Which Rigid Insulation Should I Choose?
Get the details right when installing foam, mineral wool, or other rigid insulation types, and a small increase in wall thickness can make a big difference in energy efficiency.
Rigid-foam insulation packs a lot of R-value into a relatively thin package. It is often used as a layer of continuous insulation on exterior walls and in the roof. Used in this way, the foam lowers the loss of energy through framing members, a phenomenon called thermal bridging, and increases the overall R-value of the roof or wall assembly. Some types of foam also can be used under basement slabs and on slab perimeters to lower heat loss through the concrete, which is a very poor insulating material. In choosing which type of foam to use, consider its location, R-value, and other performance attributes. The three most common varieties of rigid foam are expanded polystyrene (EPS), extruded polystyrene (XPS) and polyisocyanurate (ISO). An Irish manufacturer offers a fourth and more recently developed type, phenolic foam.
Foam isn’t the only way to build a super-insulated home
If you’re still in the planning stage of your project, be aware that exterior foam insulation isn’t the only way to build an energy efficient home. Take a look at the article Six Proven Ways to Build Energy-Smart Walls if you want to explore your options. Also, remember there are other options for continuous exterior insulation, including mineral wool and fiberboard insulation, neither one of which is comprised of petrochemicals.
Three rigid-foam choices
Expanded polystyrene (EPS)
EPS is the insulation used most widely in insulated concrete forms and structural insulated panels (SIPs). EPS has the lowest average R-value of the three most common types of rigid-foam insulation, around R-4 per inch. It also is the least expensive. EPS is suitable for ground contact and can be treated to resist insects. If you plan on placing it in contact with the ground, make sure it’s rated for that use. Some builders avoid using any type of foam on foundation exteriors because of the risk that tunneling insects like carpenter ants and termites will bore through it or nest in it. Check with your local building office first. When applied as sheathing, EPS should be used over housewrap. Most EPS is unfaced, which means it is fragile. It’s also considered semipermeable to water vapor, so it does not create a vapor barrier.
Extruded polystyrene (XPS)
Easily recognized by its blue, green, or pink color, XPS falls in the middle of the three types of rigid-foam insulation in both cost and R-value (about R-5 per inch). XPS comes unfaced or with a number of different plastic facings. Unfaced 1-in.-thick XPS has a perm rating of around 1, making it semipermeable. Thicker, faced XPS is stronger and can have a lower perm rating, but it is still considered a vapor retarder, not a vapor barrier.
If you are concerned about the environmental impact of the building materials that you use, remember that the blowing agent used to make XPS has a very high global warming potential. For this reason, many green builders avoid using it. Thermal drift, the gradual lowering of R-value over time, is a consideration with both XPS and Polyisocyanurate.
Polyisocyanurate (ISO)
ISO panels are the most expensive of the three and has the highest nominal R-value, R-5.7 to R-6. Its blowing agent is pentane, which has a very low global warming potential. Because ISO starts as liquid foam and has to be sprayed against a substrate to form a rigid panel, all ISO panels are faced. Foil-faced ISO panels are considered vapor impermeable. Because applying these products as sheathing creates an exterior vapor barrier, they never should be used with an interior vapor barrier. More permeable ISO panels are faced with fiberglass and can be used without creating a vapor barrier.
Although the nominal R-value of polyiso is the highest of the three major types of rigid foam, its cold weather performance is lower: As the temperature drops, so does the R-value. Some builders working in cold climates give it an R-value of 4.5 or 5 per inch. Polyiso is not rated for ground contact.
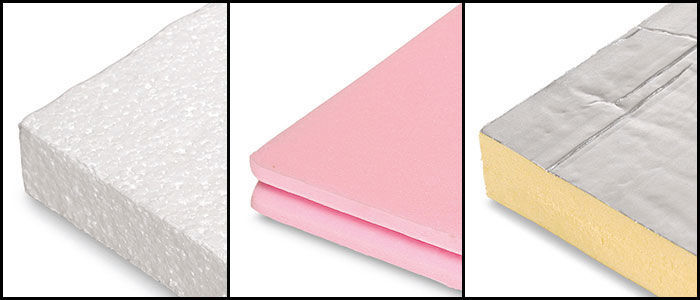
Read the complete article: Save Energy with Rigid-Foam Insulation
More about rigid-foam insulation choices and construction details:
Get the Right Rigid Foam – Foam-board insulation can boost R-value, slow thermal bridging, and control condensation—but you better choose the right type.
Is Your Exterior Rigid Foam Too Thin? – Whether it’s to meet code or to adhere to a “green” target, more and more builders are adding a layer of rigid foam insulation on the outside of homes. The idea makes sense, if it’s done correctly. Learn if you’re applying exterior rigid foam correctly.
Detailing Walls With Rigid Foam – Builder Steve DeMetrick shares construction and design details for efficient and trouble-free installation of exterior foam sheathing. His method employs Zip System sheathing for structure and air-sealing, 2-in. foil-faced foam for exterior insulation, and a felt-paper weather-resistive barrier behind a rain screen.
Choosing the Right Thickness of Exterior Foam – Rigid foam must be thick enough to prevent condensation on the roof sheathing.
Insulate Your Basement, Part 3 – In this episode, Justin Fink explains the why and how of using foam insulation on masonry walls, and demonstrates how to properly insulate the rim joist area with rigid foam and batt insulation in your basement.
View Comments
I'm finishing up a 1200 sq/ft addition and energy efficency was at the top of the list. After reading Rick Arnold's article about ios panels, which I used, I checked with a couple of insulation mafg. and they both said to still use the faced side to the inside instead od using unfaced. What i wound up also using was that breathable vapor barrier that Certinteed sells. It is only 2mil thick and I don't see how it works, time will tell. according to Ricks article no faced insulation was used on the inside. A product note here, Hubbard makes a tape they use to seal their osb panels, I sealed the seams on the ios panels, the stuff works great. Better than the foil tape.
Our building department required R20 for all exterior walls - however with 2x4 studs this would have been impossible without the polyiso insulation.
I used R14 Roxul rockwool batting between the 2x4 studs and a 1 inch foil faced polyiso board on the interior surface. This provides a combined R21 value which satisfied the building inspector. All seams were taped with foil tape so the vapor barrier was intact. Interior sheathing was 1/2" G1S fir ply.
This construction also isolates the interior wall from the thermal conduction through the studs, effectively increasing the overall wall R value.
We just wrapped a new house here in Portland, OR, with 1" of unfaced xps. The obvious upside is the thermal insulation gain.
The less obvious, but possibly more important benefit in our climate, is that code then allows us to omit the interior vapor barrier between the sheet rock and the stud wall.
The xps, Tyvek, plywood, 2x6 stud wall with batts, and drywall and latex paint, is built to breath inwards and outwards. The science I read suggests that this is close to optimal construction for our marine climate.
You can always build and spend more, but this feels like a much smarter way to build here.
Rory Read
RDG Read Development
Its too late to save Royread, but for anyone else considering installation of hardboard insulation on the outside of the studs, plese read on. The purpose of the vapor barrier on the inside of the insulation is to keep water vapor from inside the living space from traveling through the sheet rock and condensing inside the insulation in the wall cavity when it gets close enough to the outside wall for the temperature to reach the dew point. Adding an inch of hardboard insulation to the outside of the studs in the Pacific NW does not provide enough insulating value to keep the temperatures inside the wall above the dew point so it is inevitable that this arrangement will cause condensation within the wall space. Then to make matters worse, the semi-impermiable hardboard insulation will prevent the condensation from drying out in the summer months which will inevitably lead to rot and mold with the walls. Then to add further insult to injury, your contractors liability insurance company will probably refuse to cover the damage based on this configuration constituting a sort of home made EIFS system which is excluded from coverage on virtually all contractor liability policies in the Pacifice NW. To make matters worse, there so far, is not a good solution to the problem of sagging fasteners which are likey to allow movement in the siding and open up gaps which can add further water intrusion into the system which will be trapped behind the hardboard product. Some insulation manufacturers have been sending their sales people around pimping this system based on a study in Alaska where they used 5" of hardboard on the outside of the studs and in an area where most of the precipitation falls in solid rather than liquid form. Anyway, for anyone who has been around for a while, this new idea of hardboard insulation on the outside of the studs is destined to be a painful redux of the EIFS debacle from the 90's where the product manufacturers once again foisted off an untested and conceptually unsound system on bulders and the public.
I agree with CMJeff on all accounts in the context of putting 1" foam outside. I would like to add to what he says.
The study in AK with REMOTE walls (insulation/vapor barrier on the outside) was based in the hypothesis that if there were nearly double the R value in the outside of the wall creating an exterior vapor barrier, the dew point would occur somewhere in the layers of foam and therefore prevent the condensing of moisture with in the first third of the wall ( the interior ). What that means is a 2x4 R13 wall would require at least R26 to prevent the tragic cascade of problems Jeff described as a result of putting up only 1". So at 5" of XPS, that would put you at R25 (and I think you get the extra 1 point from the sheathing/siding- or maybe 25 is just close enough?). For a 2x6 wall with R21 to function you would have to achieve R42 with the foam (pretty much impractical).
There have been many REMOTE walls constructed here, and I have not seen or heard of their failures when the theory has been properly applied. I wondered the same about the sag problem with the fasteners but have not heard any first or even second hand stories about that.
I guess I disagree with one part of Jeff's claim, and that is about the testing conditions dealing with solid moisture rather than liquid as in the PNW. South East Alaska has a particular problem with not only high amounts of rainfall almost year round, but also winds driving it sideways allowing it to penetrate siding on a regular basis. The REMOTE walls have been tested in this harsh environment and have been reported to perform very well.
Only time will tell if the properly constructed walls continue to function, but I guarantee the "painful redux" will be seen from the improperly applied theory.
Paul
I hope this is the right place to ask this question. I am finishing a third floor of a two and a half story house. I have 2x10 rafters. I have at my disposal four inch polyiso board with the foil facing. My plan was to rip one inch strips of wood to put on the back of the roof decking then cut the polyiso board to fit in between the rafters leaving one inch gap for ventilation as well as a 1/4 inch gap on either side to seal after installation. I was going to double up the polyiso board for a total of eight inches. Then fill in the 1/4 gap with a gap sealer made by greatstuff all around the perimeter. In the end I would have the foil facing the air gap for ventilation on the outside and I would also have foil facing the conditioned space on the inside. Any questions or concerns would be much appreciated.
Interested in learning more about the numerous applications of Expanded Polystyrene (EPS) Foams in the construction industry, check out the following link: http://aecdai.ly/8i
EPS insulation is used in the construction of buildings to insulate roofs, walls, floors or foundations. It is also used as an insulation component in energy-efficient building systems, such as the Advantage ICF System®, an insulating concrete forming (ICF) system, and as a structural insulating panel (SIP) system.
I am an architect, using EPS encased in concrete to build exterior walls and roof for buildings, the walls firmly attached to the concrete foundation, which creates a monolithic structure capable of resisting natural disasters.
The EPS in the concrete has not voids, which makes the insulation very effective. I use 14 inches EPS with has for one pound density an R value of 4, 14x4=56. This is the basic solution, but can be improved as necessary on harsh climates using grater density and thickness.
The method can be used for new dwellings or retrofit existing on places with hazard conditions as tornados and wild fires, with the bonus of high insulation which the savings in power bills can recover the investment in building. More information, free (videos, answers to questions) upon request by email: [email protected]
Good article!EPS and XPS are all produced by polystyrene, polystyrene can be applied to many products. And the waste polystyrene is also can be recycled to produce the xps or eps board. our company INTCO has several machines to recycle waste polystyrene. Here is our website: http://www.intcorecycling.com/GREENMAX-EPS-Styrofoam-Recycling-Machines.html
I have a question. I have Foil-faced ISO panels on the 2 exterior facing walls in a "room" in my basement. I want to fix up the room to look nice, though on a strict budget. I just want to know how or what I can use to cover the panels with. Not thinking sheet rock but some inexpensive paneling perhaps? Just don't know if that's okay to do over those panels.
Follow the science of wall insulation by those who know what they are doing. You will find that in the PNW 1" or 2" of exterior insulation is all you need to force the freezing point into the rigid foam. Divide your temperature difference by your Rs and plot where 32 deg. lands. Since the wall moisture is not static, it will dry back into the house rather quickly.Where you can also control it. Remember not to put the vapor barrier at the drywall. Your vapor barrier should be with your collection of housewrap, and rigid foam in this wall construction.
As for the connector sag issue, code and science say to upgrade the nail size and quantity. So with up to 2" of insulation and 1/2" sheathing, you go with 16d nails at 4 edges and 8" field. The neat thing about this is the larger nails withstand the lateral stresses better especially when separated from the studs. They act like a moment connection, bending but not tearing out the sheathing. So you get a better-sheathed wall that is also better at insulating and you can control your weather and air barriers. Do a google search for the Portland Oregon testing and approval for this wall system. Win - win.