or some type of batt insulation. For a thorough discussion of different ways to insulate this type of floor, see “Insulating a Wood-Framed Floor Assembly.”
Note that we aren’t talking about a crawlspace foundation. If you’re building a crawlspace, the best location for crawlspace insulation is on the crawlspace walls, not in the floor joists above the crawlspace. To learn why, see “Building an Unvented Crawlspace.”
The main difference between a house on piers and a house with a crawlspace is that with a house on piers, the wind is able to blow under the floor assembly. A crawlspace foundation should exclude the wind. For more information on this distinction, see “Crawl Spaces vs. Skirts.”
If you decide to build a house with a pier foundation, there are a few important points to keep in mind:
- You’ll need to specify floor joists that are deep enough to hold the insulation thickness required for your R-value goal. In many cases, engineered floor trusses or I-joists are good choices to provide the needed depth.
- You’ll need a durable soffit material (usually plywood or OSB) on the underside of the floor joists to keep raccoons and squirrels out of your floor insulation.
- You’ll need to install this soffit material in an airtight manner; the easiest way to do this is to seal the seams with a high-quality tape like Siga Wigluv or 3M All Weather Flashing tape.
- You’ll need adequate access under the floor framing to install the soffit material and tape the seams; in most cases, this means that the floor joists should be at least 30 inches above grade. If you want the floor joists to be closer to grade, you may have to get creative; for more information on one alternative approach, see “Air Sealed and On Piers.”
- If you live in a cold climate, you’ll need to come up with a way to prevent your water supply pipes and drain pipes from freezing. The typical solution is to build an insulated chase around the vertical pipes and protect the pipes with electrical heat tape.
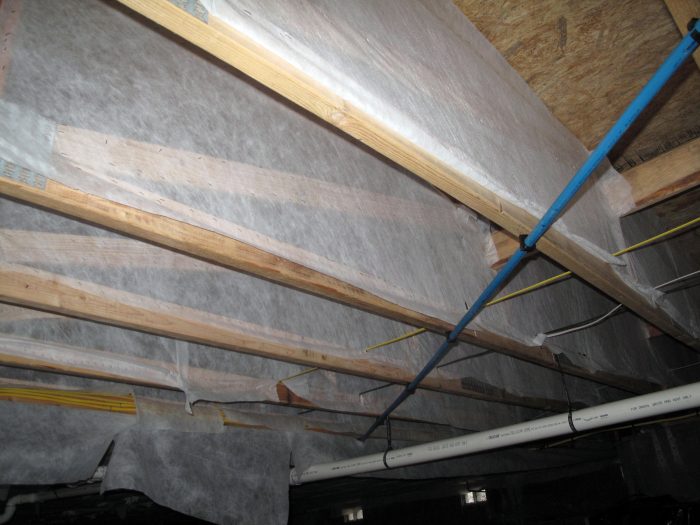
Helical piers
In any conversation about foam-free homes with pier foundations, the discussion eventually turns to the pluses and minuses of using helical piers instead of pressure-treated piers.
Helical piers are corkscrew-shaped piers of galvanized steel that are screwed into the soil with special equipment. Helical piers can be installed quickly, with minimal site disruption. When labor costs are included, helical piers often cost less than pressure-treated piers.
Although there is no need to excavate any holes for the helical piers, some excavation is still required, since most houses need a utility trench for plumbing pipes or electrical cables.
I recently spoke with Dan Kolbert, a Maine builder, about his experiences using helical piers. “We’ve used helical piers for one new house and one addition, and we were quite pleased with both projects,” Kolbert told me. “You need to get some engineering done for the piers. One advantage is speed: They can show up at eight in the morning and you are framing by 10. The cost is for helical piers is dirt cheap compared to hiring someone to dig holes. We paid between $350 and $400 per pier.”
The Ecocor approach
Ecocor is a Maine construction company specializing in high-performance homes and Passivhaus buildings. Ecocor touts its version of the foam-free foundation on the company’s web site under a heading that reads “Foam-Free Framed Floors.” The web page notes, “For projects where treading lightly on the land is a key concern, eliminating plastic foam is a goal, or access to the site is compromised, we offer a pier foundation system. Using helical piers—galvanized metal posts with an auger screw at the bottom, literally drilled into the ground—we minimize disturbance of the site. The floor is framed with deep I-joists and filled with dense-packed cellulose, with an airtight, moisture-repelling skin applied to the bottom of the floor system. We use a small, insulated chase to bring utilities into a central location. … Our foam-free framed floor system uses 16″- 24″ I-joists filled with dense-packed cellulose.”
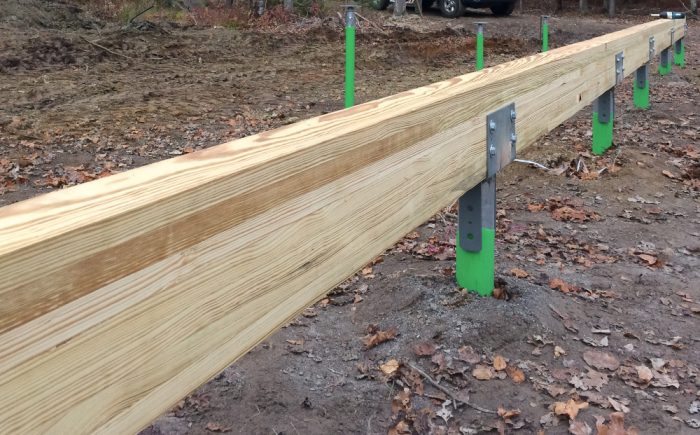
I called up Chris Corson, Ecocor’s technical director, and asked him about the cost of helical pier foundations. “The piers are about 250 bucks a pop,” he told me. I asked if this type of foundation was cheaper than other approaches. He answered, “These projects were trying to achieve Passive House. We used 24 inches of dense-packed cellulose with deep I-joists. The R-value was pretty high, and because of that the cost was probably about the same as a frost-protected shallow foundation.”
When I asked about the advantages of the helical pier approach, he said, “Speed and ease of installation. One nice thing is that we were able to set up a laser and then cut off all of the helical piers so they were perfectly level.”
I asked whether he was worried about freezing pipes. He said, “We built a superinsulated service cavity, but I still insisted on installing electrical heat tape.”
Originally published on GBA.com.
Fine Homebuilding Recommended Products
Fine Homebuilding receives a commission for items purchased through links on this site, including Amazon Associates and other affiliate advertising programs.
Loctite Foamboard Adhesive
Respirator Mask
Foam Gun