Convert a Porch to a Mudroom
The key to this budget-friendly and comfortable entry remodel is a new airtight and insulated floor system
Last winter a longtime customer asked us to convert his existing porch into a mudroom. The enclosed porch, which was approximately 60 sq. ft., had single-pane windows, no wall or roof insulation, and a storm door in place of a proper entry door. A small staircase within the porch footprint provided access to the client’s home workshop, where he restores and refinishes furniture professionally. Given that the porch was almost always too hot or too cold, it was only used for accessing the backyard and the workshop. Our plan was to eliminate the staircase (with the client accessing his shop from outside the house in the future) and rebuild the porch into a semi-conditioned mudroom that would include a utility area for laundry as well as space for kicking off boots, hanging jackets, and storing hats and gloves.
As with most porches in the area, there was a step down from the house to the porch floor. We decided to raise the floor system so the mudroom would be on the same level as the rest of the house and feel like part of the original floor plan. Exploratory demolition by the homeowner revealed some problems with the original structure. The posts supporting the roof were not solid lumber but rather four 1x trim boards nailed together to create a hollow post. There were also load-carrying beams at the roof level with voids and spaces, particularly at the outside corner of the roof valley. Addressing these structural deficiencies would be part of the scope.
To keep costs down, we did not change the porch’s tongue-and-groove beadboard ceiling. We also left the existing clapboard siding as an interior wall finish, using salvaged pieces from other parts of the house for repairs. To control costs further, the client would finish the drywall, install a vinyl floor, and trim out the entry door and two windows himself.
Porch-to-mudroom conversions like this challenge the standard construction sequence because they’re often on a concrete slab or inaccessible crawlspace. In this case, the existing block foundation was in excellent condition, but there is no access from inside or outside the home. This meant we would need to install the electrical, insulation, and venting in the floor system before sheathing the floor and building the walls.
The new mudroom would have insulation but no heat source, so I wanted a robust insulation and air-sealing strategy to keep the space comfortable. The crawlspace under the porch floor was vented when we started construction, and we wanted to keep it that way. This meant we needed to insulate and air-seal the floor assembly. The 2×8 floor joists can only hold 7-1/4 in. of insulation, so we installed 2-in.-thick XPS rigid insulation ripped to fit between the joists, with mineral-wool batts on top. I love mineral wool for its fire resistance, sound-deadening characteristics, and R-value (R-4 per in.). The rigid foam provides an even greater R-value per inch (R-10 for 2 in.), and because it is sealed around the perimeter with canned spray foam, it creates an air barrier below the mineral wool. The floor assembly is approximately R-35.
We retained the two passive vents to allow seasonal drying in the crawlspace. We constructed those using the 2-in. XPS. The vents were covered with basic, aluminum, louvered register covers.
For the exterior walls we used Zip System R-sheathing (R-6.6), which has a layer of insulation built into it. With the addition of R-15 mineral-wool batts, our wall assembly is approximately R-21. Although this space isn’t fully conditioned with a heat source, because it is so well-insulated and air-sealed and has such a small footprint, it is generally comfortable and can be made more so by opening the door to the main house.
This project cost about $9000, not including the client’s labor, which easily saved a few thousand dollars. It’s always enjoyable to help a family make their house more livable, and it’s especially satisfying to do so for a reasonable sum of money.
Frame a New Floor
We considered leaving the porch’s floor joists in place and sistering taller joists or adding sleepers to raise the floor, but we found an untreated mudsill sitting on the block foundation with no sill-seal gasket. Even though there were no signs of rot, we chose to cut out the existing joists and sill plates and start fresh with a new floor system raised to match the rest of the house.
Support the roof
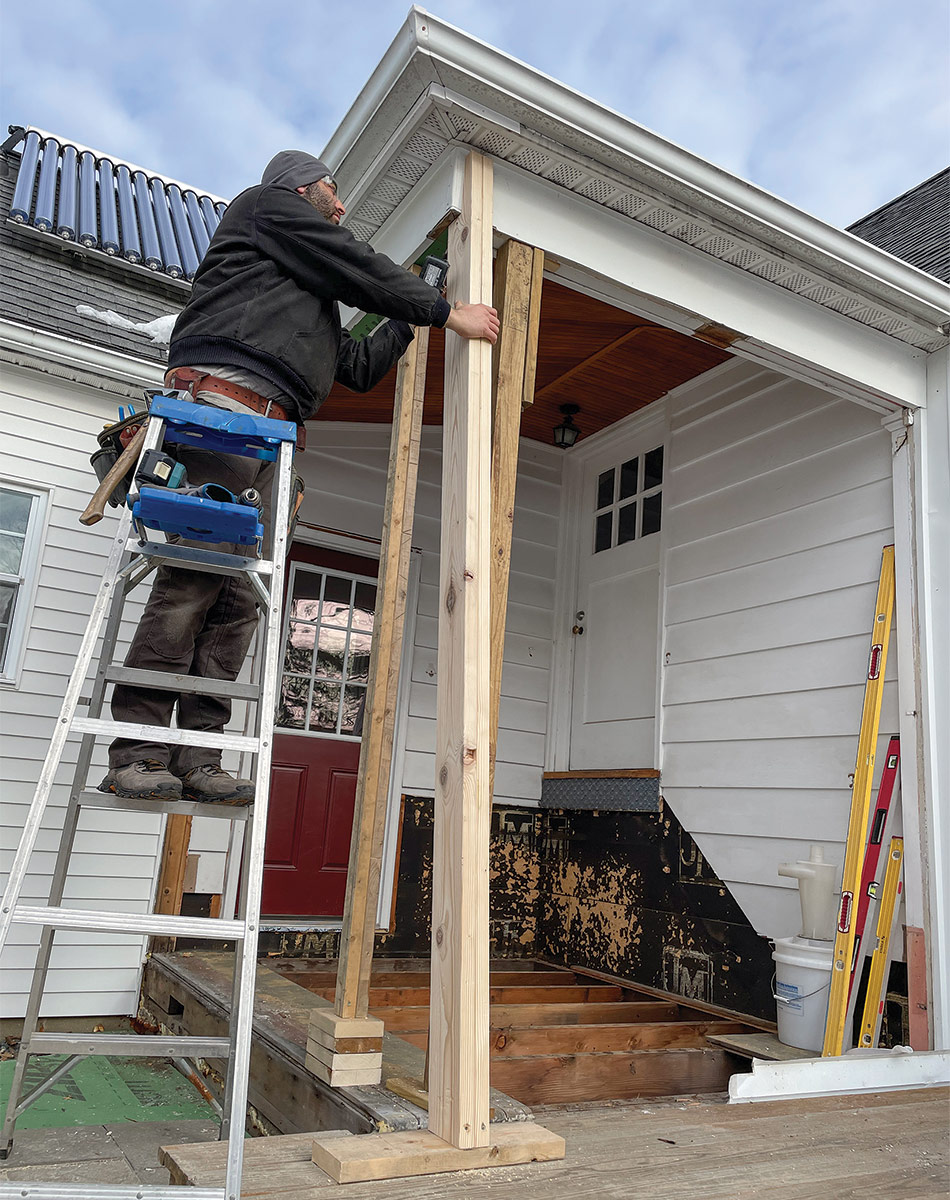
Demo the floor
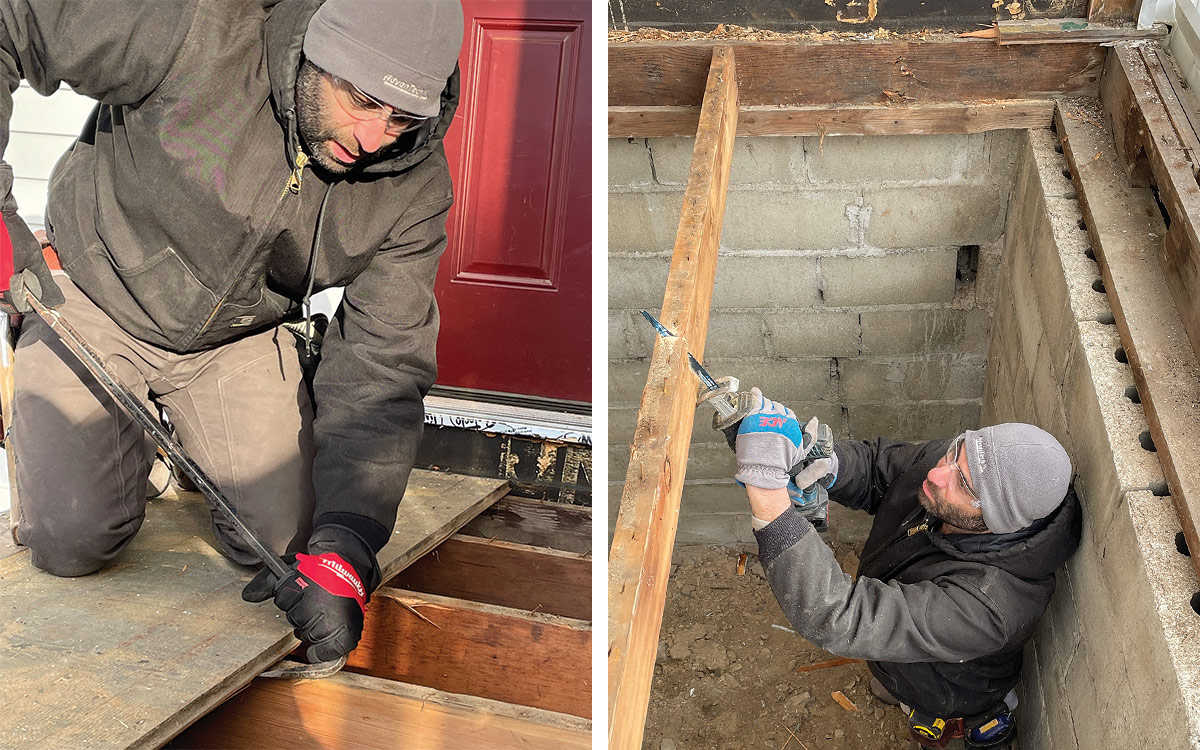
Start straight and smooth
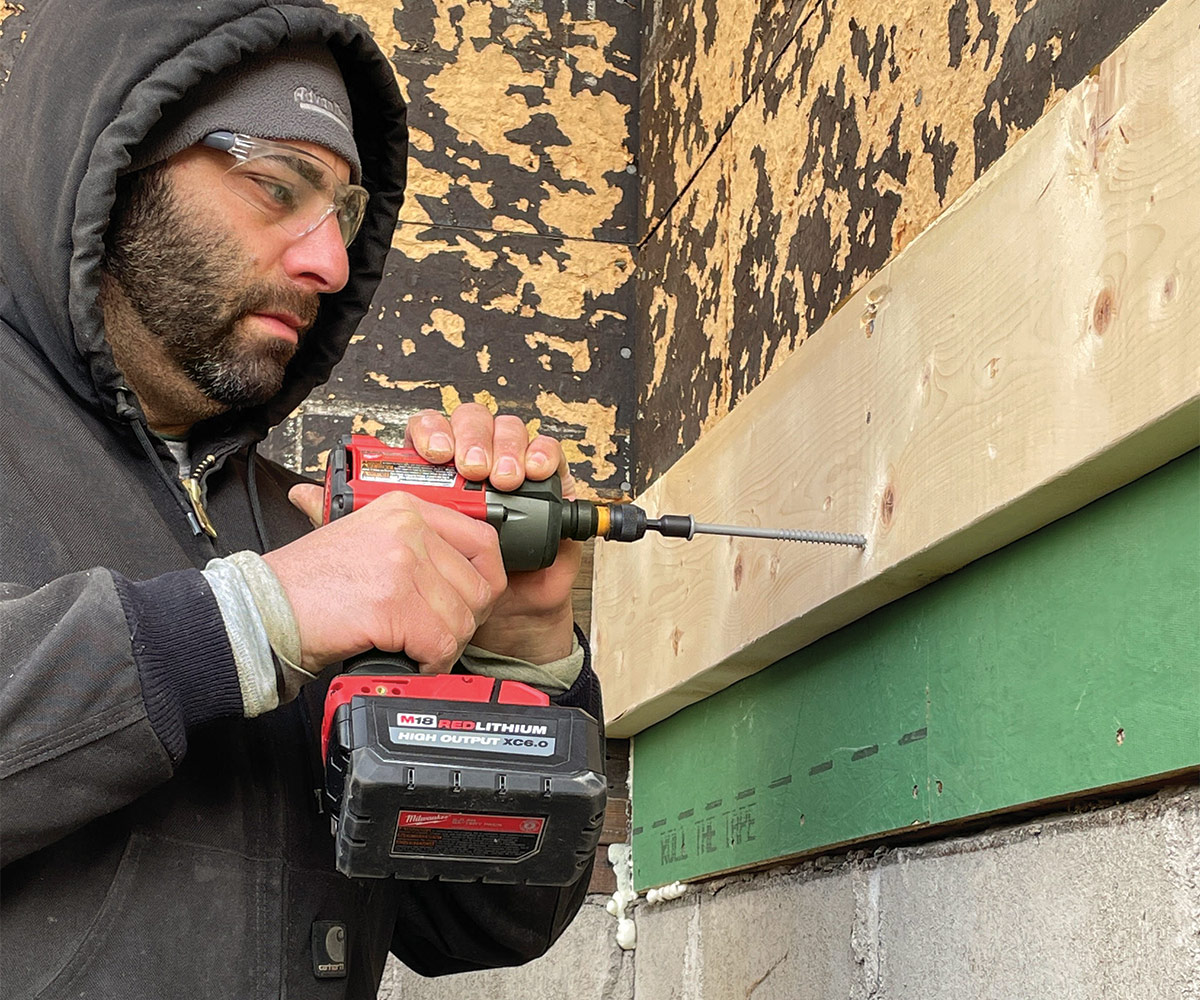
New higher joists
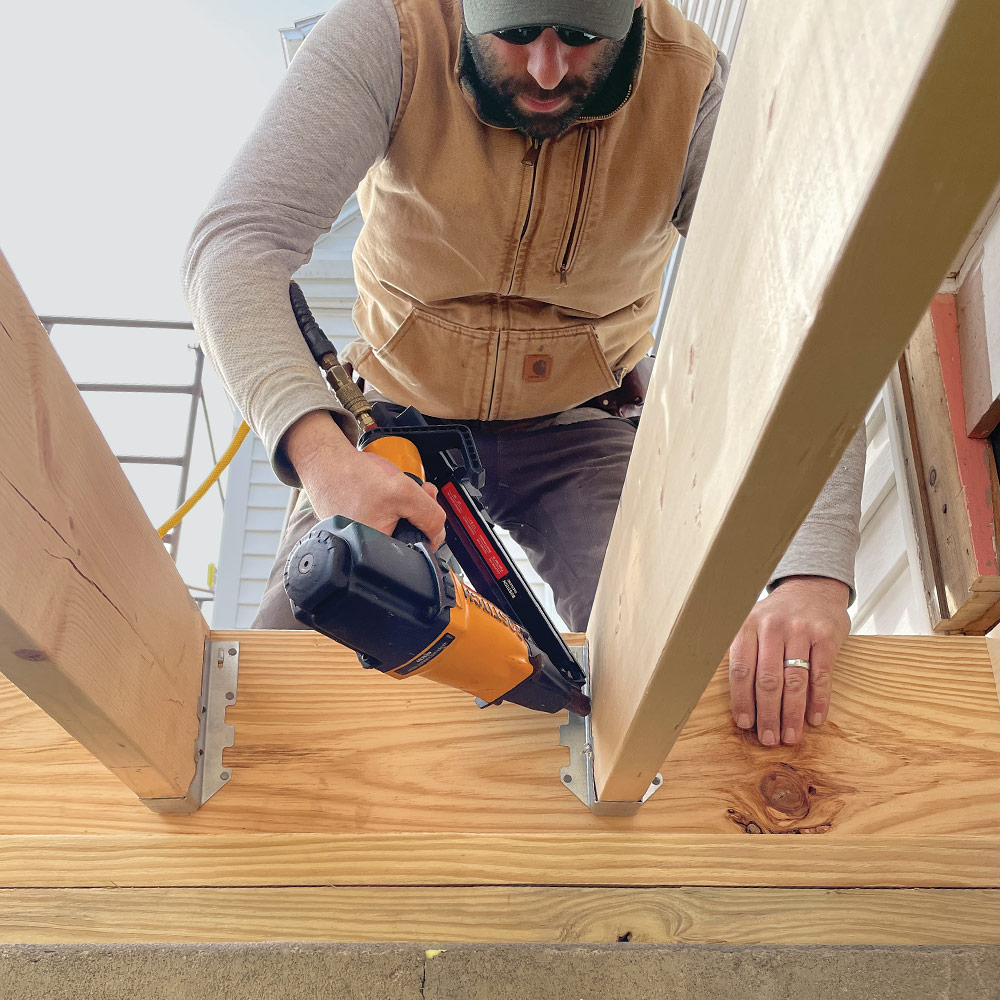
Add electrical
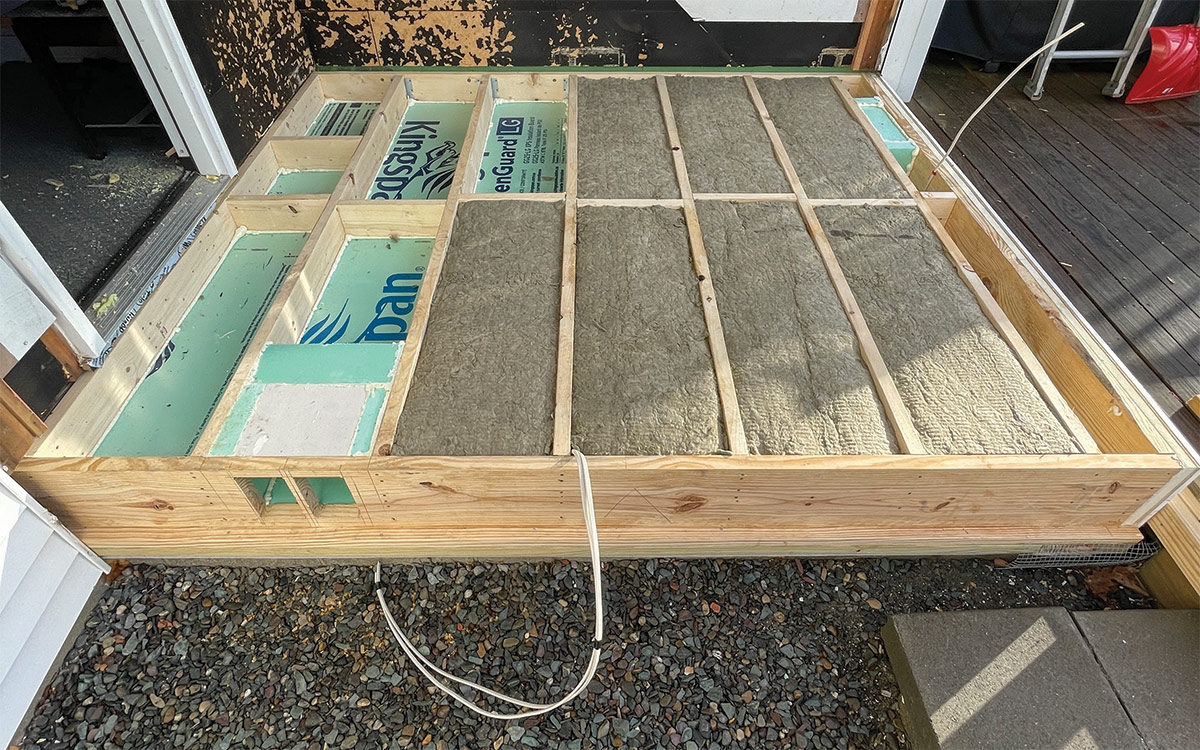
Foam for a warmer floor
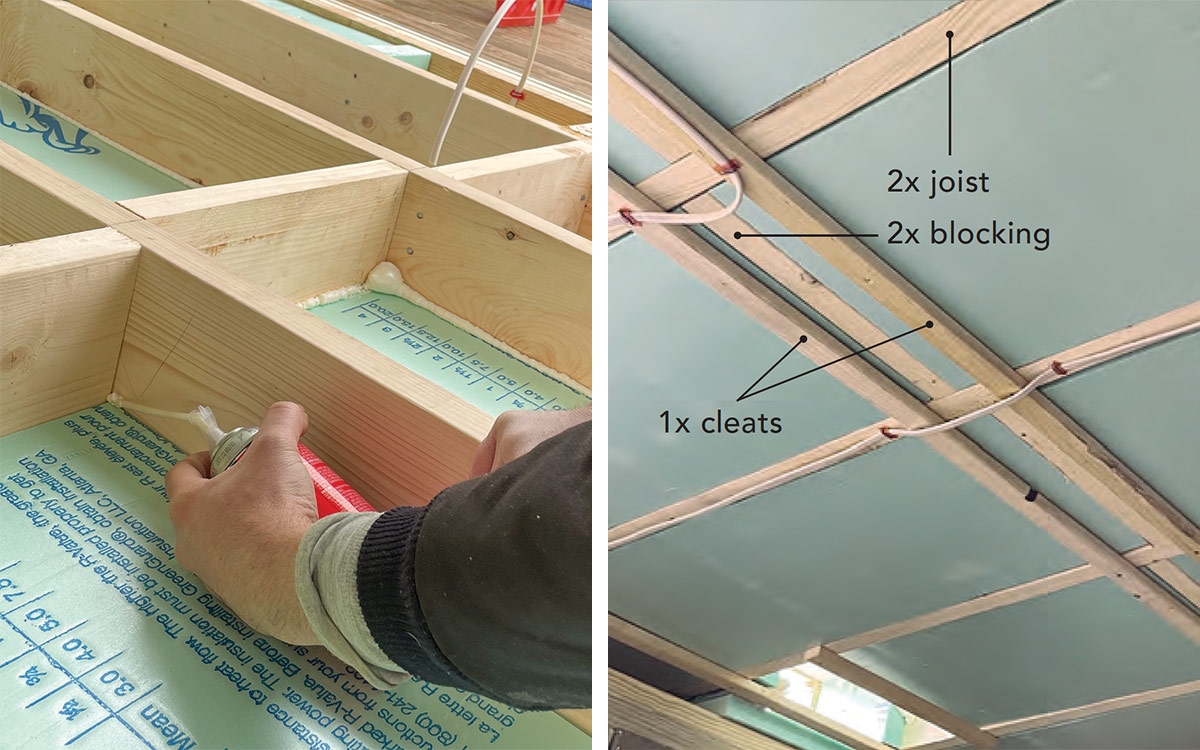
Space to breathe
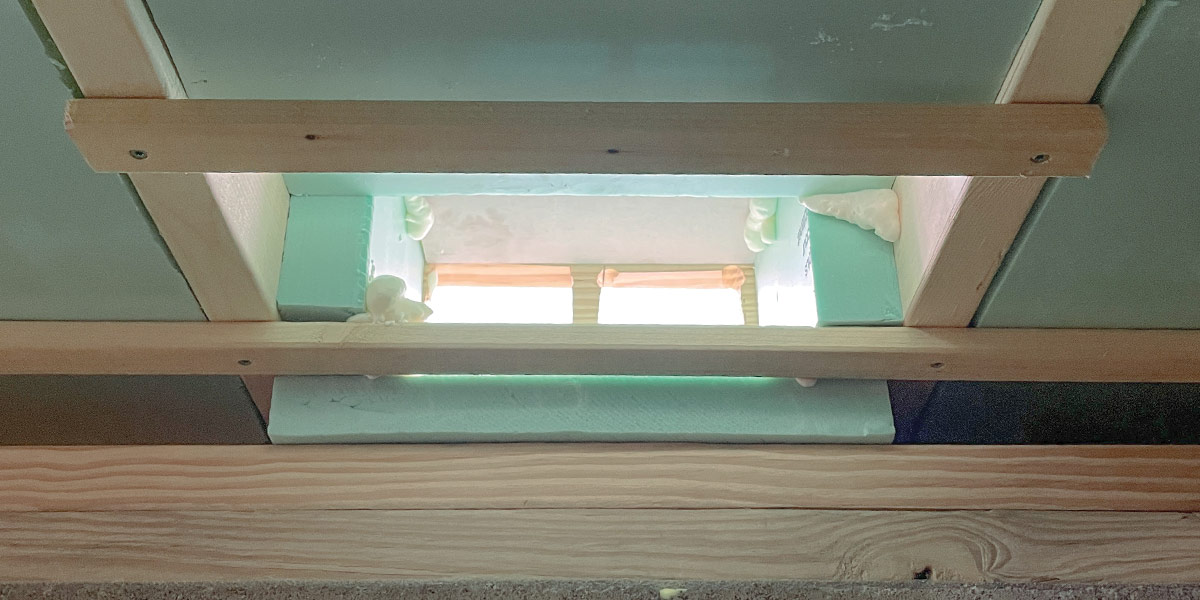
Fit and fasten the subfloor
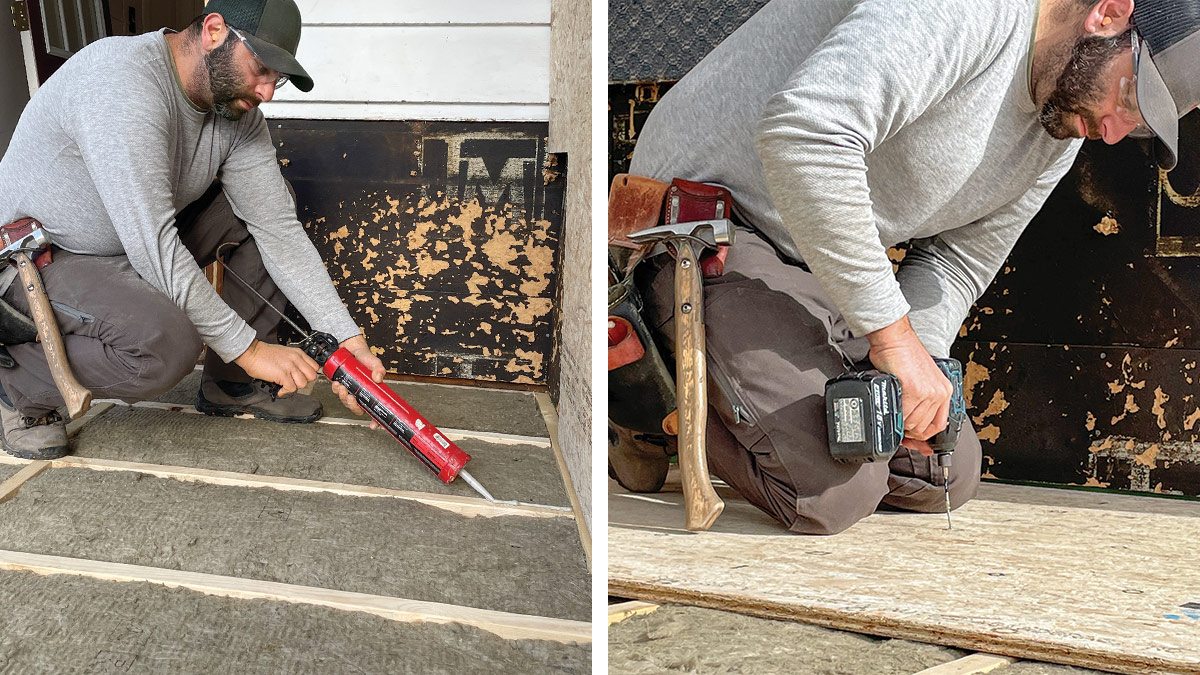
Build New Walls
After the floor was framed and insulated and the electrical stubbed up, we could build the walls. As in most remodeling situations, we built the new walls in place to make sure they followed any framing irregularities caused by seasonal movement or settling over time. Once the walls were built, we sheathed them with Zip R-sheathing and taped the seams for weather resistance and air-sealing.
Fit studs individually
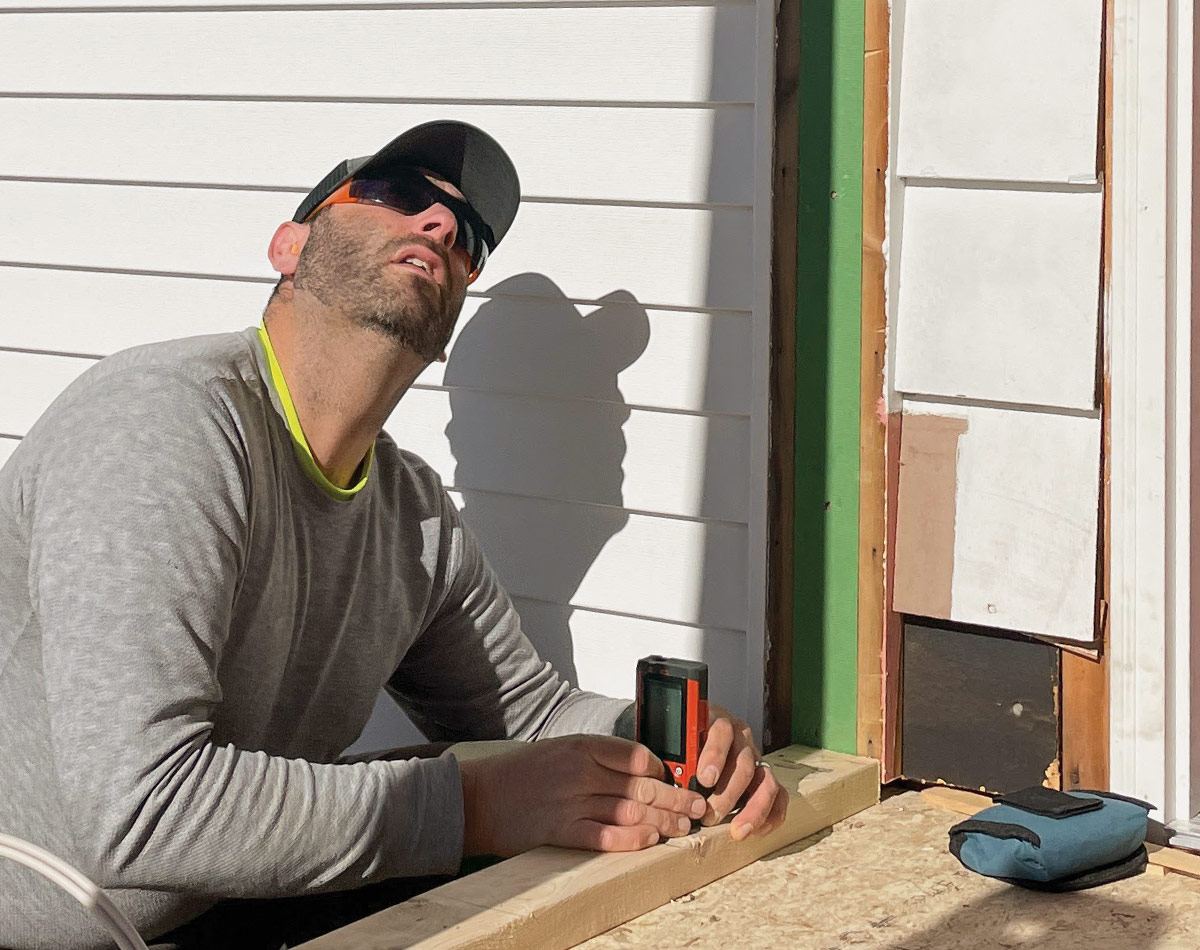
Toenail the top and bottom
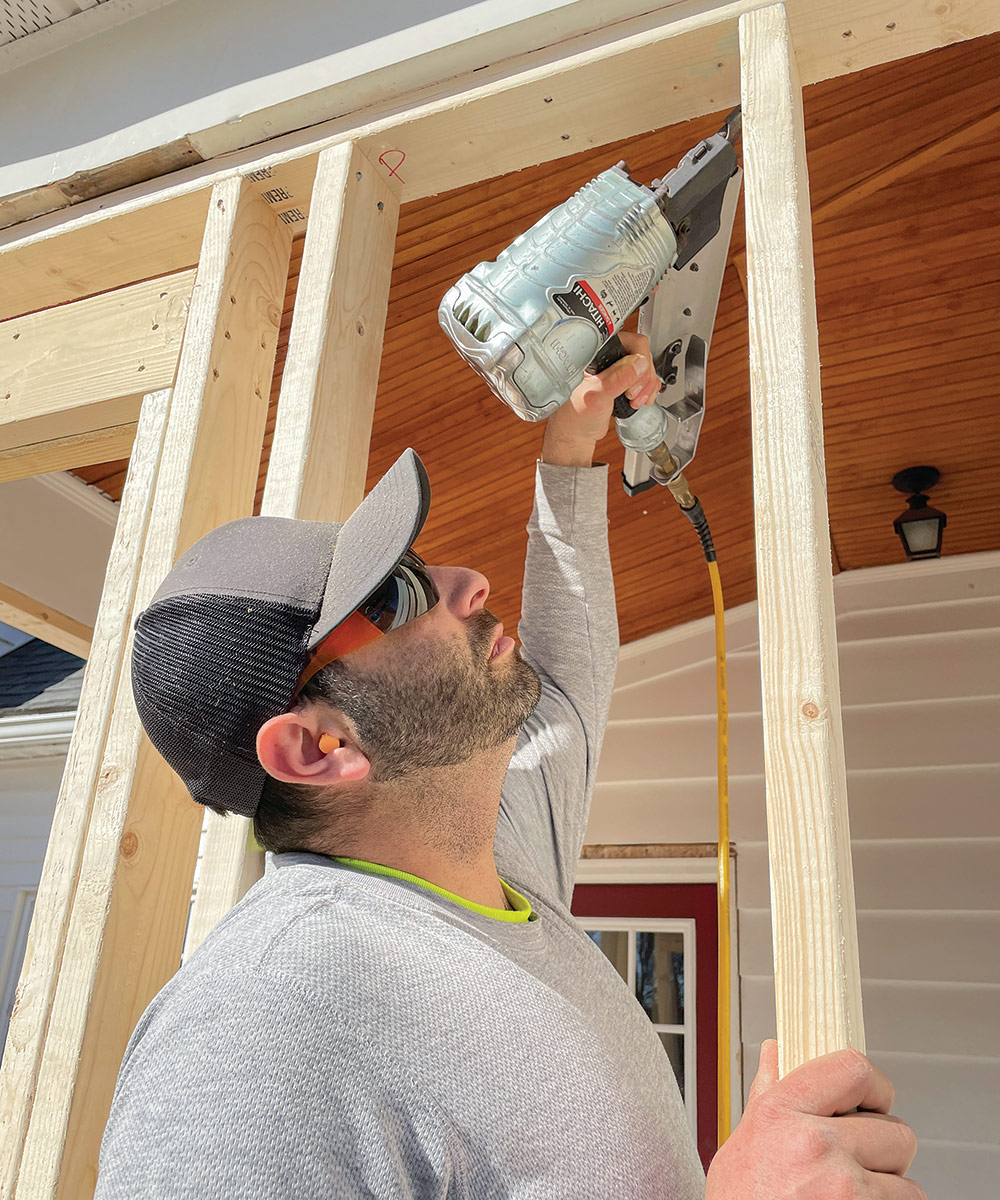
Foam and sheathing combined

Install Windows, Doors, and Siding
The material choices were simple and inexpensive and were meant to match the aesthetic of the rest of the home. We installed basic vinyl windows, a fiberglass door, and white D-4 vinyl siding. While not fancy, these building products are affordable, quick to install, and easy to maintain and clean.
Install windows with care
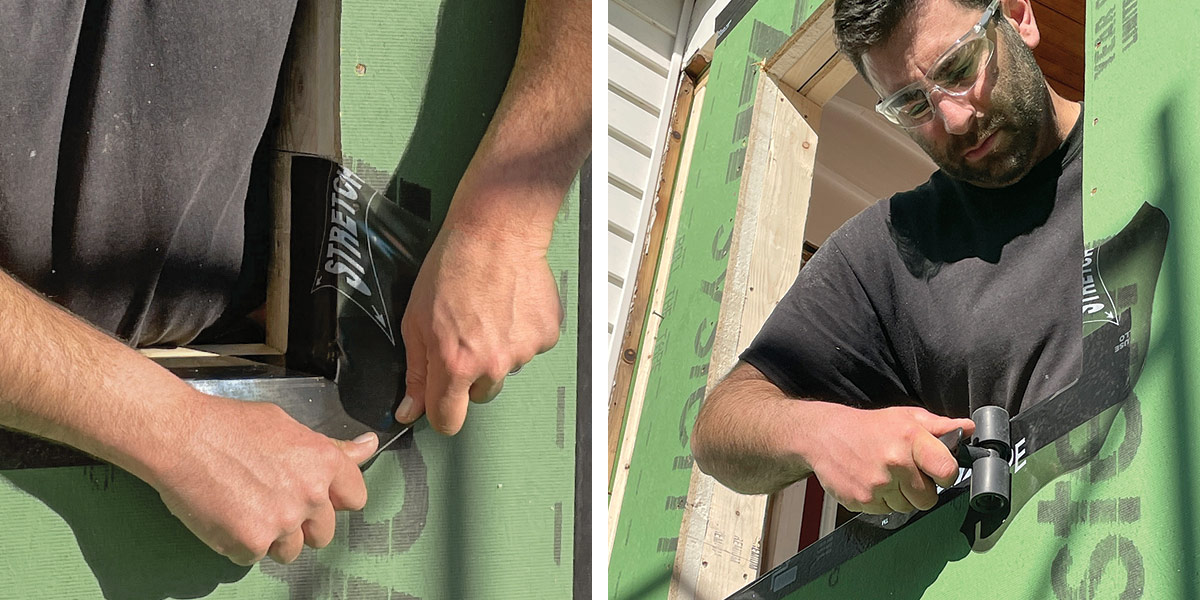
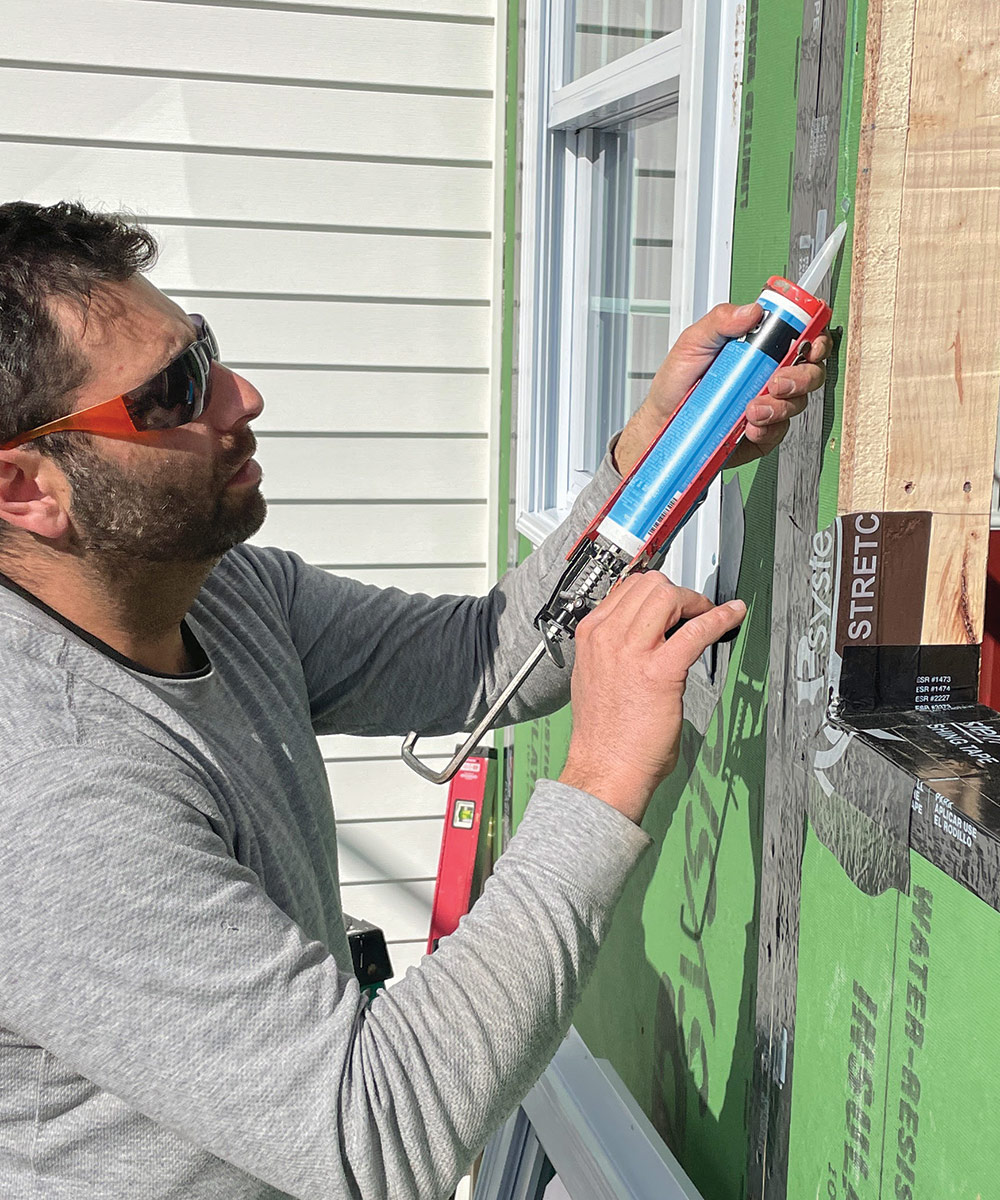
Fasten the windows
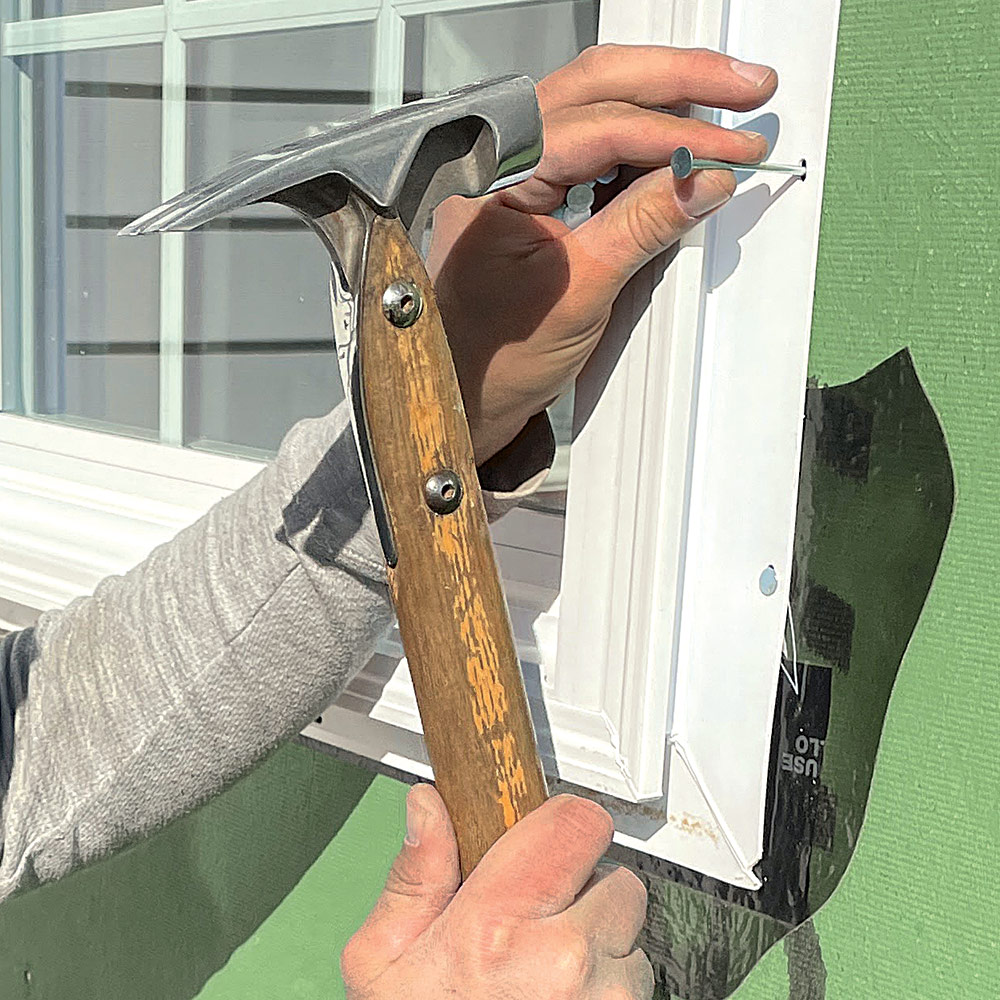
Install accessories first
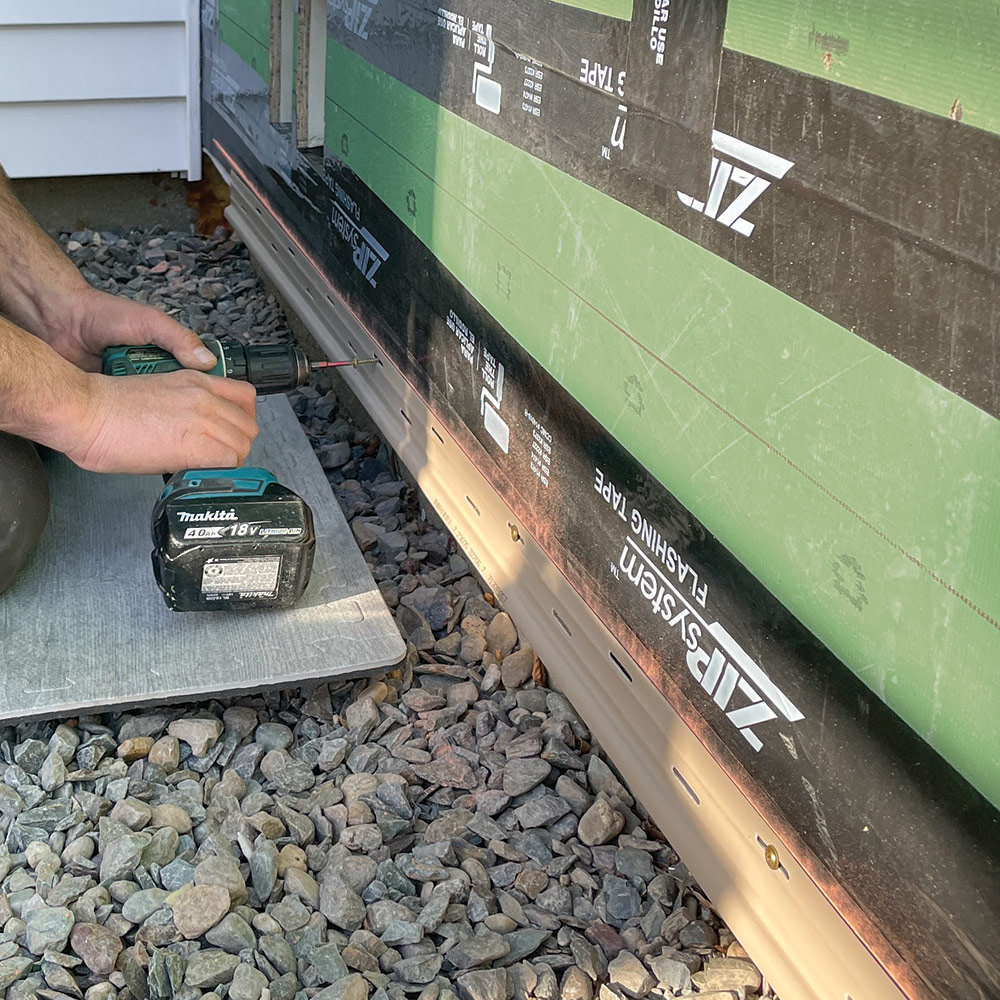
Line up corners
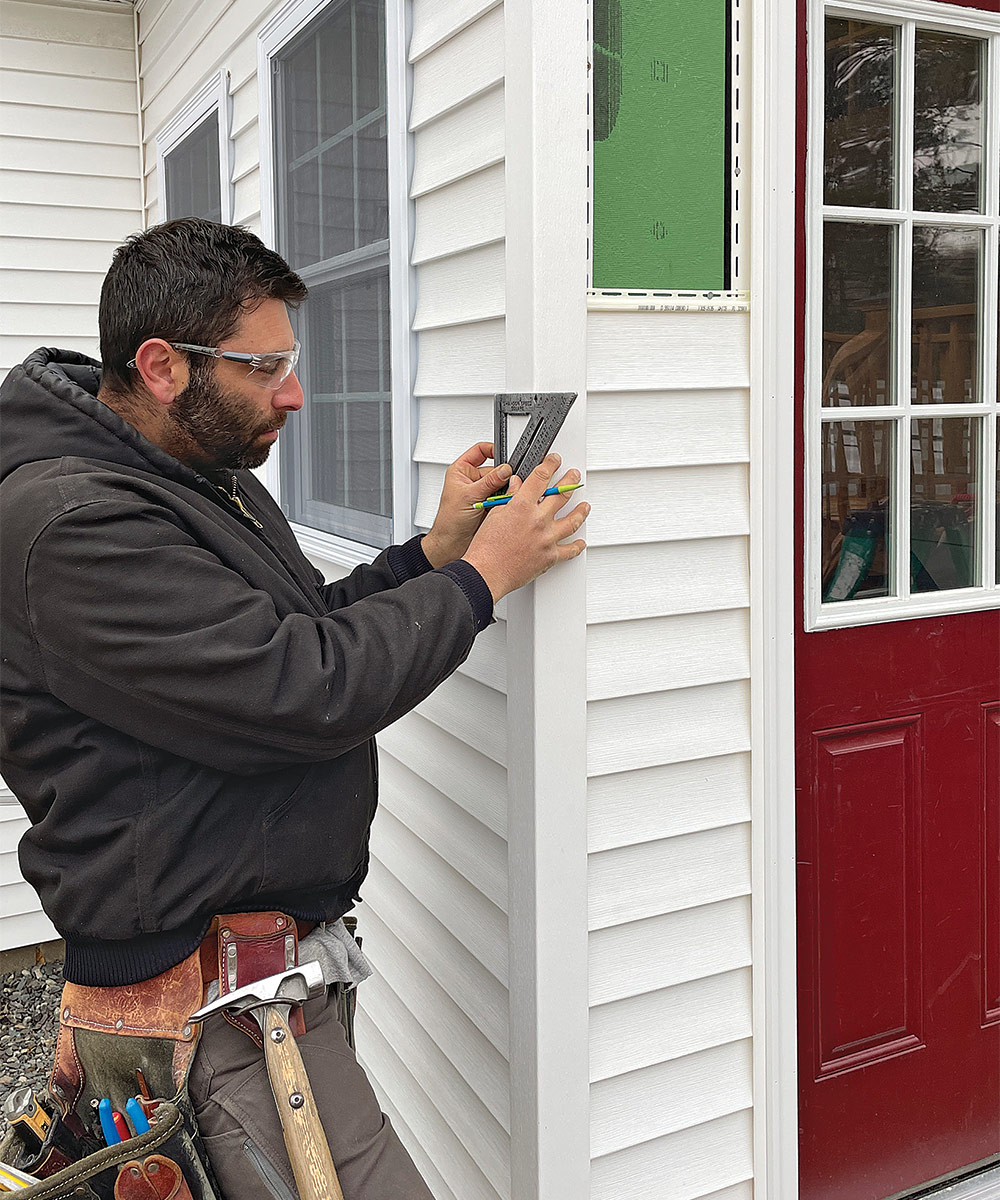
Jeremy Kassel (@kasselconstruction) is a builder in Glenmont, N.Y. Photos by Jeremy Kassel and Levi Kovach.
RELATED STORIES
View Comments
A classic example where the After product looks FAR worse than the Before. They should have just insulated around the windows and floor and installed a new door. The functionality of the floor space didn't change. It went from cute to ugly really fast, and at a much higher expense.